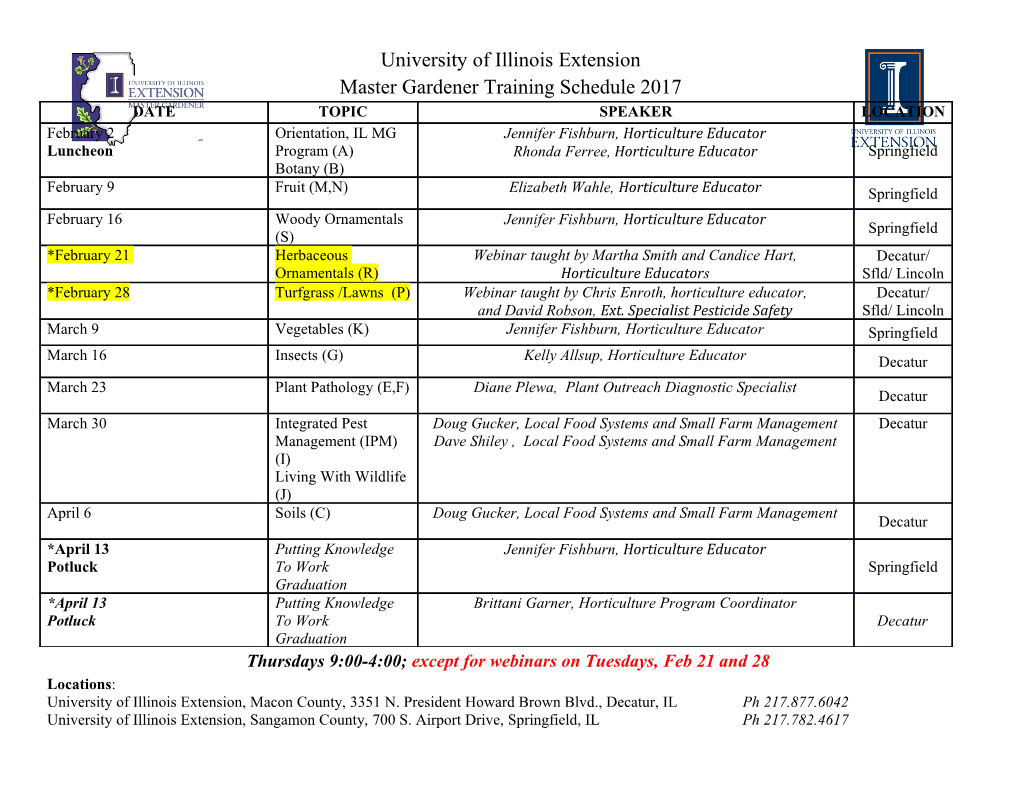
2016 / 2017 EN I DE MAGAZINE Gear Technology and Automation Systems Gear Technology: Internal gears with that Liebherr finish // P. 18 Automation Systems: Bin picking: We are targeting your workpiece // P. 20 In Practice: Case studies // P. 24 New vision system We are targeting your workpiece The Executive Directors of Liebherr-Verzahntechnik GmbH (from left to right): Dr. Klaus Finkenwirth, Dr. Christian Lang and Dr. Hans Gronbach Dear readers, We’re delighted that you are holding the fourth edition of Liebherr’s gear-cutting technology and automation systems magazine. This issue will showcase an abundance of innovations – you’ll see how we are transforming gear-skiving into a reliable pro- cess and thus creating new gear machining opportunities. We will present our new gear-shaping machine, which was specifically designed for high precision shaping of small pinions and multiple gear teeth, meeting the high standards of the aero- space industry. To round off the gear-cutting technology topics is our new grinding heads for internal gear teeth. Our automation division has revolutionary technology to offer as well – a new im- age recognition system for our bin picking robot application. Smaller components can now be picked from deeper bins in shorter cycle times. We also showcase the newly developed LP100 loading gantry, which coincides with the “rightsizing” trend. Every user can now find the optimum size of loading gantry for their needs in Liebherr’s portfolio. We would also like to introduce a new colleague, who has joined the Management Board of Liebherr-Verzahntechnik GmbH – Dr. Hans Gronbach. Dr. Gronbach has been the Chief Development and Design Engineering Officer since June 2016, and is responsible for championing innovation. He has a doctorate in mechanical en- gineering. His CV includes positions in both science and business; in-depth de- velopment experience and knowledge of machine tool markets. This makes him a perfect addition to our team – he will help guide Liebherr-Verzahntechnik GmbH into a successful future and enable the company to provide the best products for the markets of tomorrow. Your needs are our incentive and inspiration. We hope this magazine will provide you with some inspiration in return. Dr. Klaus Finkenwirth, Dr. Christian Lang and Dr. Hans Gronbach The Executive Directors of Liebherr-Verzahntechnik GmbH 2 Liebherr Magazine 2016 / 2017 – Gear Technology and Automation Systems Content Gear Technology “Quality, flexibility, availability” Skiving³: Machine – Tool – Process Bauer Gear Motor produces geared components on LC 180 gear-hobbing machines 27 The new LK 300 / 500 gear-skiving machine makes gear-skiving a more reliable process 4 Liebherr World Skiving instead of broaching Liebherr 4.0 Liebherr’s gear-skiving tools meet stringent requirements 8 The “smart factory” in Kempten – and by customers 30 Small and flexible Represented around the world New shaping machine for small workpieces: the LS 180 F 10 New branches in Europe and Asia 32 Finger milling 2.0 “Our super talent pool” Innovative technology for special gear teeth 12 Liebherr-Verzahntechnik GmbH trains people out of conviction 34 The best of two machine platforms