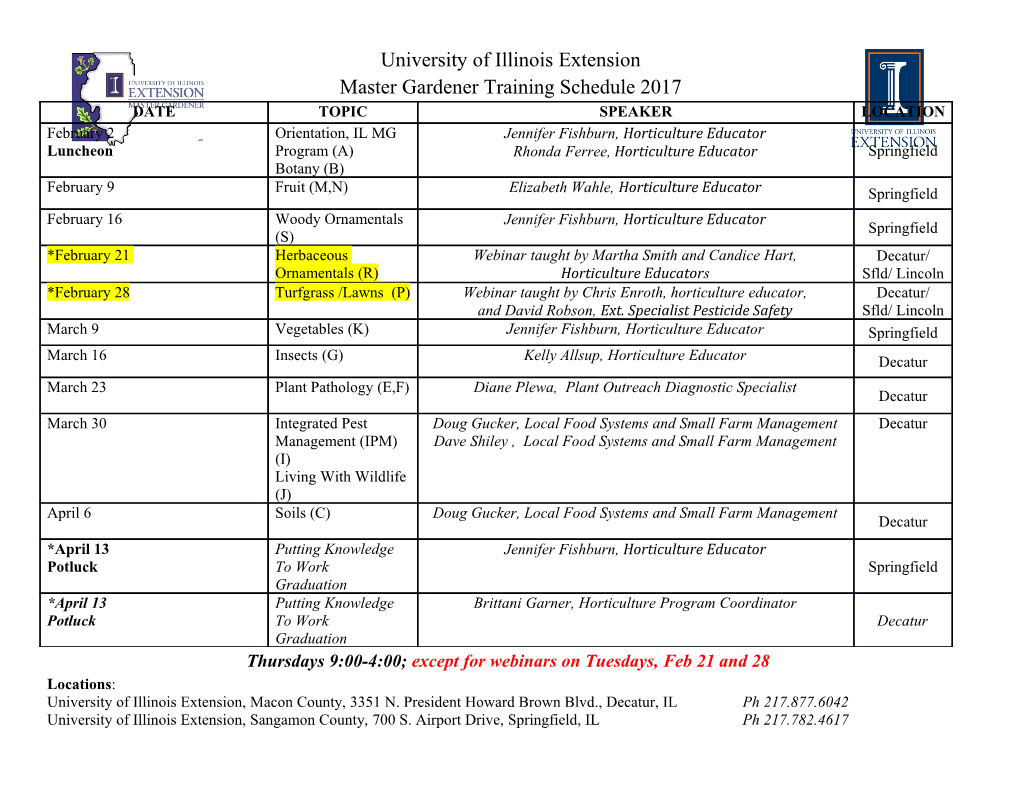
A.3 Friction Stir Processing of Aluminum Casting Alloys: Microstructure Manipulation/Surface Composite Fabrication Ning Sun and Diran Apelian Report No. 07-#2 1 PROJECT STATEMENT 1.1 OBJECTIVES Explore and evaluate the feasibility of friction stir processing in aluminum alloys, specifically to: 1. Manipulate the microstructure to refine or strengthen locally. 2. Investigate the potential of friction stir processing to form a particle-reinforced zone in standard Al cast components, by mixing and creating strengthening particles, and establish optimum processing conditions. 1.2 STRATEGY In order to achieve the above, the following methodology and strategies will be pursued: 1. Carry out a critical literature review. Learn the principles of friction stir processing as it applies to manipulate microstructure of Al alloys, the tool geometries that are appropriate for the intended purpose, and the applications that need to be considered. 2. Conduct friction stir processing experiments in two directions. First, confirm microstructure evolution that takes place during friction stir processing; verifying and validating some of the claims that have been made in the literature. Second, investigate surface composites fabrication via friction stir processing. Experimental parameters and tool geometries need to be designed. 3. Complete analysis of resultant microstructures using the latest available methodologies, as well as evaluate resultant mechanical properties. 4. Establish optimum parameters for both microstructure evolution and surface composite fabrication. 5. Investigate the opportunity to develop a predictive model in order to have the ability to simulate and analyze a-priori. 2 ACHIEVEMENTS TO DATE Appendix A: Literature review WORK PLAN Phase I ! Codify information on working principles of FSP tooling ! Select aluminum alloys A365, A380, 206 as experimental alloys. ! Carry out friction stir processing experiments using selected alloys, for a designed set of different processing parameters. ! Microstructure examination of FSP processed alloys. ! Analyze results based on different parameters. Phase II ! Carry out surface modification experiments by creating a particle reinforced zone for the selected alloys (as given above). ! Create particle reinforced zone by mixing-in strengthening particles via three methods: o Making a groove on the surface of the work-piece. Preparing second phase (strengthening particles) and emplacing into the groove. o Preparing slurry that contains the strengthening particles and painting it onto the surface of the particle-reinforced zone. o Preparing powder that contains strengthening particles, and putting the powder into a nozzle before FSP. The powder is injected into the FSP zone by a carrier inert gas simultaneously with FSP. ! Create particle reinforced zone by forming strengthening particle by in-situ chemical reactions with three methods: o Alloy + Reactant + Catalyst Particles + Secondary product o Pin tool + Reactant + Catalyst Particles + Secondary product o Reactant (1) + Reactant (2) + Catalyst Particles + Secondary product ! Microstructure examination of FSP processed alloys. ! Analyze results based on different parameters. ! Mechanical property evaluations. ! Establish optimum parameters for surface composites fabrication. 