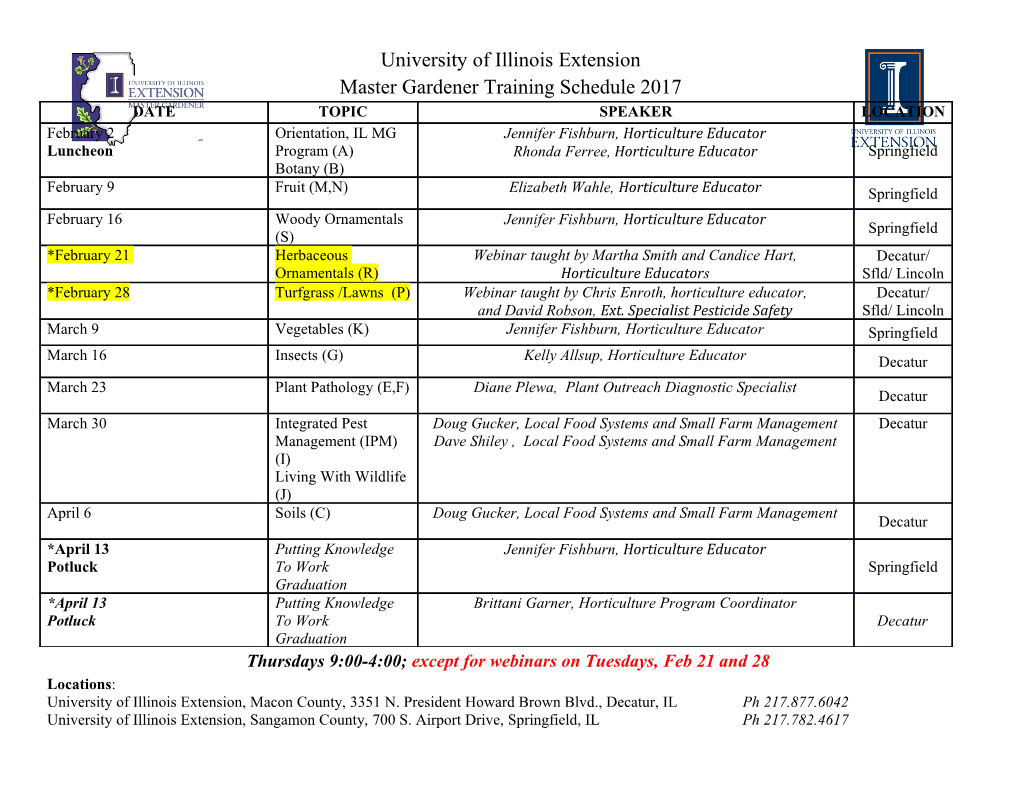
University of Southampton Research Repository ePrints Soton Copyright © and Moral Rights for this thesis are retained by the author and/or other copyright owners. A copy can be downloaded for personal non-commercial research or study, without prior permission or charge. This thesis cannot be reproduced or quoted extensively from without first obtaining permission in writing from the copyright holder/s. The content must not be changed in any way or sold commercially in any format or medium without the formal permission of the copyright holders. When referring to this work, full bibliographic details including the author, title, awarding institution and date of the thesis must be given e.g. AUTHOR (year of submission) "Full thesis title", University of Southampton, name of the University School or Department, PhD Thesis, pagination http://eprints.soton.ac.uk UNIVERSITY OF SOUTHAMPTON FACULTY OF ENGINEERING, SCIENCE AND MATHEMATICS School of Engineering Sciences Development of a Fabrication Process for a MEMS Component from Ultra Fine Grained Alloys by Xiao Guang Qiao Thesis for the degree of Doctor of Philosophy February 2010 UNIVERSITY OF SOUTHAMPTON ABSTRACT FACULTY OF ENGINEERING, SCIENCE & MATHEMATICS SCHOOL OF ENGINEERING SCIENCES Doctor of Philosophy DEVELOPMENT OF A FABRICATION PROCESS FOR A MEMS COMPONENT FROM ULTRA FINE GRAINED ALLOYS By Xiao Guang Qiao This thesis presents a study on the feasibility of fabricating a MEMS component by embossing using ultra-fine grained (UFG) aluminium alloys. The main elements of the work involved designing the equipment, production of UFG aluminium alloys through equal channel angular pressing (ECAP), embossing of the UFG alloys and the construction of models that improve the understanding of the main elements of the processing. ECAP was performed on Al-1050, AlZr and AlZrSiFe alloys to produce UFG Al alloys. Microstructure and texture evolution were analyzed by electron backscattered diffraction (EBSD) and transmission electron microscopy (TEM). A new predictive model of grain refinement allows the understanding of the grain refinement process. Microhardness inhomogeneity of UFG Al-1050 processed by one pass of ECAP was studied through measuring the distribution of Vickers hardness and microstructure on the cross section before and after annealing at different temperature. Microhardness of UFG Al alloys processed by various passes of ECAP was measured after annealing at various temperatures. The relation between microhardness and microstructure was studied with the aid of a dislocation model. The model suggests that most of the strengthening in the severely plastically deformed alloys is due to enhanced dislocation density. Nanoindentation hardness of UFG Al-1050 was also measured. A modified model of indentation size effect was derived. The model was justified through comparison with our own data and data in literature. The UFG Al alloys were embossed using a micro silicon die with a pattern of microchannels at both room temperature and high temperature. The topography of embossed sample was observed by scanning electron microscopy (SEM), optical microscopy (OM) and confocal laser system. Nanoindentation hardness was measured on cross section of the embossed sample to detect the hardness distribution. Focus ion beam (FIB) and EBSD were used to characterize the microstructure on the cross section. A model employing concept of geometrically necessary dislocations (GND) was present to predict embossing force and hardness distribution on the cross section. This study shows a good potential for fabrication of microdevices by embossing UFG alloys processed by ECAP. An optimized process was obtained through analysis of microstructure and properties of the UFG alloys before and after embossing. The understanding of the processing was enhanced through construction of models. I List of Contents ABSTRACT.......................................................................................................................I List of Contents................................................................................................................ II List of Figures .................................................................................................................VI List of Tables ..................................................................................................................XI Declaration of Authorship............................................................................................. XII Acknowledgements......................................................................................................XIV Definitions and Abbreviations ...................................................................................... XV 1 Introduction...................................................................................................................1 