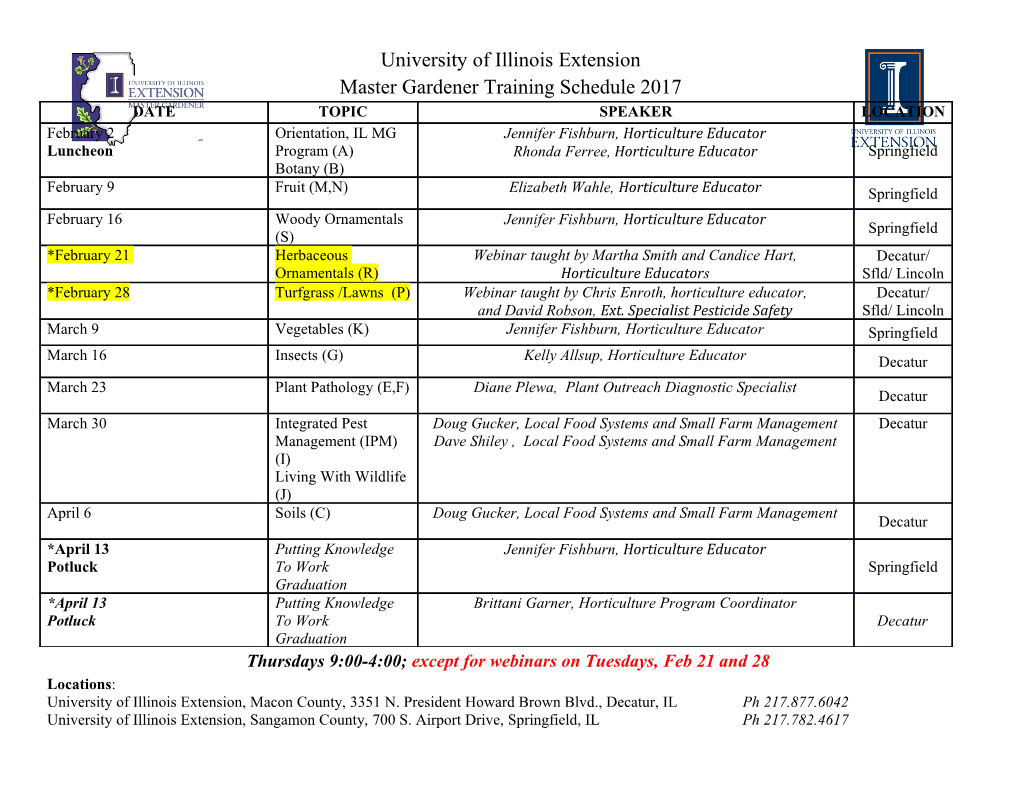
Article A Hexapod Robot with Non-Collocated Actuators Min-Chan Hwang *, Chiou-Jye Huang ID and Feifei Liu School of Electrical Engineering and Automation, Jiangxi University of Science and Technology, No. 86, Hongqi Road, Ganzhou 341000, China; [email protected] (C.-J.H.); [email protected] (F.L.) * Correspondence: [email protected]; Tel.: +86-177-7075-4280 Received: 8 April 2018; Accepted: 12 June 2018; Published: 25 June 2018 Abstract: The primary issue in developing hexapod robots is generating legged motion without tumbling. However, when the hexapod is designed with collocated actuators, where each joint is directly mounted with an actuator, the number of actuators is usually high. The adverse effects of using a great number of actuators include the rise in the challenge of algorithms to control legged motion, the decline in loading capacity, and the increase in the cost of construction. In order to alleviate these problems, we propose a hexapod robot design with non-collocated actuators which is achieved through mechanisms. This hexapod robot is reliable and robust which, because of its mechanism-generated (as opposed to computer-generated) tripod gaits, is always is statically stable, even if running out of battery or due to electronic failure. Keywords: hexapod; mechanism; non-collocated 1. Introduction Wheeled robots can efficiently move on flat surfaces, but they become ineffective as soon as they encounter rough and uneven environments, which comprise the majority of the Earth’s surface. For such terrains, legged robots simply always outperform wheeled robots. Hence, the development of a legged robot is motivated by the need to maneuver over rough terrains for outdoor activities. The challenge of developing a legged robot lies in one primary fact: how to generate the legged motion without tumbling. In 1968, McGhee and Frank [1,2] proposed the center of gravity projection (COG) method, where the legged robot is statically stable if the horizontal projection of its COG lies inside the support polygon, defined as the convex polygon formed by connecting footprints. Orin [3] proposed a generalized COG in 1976 called the COP (center of pressure) method, wherein a robot is dynamically stable if the projection of the COG along the direction of the resultant force acting on the COG lies inside the support polygon. A variety of legged robots, including quadruped, hexapod, and octopod robots commonly practice the above methods [4–6]. On the other hand, bipedal robots favor the ZMP (zero moment point) method, first defined by Vukabratovic and Juricic [7,8] in 1969, stating that a robot is stable if the moment about the COP at its supporting foot is zero. Meanwhile, two distinct methodologies evolved and were later introduced into robotics— that is, fuzzy theories and neural networks. Fuzzy theories [9–11] address the imprecision of systems by defining the fuzzy numbers or fuzzy sets that can be expressed in linguistic terms. For instance, the technology for finding the best value of foot acceleration for a given trajectory can be achieved by using a very simple Mamdani fuzzy inference system [12]. Once the foot acceleration function has been obtained, the real-time implementation of the fuzzy reasoning process can be optimized [13,14]. Neural networks [15–17] are able to represent complex nonlinear relationships and are good at classifying patterns into preselected categories used in the training process. One important observation from neuroscience is that the CPG (central pattern generator) [18,19] located in the spinal cord is an autonomous device generating rhythmic behaviors such as locomotion, requiring neither peripheral Appl. Syst. Innov. 