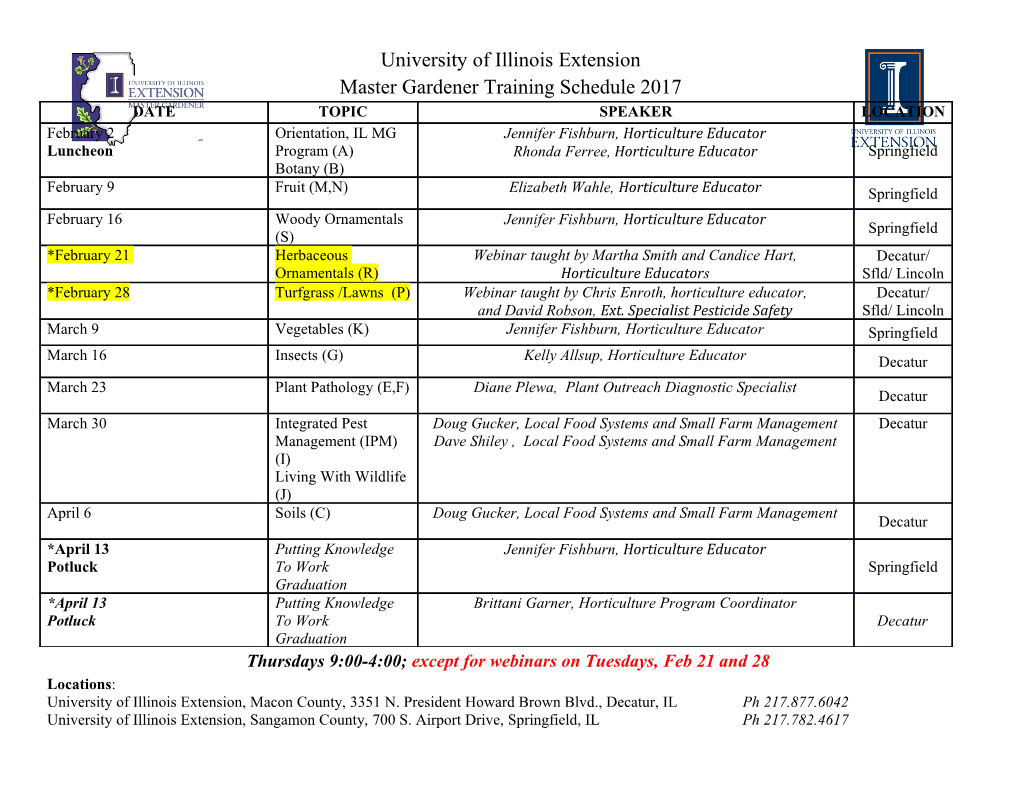
LOW ALLOY STEEL SUSCEPTIBILITY TO STRESS CORROSION CRACKING IN HYDRAULIC FRACTURING ENVIRONMENT Thesis Submitted to The School of Engineering of the UNIVERSITY OF DAYTON In Partial Fulfillment of the Requirements for The Degree of Master of Science in Chemical Engineering By Ezechukwu J. Anyanwu Dayton, OH May, 2014 LOW ALLOY STEEL SUSCEPTIBILITY TO STRESS CORROSION CRACKING IN HYDRAULIC FRACTURING ENVIRONMENT Name: Anyanwu, Ezechukwu John APPROVED BY: ______________________ ________________________ Douglas C. Hansen, Ph.D. Sean C. Brossia, Ph.D. Advisory Committee Chairman Research Advisor Research Advisor and Professor Senior Vice President and Chemical and Materials Engineering Senior Principal Engineer DYCE USA ________________________ Robert J. Wilkens, Ph.D., P.E. Committee Member Professor Chemical and Materials Engineering _______________________ ________________________ John G. Weber, Ph.D. Tony E. Saliba, Ph.D. Associate Dean Dean, School of Engineering School of Engineering and Wilke Distinguished Professor ii ABSTRACT LOW ALLOY STEEL SUSCEPTIBILITY TO STRESS CORROSION CRACKING IN HYDRAULIC FRACTURING ENVIRONMENT Name: Anyanwu, Ezechukwu John University of Dayton Research Advisors: Dr. Douglas C. Hansen Dr. Sean C. Brossia The pipelines used for hydraulic fracturing (aka. “fracking”) are often operating at a pressure above 10000psi and thus are highly susceptible to Stress Corrosion Cracking (SCC). This is primarily due to the process of carrying out fracturing at a shale gas site, where the hydraulic fracturing fluid is pumped through these pipes at very high pressure in order to initiate fracture in the shale formation. While the fracturing fluid is typically more than 99% water, other components are used to perform various functions during the fracturing process. Research into the occurrence of SCC reveals that SCC is engendered by a number of factors, of which two main contributors are stress in iii the pipe steel and a particular type of corrosive environment in contact with the pipeline in the service setting. The variety of fracturing fluid formulas which could be used and the insufficient reported information about the fracturing fluid chemistry makes it very important to carry out analysis to ensure the integrity of the pipelines used for this process. The current research described here is focused on the evaluation of the susceptibility of low alloy steel (AISI 4340) to stress corrosion cracking in different environments as it relates to hydraulic fracturing fluid chemistry and operating conditions. These different environments are achieved by varying the solution pH, the pH adjusting agent and the applied stress. Electrochemistry and stress measurements showed that at near neutral pH solution, AISI 4340 showed a higher SCC susceptibility in solutions where Na2CO3 was used as the pH adjusting than in solutions where NaOH was used as the pH adjusting agent. Scanning electron microscopy and Auger electron spectroscopy was used to analyze the oxide film in solution with the two pH adjusting agents at a pH of 7. Depth profiles of the passive film formed in a solution with pH adjusted to 7 using NaOH pH adjusting agent suggests the presence of