Conferred with outstanding partner award Our LGG-range grinding machines are being reconfigured, Liebherr-Verzahntechnik GmbH wins John Deere Award 36 including adding more grinding heads 15 Automation division boosts presence Internal gears with that Liebherr finish New branches and cooperations boot the market presence 36 New grinding heads can also machine internal gear teeth to Liebherr standards of quality 18 Grinding machine for the aviation industry Liebherr-Aerospace Lindenberg GmbH produce on LGG 280 37 Automation Systems Bin picking: We are targeting your workpiece “As I see it, the crane’s rope is its heart” A new vision system improves accuracy and component High-strength fibre ropes revolutionize the use on cranes 38 recognition 20 In retrospect: Liebherr catches the Bauma bug Fast, powerful and flexible Liebherr made its presence felt at the show: record-breaking The LP 100 loading gantry provides a modern automation concept 22 machines on a record-breaking booth 40 In Practice Product and services overview A neat solution An overview of Liebherr-Verzahntechnik GmbH’s range of Weishaupt redesigns one of its production facilities using two products and services 42 Liebherr-Verzahntechnik GmbH pallet handling systems 24 We are Imprint targeting Publisher / Responsible for content: your Liebherr-Verzahntechnik GmbH workpiece Kaufbeurer Straße 141 87437 Kempten / Allgäu, Germany Editorial staff: Walter Ferstl, Dr.-Ing. Hansjörg Geiser, Manfred Kaut, Ottmar Kern, Thomas Mattern, Dr.-Ing. Andreas Mehr, Karl Sauterleute, Florian Schuon, Sebastian Schuster, Thomas Weber, Ronja Wildberger, Martin Winterstein, Dr.-Ing. Oliver Winkel, Thomas Zeller, Sandra Ziemons Issue: New 2016 / 2017 vision system Layout / Design: C&G: Strategische Kommunikation GmbH, Overath, Germany © Liebherr-Verzahntechnik GmbH No part of the contents of this magazine may be reproduced or published in any form or by any means without the consent of the publisher. Liebherr Magazine 2016 / 2017 – Gear Technology and Automation Systems 3 New LK 300 /500 Gear Skiving Machine Skiving³: Machine – Tool – Process The principle of gear skiving was invented back over a century ago. Yet in practice the highly dynamic kinematics involved in this method frequently caused major problems. Up to now, the process was very unfavourable for the tools. The skiving tools are very complex and an incorrectly designed tool has a negative impact tool life and machining quality. Liebherr-Verzahntechnik GmbH has now mastered both the mechanics and the technology involved, meaning it is now in a position to create the ideal process for either conical or cylindrical tools. Liebherr-Verzahntechnik GmbH is opening a new chapter in the evolution of gear-skiving with the LK 500 Gear skiving can be classified somewhere between the more solve this problem. Furthermore, poor chip removal prevented familiar methods of gear hobbing and gear shaping. Com- gear skiving from being a success for a long time. pared to shaping, skiving enables similar gears to be pro- duced in equal or higher quality and in a third of the time. Principle of gear skiving Skiving is suitable for producing both internal and external The principle of gear skiving equates to a crossed axis