2018, 1, 20; doi:10.3390/asi1030020 www.mdpi.com/journal/asi Appl. Syst. Innov. 2018, 2, x FOR PEER REVIEW 2 of 15 Appl. Syst. Innov. 2018, 1, 20 2 of 15 spinal cord is an autonomous device generating rhythmic behaviors such as locomotion, requiring neither peripheral sensor feedback nor the regulation command from the brain-stem. Hybrid sensorschemes feedback using noreither the regulationfuzzy controllers command or from neur theal brain-stem.networks to Hybrid implement schemes bionic using eithercontrol fuzzy are controllersappealing, and or neural have been networks conducted to implement extensively bionic in many control articles are appealing, (e.g., [20–27]). and have been conducted extensivelyWe found in many that all articles of the (e.g., legged [20 robots–27]). under discussion are designed with collocated actuators. That Weis, each found joint that is all mounted of the legged with an robots actuator under so discussionthat the number are designed of actuators with collocatedis usually high. actuators. The Thatadverse is, effects each joint of using is mounted a great numb wither an of actuator actuators so include that the increasing number the of actuatorschallenge of is algorithms usually high. to Thecontrol adverse legged effects motions, of using degrading a great number the loading of actuators capacity, include and raising increasing the thecost challenge of construction. of algorithms This toinspired control us legged to overcome motions, these degrading weaknesses the before loading resorting capacity, to other and raisingtechniques. the costHence, of construction.we designed Thisan innovative inspired mechanism us to overcome to lessen these the weaknessesnumber of actuators. before resorting Since stable to other tripod techniques. gaits are generated Hence, weby designedmechanism an instead innovative of computer, mechanism a togreat lessen amount the number of computing of actuators. resources Since stablecan be tripod released gaits and are generateddiverted to by engineering mechanism insteadapplications. of computer, In this apape greatr, amount we will of briefly computing discuss resources some candesign be released issues, andelaborate diverted the tomechanism engineering of applications.reducing the Innumber this paper, of actuators, we will brieflyestablish discuss the mathematical some design model, issues, elaborateand introduce the mechanismthe relevant ofhardware reducing as the well number as software. of actuators, establish the mathematical model, and introduce the relevant hardware as well as software. 