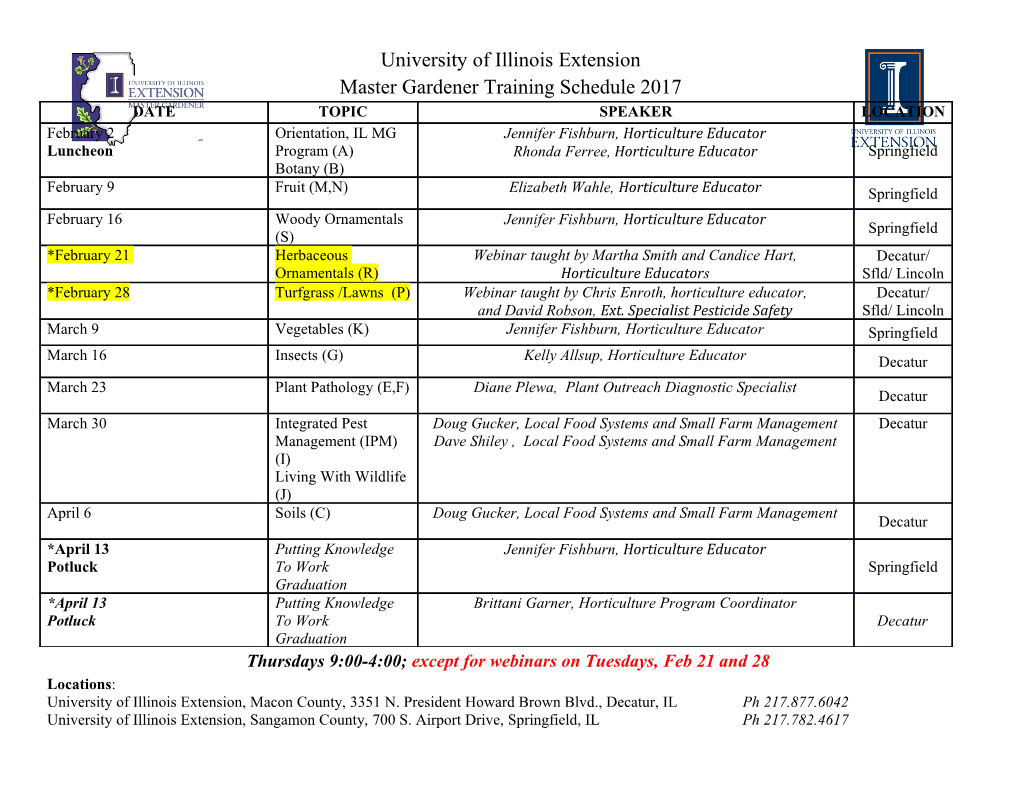
Polymer 48 (2007) 3306e3316 www.elsevier.com/locate/polymer Melt blown nanofibers: Fiber diameter distributions and onset of fiber breakup Christopher J. Ellison1, Alhad Phatak1, David W. Giles, Christopher W. Macosko, Frank S. Bates* Department of Chemical Engineering and Materials Science, University of Minnesota, 151 Amundson Hall, 421 Washington Avenue SE, Minneapolis, MN 55455, USA Received 4 December 2006; received in revised form 2 April 2007; accepted 3 April 2007 Available online 10 April 2007 Abstract Poly(butylene terephthalate), polypropylene, and polystyrene nanofibers with average diameters less than 500 nm have been produced by a single orifice melt blowing apparatus using commercially viable processing conditions. This result is a major step towards closing the gap between melt blowing technology and electrospinning in terms of the ability to produce nano-scale fibers. Furthermore, analysis of fiber diam- eter distributions reveals they are well described by a log-normal distribution function regardless of average fiber diameter, indicating that the underlying fiber attenuation mechanisms are retained even when producing nanofibers. However, a comparison of the breadth of the distributions between mats with differing average fiber diameters indicates that the dependence of the breadth with average fiber diameter is not universal (i.e., it is material dependent). Finally, under certain processing conditions, we observe fiber breakup that we believe is driven by surface tension and these instabilities may represent the onset of an underlying fundamental limit to the process. Published by Elsevier Ltd. Keywords: Nanofibers; Melt blowing; Electrospinning 1. Introduction functionalization. In addition, the ultimate mat properties such as overall mat strength (related to individual fiber A ‘‘nonwoven’’ refers to a sheet or mat of fibers connected strength, average fiber length, and fiber entanglement density) together by physical entanglements, or contact adhesion be- and porosity play an equally important role in end-use appli- tween individual fibers, without any knitting or stitching. cations. Nonwoven fibers find use in a range of applications The nonwovens industry was worth $14 billion in 2004 [1] such as filtration, membrane separation, protective military and is expected to grow further due to new applications requir- clothing, biosensors, wound dressings, and scaffolds for tissue ing fibers with increasingly smaller sizes. Since the surface engineering [2e5]. area of a fiber scales linearly with the diameter and the volume Electrospinning, melt spinning, and melt blowing are the (and mass) scales as the square of the diameter, the specific most commonly used processes for nonwovens production. surface area varies inversely with diameter (w1/d ), leading Electrospinning involves applying a strong electric potential to high specific surface areas for small fibers. As an example, (w10 kV) to a polymer solution contained in a syringe to a gram of a mat containing 100 nm polymer fibers (of density force a jet of the solution onto a grounded screen located 1 g/cm3) has about 10 m2 of surface area that can be made a few centimeters away. Rapid evaporation of the solvent re- available for a wide variety of processes via surface sults in a mat of fine (10 nme1 mm) polymer fibers that are de- posited on the screen. In contrast, melt spinning is performed * Corresponding author. Tel.: þ1 612 624 0839; fax: þ1 612 626 1686. by extruding a polymer melt and drawing it down with a take- E-mail address: [email protected] (F.S. Bates). up wheel. Since the polymer solidifies during the drawing pro- 1 The authors contributed equally to this work. cess, this yields highly oriented chains resulting in strong 0032-3861/$ - see front matter Published by Elsevier Ltd. doi:10.1016/j.polymer.2007.04.005 C.J. Ellison et al. / Polymer 48 (2007) 3306e3316 3307 fibers that can be produced at fast rates; however, the fibers are frequently whip across the air stream (a similar motion is ob- usually not smaller than 10 mm [2]. served in electrospinning, but is due to a fundamentally differ- During melt blowing, fibers are produced in a single step by ent mechanism [11,12]) after it exits the die and proceeds extruding a polymer melt through an orifice die and drawing towards the collection device [10,13]. This fiber motion pro- down the extrudate with a jet of hot air (typically at the duces a transient drag force from air flowing normal to and same temperature as the molten polymer). This environmen- down the axis of the fiber [14]. An additional level of exten- tally benign processing method was first developed in the 1950s sional force may be introduced when multiorifice dies are at the Naval Research Laboratory with the goal of making employed allowing adjacent fibers to participate in fibere sub-micron fibers to trap radioactive particles in the upper at- fiber interactions. mosphere [6]. Wente first described the construction