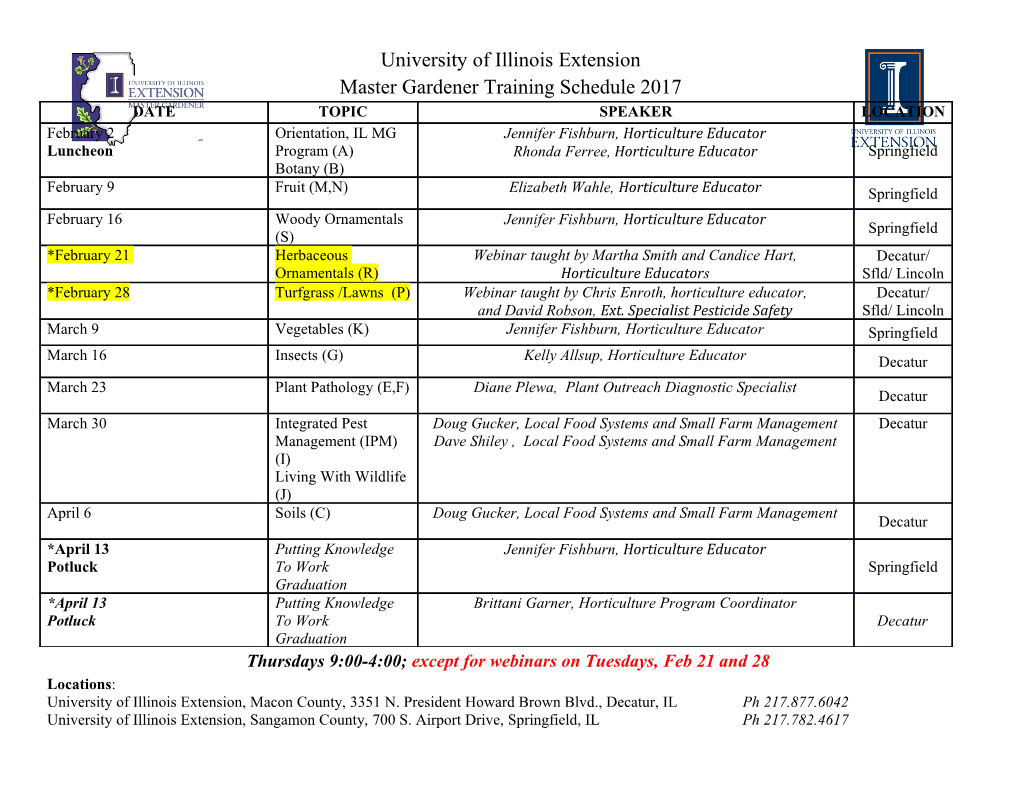
Construction of a Computational Model of a Go-Kart for Dynamic Analysis Multibody model construction and theoretical analysis Jonathan Mikler A. Advisor: Andres Leonardo Gonzales Mancera Ph.D A thesis presented to apply for the degree of B.Sc Mechanical Engineer Department of Mechanical Engineering Los Andes University Bogot´a,Colombia December 2018 Abstract A multibody model was developed in the Msc-Adams/Car software to recreate an electric Go- Kar. The prototype vehicle was built on top of a ICE chassis, where an PMAC motor and the subsequent powertrain were installed. The model was created by examining the real prototype and modelling its components to a basic but satisfying level of details, taking into account each individual weight and position. The simulations carried out were a step steer were for most cases was ran at 30 km/h (48 mph) offered results on the dynamic response of the vehicle to this simple maneuver and simple analysis of the consistency and congruence with theory was possible. Weight distribution for both axles, as well as slip angle development were observed in the simulations, and since the vehicle was cataloged as understeer, this results were consistent with the theory. lastly, the characteristic speed was validated through multiple simulation ran at different speeds, where the maximum yaw rate was observed at a speed close to the theoretical characteristic speed. 2 Dedication This work is completely dedicated to my family, who in different ways contributed, promoted and celebrated my passing through engineering school. To my parents who's trust never quivered, to my siblings, who's support for me was felt at every step and to my grandparents, who's love and pride played a much more subtle but equally powerful role in my life. 3 Acknowledgements I want to thank on first account to my work advisor, Andres Gonzales Mancera, for accepting me when I struggled to find a supervisor for my bachelor thesis. This meant a big leap of faith which I worked hard to meet the expectations that came with it. Furthermore, this work could not have been done without the constant help of many parties. First and foremost, the support staff at MSC software, embodied primarily by Lucas Fazecas, signified an invaluable help, without which I would not have gotten as far as i did. The support staff at the advance simulation room also helped in some measure and therefore a warm thank you is in order. Lastly, I want to thank the mechanical engineering department of my school, specially the teachers that contributed to my formation along the 4 and a half years spent in the campus. With out their open mindedness, and their will to enable students explore a variety of different topics somehow distant from the mainstream research topics on campus, my project would not have been possible. 4 Contents 1 Introduction 8 1.1 Motivation . 8 1.2 Previous work . 8 1.3 Objectives . 9 1.3.1 General Objective . 9 1.3.2 Specific objectives . 9 2 Background theory 10 2.1 Vehicle Dynamics Basics . 10 2.1.1 Forward Vehicle Dynamics . 11 2.1.2 Cornering . 13 2.2 Tire characteristics . 18 2.2.1 The contact patch pressure . 18 2.2.2 Tire forces and moments . 19 2.3 Multibody System approach . 22 2.3.1 modelling basics . 23 2.3.2 Tire modelling . 27 2.3.3 Solving linear and non-linear equations . 28 3 Model development 30 3.1 The Go-Kart model . 30 3.1.1 The Kart's Dynamic Characteristics . 31 3.2 MBS modelling . 34 3.2.1 Part modeling . 34 3.2.2 Topology . 37 4 Summary of achievements 39 4.1 results and interpretations . 39 4.2 Conclusions . 44 4.3 Challenges and limitations . 45 4.4 Future work . 45 5 List of Figures 2.1 SAE Vehicle axis system (Automotive Engineers 2008) and (Gillespie 1994) . 10 2.2 Alternative coordinate axis system (Jazar 2014) . 11 2.3 Inclined scenario for CoG determination (Jazar 2014) . 12 2.4 Vehicle's condition on steady state cornering(Bradley 2018) . 13 2.5 Lateral force's dependency on slip angle (Gillespie 1994) . 14 2.6 Lateral force dependency on normal force (Jazar 2014). 15 2.7 Cornering of a bicycle model (Gillespie 1994) . 15 2.8 Change of steer angle with speed for a fixed radius turn. Taken from (Gillespie 1994) 17 2.9 Yaw gain as a function of speed. Taken from (Gillespie 1994) . 18 2.10 Pressure distribution on a stationary tire (Blundell and Harty 2014) . 19 2.11 Normal stress (pressure) on the contact patch due to pressure (Jazar 2014) . 19 2.12 Vertical forces wheel model . 20 2.13 Tire lateral deflection . 20 2.14 Contact patch deflection, asymmetric for a turning tire (Jazar 2014) . 21 2.15 Generation of lateral force and aligning moment due to slip angle (Blundell and Harty 2014). 