a complex, FeOCl, which dissolves actively and thus reduces the SCC susceptibility of AISI 4340 in this environment. It is inferred from the SEM image of AISI 4340 material after testing and stress measurements showed that low alloy steel is more susceptible to SCC in solutions with Na2CO3 as the pH adjusting agent than solutions with NaOH pH adjusting agent especially at near neutral pH. Whereas, at high pH environment AISI 4340 showed a higher SCC susceptibility in solution with NaOH as the pH adjusting agent. iv ACKNOWLEDGEMENTS This thesis would not have been accomplished without the support of so many people. In order to show them how grateful I am for their kindness, I wish to acknowledge them. First I would like to thank my thesis advisors, Dr. D. C. Hansen and Dr. S. C. Brossia for their financial generosity, extraordinary patience and their time which definitely contributed a whole lot to this work. I also want to thank Dr. Robert Wilkens for his role in making this work come to conclusion. I also want to thank the company that sponsored the major part of this work, DET NORSKE VERITAS (DNV) Columbus, for their generosity and support in terms finances and other equipment to carry out my experimental work. I would also like to extend my thanks to Joe Gerst of DNV Columbus and Steven Goodrich of University of Dayton Research Institute (UDRI) for their invaluable assistance with the slow strain rate tests, and also Kenny Evans for his inputs in my electrochemistry measurements. My warmest thanks goes to my past and present lab group, William Nelson, Lu Han, Phil, Rachel, Yuxin, Yaqiu, Dr. Yuhchae Yoon, Dr. Leanne Petry, for creating a very friendly and happy working environment. Also my thanks go to the people of DNV, v Ashiwini, Noi, Barry, Kris, Beth, Nicky, Feng and others for also making my experience at DNV a very memorable one. I would like to extend my special thanks to my family who have been strongly behind me and for their love and belief I am able to push further in my academic pursuit, namely Chief Sir and Dr. Lady H. E. Anyanwu, Mr. and Mrs. Ben Anunne, Arch. and Mrs. Ikenna Anyanwu, Arch and Mrs. Julius Egbeogu, Mr. and Mrs. Chino Ilechukwu, Engr. and Mrs. Ceejay Anyanwu, Rev. Sr. Dr. C. Osuagwu, Rev. Fr. Dr. Dennis Osuagwu and Rev. Fr. Dr. Reginald Ejikeme. Finally, I would like to thank Chinenye for her love and belief in me. I dedicate this work to the memories of Dr. N. I. Onuoha. vi TABLE OF CONTENTS ABSTRACT…………………………………………………………………………iii ACKNOWLEDGEMENTS…………………………………………………………v TABLE OF CONTENTS…………………………………………………………... vii LIST OF FIGURES……………………………………………………………….. x LIST OF TABLES…………………………………………………………………. xv NOMENCLATURE……………………………………………………………….. xvi CHAPTER 1……………………………………………………………………….. 1 INTRODUCTION…………………………………………………………………. 1 1.1 Background…………………………………………………………………….. 1 1.2 Fracturing Fluid Chemistry…………………………………………………….. 2 1.3 Literature Review ………………………………………………………………4 1.4 Hypotheses………………………………………………………………………9 vii CHAPTER 2……………………………………………………………….. ……....11 MATERIALS AND METHODS………………………………………………….. 11 2.1 Test Materials and Sample Preparation………………………………………...11 2.2 Electrochemical Testing in Environment with Varying Chloride Ion Concentration………………………………………………………………………. 