2 Literature Review..........................................................................................................4 2.1 Introduction of aluminium alloys..........................................................................4 2.2 Al-Zr alloys...........................................................................................................6 2.2.1 Microstructure of Al-Zr alloys........................................................................6 2.2.2 Property of Al-Zr alloys................................................................................10 2.3 MEMS technologies............................................................................................13 2.3.1 Developments of MEMS technology............................................................13 2.3.2 Applications of MEMS .................................................................................14 2.3.2.1 Communications ...................................................................................14 2.3.2.2 Automobile............................................................................................14 2.3.2.3 Biotechnology .......................................................................................15 2.3.3 Microfabrication technologies......................................................................15 2.3.3.1 Anisotropic wet etching........................................................................16 2.3.3.2 Dry etching............................................................................................17 2.3.3.3 LIGA .....................................................................................................20 2.3.4 Embossing.....................................................................................................21 2.3.4.1 Embossing equipment ...........................................................................22 2.3.4.2 Embossing Process................................................................................24 2.3.4.3 Embossing on metals ............................................................................24 2.3.4.4 Nanoindentation as a method for characterising embossed metals.......27 2.4 Micro-heat exchangers........................................................................................30 2.4.1 Classification of micro heat exchangers .......................................................30 2.4.2 Materials and forming methodology for micro heat exchangers ..................32 II 2.5 Severe plastic deformation..................................................................................36 2.5.1 High pressure torsion ....................................................................................38 2.5.2 Multi-directional forging...............................................................................38 2.5.3 Accumulative roll bonding............................................................................39 2.5.4 Cyclic extrusion and compression ................................................................40 2.5.5 Repetitive corrugation and straightening ......................................................41 2.5.6 Twist extrusion..............................................................................................42 2.6 Equal channel angular pressing...........................................................................42 2.6.1 Principle of ECAP.........................................................................................43 2.6.2 Mechanisms of grain refinement in ECAP ...................................................45 2.6.3 Application of ECAP in aluminium alloys ...................................................49 2.6.3.1 Microstructure of aluminium alloys after ECAP ..................................49 2.6.3.2 Thermal stability of UFG aluminium alloys .........................................51 2.6.3.3 Properties of aluminium alloys after ECAP..........................................54 2.7 Summary .............................................................................................................58 3 Design of Equipment...................................................................................................60 3.1 ECAP facilities....................................................................................................60 3.2 ECAP processing procedures..............................................................................63 3.3 Embossing Facilities...........................................................................................63 3.4 Embossing process and procedures.....................................................................73
Details
-
File Typepdf
-
Upload Time-
-
Content LanguagesEnglish
-
Upload UserAnonymous/Not logged-in
-
File Pages223 Page
-
File Size-