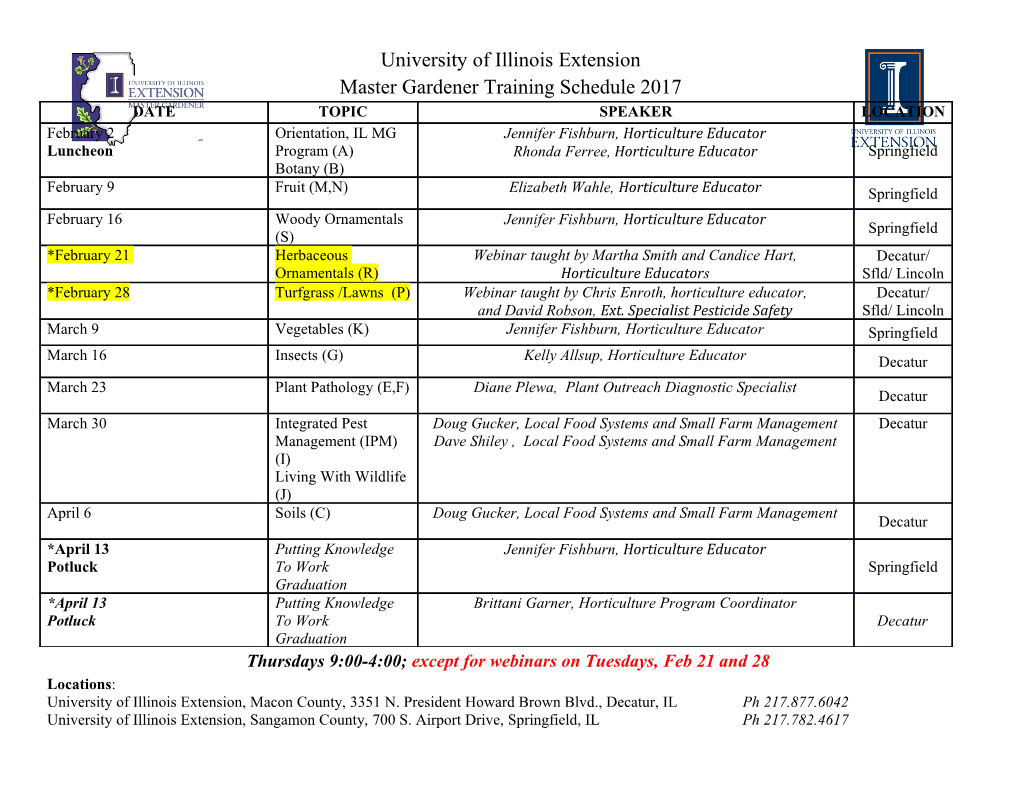
id44729227 pdfMachine by Broadgun Software - a great PDF writer! - a great PDF creator! - http://www.pdfmachine.com http://www.broadgun.com MAGNESIUM USAGE BY MARKET (End of 2002) MAGNESIUM ALLOY DEVELOPMENT FOR HIGH-TEMPERATURE AUTOMOTIVE APPLICATIONS ALUMINUM ALLOYING 146 K MT 40% OTHERS including Mihriban Pekguleryuz gravity casting & McGill University MAGNESIUM wrought alloys (mainly Metals & Materials Engineering DIECASTING aerospace) Automotive ALLOYS 20 K MT & electronics 128 K MT DESULF. 5 % industries 57 K MT 35 % CHEM ICAL, ELECTRO- 16% CHEM ICAL, METAL January 2004 REDUCTION NODULAR IRON TOTAL : 365 K metric tons 14 K MT 4 % AUTOMOTIVE USE OF MAGNESIUM AUTOMOTIVE USES OF MAGNESIUM CURRENT USE: INTERIOR MID-TO-LONG-TERM Growing use of magnesium in automotive • Growing use of magnesium in automotive COMPONENTS applications in the 90’s e.g. I nstrument Panel, BODY steering wheel e.g Inner door panel, pillar structures - Stiffness, high ductility - Wrought products (formability) • valve covers to steering wheels, - Energy absorption - Structural casting alloys (ductility) R- equires new alloys and processes instrument panels, AM alloys seat-frames. STEEL 50lb-Mg 18lb CHASSIS e.g. Wheel, suspension arm SHORT TERM : POWERTRAIN - Strength e.g. Transmission case, engine parts - High ductility, fatigue - Creep resistance (150-200C) - Corrosion resistance - Yield strength -R equires new alloys AZ91D - Corrosion resistance AM60, AM50, AM20 - Mg-Al-RE & Mg-Al-Si Requires new alloys Mg-9Al-1Zn Mg-Al-Mn alloys ALLOY DEVELOPMENT ALLOYING BEHAVIOR OF MAGNESIUM FOR MAGNESIUM HIGH-TEMPERATURE APPLICATIONS FOR MAGNESIUM HIGH-TEMPERATURE APPLICATIONS Strength -- solid solution hardening & second phase hardening, PHASE I: 1992-1997 HUME-ROTHERY RULES - Atomic size ratio (15%) Development of Industrial Trials d Mg = 3.2 Å Learning preliminary alloys Li, Al, Ti, Cr, Zn, Ge, Y, Ce, Zr, Nb, Mo, Pd. Ag, Cd, In, Sn, Sb, Te, Nd, Hf, W, Re, Os, Pt, Au, Hg, Tl, Pb, Bi, Alloying & creep ITM Alloy behavior of IMRA Alloy - Similar Crystal Structure Mg and its alloys Honda Alloy - Similar Crystal Structure Zn, Cd (%0.9) PHASE II: 1998-2003 - Relative Valency Effect Group II - Group VII Commercial Prototyping & Development of alloys & evaluation improved alloys - Electro-negativity applications Compound formation BMW engine block Noranda Alloys GM Alloy * M. Pekguleryuz, M. Avedesian “Magnesium Alloying-Some Metallurgical Aspects,” DSM Alloy Magnesium Alloys and Their Applications, DGM, 1992, pp. 213-220 1 Mg-Al & Mg-Al-Zn ALLOYS ALLOYING BEHAVIOR OF MAGNESIUM AZ91, AM20, AM50, AM60 casting alloys Precipitation hardening alloys Good R.T strength & ductility - Elements that Increase both Strength and Ductility AZ31, AZ61 wrought alloys LOW CREEP RESISTANCE Strength Criterion : Al, Zn, Ca, Ag, Ce, Ga, Ni, Cu, Th, Y AZ80 forging alloy Ductility Criterion : Th, Y, Ga, Zn, Ag, Ce, Ca, Al, Ni, Cu - Elements that Increase Strength at the Cost of Ductility Sn, Pb, Bi, Sb - Elements that Increase Ductility but not Strength Cd, Tl, Li, Mn - Creep Mg17Al12 RE, Y, Ca, Cu, Th, Ag CREEP DEFORMATION CREEP -- THE TIME DEPENDENT STRAIN CREEP STRENGTH OF Mg DIECASTING ALLOYS •slow, continuous deformation with time. = f() elastic/plastic deformation, = f(, T, t) creep deformation Due to the thermally activated stress component (short range component) ) ) = u + * a a P P = u + * M M ( ( s s CREEP RATE s s e e r r t strain rate at a given stress is temperature t S S sensitive. Ý = A e (-q/kT). e(*/kT) n Dislocation Creep Ý = A e (-Q/RT) dislocation intersection, dislocation climb, movement of dislocation atmospheres, cross-slip, grain-boundary shear. Diffusion-Creep Ý = B e (-Q/RT) fast diffusion paths (dislocation cores or GB) or bulk diffusion (vacancy and interstitial) Temperature (C) (qd or qs) T> 0.3 Tm CREEP MECHANISMS--What can be Thermally Aided ? CREEP BEHAVIOR OF Mg DIECASTING ALLOYS • Dislocation Intersection - work required to force a dislocation 2 through the stress field of another can be thermally aided. Ý = A e [-(qi - *b l)/kT] Mg single crystals AZ91D, AS21, AE42 • Activated Cross Slip - Thermally activation to unite partial q =100 kJ/mol dislocations and to breakdown into partials on different for high stacking fault metals 150 C, 150 C, slip systems. 