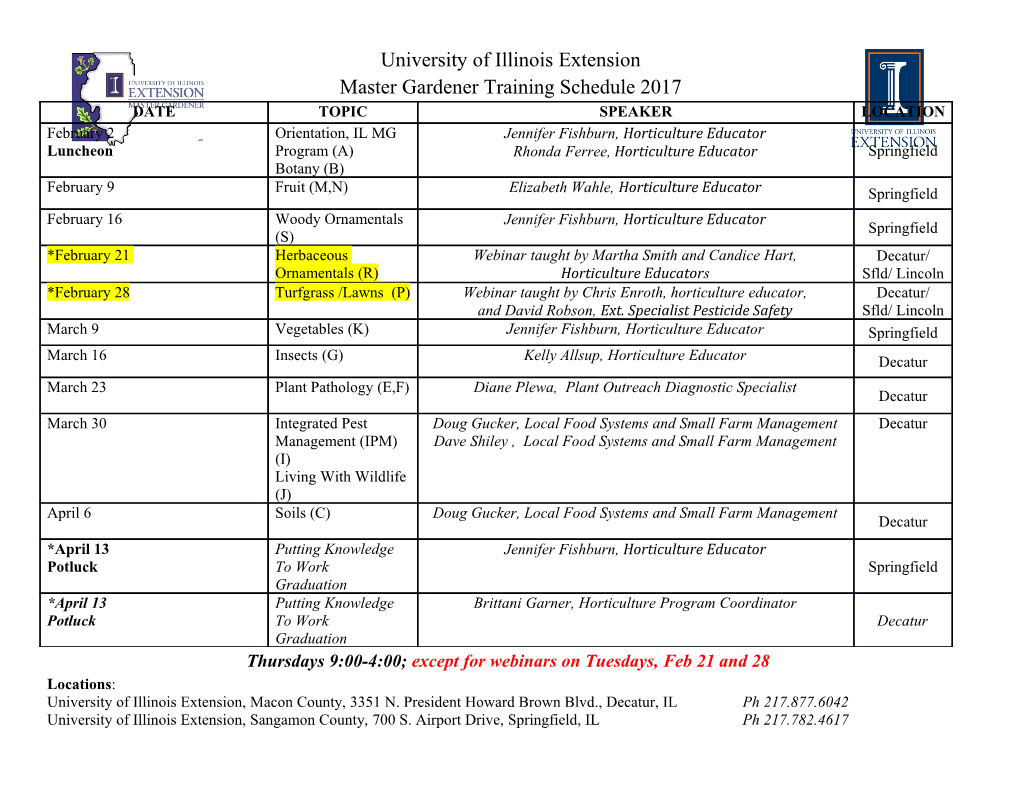
NASA Technical Paper 2969 1990 NASA Supercritical Airfoils A Matrix of Family-Related Airfoils Charles D. Harris Langley Research Center Hampton, Virginia National Aeronautics-and Space Administration Office of Management Scientific and Technical Information Division Summary wind-tunnel testing. The process consisted of eval- A concerted effort within the National Aero- uating experimental pressure distributions at design and off-design conditions and physically altering the nautics and Space Administration (NASA) during airfoil profiles to yield the best drag characteristics the 1960's and 1970's was directed toward develop- over a range of experimental test conditions. ing practical two-dimensional turbulent airfoils with The insight gained and the design guidelines that good transonic behavior while retaining acceptable were recognized during these early phase 1 investiga- low-speed characteristics and focused on a concept tions, together with transonic, viscous, airfoil anal- referred to as the supercritical airfoil. This dis- ysis codes developed during the same time period, tinctive airfoil shape, based on the concept of local resulted in the design of a matrix of family-related supersonic flow with isentropic recompression, was supercritical airfoils (denoted by the SC(phase 2) characterized by a large leading-edge radius, reduced prefix). curvature over the middle region of the upper surface, and substantial aft camber. The purpose of this report is to summarize the This report summarizes the supercritical airfoil background of the NASA supercritical airfoil devel- development program in a chronological fashion, dis- opment, to discuss some of the airfoil design guide- lines, and to present coordinates of a matrix of cusses some of the design guidelines, and presents family-related supercritical airfoils with thicknesses coordinates of a matrix of family-related super- critical airfoils with thicknesses from 2 to 18 percent from 2 to 18 percent and design lift coefficients from and design lift coefficients from 0 to 1.0. 0 to 1.0. Much of the discussion pertaining to the fun- damental design concepts is taken from reference 1 Introduction and unpublished lectures on supercritical technology presented by Richard T. Whitcomb in 1970. In- A concerted effort within the National Aero- formation on the development of supercritical air- nautics and Space Administration (NASA) during foils and earlier publications were originally clas- the 1960's and 1970's was directed toward develop- sified confidential but have since been declassified. ing practical airfoils with two-dimensional transonic Reference 2 discusses potential benefits of applying turbulent flow and improved drag divergence Mach supercritical airfoil technology to various types of air- numbers while retaining acceptable low-speed max- craft and flight programs to demonstrate such appli- imum lift and stall characteristics and focused on a cations. Table I indicates some of the major mile- concept referred to as the supercritical airfoil. This stones in the development of supercritical airfoils. distinctive airfoil shape, based on the concept of local The high maximum lift and docile stall behavior supersonic flow with isentropic recompression, was observed on thick supercritical airfoils generated an characterized by a large leading-edge radius, reduced interest in developing advanced airfoils for low-speed curvature over the middle region of the upper surface, general aviation application. Starting in the early and substantial aft camber. 1970's, several such airfoils were developed. Empha- The early phase of this effort was successful in sis was placed on designing turbulent airfoils with low significantly extending drag-rise Mach numbers be- cruise drag, high climb lift-to-drag ratios, high maxi- yond those of conventional airfoils such as the Na- mum lift, and predictable, docile stall characteristics. tional Advisory Committee for Aeronautics (NACA) During the mid 1970's, several medium-speed air- 6-series airfoils. These early supercritical airfoils (de- foils were developed that were intended to fill the gap noted by the SC(phase 1) prefix), however, experi- between the low-speed airfoils and the supercritical enced a gradual increase in drag at Mach numbers airfoils for application on light executive-type air- just preceding drag divergence (referred to as drag planes. These airfoils provided higher cruise Mach creep). This gradual buildup of drag was largely as- numbers than the low-speed airfoils while retaimng sociated with an intermediate off-design second ve- good high-lift, low-speed characteristics. locity peak (an acceleration of the flow over the rear References 3 to 12 document the research effort upper-surface portion of the airfoil just before the fi- on NASA low- and