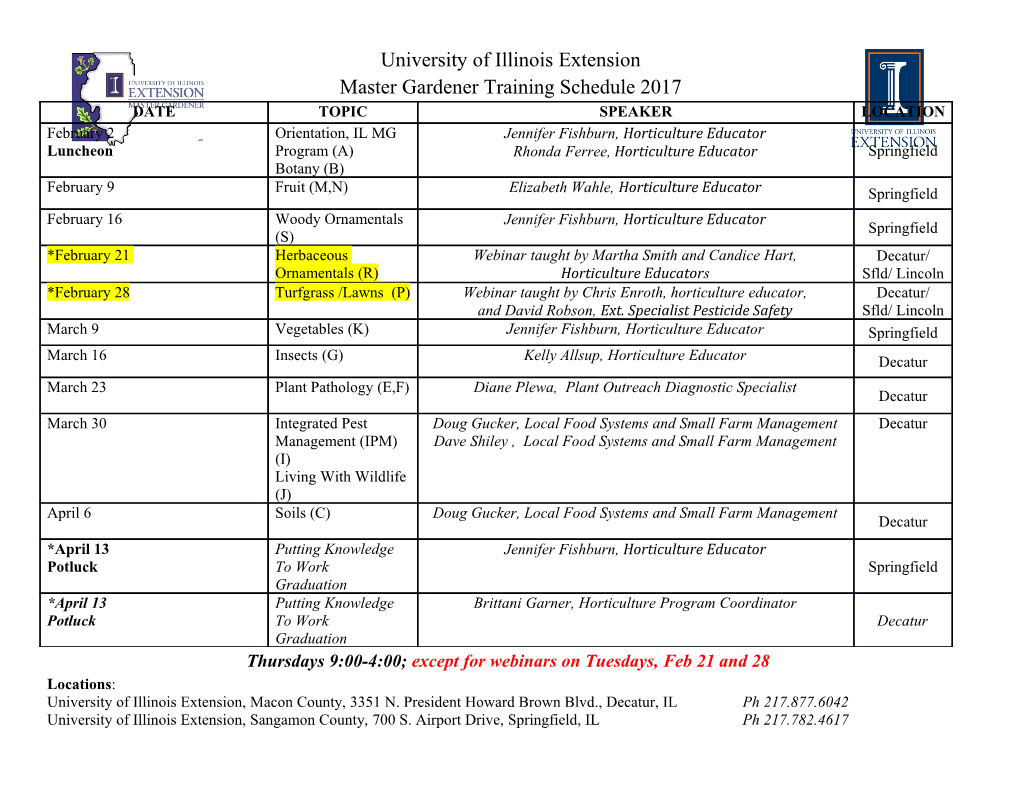
Effects of Intergrinding 12% Limestone with Cement on Properties of Cement and Mortar James Mohammadi, Warren South Journal of Advanced Concrete Technology, volume 14 ( 2016 ), pp. 215-228 Assessment of blended cements effectiveness against ASR by mortar and concrete expansion tests. Umberto Costa, Teresa Mangialardi, Antonio Evangelista Paolini Journal of Advanced Concrete Technology, volume 12 ( 2014 ), pp. 266-278 Sodium and Magnesium Sulfate Resistance of Mortars with Interground Limestone and Limestone Powder Replacing Cements Ittiporn Sirisawat , Lalita Baingam , Warangkana Saengsoy, Pitisan Krammart, Somnuk Tangtermsirikul Journal of Advanced Concrete Technology, volume 12 ( 2014 ), pp. 403-412 Decision-making on Increasing Limestone Content of General Purpose Cement Iman Mohammadi, Warren South Journal of Advanced Concrete Technology, volume 13 ( 2015 ), pp. 528-537 Journal of Advanced Concrete Technology Vol. 14, 215-228 May 2016 / Copyright © 2016 Japan Concrete Institute 215 Scientific paper Effects of Intergrinding 12% Limestone with Cement on Properties of Cement and Mortar James Mohammadi1 and Warren South2 Received 18 November 2015, accepted 11 May 2016 doi:10.3151/jact.14.215 Abstract This paper provides information concerning the results of test programme to investigate the properties and performance of Type General Purpose (GP) cement containing up to 12% limestone. Cement properties, including chemical and physical properties and mortar properties, such as compressive strength, drying shrinkage, and sulfate expansion were investigated comprehensively for effects of introducing higher limestone content to General Purpose (GP) cement. Test results showed that there is no significant effect on most properties due to increasing the limestone addition in cement from 7.5% to a maximum of 12%. 1. Background addition than the 7.5% allowed in the cement Standard AS 3972-2010. This study investigated an increase in the limestone con- tent of cement to provide more sustainable General Pur- 2. Literature review pose (Type GP) cement in Australia, without compro- mising the existing properties of concrete. To propose The literature review involved the effects of higher an increase in allowable clinker substitution up to 12% limestone content in cement on different properties of from the present 7.5% maximum, the current research cement and mortar. Different properties including set- programme on cement and mortar has drawn along with ting time, peak temperature rise, compressive strength, other studies examining properties of laboratory grade drying shrinkage and sulfate expansion were reviewed concrete (Mohammadi and South 2015), high-strength as follows: grade concrete (Mohammadi and South 2016) and con- (1) Cement Setting time: crete for aggressive environments (Mohammadi and Some studies showed substituting cement by limestone South 2016). In many other countries, as shown in Fig. increases setting times (Elkhadiri et al. 2002; Temiz and 1, cements with higher levels of limestone substitution Kantarcı 2014; Meddah et al. 2014; Dhir et al. 2007), have been in for a number of years in a wide range of whilst other investigations reported an opposite effects applications. However, in some countries such as Japan (Moir and Kelham 1999; Helal 2002; Kakali et al. 2000; the maximum allowable limestone content of cement is Vo gl i