2. Design Issues 2. Design Issues Determining how to build a robot is somewhat mundane. Nevertheless, it is sufficiently Determining how to build a robot is somewhat mundane. Nevertheless, it is sufficiently nontrivial and in fact sophisticated that we must have a design mechanism, select materials, nontrivial and in fact sophisticated that we must have a design mechanism, select materials, determine component sizes, make engineering drawings as shown in Figure 1, machine all of the determine component sizes, make engineering drawings as shown in Figure1, machine all of parts, and assemble them into a robot as shown in Figure 2, where the size of the robot is about 712 the parts, and assemble them into a robot as shown in Figure2, where the size of the robot is about mm × 641 mm × 189 mm and the size of its main body is 382 mm × 222 mm × 134 mm when six legs 712 mm × 641 mm × 189 mm and the size of its main body is 382 mm × 222 mm × 134 mm when are detached. Figure 1 shows that there are only three motors required by this hexapod (i.e., bottom six legs are detached. Figure1 shows that there are only three motors required by this hexapod (i.e., motor, upper motor, and swivel motor). Although ball bearings are better than porous metal bottom motor, upper motor, and swivel motor). Although ball bearings are better than porous metal bearings in terms of overall performance, they require more space in their housing and more bearings in terms of overall performance, they require more space in their housing and more material material to construct. In order to achieve a light-weight design, the structure is made of lighter to construct. In order to achieve a light-weight design, the structure is made of lighter aluminum aluminum AT6061T6 and porous metal bearings. AT6061T6 and porous metal bearings. Figure 1. Visualization of components. Figure 2. Completed hexapod robot. The servos used in the hobby radio control (RC) market for controlling model airplanes, cars, The servos used in the hobby radio control (RC) market for controlling model airplanes, cars, and boats are also frequently used in robots. The servos that are good for light-weight application and boats are alsoalso frequentlyfrequently usedused inin robots.robots. The servosservos thatthat areare goodgood forfor light-weightlight-weight application Appl. Syst. Innov. 2018, 1, 20 3 of 15 Appl. Syst. Innov. 2018, 2, x FOR PEER REVIEW 3 of 15 Appl. Syst. Innov. 2018, 2, x FOR PEER REVIEW 3 of 15 have threethree wires:wires: two two for for power power (red) (red) and and ground ground (black), (black), and theandthird the third for control for control (yellow), (yellow), as shown as have three wires: two for power (red) and ground (black), and the third for control (yellow), as shownin Figure in3 a.Figure The signal 3(a). isThe generally signal ais variable-width generally a pulse.variable-width The neutral pulse. position The correspondedneutral position to shown in Figure 3(a). The signal is generally a variable-width pulse. The neutral position correspondeda pulse of about to a 1.5 pulse ms, of sent about at 1.5 intervals ms, sent of at 20 inte ms.rvals The of servo 20 ms. HS-5645MG The servo HS-5645MG used in [28 used] with in size [29] corresponded to a pulse of about 1.5 ms, sent at intervals of 20 ms. The servo HS-5645MG used in [29] with40.39 size mm 40.39× 19.56 mm mm × 19.56× 37.59 mm mm × possesses37.59 mm apossesse stalled torques a stalled of 12 torque kg-cm. of In 12 order kg-cm. to improveIn order the to with size 40.39 mm × 19.56 mm × 37.59 mm possesses a stalled torque of 12 kg-cm.
Details
-
File Typepdf
-
Upload Time-
-
Content LanguagesEnglish
-
Upload UserAnonymous/Not logged-in
-
File Pages15 Page
-
File Size-