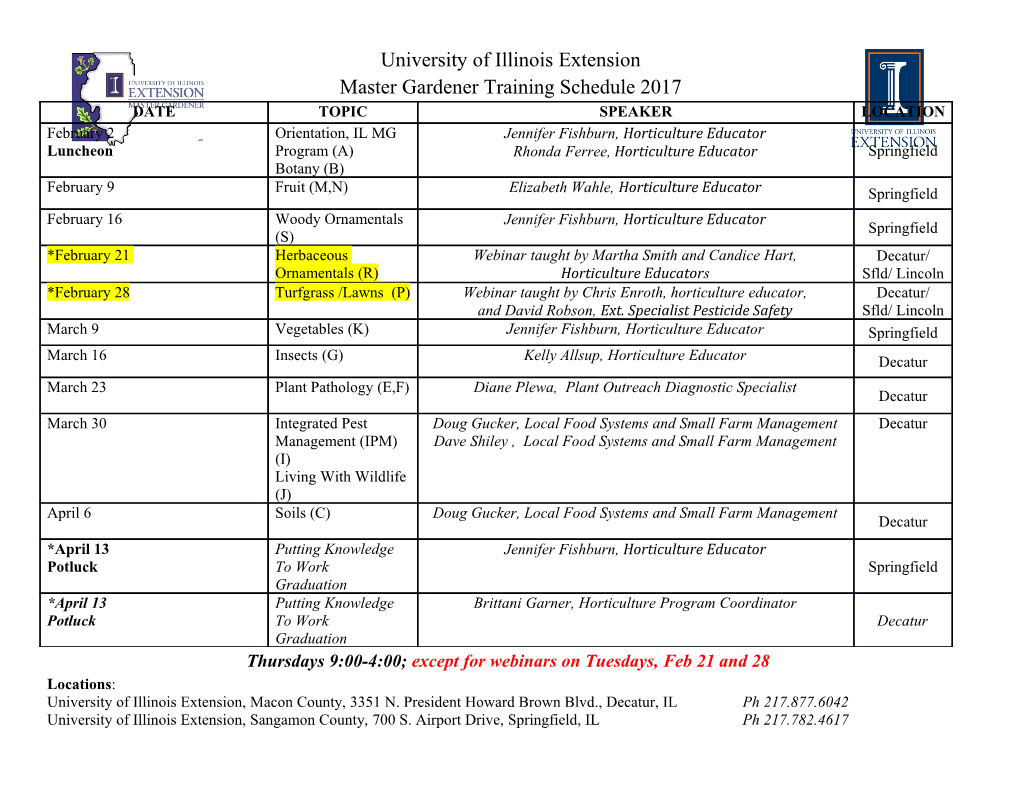
Scale-Up Economics for Cultured Meat Techno-Economic Analysis and Due Diligence David Humbird DWH Process Consulting LLC Centennial, Colorado USA Prepared for Open Philanthropy San Francisco, California USA December 28 2020 Executive Summary “Cultured meat” technologies aim to replace conventional meat with analogous or alternative bioproducts from animal cell culture. Developers of these technologies claim their products, also known as “cell-based” or “cultivated” meat, will be safer and more environmentally friendly than conventional meat while offering improved farm-animal welfare. To these ends, Open Philanthropy commissioned this assessment of cultured meat’s potential to measurably displace the consumption of conventional meat. Recognizing that the scalability of any cultured-meat products must in turn depend on the scale and process intensity of animal cell production, this study draws on techno-economic analysis and due-diligence perspectives in industrial fermentation and upstream biopharmaceuticals to assess the extent to which animal cell culture could be scaled like a fermentation process. The analysis identifies a number of significant barriers to the scale-up of animal cell culture. Bioreactor design principles indicate a variety of issues associated with bulk cell growth in culture: Low growth rate, metabolic inefficiency, catabolite and CO2 inhibition, and bubble-induced cell damage will all limit practical bioreactor volume and attainable cell density. With existing bioreactor designs and animal cell lines, a significant engineering effort would be required to address even one of these issues. Economic challenges are further examined. Equipment and facilities with adequate microbial contamination safeguards are expected to have high capital costs. Suitable formulations of amino acids and protein growth factors are not currently produced at scales consistent with food production, and their projected costs at scale are likewise high. The replacement of amino-acid media with plant protein hydrolysates is discussed and requires further study. Capital- and operating-cost analyses of conceptual cell-mass production facilities indicate production economics that would likely preclude the af- fordability of their products as food. The analysis concludes that metabolic efficiency enhancements and the development of low-cost media from plant hydrolysates are both necessary but insufficient conditions for the measurable displacement of conventional meat by cultured meat. Analysis highlights Bioreactor design and scale-up principles are used to examine practical vol- umes and attainable cell densities in fed-batch and perfusion suspension cultures. Equipment costs consistent with appropriate levels of sterility assurance and commoditization are developed with process-industry estimation software and cost-factor techniques. ii iii Price-volume relationships are leveraged for demand-consistent forecasting of amino acid and protein prices in cell-culture media. The costs and suitability of speculative plant hydrolysates as cell-culture media are also considered. Process designs and production cost estimates are developed for conceptual fed-batch and perfusion facilities producing bulk animal cell mass within a total market of 100 kTA (wet basis). Both are examined in the context of a cellular metabolism significantly enhanced over a wild-type animal cell. A fed-batch facility of 24×20 m3 