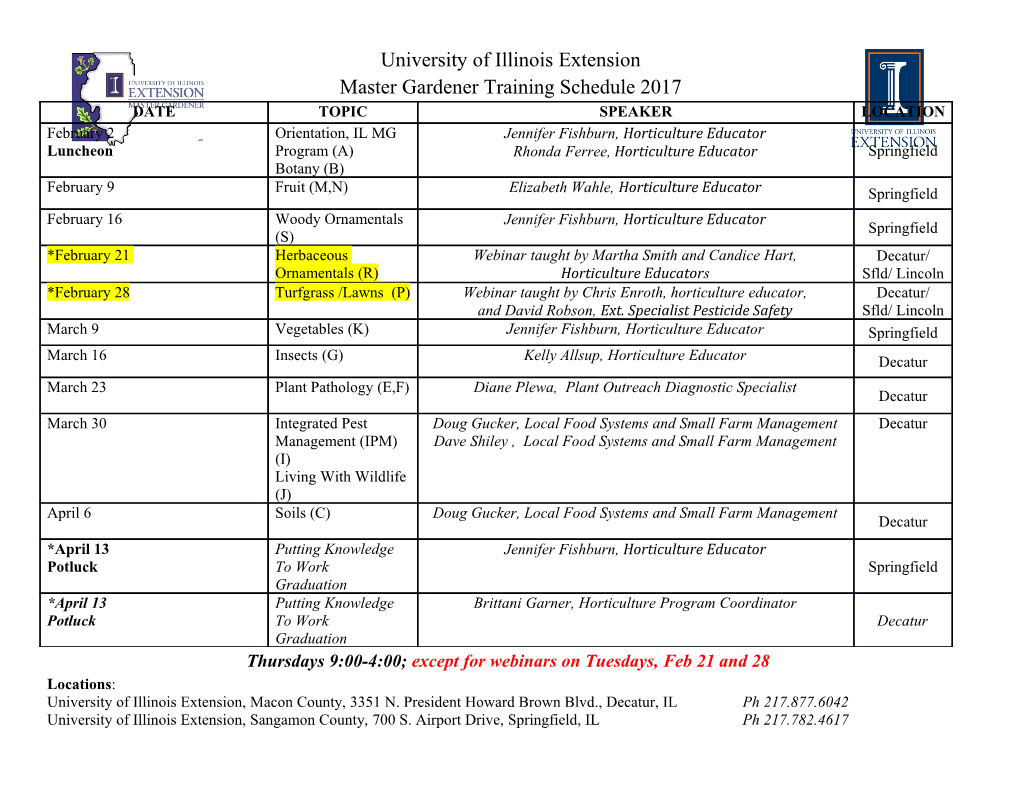
3% LUEIS ON THE SEPARATION OF GALENA AND BLENDE. [Selected (Paper No. 1942.) The Separation of Galena and Blende fiom their gangue as practised at the Mines of Sentein, Arihge, France.” By ERNESTDU BOISLUKIS, Assoc. M. Inst. C.E. THISis a record of detailed observations made whilst preparing formarket galena and blende, at the mines of Sentein in the Pyrenees. The oreswere intimately mixed in the proportion of 8 to 10 per cent. of galena, 15 to 20 percent. of blende, and gangue consisting of hard quartz, quartzose rock, schist, &c. The market lead-ore obtained included from 16 to 20 oz. of silver per ton.The blende did not contain sufficient silver for valuation. By experiments in the laboratory, it was found that the galena lost very little silver byfine crushing and washing. The machinery, supplied by Mr. George Green, of Aberystwyth, was erected in existing buildings; but these were so scattered that it is not thoughtnecessary to givea plan of them. Instead of this, a method of arranging the whole of the required plant under one roof, with slight modifications, that would render such proposed dressing-floors more efficient, is given in Plate 7, Figs. 1, the sub- stantialstructure indicated being necessary on account of the climate of the Pyrenees, where protection from frost and snow is indispensable. Water-power was used, being abundant, but the motors are not shown in Figs. 1, for, depending on the position of such proposed floors, steamor water wouldbe used asmight be found most advantageous. Mention is, however, made later on of the power required. The first point of importance is to size the ore-stuff; that is, when it has been crushed, particles of equal volume must be collected together, in order that they may be treated separately. For this purpose, riddles and classifers are used, and the ores of various sizes are treated by different machines, whether jiggers or budd1es.l The operations should be so conducted as to separate the marketable minerals in as large grains as possible. The reduction 1 “The Dressing of Lead Ores.” By Thomas Sopmith, Jun., M. Inst. C.E. Min. Proo. Inst. C.E. vol. sxx. p. 106. Downloaded by [ Syracuse University] on [12/09/16]. Copyright © ICE Publishing, all rights reserved. Papers.] LUKIS ON THE SEPARATIOX OF GALENA AND BLENDE. 359 to absolute fineness should be gradual, and intermediate dressing operationsresorted to, for the finerthe particles through sub- division the more difficult and costly become the dressing opera- tions, and the greater the loss of minerals. In the present case the ore-stuff is crushed to pass through a riddle having square holes of 44 millimetres (0.18 inch). Jiggers are used as far aspossible to separate the minerals from their gangue, as they entail only one-tenth the cost of buddle- work, as regards labour, and less loss of mineral. Ore-stuff that would pass through a riddle, with holes 4 millimetre (0.02 inch) in diameter, could be jigged perfectly well, if freed from dimes. Ore-stuff that cannot be jigged is divided into twoclaases, ‘‘ fines ” and “ dimes,” and is dressed by budding. The rich ‘‘ heads ” of