helical gears. This method requires significantly less approach and gear drive with tool and workpiece axes in skewed configu- overruns than gear hobbing and can therefore be used for ration. During the cutting process the workpiece and tool are components where space is more restricted. But why did this rotated, whereby, due the axis intersection angle, a relative method, which was patented back in 1910, not become a velocity is created between the tool and workpiece. “This standard method straightway? “To be successful at gear skiving, you need to have an exact Skiving³: machine, tool and process from a understanding of the process – gear hobbing and shaping are single source significantly more forgiving of mistakes,” explains Dr. Hansjörg Geiser, Head of the Gear Cutting Development and Design Machine: Engineering team at Liebherr-Verzahntechnik GmbH. “During automation, deburring and tool changer rigidity the cutting process the rake angle can change to high nega- tive values, which can put extreme pressure on the cutting Tool: edges.” Therefore, gear skiving is creating high cutting forces design, machining, processing which can lead to considerable machine vibrations. In the past, rotational axes in particular represented a weakness in Process: the gear skiving process. Nowadays, modern drive systems technology configuration, implementation, optimisation 6 Liebherr Magazine 2016 / 2017 – Gear Technology and Automation Systems Gear Technology that can handle parts up to 500 millimetres diameter. The tool LK 300 / 500 can be pivoted, rotated and moved about every axis. “The • Maximum workpiece diameter: 300 / 500 mm first tool can be configured correctly right away; geometrical • Maximum table speed: 3000 / 1500 1 / min iterations are not required,” is how Oliver Winkel explains the • Maximum tool diameter: 250 mm machine’s complex motion. “Sound mathematical modelling • Maximum tool speed: 2700 1 / min that does not involve correction cycles is one of the special • Maximum spindle output: 32 kW features of our solution.” While the tools are engineered and designed in Ettlingen, they are produced by the Liebherr sub- relative motion is utilised as a cutting motion, with the main sidiary, Liebherr-Utensili S.r.l., in Collegno (Italy). cutting direction along the tooth flank,” (see image on page 9) Dr. Oliver Winkel, Head of the Gear Skiving Applications Engi- Liebherr’s experts regard the “complete delivery package” of neering and Technology Development team in Kempten, ex- the complete machine, tools and technology from a single plains. The magnitude of the cutting speed depends on one hand source as a major benefit. The first machine is due to be de- on the size of the axis intersection angle and on the other hand livered in 2016 – preparative customer trials were success- on the rotating speed of the cutting tool. “With an axial feed along ful. The first customers overall package includes the control the rotation axis of the workpiece the entire width of the gear is system and ring-loader-aided automation – Liebherr-Verzahn- machined. Helical gear teeth also require
Details
-
File Typepdf
-
Upload Time-
-
Content LanguagesEnglish
-
Upload UserAnonymous/Not logged-in
-
File Pages44 Page
-
File Size-