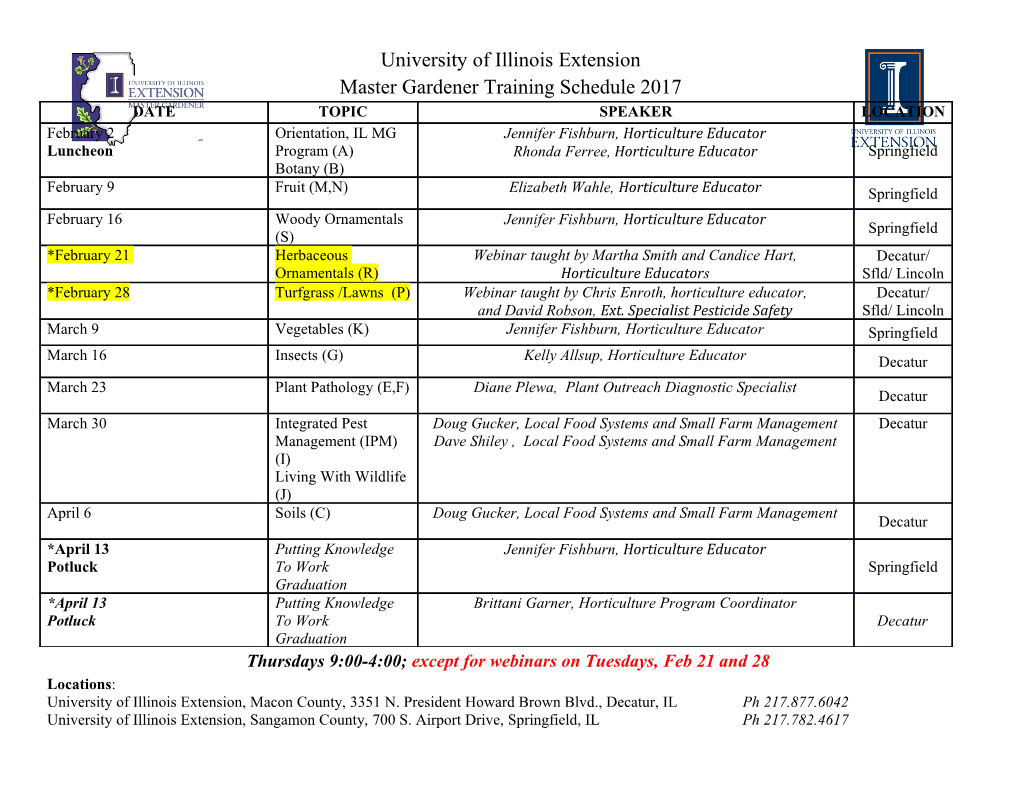
International Research Journal of Engineering and Technology (IRJET) e-ISSN: 2395 -0056 Volume: 02 Issue: 04 | July-2015 www.irjet.net p-ISSN: 2395-0072 INVESTIGATION OF SURFACE FINISH AND MRR DURING ABRASIVE ASSISTED DRILLING ON POLYMER MATRIX COMPOSITE MATERIAL. Dilpreet Singh1, Gurmeet Singh Chhatwal2, Mandeep Kumar3 1 Dept. of Mechanical Engineering, Punjab College of Engineering & Technology, Lalru Mandi, Punjab, India 2 Assistant Professor, Dept. of Mechanical Engineering, Punjab College of Engineering & Technology, Lalru Mandi, Punjab, India 3 Assistant Professor, Dept. of Mechanical Engineering, Chandigarh University, Gharuan, Punjab, India ---------------------------------------------------------------------***--------------------------------------------------------------------- Abstract - This report is concerned with investigating and tool life. Drilling is an essential operation in the the Surface finish when drilling POLYMER MATRIX assembly of the structural frames of automobiles and aircrafts. The life of a joint can be critically affected by the COMPOSITE (E-Glass) with HSS drill. This study included quality of the drilled holes. The growing demand for drilling of PMC with supply of Sic abrasive, Alumina higher productivity, product quality and overall economy Oxide Abrasive having grain size 800, 1000, 1200 mesh in manufacturing by machining, grinding and drilling, size through abrasive slurry system & with Coolant. particularly to meet the challenges thrown by Abrasives not only used for cooling purpose but also liberalization and global cost competitiveness, insists high increases the surface finish, MRR and reduce tool wear. material removal rate and high stability and long life of the cutting tools. However, high production machining and Experiments were conducted on a CNC Drilling machine. grinding with high cutting velocity, feed and depth of cut is Taguchi is applied for executing the planning of inherently associated with generation of large amount of experiments. The drilling parameters namely Feed rate heat and high cutting temperature. Such high cutting (mm/min) ,Spindle speed (rpm) ,Type of abrasive grain temperature not only reduces dimensional accuracy and size ,Slurry Concentration ,Type of Abrasive (Silicon tool life but also impairs the surface finish of the product. Carbide, Alumina oxide), were optimized using multiple One estimate is that 75% of all metal-cutting material performance characteristics for Surface Finish. The removed comes from drilling operations. Drilled holes are characterized by their sharp edge on the entrance side and result shows that the feed rate, Type of Abrasive & the presence of burrs on the exit side (unless they have slurry concentration are the most significant factors been removed). which affect the Surface finish in the drilling can be We all know that the 20th century has witnessed effectively improved by using this approach revolutions in a number of fields like computer, Radar, space, missiles, etc. but the most interesting Key Words: Abrasives, ANOVA, Drilling, Taguchi changes have taken place in the area of polymer matrix composites. In the literature review we will review the Technique, Polymer Matrix Composite material E- surface roughness and material removal rate, Taguchi Glass , Surface roughness, MRR. technique. 2. LITERATURE REVIEW 1. INTRODUCTION J.Pradeep Kumar analyzed that to utilize Taguchi method Drilling is one of the most fundamental machining to investigate the effects of drilling parameters on surface processes. It is most frequently performed in material roughness, tool wear by weight, material removal rate and removal and is used as a preliminary step for many hole diameter error in drilling of OHNS material using HSS operations such as reaming, tapping and boring. It is spiral drill. Orthogonal arrays of Taguchi, the Signal–to- moving toward high speed applications for productivity Noise (S/N) ratio, the analysis of variance (ANOVA), and enhancement. Drilling is a process of producing round regression analysis are employed to analyze the effect of hole in solid material or enlarging existing hole with the drilling parameters on the quality of drilled holes. A series use of multi-point cutting tools called drill or drill bits. of experiments based on L18 orthogonal array are Various cutting tools are 297blind hole in a solid material. conducted. The experimental results are collected and It has found that high production machining and drilling analyzed using commercial software package MINITAB 13. with high cutting velocity, feed and depth of cut is Linear regression equations are developed with an inherently associated with generation of large amount of objective to establish a correlation between the selected heat and high cutting temperature which reduces accuracy