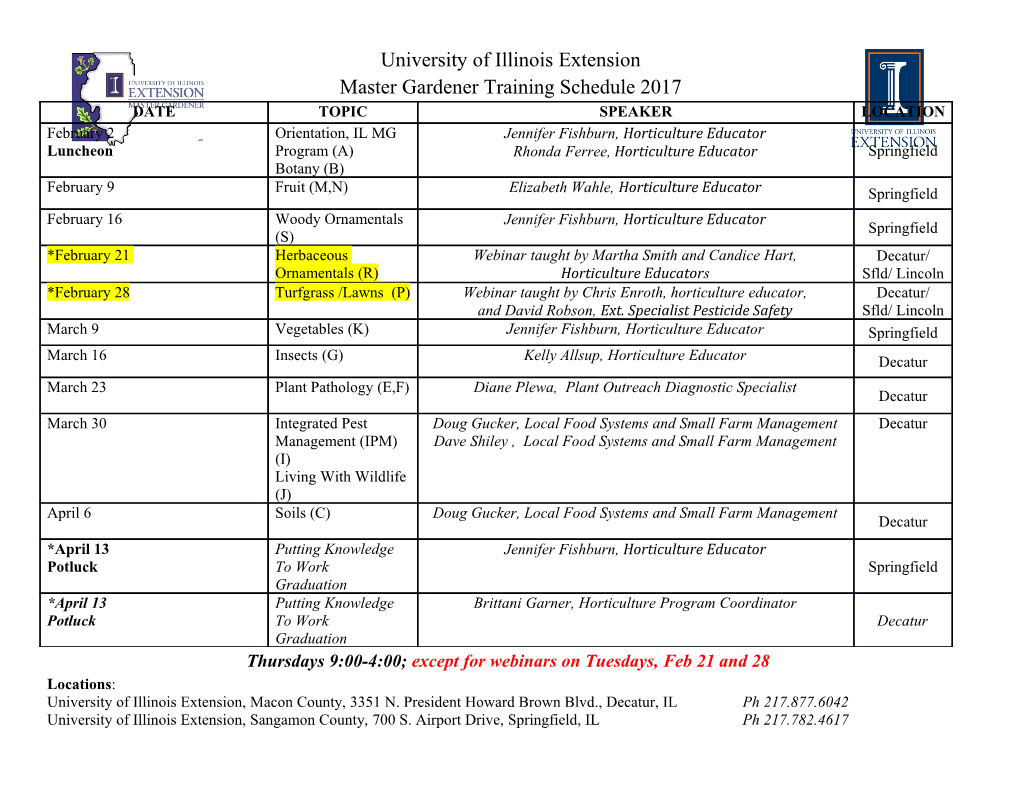
UPF PROJECT PROCEDURE Title: UPF WELDING AND CUTTING SAFETY Document Number: UPF-CP-225WCS Revision: 000 Page: 1 of 13 Prepared by: . 05/09/16 . Brian Garrett, Date BNI UPF ES&H Lead Approved by: . 05/09/16 . Ed Kelley, Date BNI UPF ES&H Manager Approved by: . 05/09/16 . Gary Hagan, Date UPF ES&H Manager Concurrence by: . 05/09/16 . Lynn Nolan, Date UPF Manager of Construction . 05/10/16 . James W. Sowers, Date UPF Quality Assurance Manager 05/11/16 Effective Date RC-UPF DMC This document has been reviewed by a Y-12 DC / RC-UPF DMC UCNI-RO and has been determined to be 05/10/16 15:15 UNCLASSIFIED and contains no UCNI. This review 05/10/16 15:32 does not constitute clearance for Public Release. Name:________________________ Date:__________05/09/16 UPF-CP-225WCS Revision 00 Page 2 of 13 UPF Welding and Cutting Safety Revision History Revision Reason/Description of Change Initial issue. 000 UPF-CP-225WCS Revision 00 Page 3 of 13 UPF Welding and Cutting Safety Table of Contents 1.0 PURPOSE ..................................................................................................................................4 2.0 GENERAL ..................................................................................................................................4 Description ....................................................................................................................4 Acronyms .......................................................................................................................4 Definitions ......................................................................................................................4 3.0 RESPONSIBILITIES ...................................................................................................................5 Construction Manager ..................................................................................................5 Field Safety Manager. ...................................................................................................5 Field Safety Representative .........................................................................................5 Discipline Superintendent ............................................................................................5 Supervisor .....................................................................................................................5 Worker. ...........................................................................................................................5 4.0 WELDING AND CUTTING CONTROLS ....................................................................................5 Fire Prevention ..............................................................................................................5 Protection of the General Area ....................................................................................6 Exposure Controls ........................................................................................................6 Cylinder “Use Status” ...................................................................................................8 4.5 Other Gas Welding, Cutting, and Heating Equipment ...............................................8 4.6 Welding or Cutting with Electrical Equipment ...........................................................9 Exothermic Welding ....................................................................................................11 5.0 RECORDS ................................................................................................................................11 6.0 REFERENCES .........................................................................................................................11 Source References ......................................................................................................11 Interfacing References ...............................................................................................11 7.0 EXHIBITS / APPENDICES / FIGURES ..................................................................................111 7.1 Appendix A – Welding Filter Lenses and Plates ....................................................112 UPF-CP-225WCS Revision 00 Page 4 of 13 UPF Welding and Cutting Safety 1.0 PURPOSE This procedure provides safety and health requirements for welding and thermal cutting activities performed on the UPF construction site and other support areas. 