s et al. 2005). It was confirmed by most studied still limited to the maximum of 5%. that the change in setting times were limited when lime- In Australia, it has been proposed to change the level stone content was less than 15% (Irassar et al. 2011; of substitution in Type GP cement, the main cement Tsivilis et al. 1999). type in general use. This is due to the fact that the Aus- (2) Cement peak temperature rise: tralian Standard allows a small range of cements com- Published data on the influence of limestone on the heat pared to other countries, and is a relatively smaller di- of hydration gives some evidence to support the conten- verse market than, say, Europe or North America. There tion that fine limestone addition serves to accelerate is no ability to deliver a separate cement supply stream some cement hydration reactions as well as to form without significant capital investment, determined to be carbo-aluminate compounds. Where limestone is used upwards of $192 million based on current industry cost- as an addition to cement, heat of hydration is generally ings. The intent of the testing programme was to study increased (Praay et al. 1999; Tsivilis et al. 2002; Vuk et whether there is any detrimental effect on cement per- al. 2001; Thongsanitgarn et al. 2014). However, it is formance from the higher levels of limestone mineral noted that substitution of clinker with limestone fillers reduced the release of heat, height of the main peak or the total heat released (Marzouki et al. 2013; Irassar et 1 al. 2011). The particle size of limestone powder was Research Engineer, Cement Concrete & Aggregates found to have an influence on the heat of hydration both Australia (CCAA), Sydney, Australia. on the rate of heat and the total amount of heat release. *Corresponding Author, Thongsanitgarn et al. (2014) reported that the early-age E-mail: [email protected] 2 hydration rate was accelerated by the finer particle size, Director of Research and Technical Services, Cement while no significant effect was observed when particle Concrete & Aggregates Australia (CCAA), Sydney, size was 20μm or larger. Australia. J. Mohammadi and W. South / Journal of Advanced Concrete Technology Vol. 14, 215-228, 2016 216 Fig. 1 International perspective of Portland-limestone cements. (3) Mortar compressive strength: age for mortar samples, other studies has found almost Tsivilis et al. (1999) observed that up to 15% addition similar shrinkage between control samples and samples of limestone provided equal or improved mortar prepared with 15% limestone (Voglis et al. 2005). strength. Similar results observed by other investiga- Marzouki (2013) discussed that the limestone content in tions (Elkhadiri et al. 2002; Felekoğlu et al. 2006). cement has no real influence on shrinkage over longer However, it was reported that for high limestone con- time periods where the dry shrinkages are essentially tents over 15% mortar compressive strength reduced by equivalent regardless of the limestone filler ratio in the increasing limestone content (Dhir et al. 2007; İnan cement. Sezer 2012; Felekoğlu et al. 2006; Yılmaz and Olgun (5) Mortar sulfate expansion: 2008; Sprung and Siebel 1991; Kakali et al. 2000). Some studies concluded that the substitution of less than Nehdi et al (1996) showed that at 3-day tests, the com- 15% of cement with limestone showed no adverse effect pressive strength is little affected