3 OPERATIONAL SCHEDULE FOR THE PROJECT Sep '07- Jan '08- Jun '08- Jan '09- Jun '09- Dec'07 May '08 Dec '08 May '09 Dec '09 Critical Lit Review (I) (I) Project Planning (I) Finalize Exp. Plan (I) (I) Execute Exp. Part I (II) (II) Execute Exp. Part II (II) (II) (II) Modeling (III) (III) (III) Thesis Write-up (IV) Thesis Defense (IV) Appendix A Literature review 1 TABLE OF CONTENTS 1 Introduction 1.1 Historical notes 1.2 Applications 1.2.1 Ship construction 1.2.2 Defense applications 2 Friction Stir Process 2.1 Working principles 2.2 The tool 2.3 Energy Considerations 2.3.1 Heat Generation 2.3.2 Different fraction of heat input from different parts 2.3.3 Work-piece contributions 2.4 Metal flow 2.4.1 Methods to measure metal flow pattern 2.4.2 Materials flow patterns 2.5 Friction stir welding vs. Friction stir processing 2.5.1 Similarities 2.5.2 Differences 3 Friction stir processing applications 3.1 Structure manipulation 3.1.1 Different microstructure zones 3.1.2 Grain size 3.1.3 Second-phase particles 3.1.4 Grain boundary morphology 3.1.5 Recrystallization and mechanisms 3.2 Superplasticity 3.2.1 Development of superplasticity 3.2.2 Processing parameters effect on superplasticity 3.2.3 Mechanisms 3.3 Surface composites 3.3.1 Development for surface modification 3.3.2 Effect of FSP processing parameters 3.4 Mechanical property improvements 3.4.1 Hardness 3.4.2 Tensile 3.4.3 Fatigue 2 4 Critical issues 4.1 Tool geometry 4.2 Tool wear 4.3 Overlap processing 4.4 Microstructure stability 4.5 FSP in other materials 5 Opportunities of FSP for cast components 6 References 3 1 Introduction 1.1 Historical notes Strong demand of weight reduction in vehicle and aircraft manufacturing industry urges the design of products employing light-weight materials. Al cast components have certainly contributed to these needs, even though there are challenges in having robust and always predictable resultant products [1-4]. There exist an opportunity to utilize advanced processing methods that enhance specific modulus, strength to weight ratio, fatigue strength and wear resistance. Chemical modification and thermal heat treatment [4-6] have certainly contributed to addressing some of these shortcomings [7-8], but there exists additional post-processing methods that ought to be investigated, such as friction stir processing. Friction stir processing (FSP) was generated in the late 90s, based on the principle of friction stir welding (FSW) [9]. Friction stir welding was invented at The Welding Institute (TWI) in UK by W. M. Thomas et al. in 1991 as a solid- state joining technique, and it was initially applied to aluminum alloys [10, 11]. The principle of FSW can be seen in Fig. 1 showing the FSW tool plunging and traversing on the workpiece [12]. A non-consumable rotating tool is employed, and the probe of the tool is applied to the abutting faces of the workpiece and rotated. While the tool is rotating, the workpiece is softened due to the heat generated by friction between the tool and the workpiece. In addition, plastic deformation of the workpiece does takes place. The plasticized region is around the immersed probe and at the interface between the shoulder of the tool and the workpiece [13]. FSP was developed in 1997 by Mishra et al.[9, 14]. In this case, a rotating tool is inserted in a monolithic workpiece (Fig. 2) [15], which is the main difference from FSW. In FSP the material undergoes intense plastic deformation at elevated temperatures, resulting in generation of locallized fine and equiaxed recrystallized grains [16-18]; the latter yields improvements in mechanical properties. 