50 MPa 2 • Movements of Dislocations with jogs - formation (qf) and Ý = A e [-(qd - *b x)/kT] movement (qm) of vacancies. Self diffusion (qd = qf + qm). qd Mg 135 kJ/mol, q Mg 125 kJ/ mol. • Dislocation Climb - Climb of dislocations over sessile Ý = A e (- qd ) / kT dislocations or precipitates. Vacancy diffusion to and Ý = Be e (-qd ) / kT from edge dislocations (qd) and formation of jogs (qj) . q in the range of qd (135kJ/mol) Activation energy, q = qd + qj •Movement of Dislocation Atmospheres - Diffusion of solute Ý = A e (- qs ) / kT atoms and the viscous behavior of the solute atmosphere qAl in Mg 143 kJ/mole •Grain Boundary Shear - relative movement of grains, deformation in very narrow region adjacent to the GB, the shear direction lies in the boundary with the max resolved shear stress. Affective at high temperatures, usually when the recovery temperature is achieved. Discontinuous. GBs recover before the grains, softening. Accounts for 30% of the deformation. Grain boundary diffusion: 80 kJ/mol. M. S. Dargusch, G.L.Dunlop, K. Pettersen, Proc of Conf. on Magnesium Alloys and their Applications,” B.L. Mordike and K.U. Kainer, Eds,, Wolsburg, Germany, 1998 pp. 277-282. 2 CREEP BEHAVIOR OF Mg-Al ALLOYS (AZ, AM) CREEP BEHAVIOR OF Mg-Al-RE ALLOYS (AE) AZ91D -- Activation energy in Ý=Anexp (-Q/RT), 125-175°C, 50 MPa Mg-Al-RE was 30-45 kJmol-1, n=2 • Activation energy 35-40 kJmol-1 self-diffusion of Mg (135 kJmol-1) or • Higher creep resistance diffusion of Al in Mg (143 kJmol-1) or • Stable Al-RE containing phases grain boundary diffusion (80 kJmol-1) AE42 ALLOY • No Mg17Al12 phase but some Al coring Al-RE Q for discontinuous precipitation of Mg17Al12 = 30 kJ/mol Creep induced Mg17Al12 aids easy grain boundary sliding and migration. At higher stresses: 95 kJ/mol, n = 5 Activated cross slip Dislocation intersection ? M. S. Dargusch, G.L.Dunlop, K. Pettersen, Proc of Conf. on Magnesium Alloys and their Applications,” B.L. Mordike and K.U. Kainer, Eds., Wolsburg, Germany, 1998 pp. 277-282. M. S. Dargusch, G.L.Dunlop, K. Pettersen, Proc of Conf. on Magnesium Alloys and their Applications,” B.L. Mordike and K.U. Kainer, Eds,, Wolsburg, Germany, 1998 pp. 277-282. ALLOY DESIGN FOR CREEP IN Mg DIECASTING ALLOYS Metallurgical Stability in Mg-Al-RE ALLOYS (AE) GENERAL PRINCIPLES T (C) Mg Al11RE3 Al 2RE Mg17Al12 AVOID Mg17Al12 As-cast 97.5 1.8 0.8 0.0 creep induced precipitation, e.g. Mg17Al12 25C aging, microstructural instability Sr, Ca, RE 150 C 97.7 1.5 0.8 0.0 STRONG GRAIN BOUNDARIES High temperature surface active solutes Sr, Ca, RE (a) (b) 97.0 1.2 1.3 0.6 175 C 97.0 1.2 1.3 