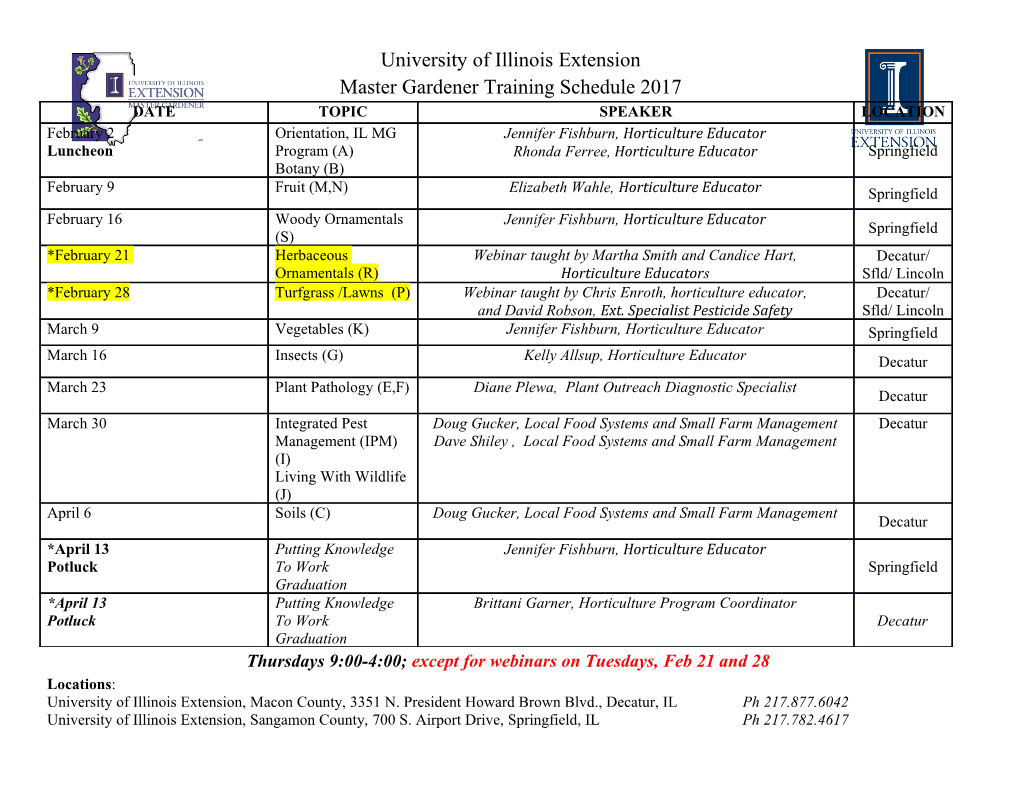
HAND PAPERMAKING NEWSLETTER Number 122, April 2018 Newsletter Editor: Shireen Holman Dear Readers, Columnists: Sidney Berger, Maureen and The identification of local and avail- Simon Green, Donna Koretsky, Winifred able resources and their safe Radolan, Amy Richard conversion into something useful, Hand Papermaking Newsletter is published something needed, is a powerful quarterly. Annual subscriptions are $55 in human activity. I would like to spread North America or $80 overseas, including two the word about The Invasive Paper issues of Hand Papermaking magazine. For Project, which does just that. This more subscription information, or a list of back project is about material exploration issue contents and availability, contact: and community exchange, rather than Hand Papermaking, Inc. an initiative focused on the art and PO Box 50859, Mendota, MN 55150-0859 craft of making paper. Phone: (651) 447-7143 I had been intrigued when a E-mail: [email protected] friend told me that the youth from Web: www.handpapermaking.org the Student Conservation Association (SCA) were removing invasive weeds in Detroit. To me, this “waste” posed both an interesting The deadline for the next newsletter (July 2018) challenge and an opportunity. My research led me to the work of Patterson Clark, who has been is May 15. Please direct correspondence to making beautiful paper and art objects from invasive plants; Julie Johnson, who wrote about her the address above. We encourage letters from our experiences with invasives in Hand Papermaking;1 and of course Helen Heibert, who originally subscribers on any relevant topic. We also solicit taught me papermaking, and whose book Papermaking with Plants2 has been indispensable to me. comments on articles in Hand Papermaking I knew nothing like this existed in Detroit and I needed to lead the charge. The young people magazine, questions or remarks for newsletter from the SCA Detroit showed me how to skillfully remove Amur honeysuckle. Back at the studio columnists, and news of special events or activities. I successfully rendered a gentle, yellow-hued paper. Next, I gave garlic mustard a try. A different, Classified ads are $2.00 per word with a 10-word more rigid, and fragrant paper was the result. In exchange for their expertise, I had the youth minimum. Rates for display ads upon request. come to my studio to learn about papermaking. It was significant for these young people to Hand Papermaking is a 501(c)(3) non-profit convert the unwanted plants, plants they had spent countless hours removing, into some- organization. Staff: Michael Fallon, Executive thing of value with their own hands. The alchemical magic of papermaking wasn’t just for Director; Mina Takahashi, Magazine Editor; me, but something that I could share with others in a meaningful way. The photo above, by Shireen Holman, Newsletter Editor; Karen Kopacz, Eric Wheeler, shows us in one of the workshops. Designer. Board of Directors: May Babcock, Tom As the Invasive Paper Project travels beyond Detroit to other locales in the US, it acts as Balbo, Lisa Cirando, Kerri Cushman, Tatiana a method of sharing plant stories, landscape stories, and stories about how we situate ourselves Ginsberg, Joan Hall, Mary Hark, Steve Kostell, in our places. Follow the project at meganheeres.com or @megheeres on Instagram. Daniel Murphy, Alta Price, Michelle Samour, Megan Heeres Flora Shum, Teri Williams. Board Student Detroit, Michigan Representative: Sarah Luko. International Board of Advisors: Yousef Ahmad (Qatar), 1. See Julie Johnson, “Using Invasive Plant Fibers Responsibly,” Hand Papermaking 25, no. 1 Timothy Barrett (US), Simon J. Blattner (US), (Summer 2010). Kathryn & Howard Clark (US), Mandy 2. See Helen Hiebert, Papermaking with Plants: Creative Recipes and Projects Using Herbs, Coppes-Martin (So. Africa), Jane Farmer (US), Flowers, Grasses, and Leaves (1998). Peter Ford (UK), Helen Frederick (US), Peter & Pat Gentenaar (Netherlands), Simon Barcham Green (UK), Helen Hiebert (US), Dear Handmade Paperistas, Therese Hofmann (Brazil), Dard Hunter III (US), Kyoko Ibe (Japan), Winsome Jobling Western Renaissance papers have sharp curly marks impressed on the surface by the rough (Australia), Elaine Koretsky (US), Carolina woolen couching felts used by early papermakers. Optimal for chalk drawings and pastels Larrea (Chile), Roberto Mannino (Italy), (a Renaissance invention), this “tooth” established paper as an ideal medium for Old Master Beatrix Mapalagama (Austria), Bob Matthysen artworks. However, not everyone was happy with the rough surfaces. (Belgium), Radha Pandey (India), Giorgio Printers, and especially copyists and writers, required more even paper. Their demands Pellegrini (Italy), Brian Queen (Canada), were heard and met. Today, industrial paper is silky-smooth, perfect, and cheap. Machines Victoria Rabal (Spain), Vicky Sigwald (Argen- provide artificial random tooth only on purpose; no handmade-curly. tina), Lynn Sures (US), Aytekin Vural (Turkey). Unless one raids old book collections for end papers, our tooth has been lost and unavail- Co-founders: Amanda Degener and Michael able for the last couple of centuries or so. Meanwhile even sheep have gone soft, as Donald Durgin. Cont. on next page Farnsworth recounts in A Quest for the Golden > ALONG THE PAPER ROAD... But they obviously used an excellent retention Fleece,1 his description of his efforts to replicate agent. Brian immersed his hand into the Renaissance woolen felts. Since 1998 this column has featured paper mus- black pulp and when he lifted it out the water When I was visiting Rix Jennings in ings from Elaine Koretsky—renowned paper ran clear. Houston in mid-2017, he showed me a sample historian, researcher, and traveler. Her daughter Finally we arrived at the machine that of fiberglass “landscape fabric.” Experiment- Donna Koretsky now continues the legacy. In makes the cones, where each cone is made ing with a new vacuum table strainer in this description of her visit to Loudspeaker individually from pulp by a mechanized cast- November, I pressed paper and let it dry on Components, Donna surprises us with the details ing method. The cone-shaped mold is made this fabric. To my extreme surprise, the of how speaker cones are made from paper pulp. from thick metal that has quarter-inch holes surface looked ancient, museum-like “curly”! drilled into it and the back hollowed out. A think about paper pulp and paper a lot. It turns out that couching, pressing, and cone-shaped piece of brass screening is placed But the realization that paper can be a drying on conventional fiberglass landscape I on top of the mold. These two pieces are