bioreactors is estimated to produce 6.8 kTA of wet cell mass at a production cost of $37/kg. Amino acids contribute 50% of this cost. Clean room costs limit the size of a single facility, while CO2 accumulation limits the volume of the production bioreactor. A perfusion facility of 96×2 m3 bioreactors is estimated to produce 6.9 kTA of wet cell mass at a production cost of $51/kg. The economics of perfusion are disadvantaged by the high installation costs of small bioreactors and the extra capital and consumables costs associated with the perfusion device. Both estimates exceed a price target of $25/kg wet cell mass asserted for consistency with 100 kTA consumption. Low-cost plant hydrolysate at $2/kg could reduce all production cost estimates by $15–16/kg. A fed-batch process with hydrolysate media would thus fall below $25/kg. Lower-grade mate- rials of construction, elimination of clean rooms, and additional metabolic enhancement offer smaller reductions. With either technology, reduced metabolic efficiency leads to catabolite-limited cell densities that cause the modeled production cost to increase beyond economically sustainable levels. Supplemental information An Excel spreadsheet containing the calculations in this analysis can be down- loaded at https://doi.org/10.17605/OSF.IO/AJSU9. Contents executive summary ii contents iv 1 introduction 1 1.1 Background . 1 1.2 Industrial scale-up perspectives . 3 1.3 Analysis approach: powers of ten . 9 2 technical aspects 13 2.1 Model cell characteristics . 13 2.2 Stoichiometry of animal cell growth . 15 2.3 Bioreactor design principles and limitations . 22 2.4 Aseptic operation . 31 3 economic aspects 34 3.1 Capital costs . 34 3.2 Costs of media components . 39 3.3 Fixed operating costs . 46 4 production cost studies 48 4.1 Fed-batch operation . 48 4.2 Perfusion operation . 59 4.3 Economic sustainability metrics . 66 5 concluding discussion 70 5.1 Summary . 70 5.2 Recommendations . 72 5.3 Related topics . 74 acknowledgments 77 bibliography 78 a baker’s yeast analysis 90 b physical properties used in the analysis 100 iv 1 Introduction 1.1 Background “Cultured meat” refers to a nascent field of bioproducts that aim to replace conventional meat produced by farming and slaughter with analogous or alternative products made from edible animal cell culture.1 In one concept 1 Alternatively, “lab-grown” or “in vitro” (Figure 1.1), animal cells from a live-animal biopsy are propagated through meat, along with other terms. During the a series of increasingly large bioreactors, growing in number with each step preparation of this report, the preferred term of art (according to consumer re- 3 and ultimately inoculating a 20 m bioreactor [4]. After a total cycle time search conducted by The Good Food In- lasting several months, 2–3 tons of animal cell slurry are harvested from stitute) shifted from “clean” [1] to “cell- based” [2] to “cultivated” meat [3]. For the this bioreactor. The cultured cell mass, perhaps blended with vegetable present discussion, “cultured” has been re- 2 tained as a neutral term indicating a prod- proteins and fats, can be further processed with enzymes and conventional uct of cell culture. extrusion/texturization operations into edible mincemeat- or nugget-style 2E.g., transglutaminase AKA “meat glue” food products. In Figure 1.1, these are indicated as “unstructured” products. [5]. Some developers, probably sensing consumer and investor ambivalence to such products [6,7], have