buddles, when concentrated to about 60 per cent. of metallic lead far galena, or blende of about 42 per cent. of metallic zinc, are worked by tossingand packing in a kieve or dolly, so as to obtain marketable ores of about 69 per cent. Pb, and 48 per cent. Zn respectively. This operation of ore-dressing, briefly alluded to, is divided into eight sections : (1) Picking for Prills ; (2) Breaking and crushing ; (3) Sizing and classifying ; (4) Jigging ; (5) Buddling ; (6) Re- crushing, pulverizing, and dressing chatts; (7) Dollying, or tossing andworking the flat-buddle ; and (8) Treatingand collecting dimes. 1. Picking for Pri1lS.-At the Sentein mines the ores were too intimately mixed torender picking of practicalvalue; but at many mines, especially those whose ores are rich in silver, this process is most serviceable, and is therefore mentioned here. The ore-stuff is tipped in toa large masonry hopper, A, Plate 7, Figs. 1, at thebottom of which cast-iron plates,B, are placed, and a revolvingpicking-table might be alsoused. The ore-stuff is washed by a jet of water from a hose, enabling the workmen to quickly distinguish and pick out the. prills orpieces of virgin galena or blende, as they rake the ore over the plates towards the grating, W. The plates, B, are so arranged as to allow the water to run off into a launder below, carrying with it fine particles of ore and dimes. This water passes through the doubletrommel, E, and thence to the dressing-floors, whereits contents are treated. Theprills being put to oneside are again picked over before sampling for market. 2. Breaking and crushing.-The ore-stuff is next raked over the grating, W, made of flat-iron bars, 3 inches deep and 4 inch thick, set on edge 4 centimetres (1 -57 inch) apart. The ore that passes Downloaded by [ Syracuse University] on [12/09/16]. Copyright © ICE Publishing, all rights reserved. 360 LUEIS ON THE SEPARATION OF GALENAAND BLENDE. [Fclccted between these barsis conducted by a launder, in which water flows, to tho double trommel, E, Plate 7, Figs. 1. This double trommel has an inner sieve, with holes 2 centimetres (0.79 inch) square, and an outer sieve, with holes 43 millimetres (0.18 inch) square. Theinner sieve is merely to protect theouter sieve from un- necessary wear. The ore thatwill not pass throughthe outer sieve is conducted in a launder to the crushing-rolls, D. The fine stuff that passes throughthe outer sieve goes at once tothe dressing-floors. The roclc and stones that remain on the grating, W, are put intothe stone-breakers, C,, C,, wherethey are broken into fragments that willpass through a ring 4 centimetres (1 -57 inch) in diameter.These fragments also go intothe double trommel with the small stuff that has passed through the grating, the fine ore-stuff going to the dressing-floors, the coarse to the crushing- rolls. The stone-breakers at Senteinare of two sizes. The smaller one, C,, for medium-sized stones, has a mouth 25 centi- metres (9 84 inches) long by 15 centimetres (5 * 91 inches) wide. The larger one, C,, for large stones, has a mouth 50 centimetres (19 * 68 inches) by 25 centimetres (9 84 inches). The faces of the jaws areof