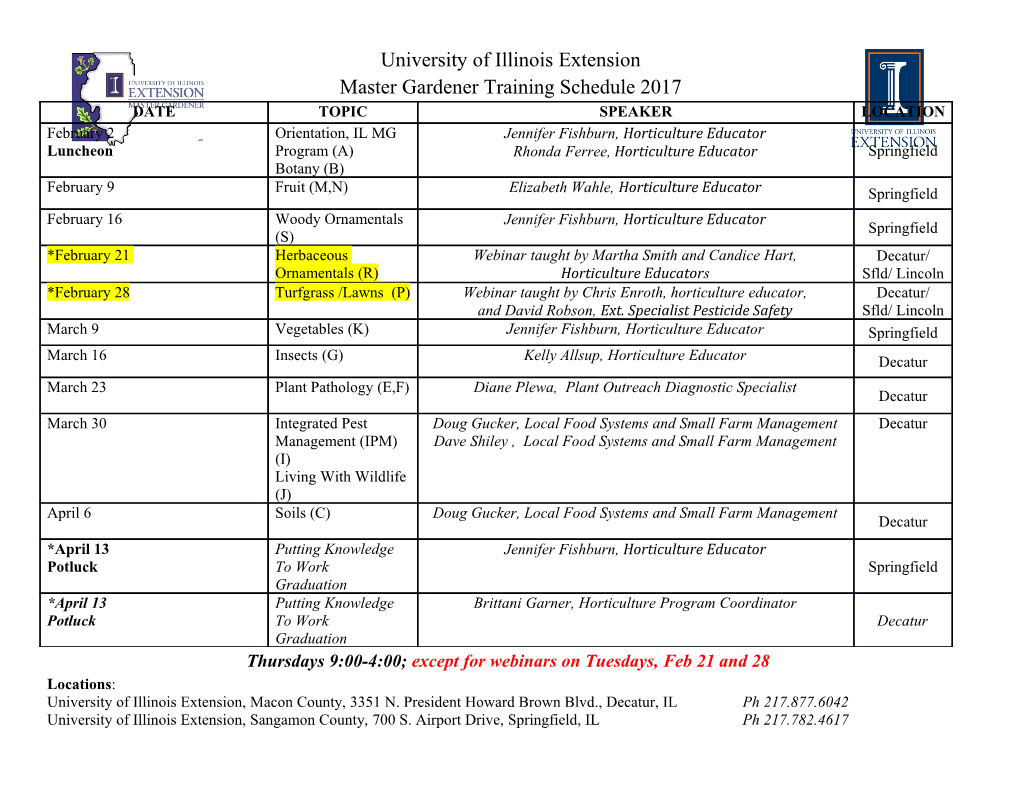
OPTIMIZING QUALITY: ENHANCE YOUR LEAN MANUFACTURING JOURNEY Sponsored by This eBook was compiled from a series of articles written for the Manufacturing Transformation Blog on Lean manufacturing. Just as the world of Lean has a goal of continuous improvement – so too is the learning of how to continue on your Lean journey. We hope you find this collection of articles interesting, thought provoking and educational. 2 SPONSORED BY DASSAULT SYSTEMES Contents It’s Time for a Lean Manufacturing Makeover 4 Taking Lean to the Supply Chain 6 Taking a Lean Approach to Quality 8 Three Ways to Improve Quality with Lean Manufacturing 10 A Lean Approach to Management 12 Lean Management Part 2: Continuous Improvement 14 Golf Lessons from Lean, Six Sigma and TOC 16 Lean Manufacturing and the World of Warcraft 18 The Authors 20 SPONSORED BY DASSAULT SYSTEMES 3 IT’S TIME FOR A LEAN MANUFACTURING MAKEOVER - BY FRED THOMAS Manufacturing has changed a lot since the 1950s when Toyota Motor Company of Japan introduced the concept of implementing an integrated process to more efficiently manage equipment, materials and its workforce throughout the production cycle. Over time, this technique allowed Toyota to deliver more reliable, higher-quality products faster — and at a lower cost — than other mass produced automakers. By the time we entered the 1980s and 1990s, the practice of eliminating waste to create customer value with fewer resources had caught on in the U.S. and other countries. Fast-forward to 2014: While the concept and best practices of the Lean production system remain intact, the implementation on the plant floor faces a major facelift. That’s simply because the entire manufacturing dynamic has transformed to include new technology, new global competition, new government regulations, and a hyper-connected world of intelligent devices and social networks that enable seamless communication between companies and their customers. Times have changed. And, in order to remain an agile manufacturer, Lean methodologies must adapt and change too. Otherwise, organizations will remain stuck in the 1950s while the competition soars into 21st century manufacturing. Before rushing into a new Lean manufacturing model, however, it’s a worthwhile exercise to take a step back to identify what’s different and the direct impact it has on Lean processes. 4 SPONSORED BY DASSAULT SYSTEMES 1. Technology is a good thing 4. Government regulations Early pioneers of Lean systems pursued strategies of removing IT from production New regulations emerge in specific industries all of the time, forcing companies to processes, viewing this technology as an additional step which could be “leaned” out of reexamine processes. The Food Safety Act, for example, is a sweeping reform of food processes to remove waste. This philosophy was probably reasonable in the 1970s when safety laws. That means, back to the drawing board for many companies—especially those technology was in its early, nascent stages; today, however, is a completely different companies that are still paper-based. Time to digitize processes and reevaluate how quality situation with a level of complexity that necessitates reliance on IT systems to remove the practices are implemented, tracked, and audited. waste of manual processes. 5. Hyper-connected communication 2. Leveraging the right technology The new customer service interface is social media—especially from a mobile device. This Manufacturing Execution Systems (MES), Manufacturing Operations Management (MOM) means someone can post a comment or photo about your product anytime, anywhere. and Enterprise (MI) have become instrumental in the quest to add efficiency into scheduling And, they expect an immediate response. Manufacturers must somehow capture the production, tracking inventory, synchronizing material flows and increasing visibility across information—down to every last tweet—and sift through it to identify trends that can be the supply chain. The Just-in-Time mentality to deliver product is now being transplanted pushed back into the research, development, and production cycles. by a need to be more predictive and insightful. Manufactures need to know what customers want—and for that, they are turning to Big Data and predictive analytics. While Big Data Lean manufacturing is still a very relevant business practice. But, like everything else deals with different data sets that don’t always seem relevant to the plant floor, everything in manufacturing, the process must progress to keep pace with the organizational in the from the supply chain, plant floor, enterprise, and beyond must be interconnected in shifts happening all around it. Perhaps that means new conversations will have to take today’s day and age. Therefore, it’s time to analyze the impact of every data stream on the place between CIOs and manufacturing executives. Or, that traditionally accepted best production of goods. manufacturing practices have to get better. Either way, Lean is not going away, it’s just in a new phase of innovation and transformation. 