2.0 GENERAL Description This procedure is applicable to welding, cutting, heat-treating, grinding, and other welding operations in support of Uranium Processing Facility (UPF) construction operations. Acronyms CM Construction Manager DS Discipline Superintendent FSM Field Safety Manager FSR Field Safety Representative UPF Uranium Processing Facility Definitions Combustible Material - A material that, in the form in which it is used and under the conditions anticipated, has the potential to ignite and burn. Enclosed Spaces - Any space, other than a confined space, which is enclosed to the extent that natural ventilation is not favorable. Exothermic Welding - A welding process, including, but not limited to Thermite or Cad- Welding, that produces coalescence of metals by heating them with superheated liquid metal resulting from a chemical reaction between a metal oxide and aluminum, with or without the application of pressure. Filler metal, where used, is obtained from the liquid metal. Flammable Material – Materials (solid, liquid, or gas) that are easily ignited and capable of burning rapidly. Fuel Gas - Acetylene; hydrogen; natural gas; LP-Gas; methylacetylene-propadiene, stabilized; and other liquefied and non-liquefied flammable gases that are stable because of their composition or because of the conditions of storage and utilization Gas(es) – Propane, argon, nitrogen, mixed gases, or other fuel gases used with or without oxygen for cutting and welding activities. Gas Cylinders “In Storage” - A gas cylinder is considered “In Storage” when it is reasonably anticipated that gas will not be drawn from the cylinder within 24 hours (overnight hours included). In Use - Gas Cylinders “In Use” - A gas cylinder is considered “In Use” when it is reasonably anticipated that gas will [ibid] be drawn from the cylinder within 24 hours, based on the welding work being planned. Mechanical Ventilation – Work environment air movement systems are of two types for the purpose of this procedure: UPF-CP-225WCS Revision 00 Page 5 of 13 UPF Welding and Cutting Safety General Mechanical Ventilation – Systems that move air for an identified area (building or room) such as roof or wall exhaust fans. Coppus blowers, used for areas without established general mechanical ventilation, are also considered general ventilation. Local Exhaust Ventilation – Air movement systems, equipped with freely movable intake hoses or hoods that can be placed close to a source, and have a determined capacity, can remove airborne fumes and dust and maintain safe breathing conditions. Welding/Cutting Operations – Processes such as arc welding, oxy-fuel gas welding, metal inert gas (MIG) welding, grinding, open-flame soldering, brazing, thermal spraying, oxygen cutting, and arc cutting. 3.0 RESPONSIBILITIES Construction Manager – has the overall responsibility for ensuring the implementation of this procedure, ensuring that all project personnel actively participate; and provides worker support, facilities, and other resources necessary to effectively carry out this procedure. Field Safety Manager - has the overall authority for interpretation of the regulations associated with the procedure and the interpretation of the procedure as to intent and application. Field Safety Representative – has the responsibility of compliance oversight with the procedure through periodic field inspections and is responsible for supplying technical advice and interpretation of the environmental, safety, and health codes included in the procedure. Discipline Superintendent – is responsible for being thoroughly familiar with this procedure and their individual responsibilities regarding compliance with and implementation of this procedure, pre-planning work activities to identify the appropriate work controls and ensuring workers understand the requirements of the procedure. Supervisor – is responsible for ensuring the applicable safety controls and processes are incorporated into planning and execution of the work and that the workers are implementing and complying with this procedure within their area of responsibility. Worker – is responsible for understanding and complying with the requirements of this procedure. 4.0 WELDING AND CUTTING CONTROLS Fire Prevention Welding operations performed outside designated hot work areas are allowed only after a Hot Work Permit is generated per procedure Y17-95-64-877, Hot Work Permit. o Fire watches are activated through the Hot Work Permit and roles are defined in procedure UPF-CP-227, Safety Watches. For compressed gas cylinder requirements reference procedure UPF-CP-225, Compressed Gas Cylinders. UPF-CP-225WCS Revision 00 Page 6 of 13 UPF Welding and Cutting Safety Protection of the General Area Locate welding equipment, machines, cable and other apparatus so that it does not present a hazard to personnel. Keep passageways, ladders, and stairways clear. Route hoses, cords and leads so they do not create a tripping hazard and are not subject to physical damage. Post signs, in accordance with procedure UPF-CP-214, Barricade and Signs,
Details
-
File Typepdf
-
Upload Time-
-
Content LanguagesEnglish
-
Upload UserAnonymous/Not logged-in
-
File Pages13 Page
-
File Size-