21 2.16 Development of the camber thrust lateral force . 22 2.17 MSC Interface for creating parts . 23 2.18 Information display for reviewing and editing inertial properties . 24 2.19 Common examples of joints Blundell and Harty 2014 . 25 2.20 Example of joint implementation . 25 2.21 Example of a couple joint implemented in this work's model (Blundell and Harty 2014) . 26 2.22 Spring and damper model for a tire (Blundell and Harty 2014) . 27 2.23 Function shape for the "magic formula" . 28 3.1 E-Kart prototype . 30 3.2 Basic connections map of the developed prototype . 31 3.3 Lever arm steering mechanism (Jazar 2014) . 31 3.4 Go-Karts yaw rate gain and lat. accl. gain . 32 3.5 Front forces developed in a 16 m corner . 33 3.6 Rear forces developed in a 16 m corner . 33 3.7 Maximum cornering speed for different radii . 34 3.8 E-Kart MBS model . 34 3.9 Steering connection topology . 35 3.10 Basic connections map of the model's parts . 37 3.11 Model's detailed topology . 38 4.1 Steering wheel angular imposed motion . 39 4.2 Normal forces at the axles for a step steer maneuver . 40 4.3 Slip angles developed at the left side . 41 4.4 Slip angles at both rear and front axles . 41 4.5 Front wheels steered angles . 42 4.6 Lateral forces at both rear and front axles . 43 4.7 Yaw rates for different velocities . 44 6 List of Tables 2.1 Common joints and DOF removed by them . 27 3.1 Kart's principal characteristics . 30 3.2 Joint count for the steering system . 36 3.3 Rear axle part characteristics . 36 3.4 Joint count for the entire model . 36 3.5 Model parts and roles . 38 4.1 Maneuver parameters . 39 7 Chapter 1 Introduction 1.1 Motivation Multibody computational simulations are one of the modern engineering tools used to improve design in different areas. In automotive design, both commercial and competitive, they are used to improve the design proposals, reducing costs due to the clear advantages offered in contrast to trial and error methodologies. Cases such as the United States National Advanced Driving Simulator (NADS) (Heydinger et al. 2001) are recurrent in several divisions of the automotive industry as well as at the level of sports competition (CNN n.d.). However, the construction of these models is a monumental challenge in both reverse engineering and direct engineering. A high fidelity model implies complex mathematical approaches of all sub- systems of the vehicle, as well as an experimental validation of said models. The case of the NADSdyna model is recognized as a pioneer in the field (Pastorino et al. 2015). These models are the result of a balance between mathematical complexity (which implies an increase in computing capacity and difficulty of implementation) and reduction of complexities of the model in areas outside the focus of the particular system to be analyzed (EE and WW 2003). As a result, we have a tool that allows us to diagnose and predict behaviors and improvements in the design of vehicle prototypes in specific areas of its design. Within the context of Los Andes university, the team called Bogota Team Andes Uniandes (BTA in short), is the student group interested in automotive engineering applied to electric vehicles. Its activities revolve around an electric Kart that serves as a test and research bank. This electric kart plays a central role in the team's ability to test new designs and their effectiveness in real use conditions. It is precisely the potential offered by the computational simulations of a virtual model, which suggests the need for a virtual model of the prototype that can be subjected to dynamic track simulations, Furthermore, it is aligned with these interests, that the opportunity to conduct a bachelor thesis which revolves around the creation of a computational model of a kart type vehicle presents itself, alongside its coupling to a simulation ecosystem for dynamic behavior analysis. 1.2 Previous work Multibody simulation has been a research topic or a long time, even outside the automotive area. Within the university, relevant works have been carried out in this area. Among the most relevant is the dynamic modeling of a kart (Rojas 2003), which developed a highly detailed mathematical model in the Matlab - Simulink software and obtained results that allow predicting improvements in the performance of a vehicle by altering vehicle characteristics. Simulations of dynamic structural analysis were carried out in (Ardila 2014) and (Calderon 2004) where they obtained conclusions about torsional rigidity and deflection that serve as a guide for procedures to be carried out within this project.
Details
-
File Typepdf
-
Upload Time-
-
Content LanguagesEnglish
-
Upload UserAnonymous/Not logged-in
-
File Pages46 Page
-
File Size-