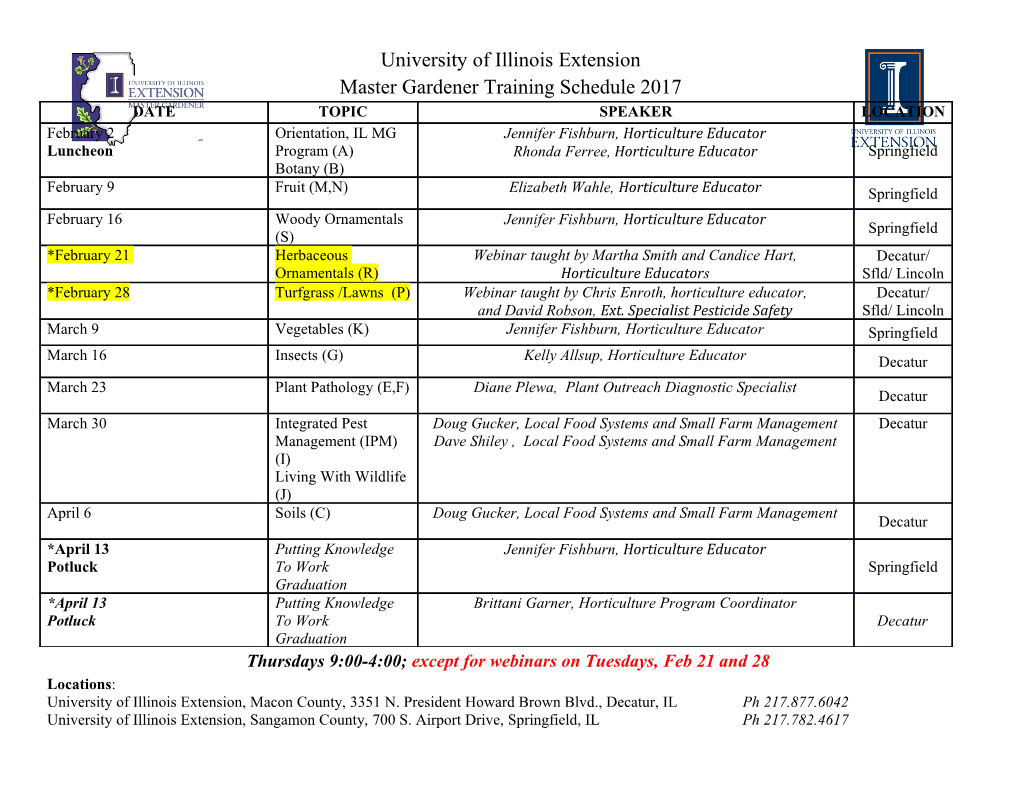
Autodesk Customer Success Story Sridevi Tool Engineers COMPANY Sridevi Tool Engineers Sridevi Tool Engineers: Challenges LOCATION Mumbai, India Create Capabilities SOFTWARE AUTODESK® Moldflow® “In the mold development and in the failure analysis the simulation has a great role. Simulation software allows fulfilling the injection molding process in a virtual reality, which helps the mold optimization, the material and process parameter determination before machining the injection mold, this way decreases the construction time and the number of potential failures.” — Rajendra Rindhe Assistant Manager CAE Sridevi Tool Engineers Image courtesy:Sridevi Tool Engineers Sridevi Tool Engineers specializes “Using Autodesk Moldflow in Design, Development and The competition in the market and the strict software is essential for Manufacturing of plastic injection requirements for the plastic parts require faster and more accurate mold making. The quality the design and production moulds for Automobile, White of injection molded thermoplastic parts largely stage of automotive parts goods, Luggage and various other depends on the process parameters. “In the and in other high accurate engineering industries. mold development and in the failure analysis plastic parts as well. Our the simulation has a great role. Simulation clients demand the use of Established in 1972, it is one of the largest software allows fulfilling the injection molding Moldflow software from commercial tool rooms in India having more process in a virtual reality, which helps the mold the suppliers thus during the than 40 years of experience in producing tools optimization, the material and process parameter construction phase so that for both domestic and foreign markets. The determination before machining the injection company majorly produce moulds for Automotive mold, this way decreases the construction time the deformation and other Trims, consoles, Pillars, Headlamp Housings, Air and the number of potential failures.” said Mr. injection failures can be filters, Exhaust assemblies, Instrument Panel and Rajendra Rindhe Assistant Manager CAE minimized. I think challenges its child parts, Grills, motorcycle fenders etc. create capabilities and Recently, while working for leading Automotive you need to adapt new Sridevi Tool Engineers has fully equipped state of OEM on development of spoiler (800 mm x 300 technologies to overcome the art Tool Room and project management skills mm) - inner and outer family mold. Sridevi Tool that challenges.” make them one of the most preferred tooling Engineers’ team faced challenging situation in suppliers to OEMs. designing and manufacturing of the mold cavity. — Rajendra Rindhe Because of complex geometry of the mold it was Assistant Manager CAE The Challenge: difficult to take into consideration the physical Sridevi Tool Engineers effects ruling in the cavity. Through the mold Nowadays, more and more polymer based deformation analysis using Moldflow, engineers products are utilized in the automotive industry, could detect potential problematic areas in the in the medical science and in many other areas. mold. The mould cavity flange was withstanding As a result of the continuous developments, several external loading issues; total mold novel polymer materials and special processes are displacement field in flange ranged from 0 mm to developed to accomplish the strict engineering 0.3 mm and the stress distribution field in flange claims. was 900 MPa. Autodesk Customer Success Story Sridevi Tool Engineers Our clients demand the use of Moldflow software from the suppliers thus during the construction phase so that the deformation and other injection failures can be minimized. “High stresses in the flange area were the major After using Moldflow for the complete molded part is a flawless mold - one that concern as the deformation of the mold changes simulation of the spoiler design, the analysis produces consistent pieces time and time again. the cavity dimensions and decreases the result showed very high stresses around 900 Autodesk Moldflow not only ensures a precise precision of the final molded parts. As a result, MPa in the flange. Based on the information adherence to final product requirements but the analysis of mold deformation becomes obtained from the structural simulation, also prolongs the overall mold life.” concludes designers quickly optimized spoiler. It was Mr. Rajendra Rindhe a valuable reference for us, especially for easy to decide boundary conditions and type optimizing the manufacturing of high-precision of meshing required using Moldflow. To products.” explains Mr. Rajendra Rindhe improve this problem the mold material was changed and the thickness of the flange was “We are able to detect increased. After