by the substitution of on sulfate performance of cements (Barkera and Hobbsb 10% and 15% of cement by limestone, while it was de- 1999; Gonzalez and Irassar 1977). Work in Brazil creased significantly for higher limestone contents. In showed improved performance of mortars containing up addition, Marzouki et al. (2013) reported mortar com- to 35% limestone exposed to a sodium sulfate solution pressive strength results for samples contained up to for up to 6 months (Tezuka et al. 1992). Other studies 15% limestone and for later ages and up to one year. It showed that at room temperature of 25ºC, no sulfate was found that the change from higher limestone con- attack was observed after a year of exposure (Kakali et tent was not significant in the later ages. In general, al. 2003; Torres et al. 2003; Skaropoulou et al. 2009). similar mortar compressive strength for limestone con- However, some researchers found that mortars contain- tent up to 15%, it can be summarised from the literature. ing high content of limestone from 15% to 30%, suf- Hoshino et al. (2006) reported that when limestone ce- fered from the thaumasite form of sulfate attack at low ment is used with blast furnace slag, the strength in- temperature of 5ºC (Kakali et al. 2003; Torres et al. creasing effect of blended limestone cement is more 2003; Skaropoulou et al. 2009; Justnes 2003; Irassar et pronounced compared to the ordinary Portland cement al. 2005). In general, it can be inferred from the litera- (OPC). It is reported to be attributed to the higher ture that external sulfate attack of mixtures containing amount of calcium aluminate hydrates generated in the limestone filler is firstly governed by mixture resistance blended slag contained system compared to the system to sulfate ion penetration rather than mix composition. without slag (Hoshino et al. 2006). Irassar (2009) reported that when limestone is used as (4) Mortar drying shrinkage: cement replacement, effective w/c ratio is the main vari- Limestone mineral addition has been found to decrease able affecting ion transport. Therefore, a low proportion the measured drying shrinkage by densifying the micro- (10%) of limestone causes no significant changes in structure and to lowering the water demand of the con- sulfate resistance of parent portland cement, while a crete (Dhir et al. 2007; McKinley et al. 2013; Felekoglu large proportion (15% or greater) may worsen sulfate and Baradan 2007). It was reported the observed reduc- performance (Irassar 2009). tion in shrinkage can be attributed to particle size distri- Other properties of cement such as fluidity of cement bution and reduction of Portland cement clinker in the paste has been discussed by Sakai et al. (2009). It was paste (Dhir et al. 2007; Bentz et al. 2009). Irassar et al. observed that a system with finely ground limestone (2011) noted that dilution effect of limestone when powders had a lower viscosity and higher fluidity of clinker is substituted with it causes a reduction of suspensions (Sakai et al. 2009). Costa et al. (2014) re- chemical shrinkage and heat released at early-age. Al- ported on the effect of limestone on alkali silica reaction though Rizwan (2012) showed higher early-age shrink- (ASR). No significant difference has been reported be- J.
Details
-
File Typepdf
-
Upload Time-
-
Content LanguagesEnglish
-
Upload UserAnonymous/Not logged-in
-
File Pages15 Page
-
File Size-