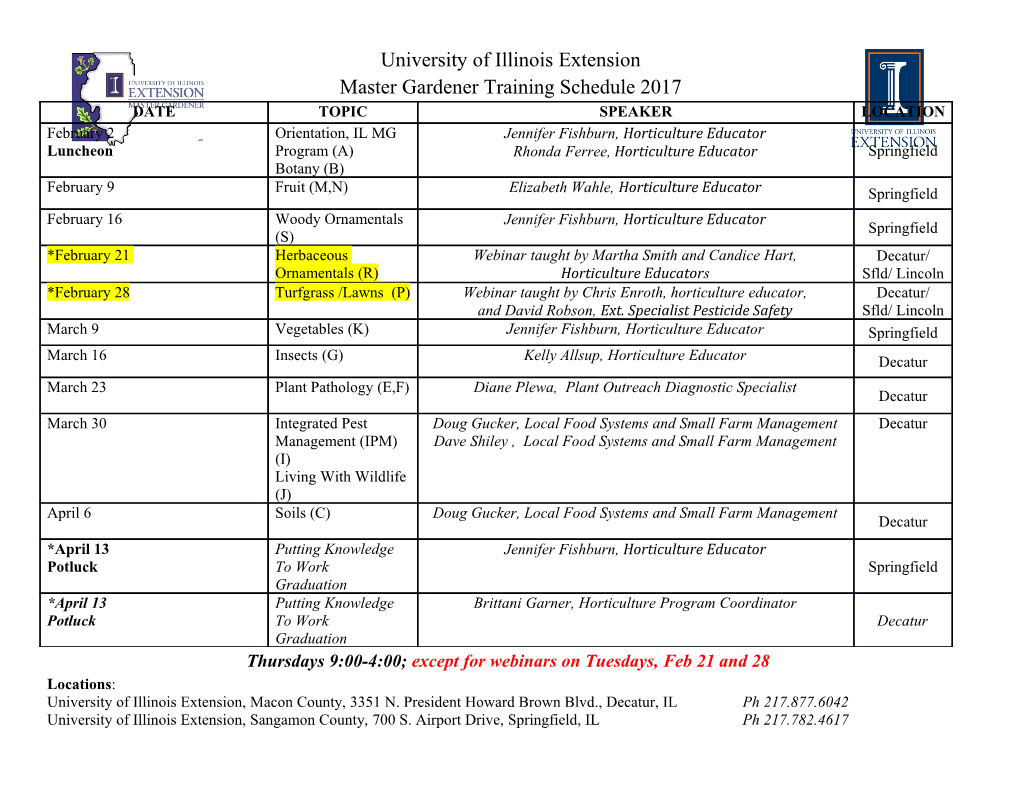
sensors Article Comparison between Resonance and Non-Resonance Type Piezoelectric Acoustic Absorbers Joo Young Pyun , Young Hun Kim , Soo Won Kwon, Won Young Choi and Kwan Kyu Park * Department of Convergence Mechanical Engineering, Hanyang University, Seoul 04763, Korea; [email protected] (J.Y.P.); [email protected] (Y.H.K.); [email protected] (S.W.K.); [email protected] (W.Y.C.) * Correspondence: [email protected] Received: 26 November 2019; Accepted: 18 December 2019; Published: 20 December 2019 Abstract: In this study, piezoelectric acoustic absorbers employing two receivers and one transmitter with a feedback controller were evaluated. Based on the target and resonance frequencies of the system, resonance and non-resonance models were designed and fabricated. With a lateral size less than half the wavelength, the model had stacked structures of lossy acoustic windows, polyvinylidene difluoride, and lead zirconate titanate-5A. The structures of both models were identical, except that the resonance model had steel backing material to adjust the center frequency. Both models were analyzed in the frequency and time domains, and the effectiveness of the absorbers was compared at the target and off-target frequencies. Both models were fabricated and acoustically and electrically characterized. Their reflection reduction ratios were evaluated in the quasi-continuous-wave and time-transient modes. Keywords: resonance model; non-resonance model; piezoelectric material 1. Introduction Piezoelectric transducers are used in various fields, such as nondestructive evaluation, image processing, acoustic signal detection, and energy harvesting [1–4]. Sound navigation and ranging (SONAR) is a technology for acoustic signal detection that can be used to detect objects under water. Stealth technology has been developed to prevent detection by such SONAR systems. Therefore, studies have focused on reducing the reflection of sound waves to prevent detection by SONAR systems. Wedge shaped structures or coatings have been used as passive sound absorbers to minimize underwater acoustic reflection. The coating is durable, but needs improvement. Therefore, minimizing detection in the low frequency range is challenging. In the low frequency range, the wavelength of the signal is several tens of centimeters. The thickness of the wedge shaped structure or coating should be at least several tens of centimeters to minimize acoustic reflection. Attaching a thick, passive sound absorbing material to a submarine hull increases the weight of the submarine and interferes with its propulsion. Sound can also be reduced using the wave scattering method. However, this technique only works under hydrostatic pressure [5,6]. Therefore, active sound absorbing materials have been developed to overcome the disadvantages of passive sound absorbing materials [7–10]. Lafluer et al. used piezorubber to realize an active sound absorbing material [11], whereas Howarth et al. used piezoelectric composites to reduce reflection. Although this material exhibited high attenuation performance at one frequency (5.4 kHz), it was not an active sound absorbing material composed of one structure. [12]. Chang et al. reduced sound reflection using two layers of a 1–3 piezoelectric composite. This resulted in an attenuation performance of 20 dB in the range of 6–10 kHz [13]. Accordingly, piezoelectric acoustic absorbers can be classified into resonance and non-resonance types based on Sensors 2020, 20, 47; doi:10.3390/s20010047 www.mdpi.com/journal/sensors Sensors 2020, 20, 47 2 of 17 Sensors 2019, 19, x FOR PEER REVIEW 2 of 17 previous studies. However, it is difficult to compare them due to the different approaches involved. Therefore,the different we believe approaches that only involved. resonance Therefore, and non-resonance we believe models that on withly similarresonance structures and non-resonance should be compared.models with In this similar study, structures resonance andshould non-resonance be compared. models In this suitable study, for resonance the target and frequency non-resonance were designedmodels via suitable mathematical for the analysis.target frequency Based on were the designs, designed the via resonance mathematical and non-resonance analysis. Based models on the weredesigns, fabricated the resonance and evaluated. and non-reso The absorbernance was models configured were fabricated in the form and of tiles,evaluated. and the The lateral absorber size of was theconfigured structure was in the equal form to of half tiles, of theand wavelength. the lateral size Our of proposed the structure resonance was equal and to non-resonance half of the wavelength. models wereOur fabricated proposed by stackingresonance commercially and non-resonance available leadmodel zirconates were titanatefabricated (PZT). by Variousstacking studies commercially have previouslyavailable investigated lead zirconate the titanate stacking (PZT). or direct Various fabrication studies of have devices previously [14–19]. investigated the stacking or direct fabrication of devices [14–19]. 