running Moldflow simulation on new geometry the results showed stresses potential problematic areas of around 495 MPa, reduced to half of the in the mold and make earlier results. Further four mechanical Locks necessary changes to were provided for positive alignment between address these issues before mold halves that in-addition reduced stresses to 280 MPa. After the design, material changes the mold is machined. We and addition of mechanical locks Sridevi Tool utilize Autodesk Moldflow Engineers’ found that Moldflow simulation results to optimize the mold analysis results were strongly correlated with the results of the actual mold trials. Moldflow’s design by adjusting the mesh technology also made the simulation processing parameters, the results more consistent with the actual results geometry model, and the in manufacture. Ultimately, engineers were able mold material. This way, the Image courtesy:Sridevi Tool Engineers to decide the optimal design of spoiler within limited development time, avoid repetitive mold mold structural strength can The Solution: trials, and reduce costs. be further enhanced in order to extend the durability of the In the case of complex projects, predicting all factors determining the final quality of a part is mold as well as to ensure the often possible only after carrying out a series of precision of the final molded tests. Autodesk Moldflow was used to optimize products.” the mold design by adjusting the processing parameters, the geometry model, and the — Rajendra Rindhe mold material. This way, the mold structural Assistant Manager CAE strength can be enhanced in order to extend Sridevi Tool Engineers the durability of the mold as well as to ensure the precision of the final molded products. The geometry of spoiler was large and complex, the Moldflow was used to target areas of concern (flange) and optimize designs to build Image courtesy:Sridevi Tool Engineers mold accordingly so that real problems can be “We are able to detect potential problematic “High stresses in the flange solved with virtual samples before the mold areas in the mold and make necessary changes was built, which saves the time and money that area were the major concern to address these issues before the mold is as the deformation of the would be required to address these problems machined. We utilize Autodesk Moldflow results after the first sample. to optimize the mold design by adjusting the mold changes the cavity processing parameters, the geometry model, dimensions and decreases the “Using Autodesk Moldflow software is and the mold material. This way, the mold precision of the final molded essential for the design and production stage structural strength can be further enhanced of automotive parts and in other high accurate in order to extend the durability of the mold parts. As a result, the analysis plastic parts as well. Our clients demand the as well as to ensure the precision of the final of mold deformation becomes use of Moldflow software from the suppliers molded products.” said Mr. Rajendra Rindhe. a valuable reference for us, thus during the construction phase so that the deformation and other injection failures can be especially for optimizing minimized. I think challenges create capabilities The Result: : the manufacturing of high- and you need to adapt new technologies to precision products.” overcome that challenges.” said Mr. Rajendra By using Autodesk Moldflow software, Sridevi Rindhe Tool Engineer’ has been able to more efficiently — Rajendra Rindhe and accurately deliver critical information to Assistant Manager CAE customers in need thereby insuring that the Sridevi Tool Engineers client is fully aware of the product’s capabilities and limitations before the tooling and manufacturing phases begin. Over the years, company has also been able to incorporate Moldflow into the process of streamlining productivity so customers can save substantially over the course of a product’s life cycle. This, in turn, reduces the probability of making further costly modifications after the initial trials. Image courtesy:Sridevi Tool Engineers “We believe that quality of the plastic injection Autodesk [and other products] are registered trademarks or trademarks of Autodesk, Inc., and/or its subsidiaries and/or affiliates in the USA and/ or other countries. All other brand names, product names, or trademarks belong to their respective holders. Autodesk reserves the right to alter product and services offerings, and specifications and pricing at any time without notice, and is not responsible for typographical or graphical errors that may appear in this document. © 2017 Autodesk, Inc. All rights reserved. .
Details
-
File Typepdf
-
Upload Time-
-
Content LanguagesEnglish
-
Upload UserAnonymous/Not logged-in
-
File Pages2 Page
-
File Size-