medium for sound is something I had never fabric from home improvement stores mimics fastened together and mounted on something considered until my recent visit to a factory quite well the gouges and sharp tooth loved called a mold wheel. that manufactures speaker cones from paper by Italian Cinquecento artists. A serendipitous It is a fascinating casting method. The pulp. I learned that nearly all speakers used discovery, this new/old Renaissance surface cone-shaped mold is suspended over a round in the music industry use paper-pulp cones, imitation is easy to achieve, and I invite stainless-steel trough filled with black pulp from tiny cones found in automobile speakers y’all to make it. Hand Papermaking being a that is constantly agitated to maintain con- to large cones used in high-end speakers. “journal of record” for all things papermaking, sistency. Suddenly the vat of pulp rises up, Loudspeaker Components, located I’m honored to share this innovation here, immersing the suspended cone in pulp. The deep in the farmlands of southwest Wisconsin, hopefully helping to increase interest and vat stays up for about two seconds during is the leading manufacturer in the US demand for what we make, especially among which time there is a powerful vacuum that of speaker cones made from paper pulp. charcoal, chalk, and pastel artists. sucks the pulp onto the form and the Thousands of paper cones are produced water is pulled through the holes of the mold. daily and shipped worldwide to customers When the trough of pulp is lowered, a cone such as JBL, who assemble the speakers. of pulp magically adheres to the mold. Next On a brisk wintry day, Brian Haas, who the drum rotates and there is another cone- owns the company along with Neil Kirsch- shaped form that is immersed into the pulp. baum, graciously showed me around their Meanwhile the newly vacuumed paper cone 55,000-square-foot facility and patiently rotates into an oven where it dries in sec- explained the cone-making process. onds and the machine operator pops it off The first part of the tour was familiar the mold. territory. Bales of paper pulp were piled high, Consistency is key and every cone is and numerous 55-gallon drums of sizing, I named my version Cinque Tooth. In weighed on a scale. If one does not meet a retention agent, colorants, and all sorts of the photo you can see mine (labelled B) in certain parameter, it is thrown in the trash additives were on their sides, obviously used between two Italian papers from the early and not recycled. Needless to say, at the end on a daily basis. Brian’s voice competed with 1600s. There is more information about my of the day I left the factory with a bag of the loud rumblings of the factory machines. research and fun on my site, papeltexano. cone rejects of all different sizes and shapes A 25-lb. Valley beater, along with two enor- org/cinque. Your comments and advice are and shades of black. I also collected a few mous refiners, process about 320 pounds of much appreciated. reject dust caps, which are small convex pulp a day. A combination of pulps is precisely domes that fit over the central hole of the beaten according the specifications of the Yama Ploskonka speaker cones.
Details
-
File Typepdf
-
Upload Time-
-
Content LanguagesEnglish
-
Upload UserAnonymous/Not logged-in
-
File Pages12 Page
-
File Size-