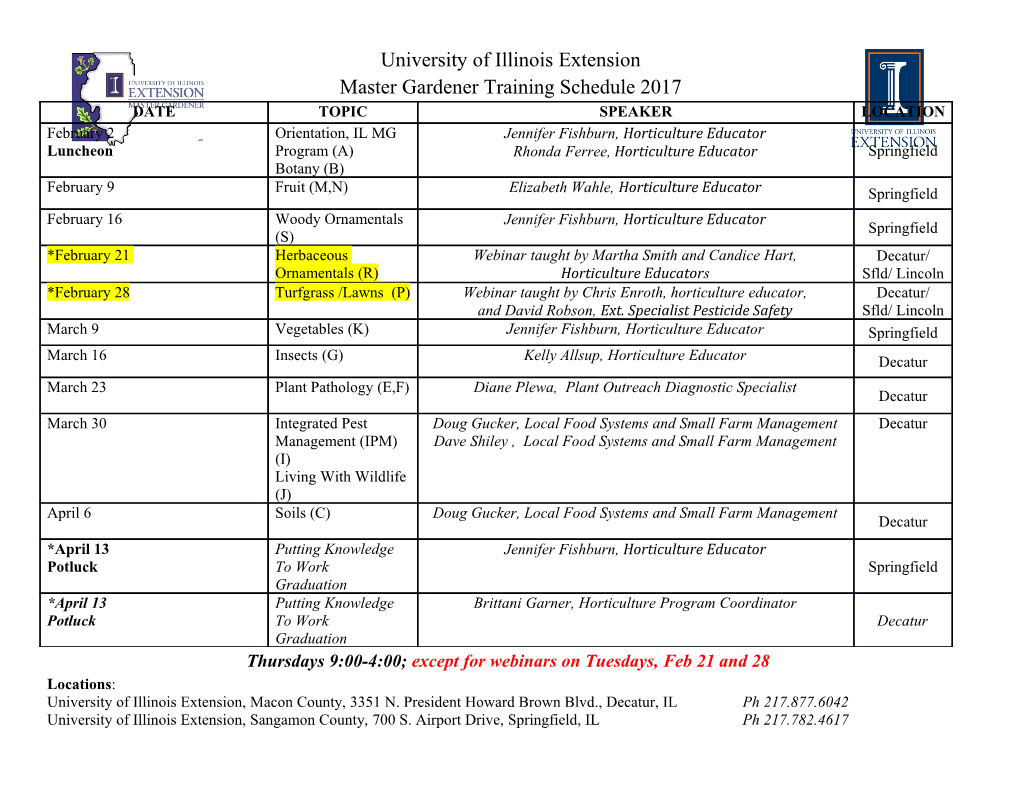
MODELLING AND OPTIMIZATION OF HIGH TEMPERATURE DIFFERENCE (HTD) GAMMA- TYPE STIRLING ENGINE PROTOTYPE By Suliman Alfarawi A thesis submitted to the University of Birmingham for the Degree of Doctor of Philosophy School of Mechanical Engineering College of Engineering and Physical Sciences The University of Birmingham September - 2017 University of Birmingham Research Archive e-theses repository This unpublished thesis/dissertation is copyright of the author and/or third parties. The intellectual property rights of the author or third parties in respect of this work are as defined by The Copyright Designs and Patents Act 1988 or as modified by any successor legislation. Any use made of information contained in this thesis/dissertation must be in accordance with that legislation and must be properly acknowledged. Further distribution or reproduction in any format is prohibited without the permission of the copyright holder. ABSTRACT Finding solutions for increasing energy demands is being globally pursued. One of the promising solutions is the utilization of renewable forms of energy with thermo-mechanical conversion systems such as Stirling engines. Nowadays, effort is made in industry and academia to promote the development of Stirling technology. In this context, this thesis was first focused on modelling of High Temperature Difference (HTD) gamma-type Stirling engine prototype (ST05-CNC) and investigating means of improving its performance. Secondly, newly parallel- geometry mini-channel regenerators (with hydraulic diameters of 0.5, 1, 1.5 mm) and their test facility were developed and fabricated to enhance engine performance. Both thermodynamic and CFD models were comprehensively developed to simulate the engine and have been successfully validated against experimental data. The modified second-order analysis with different thermal, frictional and mechanical losses was adopted in the thermodynamic model. The CFD model was based on a combined approach of dynamic meshing of compression and expansion spaces, non-isothermal flow modelling in free flow domains and non-equilibrium thermal modelling in porous domains of the engine such as regenerator and cooler. The simulation results showed that the performance of the engine can be improved with a minimum alteration of the current layout by the following; • At speeds up to 500 rpm, there is no significant difference in generated power using helium and nitrogen. However, helium tends to increase engine shaft power at higher speeds (712W at 1100 rpm) while the power generated using nitrogen is totally decayed. • Reducing the connecting pipe diameter from 30mm to 15mm can enhance the shaft power by up to 20% as the dead volume is reduced by 75%. I • Although the shaft power can be increased by 5% when the phase angle is increased from 90° to 105°, phase angle can be adjusted to normally 90° for practical reasons. • The heater tube diameter can be kept as 6mm as the original layout. Degradation of engine performance occurs at values far from this value due to reduction in surface area or the increase in heater dead volume. Theoretically, engine power can be increased by maximizing the operational temperature difference between the heat source and sink. The feasibility of utilizing the cryogenic energy storage using surplus electricity or renewable energy sources to maximize the shaft power was investigated. It was found that lowering the cooling temperature -50 °C can enhance the shaft power by 49% for helium reaching 1000 W and 35% for Nitrogen reaching 700 W. A combined approach based on experiment and CFD as an alternative to single-blow method was used to investigate heat transfer and flow friction in three fabricated mini-channel regenerators fabricated using 3D printing technology. It was found that the 0.5mm channel regenerator had the highest interstitial heat transfer coefficient compared to other investigated configurations due to the increased surface area of the matrix. On the other hand, using materials with higher heat capacity and lower thermal conductivity such as ceramic ZrO2 and Monel 400 can have good potential to generate power compared to random fibre. II ACKNOWLEDGEMENTS My sincere thanks and gratitude are due to my ALMIGHTY, ALLAH, who helped and blessed me. To my wife, Nagat and my daughters, Mariem, Sajeda and Retaj: because I owe it all to you. Many Thanks! For their supervision, valuable guidance, and continues support during my PhD research, I extend my sincere thanks to: Dr. Raya Al-Dadah and Dr. Saad Mahmoud I would like to thank Mr Simon Rowan for helping me to construct my test rig and for his continuous assessment and commissioning of the test facilities. I would like to thank all my family and friends for their moral support during my PhD study. III CONTENTS ABSTRACT .............................................................................................................................. I ACKNOWLEDGEMENTS .................................................................................................. III CONTENTS ........................................................................................................................... IV LIST OF FIGURES ............................................................................................................ VIII LIST OF TABLES ................................................................................................................ XII NOMENCLATURE ........................................................................................................... XIII LIST OF PUBLICATIONS .............................................................................................. XVII CHAPTER 1 .............................................................................................................................. 1 INTRODUCTION .................................................................................................................... 1 1.1 Introduction .................................................................................................................. 1 1.2 Stirling cycle engine history ........................................................................................ 1 1.3 Theoretical cycle .......................................................................................................... 4 1.4 Real cycle of Stirling engine ........................................................................................ 6 1.4.1 Real motion .......................................................................................................... 6 1.4.2 Leakage of working fluid ..................................................................................... 7 1.4.3 Pumping and mechanical losses ........................................................................... 8 1.4.4 Real gas and turbulence ........................................................................................ 8 1.4.5 Dead spaces .......................................................................................................... 9 1.4.6 Real heat exchangers ............................................................................................ 9 1.4.7 Thermal losses .................................................................................................... 10 1.5 Engine configurations ................................................................................................ 10 1.6 Engine heat exchangers ............................................................................................. 12 1.6.1 Heater.................................................................................................................. 12 1.6.2 Cooler ................................................................................................................. 14 1.6.3 Regenerator ......................................................................................................... 15 1.7 Stirling engine applications ....................................................................................... 16 1.7.1 Solar power generation ....................................................................................... 16 1.7.2 Computer chip cooling ....................................................................................... 17 1.7.3 Stirling engine powered submarines .................................................................. 18 1.7.4 Domestic heat and power ................................................................................... 19 1.7.5 Stirling engine powered automobiles ................................................................. 20 1.7.6 Stirling cryocooler .............................................................................................. 21 IV 1.8 Motivation .................................................................................................................. 22 1.9 Aims and objectives and thesis structure ................................................................... 23 CHAPTER 2 ............................................................................................................................ 27 LITERATURE REVIEW ...................................................................................................... 27 2.1 Introduction ................................................................................................................ 27 2.2 Review of different analysis approaches ................................................................... 27 2.2.1
Details
-
File Typepdf
-
Upload Time-
-
Content LanguagesEnglish
-
Upload UserAnonymous/Not logged-in
-
File Pages241 Page
-
File Size-