further proposed that cultured animal cells be deposited onto an edible scaffold material that provides form and possibly hypertrophy, resulting in “structured” products that more closely resemble a cut of meat from an animal. To its proponents, cultured meat is positioned to address global prob- lems associated with industrial animal farming, such as its contributions to pollution, foodborne illness, and anthropogenic climate change [8–10]. The promises of cultured meat thus include resource-efficient production of human nutrition at a global scale and reduction of livestock populations to Primary cell culture Extrusion Texturization Blending Unstructured product Host animal biopsy Bulk cell production Differentiation Scaffolding Cell Cell line Hypertrophy bank development Structured product Figure 1.1: Conceptual cultured-meat production process. 1 background 2 pre-industrial levels. At the heart of cultured meat’s conceptual appeal is the further promise that all of this could be accomplished without requiring existing meat consumers to significantly change their diet [11]. In many cases, however, these promises are contingent upon, e.g, concomitant major advances in renewable energy [12], a wholesale “rethink” of the composition and cost structure of cell-culture media [13], presumptive future feedstock sources such as mass-cultivated algae or cyanobacteria [14], or a correction to the consumer price of conventional meat that brings it up to parity with its toll on the environment [15]. The consumer price of cultured meat, mean- while, is unknown. The present analysis was therefore commissioned to assess cultured meat’s potential to measurably displace the human consumption of conventional meat. The reader is likely familiar with Mark Post’s 2013 media event [16] in which a ~$325,000 (€250,000) lab-grown hamburger was presented to a panel of food critics. This figure was computed by totaling Post’s direct costs leading up to the event, including the wages of the scientists and technicians who labored for some months to make the item [17]. In 2015, Post offered a preliminary production-cost estimate for such products of $65/kg [18, 19], which some observers extrapolated to $11 per burger [20].3 Subsequently, 3In a historical aside, the original projec- this analyst has encountered bioproducts entrepreneurs and investors who tion was “eighty dollars” per kg, which somehow inferred from these events that Post et al. were able to reduce the resolves to $11 for a 5-oz burger. These words, however, were not uttered by Post, cost of animal cell culture by five orders of magnitude in two years. The reader but by an Australian radio reporter [18] may also be familiar with this sentiment regarding cultured meat, which is and had likely been converted to AUD for the audience. Later that week, it was re- expressed in the popular media through hopeful invocations of “Moore’s law” ported that Post had claimed a production cost of USD 65/kg [19], consistent with and awed remarks about the steadily declining price of something that is not the exchange rate at the time. available for purchase [21–25]. Ultimately, however, there is no responsible comparison to be made between these two costs. The lower figure was merely a scale-up projection—an opaque one at that, as its details were not published for examination.
Details
-
File Typepdf
-
Upload Time-
-
Content LanguagesEnglish
-
Upload UserAnonymous/Not logged-in
-
File Pages104 Page
-
File Size-