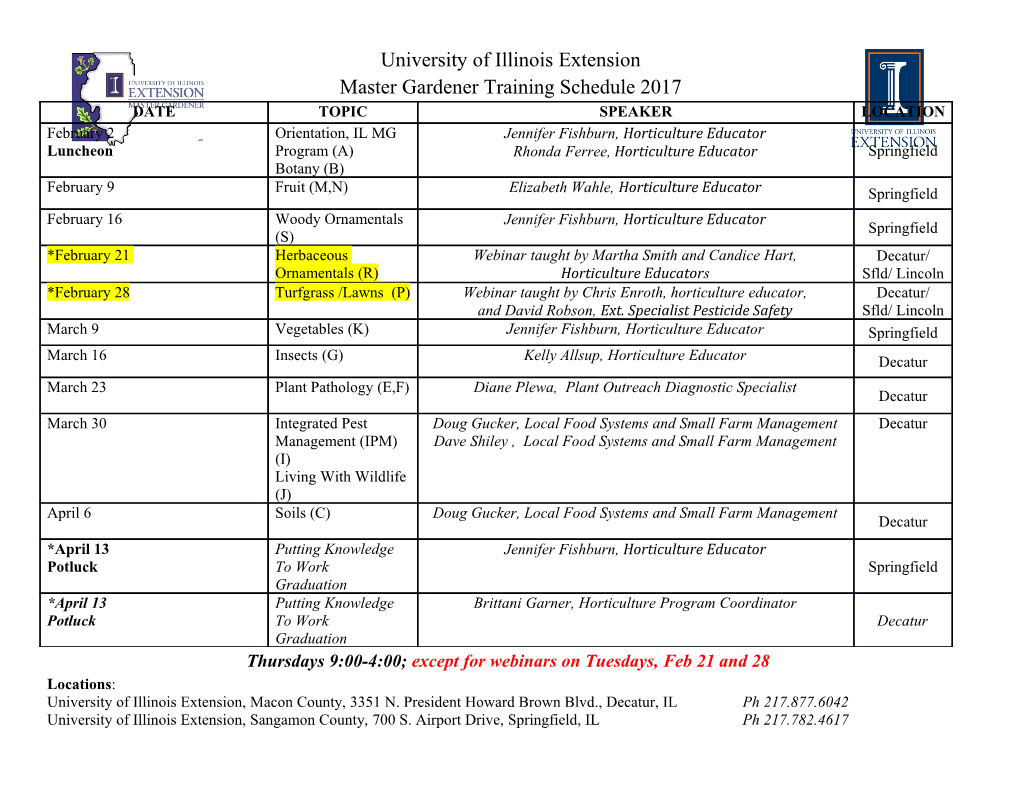
United States Patent 19 (11) 4,314,898 Nakako et al. (45) Feb. 9, 1982 (54) PROCESS FOR REFORMING COAL FOREIGN PATENT DOCUMENTS 75 Inventors: Yukio Nakako, Takarazuka; Toshio 2548946 5/1976 Fed. Rep. of Germany. 208/8 LE Ohzawa, Kobe; Shizuo Yokota, 50-67801 of 1975 Japan. Nishinomiya; Masaaki Tamura, 51-27894 of 1976 Japan. Kobe, all of Japan Primary Examiner-Delbert E. Gantz Assistant Examiner-William G. Wright 73 Assignee: Kobe Steel, Ltd., Kobe, Japan Attorney, Agent, or Firm-Oblon, Fisher, Spivak, McClelland & Maier 21 Appl. No.: 144,883 57 ABSTRACT Improvements in a process for reforming coal by sub (22 Filed: Apr. 29, 1980 jecting a mixed slurry containing a hydrocarbon solvent 30 Foreign Application Priority Data and coal fines to hydrogenation reaction under high temperature and pressure conditions, gas-liquid separa May 1, 1979 (JP) Japan ......................... 54-054516 tion, and distillation to obtain a solvent-refined coal, the improvements comprising: maintaining the reaction (51) Int. Cla........................ C10G 1/00 temperature and total reaction pressure within a hydro 52 U.S. Cl. ................................... ............... 208/8 LE genation reactor at 400 to 500° C. and 50 to 200 atms., 58) Field of Search .................... ................ 208/8 LE and controlling the residence time distribution of reac tants, excepting gaseous reactants, in the hydrogenation 56 . References Cited reaction zone to have an average residence time longer U.S. PATENT DOCUMENTS than 17 minutes, and to keep the quantity of the reac tants which have a residence time shorter than 10 min 3,508,203 4/1970 Nelson ............................. 208/8LE 3,594,304 7/1971 Seitzer et al. ... utes in a proportion less than 20% by weight of the 3,645,885 2/1972 Harris et al. .... reactants. 3,892,654 7/1975 Wright et al....... 4,094,765 6/1978 Bearden, Jr. et al. ........... 208/8 LE 3 Claims, 5 Drawing Figures FINES a CATALYST RECOWERED SOLVENT LOUID PRODUCTS U.S. Patent Feb. 9, 1982 Sheet 1 of 3 4,3 14,898 CE}}/3/005}} 1NEMTOS TITIOIT S10000}}d U.S. Patent Feb. 9, 1982 Sheet 2 of 3 4,314,898 tN S & n S. & S S S N U t S a- S N. S.am S Vo e S is & SQ Ul S No & Q we an Q N S S.(S CS CS Cs (OLIVIH973M) NOLIOvy 9NLI/93INI U.S. Patent Feb. 9, 1982 Sheet 3 of 3 4,314,898 92 90 FIG.3(I) 89 O2 O4 O6 O8 l.0 INTEGRATING FRACTION WEIGHT RATIO) Rg 92 O 5S 9 ------- 90 m 6 FIG. 3(I) N S 89 2 a INTEGRATING FRACTION WEIGHTRATIO) Sg 92 S S 9 eo - - - - - Y - - - - - - -o- 90 FIG.3(II) S. 89 oz oa os as to INTEGRATING FRACTION WEIGHTRATIO) 4,314,898 2 known to date. In other words, there have not yet been PROCESS FOR REFORMING COAL developed processes which are capable of producing solvent refined coal of commercially satisfactory qual BACKGROUND OF THE INVENTION ity in an assured manner. This invention relates to a process for reforming coal, On the other hand, when a solvent-refined coal and more particularly to a method for reforming coal which is an intermediate product in the above-men into a form useful for the production of a metallurgical tioned conventional processes is further subjected to carbonaceous material and/or a liquid product (a liquid secondary hydrogenation after separation by reduced fuel, or