medium-speed airfoils. nal recompression at the trailing edge) and relatively weak shock waves above the upper surface. Symbols Improvements to these early, phase 1 airfoils re- sulted in airfoils with significantly reduced drag creep characteristics. These early, phase 1 airfoils and the Cp pressure coefficient, qoo improved phase 1 airfoils were developed before ad- equate theoretical analysis codes were available and Cp,soni c pressure coefficient corresponding to resulted from iterative contour modifications during local Mach number of 1.0 airfoil chord, distance along refer- SC(3)-0710 supercritical (phase 3)--0.7 design ence line from leading edge to trail- lift coefficient, 10 percent thick ing edge Development of Supercritical Airfoils Cd section drag coefficient Cl section lift coefficient Slotted Supercritical Airfoil am section pitching-moment coefficient In the early 1960's, Richard T. Whitcomb of the about the quarter chord Langley Research Center proposed, on the basis of intuitive reasoning and substantiating experimenta- Cn section normal-force coefficient tion, an airfoil shape (fig. 1) with supersonic flow K curvature of airfoil surfaces, over a major portion of the upper surface and sub- d2y/dx 2 sonic drag rise well beyond the critical Mach num- ber (ref. 13). The airfoil had a slot between the up- M free-stream Mach number per and lower surfaces near the three-quarter chord m slope of airfoil surface, dy/dx to energize the boundary layer and delay separation on both surfaces. It incorporated negative camber p pressure, psf ahead of the slot with substantial positive camber rearward of the slot. Wind-tunnel results obtained q dynamic pressure, psf for two-dimensional models of a 13.5-percent-thick Rc Reynolds number based on free- airfoil of the slotted shape and a NACA 64A-series stream conditions and airfoil chord airfoil of the same thickness ratio indicated that for a design-section normal-force coefficient of 0.65 the SC supercritical slotted airfoil had a drag-rise Mach number of 0.79 TE trailing edge compared with a drag-rise Mach number of 0.67 for the 64A-series airfoil. The drag at a Mach number tic thickness-to-chord ratio just less than that of drag rise for the slotted air- x distance along airfoil reference line foil was due almost entirely to skin friction losses measured from leading edge and was approximately 10 percent greater than that for the 64A-series airfoil. The slotted airfoil shape distance normal to airfoil reference also significantly increased the stall normal-force co- line efficient at high subsonic speeds. The pitching- moment coefficients for the slotted shape were OL angle of attack substantially more negative than those for more con- Subscripts: ventional airfoils. The rationale leading to the slotted shape was discussed in reference 13. Because the slot- DD drag divergence ted airfoil was designed to operate efficiently at Mach 1 lower surface numbers above the "critical" Mach number (the free- stream Mach number at which local sonic veloci- u upper surface ties develop) with an extensive region of supersonic (x) free-stream conditions flow on the upper surface, it was referred to as the "supercritical airfoil." Reference 14 indicated that Airfoil designation: the gains obtained for this two-dimensional slot- ted airfoil shape were also realized for _. three- The airfoil designation is in the form SC(2)-0710, dimensional swept wing configuration that incorpo- where SC(2) indicates supercritical (phase 2). The rated the airfoil shape. next two digits designate the airfoil design lift co- efficient in tenths (0.7), and the last two digits desig- Integral Supercritical Airfoil nate the airfoil maximum thickness in percent chord (10 percent). It was recognized that the presence of a slot increased skin friction drag and structural complica- SC(1)-0710 supercritical (phase 1)--0.7 design tions. Furthermore, both two-dimensional and three- lift coefficient, 10 percent thick dimensional investigations of the slotted airfoil indi- cated that the shape of the lower surface just ahead SC(2)-0710 supercritical (phase 2)--0.7 design of the slot itself was extremely critical and required lift coefficient, 10 percent thick very close dimensional tolerances. Becauseof thesedisadvantages,an unslottedor free flow had been accomplished, it was decided that integralsupercriticalairfoil (fig. 1) wasdevelopedin since aircraft must be efficient over a range of oper- the mid 1960's.Theresultsof the first workon the ating conditions, a shock-free point-design flow was integralairfoilweregivenlimiteddistributionin 1967 impractical. It was believed that it was more im- in aconfidentialLangleyworkingpaper.This paper portant to design airfoils
Details
-
File Typepdf
-
Upload Time-
-
Content LanguagesEnglish
-
Upload UserAnonymous/Not logged-in
-
File Pages76 Page
-
File Size-