drilling parameters with the quality characteristics of the © 2015, IRJET.NET- All Rights Reserved Page 297 International Research Journal of Engineering and Technology (IRJET) e-ISSN: 2395 -0056 Volume: 02 Issue: 04 | July-2015 www.irjet.net p-ISSN: 2395-0072 drilled holes. The predicted values are compared with assisted drilling have lesser thrust and hence lesser de- experimental data and are found to be in good agreement lamination compared to conventional drilling, which [1]. indicates that both vibration assisted drilling and Ultrasonic assisted drilling are more appropriate for Yogendra Tyagi investigated that the drilling of mild drilling of GFRP [4]. steel with the help of CNC drilling machine operation with high speed steel by applying Taguchi methodology has B. Ramesh investigated that a non laminated Glass Fiber been reported. The Taguchi method is applied to Reinforced Plastic (GFRP) composite manufactured by formulate the experimental layout to ascertain the pultrusion process was drilled with a coated cemented element of impact each optimum process parameters for carbide drill. The thrust force and torque during drilling CNC drilling machining with drilling operation of mild were acquired through piezoelectric dynamometer and steel. A L9 array, Taguchi method and analysis of variance damage factor was measured using metallurgical (ANOVA) are used to formulate the procedure tried on the microscope. Taguchi’s orthogonal array and analysis of change of parameter layout. The available material study variance (ANOVA) were employed to study the influence in focuses optimization of CNC Drilling machine process of process parameters such as feed and spindle speed on parameters to provide good surface finish as well as high thrust force, torque and damage factor. The optimum level material removal rate (MRR).The surface finishing and of process parameters towards minimum thrust force, material removal rate have been identified us quality minimum torque and lower damage factor were obtained attribute and are assumed to be directly related to to achieve defect controlled drilling of GFRP composites. productivity. The selection of optimal machining Correlations for thrust force, torque and damage factor parameters i.e., spindle speed, depth of cut and feed rate) with process parameters were established using statistical for drilling machine operations was investigated in order software MINITAB 15. Among the process parameters to minimize the surface roughness and to maximize the examined, feed significantly influences both the thrust material removal rate [2]. force and torque with 88.52% and 92.83% respectively whereas the influence of spindle speed on the above was Arshad Noor Siddiquee had focused on optimizing deep relatively insignificant. The influence of feed and spindle drilling parameters based on Taguchi method for speed on damage factor at both entrance and exit of the minimizing surface roughness. The experiments were work piece was insignificant [5]. conducted on CNC lathe machine using solid carbide cutting tool on material AISI 321 austenitic stainless steel. 3. MACHINING SETUP Four cutting parameters such as cutting fluid, speed, feed For the entire experiment Computer Numerical Machine and hole-depth, each at three levels except the cutting (FAMUP Machining Centre) was used shown in fig 1. The fluid at two levels were considered. Taguchi L18 abrasive slurry of Silicon Carbide and Alumina Oxide of orthogonal array was used as design of experiment. The grit size 800, 1000, 1200 was cutting fluid for signal-to-noise (S/N) ratio and the analysis of variance experimentation. The slurry was used with varying (ANOVA) was carried out to determine which machining concentration of 20%, 25%, and 30%. The work material parameter significantly affects the surface roughness and used for the experimentation is Polymer matrix composite also the percentage contribution of individual parameters. (E-Glass). Then surface roughness of machined surface Confirmation test was conducted to ensure validity of the was measured with the help of Mtiutoyo SJ-201P for all the test result. It is observed that the surface finish for deep machined samples. Average surface roughness "Ra" was drilling process can be improved effectively through this measured. approach [3]. B.V.Kavad had studied that drilling is an important process for making and assembling components made from Glass Fiber Reinforced Plastic (GFRP). Various processes like conventional drilling, vibration assisted drilling and ultrasonic assisted drilling have been attempted in order to maintain the integrity of the material and obtain the necessary accuracy in drilling of GFRP. This paper attempts to review the influence
Details
-
File Typepdf
-
Upload Time-
-
Content LanguagesEnglish
-
Upload UserAnonymous/Not logged-in
-
File Pages6 Page
-
File Size-