chemical raw materials) by controlling reaction pressure distillation for the purpose of obtaining a liquid factors including the residence time distribution of reac O product, the so-called coking trouble is often experi tants in a reaction Zone, except those in gaseous phase, enced at the bottom of the distillation tower due to free in a predetermined reaction temperature range and radicals or other unstable substances which remain in under a total reaction pressure, in the “hydrogenation large amounts in the intermediate product depending process' in which a slurry mixture containing a low upon the conditions of the primary hydrogenation. In grade coal such as brown coal and a hydrocarbon base 15 addition, where such unstable solvent refined coal is solvent is subjected to hydogenation reaction under subjected to secondary hydrogenation, difficulties are high temperature and pressure conditions. also encountered in that the increase in viscosity of the To cope with the scarcity and high price in recent reaction mixture makes the deashing step troublesome, years of heavy coking coal, a raw material of coke and said free radicals or other unstable substances invite which is used in iron production, many attempts have 20 deterioration of catalyst in the succeeding hydrogena thus far been made to produce coke of increased tion step due to coke deposition on the hydrogenation strength from low-grade coals such as brown coal, peat, catalyst. However, no clarification has ever been made lignite, some bituminous coal and the like, by the so with regard to the relation between the reaction condi called coal liquefaction technology (involving the hy tions of the primary hydrogenation step and the content drogenation reaction either in one step or in two steps), 25 which produces a liquid product from coals, producing of unstable substances in the solvent refined coal, and a solvent-refined coal by hydrogenation reaction of there has been proposed no method effective for reduc low-grade coals and blending it into a raw material to be ing the content of the unstable substances. used for coke production. In this connection, Japanese SUMMARY OF THE INVENTION Laid-Open Patent Specification Nos. 67801/75 and 30 27894/76 disclose related processes: the former is di With the foregoing in view, the present inventors rected to a process consisting of hydrogenating a non have conducted extensive studies on the hydrogenation coking or coking coal with a hydrocarbon solvent in a reaction conditions and accomplished the present in pressurized hydrogen atmosphere, separating solid frac vention on the basis of findings that, among various tions, and blending desulfurized and deashed, highly 35 conditions, there is a strong correlation between the flowable products having a melting point of 100° C. to residence time distribution of reactants in the primary 350° C. into the raw coal to be coked; and the latter is hydrogenation reaction zone in a particular temperature directed to a process consisting of bringing an oxygen range under a total reaction pressure, and the quality of rich solid carbonaceous fossil fuel, which is unsuitable the resulting solvent refined coal, and that solvent re for coking, into contact with a solvent and hydrogen for 40 fined coal of