3. Global competition Cost pressure and the need to locate closer to end users has only accelerated the push to go What will your Lean strategy look like in the future? global; as a result, the need to understand foreign cultures and designing new products and services for them has never been more acute. Lean must now be agile to support continuous innovation while comprehending the complexity associated with an ever-changing, fast- paced global world. All of these elements require a fresh look at Lean manufacturing practices. SPONSORED BY DASSAULT SYSTEMES 5 TAKING LEAN TO THE SUPPLY CHAIN - BY RICK GALLISA Most large manufacturers today have established Lean or Six Sigma programs for their own operations. It’s practically a requirement to be competitive. But the line between a manufacturer’s “own” operations, and those of its partners, is getting fuzzier all the time. With today’s increasingly connected supply chains, demand- driven supply networks, and global operations, it only makes sense that big opportunities for performance improvement and cost reduction might be out there in the supply chain, just waiting to be discovered. The benefits of a Lean supply chain might be a good thing – or might not, depending upon your perspective. But is it realistic? Considering that Lean and Six Sigma programs are all about consistency and control, and involve cultural and operational transformation, can a manufacturer really expect to extend these practices outside of its own organization? And, at what cost? Pundit Perspective A new report from Gartner, “Transform Your Supply Chain to Become Demand-Driven,” cautions that creating a Lean supply chain is a journey, and won’t be easy. The authors write, “Companies striving to become demand-driven must recognize that functional integration is a prerequisite — and that it is extremely difficult to achieve. Fewer than 10% of companies that have assessed their supply chain maturity, rate it as integrated.” Nevertheless, Gartner recommends enterprises pursue the goal, and many are starting to do just that. 6 SPONSORED BY DASSAULT SYSTEMES Early Signs of Success Supporting and enabling all these efforts, of course, is ever-advancing technology A recent article in Industry Week called “Lean into the Supply Chain” describes several that makes it possible for more and more people and operations to communicate and examples of global manufacturers who have taken up the challenge, some with striking synchronize. As Paul Myerson, professor of supply chain management at Lehigh University, success: says in the article, “technology not only enables lean but it can help identify and eliminate waste by substituting information for inventory.” • Pratt & Whitney, the aircraft engine manufacturer, aims to triple jet engine production by 2020, with hundreds of suppliers. To keep control, the company has created an In other words, success with applying Lean manufacturing methodologies across “Operations Command Center,” which gathers and shares information about the delivery a distributed global supply chain is heavily dependent upon visibility, control and status of 400 suppliers worldwide, with early warnings if schedules might slip. synchronization of material flows such that as issues present themselves, they can be quickly remedied to avoid potential for large disruptions. • USG Corp., which produces and distributes gypsum wallboard, joint compound and related construction products, has trained all 100 employees in its supply chain Based on the experience of these companies, it looks like information is a lot cheaper to organization in Lean and Six Sigma; the company saved almost $10 million last store and manage than inventory. And, it certainly can be transported far more easily! year while improving operational efficiencies. Says a spokesman, “If we have a warehouse in one region with stock-out problems, we’ll involve production, transportation, logistics, What do you think? Is your enterprise ready to “Lean into the supply chain”? etc., to solve that problem. We’ll use enterprise value stream mapping from several locations throughout the entire process.” • MTU America, a Rolls-Royce Power Systems and Daimler subsidiary, created a 400,000 square-foot aftermarket logistics center. They report “huge gains” in on-time delivery and productivity, but say “the biggest accomplishment has been improved customer satisfaction.” • Even healthcare, an industry that traditionally has lagged behind in this kind of technology, is “leaning” its supply chain. Intermountain, a non-profit healthcare system of more than 20 hospitals in the southwest United States, opened a 327,000 square-foot Supply Chain Center equipped with the “latest warehousing technology, such as a new warehouse management system, a cubing and dimensioning system, and an automated conveyor system.” They hoped to save $80 million in five years. Instead, they did it in two! SPONSORED BY DASSAULT SYSTEMES 7 TAKING A LEAN APPROACH TO QUALITY - BY MILOSZ MAJTA We live in a world where every manufacturing process is under intense scrutiny, with objectives ranging from improving efficiency, cutting waste or reducing costs.
Details
-
File Typepdf
-
Upload Time-
-
Content LanguagesEnglish
-
Upload UserAnonymous/Not logged-in
-
File Pages21 Page
-
File Size-