0.6 Second phases (line compounds, Sr, Ca, RE Microstructure of AE42 (a) diecast (b) after 175C exposure coherent particles) Sb, Bi MICROSTRUCTURAL MODIFICATION Sr, Ca, RE Sb, Bi, Sn Ref : B. R. Powell, V. Rezhets, M.P. Balogh, and R.A. Waldo, “Microstructure and Creep Behavior in AE42 Magnesium Die-Casting Alloy”, Journal of Metals, TMS, August 2002, pp. 34-38 * M. Pekguleryuz, M. Avedesian “Magnesium Alloying-Some Metallurgical Aspects,” Magnesium Alloys and Their Applications, DGM, 1992, pp. 213-220 GRAIN BOUNDRY PINNING RATIONALE FOR ALLOY SYSTEM SELECTION AL Sr • AVOID COSTLY OR RARE ELEMENTS (Sc, Rare earths, Ag, etc) 4 Space Group: I 4 / mmm • MAINTAIN ALUMINUM FOR GOOD DIE CASTABILITY (5-6%) Body centered tetragonal a = 0.445 nm c = 1.105 nm • USE ALKALINE EARTH ELEMENTS (Ca, Sr) - second phases for grain boundary pinning Mg-5Al-1Sr - solute segregation Mg-5Al-2Sr Mg-Al-Sr Mg-6Al-2Sr SYSTEM • AVOID ELEMENTS THAT CAN ADVERSELY EFFECT CORROSION (Cu, Ni) • CHOOSE TERNARY SYSTEMS FOR SIMPLICITY & COST AND EASE OF MANUFACTURING • Mg-Al-Sr SELECTED AS THE OPTIMUM ALLOY SYSTEM TO DEVELOP 3 Mg-Al-Sr ALLOY COMPOSITIONS Microstructure of Diecast AJ Alloys Alloy designation : AJ Alloys where J designates Sr AJ51x AJ52x AJ62Lx AJ62x Al Sr ALLOY wt. % wt. % -Mg solid solution and a lamellar -Mg and intermetallic ( Type A ) AJ51x 4.5 - 5.5 1.2- 1.5 Type A Type B AJ52x 4.5 - 5.5 1.6- 2.3 intermetallics A-type AJ62x 5.5 -6.5 2.0- 2.6 AJ62Lx 5.6 -6.6 1.5- 1.9 Sr/Al < 0.3 Sr/Al > 0.3 Mg-Al-Sr Alloy Phases Solidification Curves of AJ51x and AJ52x Mg-Al-Sr Alloy Phases -1..5 Philips X’Pert diffractometer - Cu K radiation AJ51x Using XRD coupled with Liquidus: AJ51x Al4Sr 2500 617-618°C +-Mg AJ52x analytical STEM AJ51x -- DC ) ) s 2000 s -1 / AJ62x, AJ51x: / C C ° 1500 ° r r ( 4 4 ( S Type-A compound is S r r 4 4 0 0 0 l S 0 l S r 0 4 2 r 0 4 r 2 r l A l 1 A r S 1 4 r S 4 0 S 0 S e 0 e 4 0 1 A S 4 4 1 A 2 S 4 l 2 isomorphous to Al Sr and l r l r l 4 4 2 0 2 l t 0 4 1 0 l 4 t S 1 0 S 1000 A A 1000 A 2 A 2 4 2 4 2 A l A l 1 a 1 a A A Al/Sr ratio is close to Al Sr r Al/Sr ratio is close to Al Sr r 2 4 2 4 S S 4 0 4 0 -0.5 l R l -0.5 R 0 0 A A with some Mg in solution.
Details
-
File Typepdf
-
Upload Time-
-
Content LanguagesEnglish
-
Upload UserAnonymous/Not logged-in
-
File Pages10 Page
-
File Size-