a quality suitable for a metallurgical carbo deoxygenation under pressurized and heated condi naceous material or for an intermediate material of the tions, removing the solvent and volatile components liquid product can be obtained by suitably controlling from the resulting mixture by distillation, and recover the residence time distribution. ing the residual mixture which can be used as a blending More particularly, the present invention aims to pro material for coke making. The latter process is espe 45 vide improvements in a process for reforming coal by cially advantageous since it dispenses with the deashing subjecting a mixed slurry containing a hydrocarbon step which has been essential in the conventional coal solvent and coal fines to primary hydrogenation reac liquefaction technology. tion under high temperature and pressure conditions, It is also known in the art to obtain a liquid product gas-liquid separation and distillation to obtain a solvent by further deashing and secondarily hydrogenating the 50 refined coal (reformed coal), the improvements com Solvent refined coal which is obtained by the above prising: maintaining the reaction temperature and total mentioned process. reaction pressure in the reactor at 400° C. to 500 C. and However, in the prior art including the above-men 50 to 200 atms., and controlling the residence time dis tioned processes, the hydrogenation step itself still de tribution of reactants, excepting gaseous reactants in the pends on the conventional coal liquefaction technology, 55 primary hydrogenation reaction zone to have an aver leaving many problems unsolved in obtaining carbona age residence time longer than 17 minutes, and to keep ceous products of a quality suitable for use as a metallur the quantity of the reactants which have a residence gical carbonaceous material, including coke for iron time shorter than 10 minutes in a proportion less than production. More particularly, when hydrogenating 20% by weight of the reactants. low-grade coals such as brown coal, peat, lignite, some 60 The present invention employs low-grade coals such bituminous coals and the like to obtain coke for steel as brown coal, peat, lignite, some of bituminous coals production, the most important technical problem is and the like which have thus far been regarded as being how to improve the strength of coke of the ultimate unsuitable for the production of metallurgical coke. The product. This problem was not considered in the con solvent-refined coal which is recovered by gas-liquid ventional coal liquefaction technology, and therefore 65 separation of the reaction mixture resulting from the the relation between the conditions of the hydrogena hydrogenation reaction can be mixed into coal which is tion reaction and the quality of the solvent refined coal to be used as a starting material for the production of as a metallurgical carbonaceous material has been un metallurgical coke. In such a case, it is possible to obtain 4,314,898 3 4. coke of high quality even when strongly coking coal is phase are stripped by a second gas-liquid separator 7, used in an extremely reduced mixing ratio.
Details
-
File Typepdf
-
Upload Time-
-
Content LanguagesEnglish
-
Upload UserAnonymous/Not logged-in
-
File Pages9 Page
-
File Size-