cast-iron, chilled to a depth of 3 centimetres(1 18 inch) ; the wearing edges of the toggles, and the bearings in which they work, are also chilled. Only two such stone-breakerswere used at Sentein,but they were insufficient for the work. Thelarge stone-breaker was driven by belting from a water-wheel, 14 feet in diameter and 3 feet breast, and it often had to be worked day and night to keep one-half of the floors supplied with ore-stuff during the day. With an additional pair of stone-breakers, such dressing-floors would be amply supplied withore-stuff. The quantity of stuff that may be crushed by rolls inany given time depends upon the size to which the ore-stuff has been first reduced by the stone-breakers, and it was found that the fragments should be able to pass through a ring from 4 to 5 csntimetres (1.57 to 1-97inch) in diameter. The crushing-rolls at Sentein were three in number, one G1 cen- timetres (24.02 inches) in diameter by 40.5 centimetres (15.95 inches) wide, and two others, each 38 centimetres (14.96 inches) indiameter by 33 Centimetres (12.99 inches) wide. It was found that, with theassistance of the small stone-breaker, the largo rolls could do nearly as much work as the two small ones, one of which wasassisted by the largestone-breaker. In the proposed dressing-floors (Plate 7, Figs. 1) rolls G8 centi- metres(26.77 inches) in diameter by 46 centimetres(18.11 Downloaded by [ Syracuse University] on [12/09/16]. Copyright © ICE Publishing, all rights reserved. Papers.] LUEIS ON THE SEPARATION OF GALENA AND BLENDE. 361 inches) inwidth are designated asbeing more efficient. These rolls consist of threeparts : theshafting, 15 centimetres (5 91 inches) square, of wrought-iron; the core, which should be well keyed on to the shafting and the same width as the roll, is of cast-iron, not chilled; and the ring, of cast-iron, with the face chilled to a depth of 3 centimetres (1 18 inch),about 8 centi- metres (3.15 inches) thick, with grooves 2 centimetres (0.79 inch) deep and 2 centimetres (0.79 inch) in width diagonallyacross the face, half way across; six grooves in one half, alternating with six grooves in the other half of the face. These grooves do not continue tothe edge of the face, butto within 3 Centimetres (l *l8inch) of it. The core is made about 3 centimetres (1* 16 inch) less in diameter than the inside diameter of the ring, so that the space between may be wedged up with dry deal wedges, driven in from both sides, which are then keyed up with small soft iron wedges. To keep the rolls tightly pressed together when working, levers and a balance-box were found to answer better than springs or india-rubber. India-rubber cushions aoon deteriorate, and work- men do not pay enough attention tothem. The rollsworked better when only one roll was connected with the driving-shaft, thesecond roll working byfriction on the first. By adopting thismethod more work was done than when either equal ordifferential gearing con- nected the two rolls, and lessdriving-power was required.
Details
-
File Typepdf
-
Upload Time-
-
Content LanguagesEnglish
-
Upload UserAnonymous/Not logged-in
-
File Pages20 Page
-
File Size-