of a melt Researchers have used high speed imaging techniques to blowing die composed of a series of orifices and slots [7]. perform inline investigations of fiber formation during melt Researchers at Exxon extended this basic design and first dem- blowing. Fiber diameter measurements revealed that most of onstrated the production of melt blown microfibers on a com- the fiber attenuation occurred within several centimeters of mercial scale by modifying sheet die technology [6,8]. Since the die exit and that the temperature of the fiber dropped to then, a number of companies such as Vose, 3M, Kimberlye near-ambient values over the same distance due to entrainment Clark, Cummins, and Johns Manville have used the technol- of ambient air into the hot air stream [15,16]. Additionally, ogy to produce commercial nonwoven products [6]. In general, laser Doppler velocimetry measurements showed that average these commercial products are composed of fibers with aver- fiber and air velocities approached the same value within age diameters exceeding 1e2 mm. several centimeters of the die exit [17,18]. This has also Melt blowing equipment is designed such that the air is been corroborated by modeling studies [15,19]. It is intuitive supplied in the form of two streams that form a v-slot (see that the attenuation during melt blowing occurs only between Fig. 1); other designs such as annular air jets have been the processing (Tp) and solidification (glass transition, Tg,or used only on a laboratory scale [9]. Commercially the v-slot crystallization, Tc) temperatures. This suggests a possible ap- design is used in the form of a long channel which encom- proach to achieve greater attenuation by holding the fibers in passes a single row of hundreds or thousands of orifices the active temperature window [Tg (or Tc) < T < Tp] for longer from which the fibers originate. The drag force exerted by periods of time (where T is the fiber temperature). Haynes and the air attenuates the melt extrudate into fibers, which are col- coworkers have suggested a design to implement this idea by lected a few feet away from the die producing a self-bonded combining melt blowing with entrainment of external heated mat [10]. The nature of the drag force is more complicated air; however, the diameters of the fibers obtained by this than the air stream simply acting in the axial direction along method were not dramatically smaller than those produced a taut fiber. The fiber is highly dynamic and is observed to without hot air entrainment [20]. Fig. 1 shows a schematic of the single orifice melt blowing die used in this study which is based on the design of a typical commercial melt blowing die. However, commercial melt blowing lines employ a multiorifice design composed of a lin- ear bank of holes more than a meter in length with hole diam- eters w0.2e0.6 mm spaced at 10e20 holes/cm [6,7,21].In general, there are four basic processing parameters that can be varied e polymer and air temperatures (Tp and Ta)andmass flow rates (mp and ma). In principle, each process parameter can individually affect the average diameter and length of the fibers which are produced. Shambaugh [22] studied the ex- isting industrial data from melt blowing processes and attemp- ted to provide a universal description for the variation of the fiber diameter in terms of a number of dimensionless groups. It was shown that the air-to-polymer mass flow rate mostly affected the resulting fiber size, but this parameter could not capture all the existing data from studies involving different materials, orifice diameters, processing conditions and die ge- ometries. Milligan and Haynes employed a single-hole die to study the melt blowing of a series of polypropylenes and con- cluded that the ratio of air to polymer mass fluxes (G) provided a satisfactory description of the fiber size for a wide range of processing conditions [23,24].(G incorporates the cross-sectional areas of the die geometry that flow rates Fig. 1. Detailed schematic of the melt blowing die: (a) sectional and (b) end-on do not.) They further developed an empirical model for the views of the two pieces. dimensionless average fiber diameter in terms of relevant 3308 C.J. Ellison et al. / Polymer 48 (2007) 3306e3316 dimensionless process variables, but noted that some of the processing conditions and the die orifice diameter are not model parameters are dependent on the polymer type (due to indicated. differing viscoelastic characteristics) and the particular melt Currently, electrospinning is the most popular process to blowing line employed (due to geometry, etc.). make fibers which have diameters in the 100 nm range A wide variety of polymers including polyethylene [7], [33,34], and as a result this process has begun to forge a niche polypropylene (PP) [15,23,25], poly(methyl methacrylate) in commercial production of ‘‘nanofibers’’ [35].
Details
-
File Typepdf
-
Upload Time-
-
Content LanguagesEnglish
-
Upload UserAnonymous/Not logged-in
-
File Pages11 Page
-
File Size-