2. Materials and Methods 2. Materials and Methods 2.1. Concept 2.1. Concept In the case of a piezoelectric material, vibration along the thickness direction is observed when anIn electrodethe case ofis a piezoelectric applied, and material, the sound vibration spreads along around the thickness both the direction front and is observed rear sides when of an theelectrode piezoelectric is applied, material. and Thethe sound resonance spreads frequency around rangeboth the of afront piezoelectric and rear sides material of the depends piezoelectric on itsmaterial. thickness. The The resonance thickness frequency of a piezoelectric range of materiala piezoelectric and its material resonance depends frequency on its are thickness. inversely The proportional,thickness of i.e., a piezoelectric the thinner thematerial piezoelectric and its resona material,nce thefrequency higher are is itsinversely resonance proportional, frequency i.e., and the vicethinner versa. the piezoelectric material, the higher is its resonance frequency and vice versa. InIn this this paper, paper, we we present present a modela model that that resonates resonates in thein the low low frequency frequency region region of theof the target target frequencyfrequency and and a non-resonance a non-resonance model model that deviates that deviat from thees targetfrom the frequency. target Thefrequency. proposed The resonance proposed andresonance non-resonance and non-resonance models incorporated models incorporated a function that a function cancelled that a certaincancelled portion a certain of the portion incident of the soundincident waves. sound waves. TheThe incident incident and and reflected reflected waves waves mustmust bebe separated to to cancel cancel the the incident incident sound sound wave. wave. Two Tworeceiving receiving sensors sensors were were required required to toseparate separate the the incident incident and and reflected reflected waves, waves, as asthe the signals signals were weremeasured measured based based on on the the overlap overlap between between these these two waves.waves. TheThe incidentincident ( P(+P) and) and reflected reflected (P –()P– ) acousticacoustic pressures pressures were were the the input input and and output output of theof the system, system, respectively respectively.(Figure (Figure1). We 1) We calculated calculated the the incidentincident and and reflected reflected acoustic acoustic sensitivities sensitivities based based on on the the diff differenterent receiving receiving sensitivities sensitivities of theof the two two sensorssensors obtained obtained using using the the Krimholtz–Leedom–Matthaei Krimholtz–Leedom–Matthaei (KLM) (KLM) model. model. Figure 1. FigureIncident 1. Incident and and reflected reflected waves. waves. The proposed resonance and non-resonance models are shown in Figure2. Generally, PZTs with The proposed resonance and non-resonance models are shown in Figure 2. Generally, PZTs with low resonance frequencies are difficult to manufacture. Therefore, the frequency was reduced by low resonance frequencies are difficult to manufacture. Therefore, the frequency was reduced by attaching steel to the rear side of the PZT. The model with steel at the rear side of the PZT was the attaching steel to the rear side of the PZT. The model with steel at the rear side of the PZT was the resonance model, whereas that without steel was the non-resonance model, as shown in Figure2. resonance model, whereas that without steel was the non-resonance model, as shown in Figure 2. Both models consisted of one transmitting sensor, two receiving sensors, and three acoustic windows. Both models consisted of one transmitting sensor, two receiving sensors, and three acoustic windows. Polyvinylidene difluoride (PVDF) could be used as a receiving sensor to measure the sound pressure Polyvinylidene difluoride (PVDF) could be used as a receiving sensor to measure the sound pressure without disturbing the sound propagation. The transmitter used PZT-5A, which is insensitive to without disturbing the sound propagation. The transmitter used PZT-5A, which is insensitive to temperature changes and has excellent transmission capabilities. The resonance and non-resonance temperature changes and has excellent transmission capabilities. The resonance and non-resonance models presented herein were used underwater. Therefore, a physical gap was required between the Sensors 2020, 20, 47 3 of
Details
-
File Typepdf
-
Upload Time-
-
Content LanguagesEnglish
-
Upload UserAnonymous/Not logged-in
-
File Pages17 Page
-
File Size-