4 Figure 1: Welding tool plunge (left) and traverse (right) [12]. Figure 2: Schematic illustration of friction stir processing: a) rotating tool prior to contact with the plate; b) tool pin makes contact with the plate, creating heat; c) shoulder makes contact, restricting further penetration while expanding the hot zone; and d) plate moves relative to the rotating tool, creating a fully recrystallized, fine grain microstructure [15]. 5 1.2 Applications FSW/FSP has been used to produce high strain rate superplasticity [9, 19], surface composites on aluminum substrates [20], and homogenization of powder metallurgy aluminum alloys [21], microstructural modification of metal matrix composites [22], and property enhancement in cast aluminum alloys [23]. FSW technique is developed far more than FSP, and in real practice, FSW has been commercialized. In fact, FSW is licensed for over 170 users, including welding the seams of the aluminum main Space Shuttle external tank, Boeing Delta II and Delta IV Expendable Launch Vehicles and the Space X Falcon 1 rocket. A look at the history of production implementation of FSW (Table 1) [12] shows that the majority of production applications have involved joining extruded shapes to make useful products [24]. Table 1: Chronology of Production Application of FSW through 2004 [12]. 1.2.1 Ship construction FSW has been used to have lead [25], magnesium [26], steel [27], titanium [18], zinc, and copper [28] be welded continuously in Al. The unique properties of friction stir welds make possible some completely new structural designs with significant impact to ship design and construction [24]. Europe and Japan first demonstrated that the cost, durability and welding distortion could be improved via FSW; this is now widely accepted in the United States. For example, the US Navy highlighted FSW as one of the manufacturing technologies essential to 6 achieving the Littoral Combat Ship (LCS) Program’s strategy to reduce acquisition costs. With the planned 55 ship LCS class being a key part of the 313 ship Navy strategy, friction stir welding of aluminum panel structures is playing a key role in reducing LCS costs [29]. 1.2.2 Defense applications Wider applications of FSW and FSP have great value in weapons systems programs [29]. Apart from this, in army programs, new generation of ground combat vehicles-Future Combat System (FCS) could be developed by FSW or FSP. Because these vehicles must be lightweight, capable of transport by C-130 aircraft, aluminum alloys for improved properties is very useful, and these alloys can be produced by FSP. Moreover, in many conditions, it is required dissimilar alloys to be joined together, so FSW is an effective way to realize this end. 2 Friction Stir Process 2.1 Working principles Friction stir processing (FSP) has been developed by adapting the concepts of friction stir welding (FSW) [10]. The basic principle of FSP is remarkably simple [14]. It is a solid state processing [30]. The tool consists of a cylindrical shoulder and a non-consumable high strength pin at the end. The tool rotates at a certain speed and the pin is forced with a pre-determined load.
Details
-
File Typepdf
-
Upload Time-
-
Content LanguagesEnglish
-
Upload UserAnonymous/Not logged-in
-
File Pages47 Page
-
File Size-