13 2.3 Electrochemical Testing in Simulated Fracturing Fluid Solution………………16 2.4 Post Test Analysis ……………………………………………………………... 18 2.5 Stress Tests in Simulated Fracturing Fluid Solution…………………………... 19 2.6 Metallographic Analysis ……………………………………………………... 24 CHAPTER 3……………………………………………………………….. ……... 25 RESULTS………………………………………………………………….. ……... 25 3.1 Electrochemistry in Environment with Varying Chloride Ion Concentration….25 3.2 Electrochemistry in Simulated Fracturing Fluid Environment………………… 32 3.3 Slow Strain Rate Test Measurement (SSRT) in Fracturing Fluid Environment..36 3.4 Crack Microstructure………………………………………………………….. 44 3.5 Slow Strain Rate Tests at Potentials Close to the Ecorr………………………… 45 3.6 Long Open Circuit Potential (OCP) Measurement…………………………….. 47 viii 3.7 Static Load Test……………………………………………………………….. 47 3.8 Post Test Analysis……………………………………………………………… 52 CHAPTER 4……………………………………………………………….. ……....62 DISCUSSION………………………………………………………………............ 62 4.1 Effect of Chloride Ion Concentration on the Passivation Behavior of AISI 4340………………………………………………………………………….. 62 4.2 Electrochemical Behavior of AISI 4340 in Simulated Fracturing Fluid Solution……………………………………………………………………………. 67 4.3 Relating Test Environment to Field Condition………………………………… 71 4.4 Static Load Test Below and Above Yield……………………………………… 72 4.5 Surface Film Analysis………………………………………………………….. 73 4.6 Conclusion……………………………………………………………………... 74 REFERENCES………………………………………………………………..…… 77 ix LIST OF FIGURES Figure 1: Tensile specimen with dimensional measurement………………………..12 Figure 2: Cylindrical sample for electrochemical measurement…………………....13 Figure 3: Slow Strain Rate Test (SSRT) cell assembly…….....…………………….21 Figure 4: Cyclic potentiodynamic polarization curve for AISI 4340 test in nitrate/chloride environment………………....………………….….....…………… 27 Figure 5: Sample after testing in 3.7M NaNO3 solution.….....…………………….. 28 Figure 6: Sample after testing in 3.7M NaCl & 3.7M solution NaNO3…………… 28 Figure 7: Sample after testing in 1M NaCl & 3.7M solution NaNO3………..……. 29 Figure 8: Sample after testing in 3.7M NaCl………………….…………………… 29 Figure 9: Cyclic potentiodynamic polarization curve for AISI 4340 test in varying chloride ion concentration.….......…………………………………………….…….30 Figure 10: Difference between the breakdown and free corrosion potential in the different chloride ion concentration environment….. ……………………………... 31 Figure 11: Sample after testing in 1M NaCl solution..….....………………………. 31 x Figure 12: Sample after testing in 0.1M NaCl solution...…...………………………31 Figure 13: Sample after testing in 0.01M NaCl solution.....……………………….. 32 Figure 14: Sample after testing in 0.001M NaCl solution......…………………..…. 32 Figure 15: Comparison of CPP curves in solution 2 and solution 3 at pH 7-10 and temperature 50°C...……………..……………………………………………... 33 Figure 16: CPP curves in solution 3 at pH 7-10 and temperature 25°C.................... 34 Figure 17: Ecorr summary in solution 3 with varying pH and at temperature 25°C and 50°C……………………………………………………………...……..………35 Figure 18: Polarization resistance summary in solution 3 with
Details
-
File Typepdf
-
Upload Time-
-
Content LanguagesEnglish
-
Upload UserAnonymous/Not logged-in
-
File Pages99 Page
-
File Size-