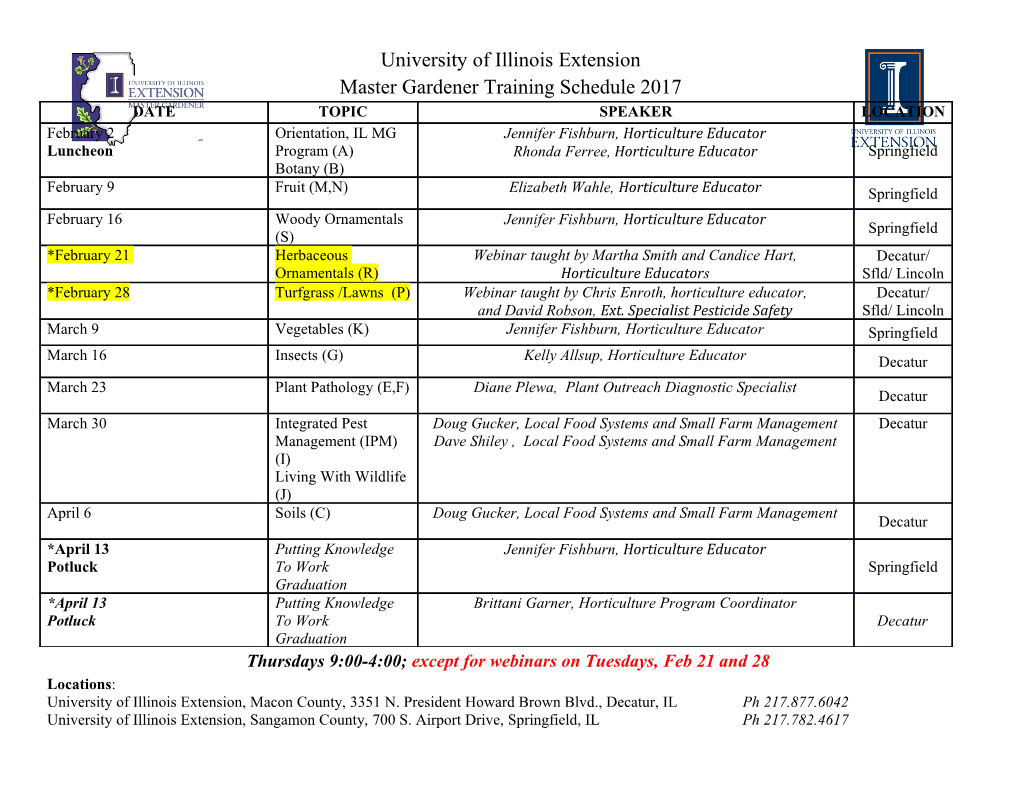
Carbonitriding—Fundamentals, Modeling and Process Optimization Report 13-02 Research Team: Liang He [email protected] Yuan Xu [email protected] Xiaolan Wang [email protected] Mei Yang [email protected] (508) 353-8889 Richard D. Sisson, Jr. [email protected] (508) 831-5335 Focus group: 1. Project Statement Objectives Develop a fundamental understanding of the process in terms of: • The diffusion of nitrogen in the steel depends on the nitrogen gradients as well as the carbon and other alloying element concentrations and gradients. The carbon content and gradients will have a significant influence on the nitrogen activity and therefore diffusivities. A fundamental understanding of the thermodynamics of solutions of carbon and nitrogen in alloyed austenite is necessary as well as the effects on diffusion of carbon and nitrogen. • The effect of nitrogen on the hardenability of carburized steels will be determined. Nitrogen stabilizes austenite and increases the hardenability by moving the TTT diagram to longer times. The effects of nitrogen content on these phenomena will be determined. • Determine the process control requirements for Carbonitriding in terms of temperature, atmosphere composition measurement and times based on the precision and accuracy required to control the process. Develop a computational model to determine the carbon and nitrogen concentration profiles in the steel in terms of temperature, atmosphere composition (ENDOGAS + NH3), steel surface 1 condition, and alloy composition. This tool will be designed to predict the carbon and nitrogen profiles based on the input of the process parameters of temperature (time), and atmosphere composition (time). Boost and diffuse cycles will be included. • CarbTool© will be modified to create CarboNitrideTool©, a software that will simulate the carbonitriding process, by adding the nitrogen absorption and diffusion in austenite with concomitant carbon uptake and diffusion. The fundamentals of these phenomena as described above will be used for the model generation. The model will include multiple cycles. • Verify the model by comparison with experimental results. The verification will initially be conducted by comparison with results in the literature and results from CHTE member companies. Selected experiments will also be conducted to test the model’s accuracy and capabilities. • Develop a model-based optimization process to determine the optimum process parameters for several process goals: minimum cycle time, minimum cost, maximum productivity, and minimum gas consumption. Strategy The objectives will be achieved by completing the following tasks. • Task 1. Literature review o Carbonitriding practices in industry o NH3 – endogas thermodynamics o Diffusivities of carbon and nitrogen in steel o N adsorption, decomposition and absorption o Hardenability of steels as a function of nitrogen and carbon contents o Control of carbonitriding systems • Task 2. Determine the boundary conditions and diffusivities of nitrogen and carbon for simulation tool development o Flux o Mass transfer coefficient o Diffusivities of nitrogen and carbon in steel 2 • Task 3. Modify Carbtool© for carbon and nitrogen absorption and diffusion to create CarboNitrideTool© • Task 4.Verify computer model o Literature data o Selected experiments • Task 5.Develop optimization methods for Carbonitriding o Minimum cycle time o Minimum cost • Task 6. Test optimization methods Deliverables • Literature review • CarboNitrideTool© • Optimization method 2. Executive Summary The increased understanding of the carbonitriding process when combined with the new process model (i.e. CarboNitrideTool©) will provide the heat treater with new opportunities to determine the process parameters and control strategy to minimize cycle times and cost while enhancing the quality of the products. The recommendations for measurement techniques of atmosphere content and steel surface condition will provide the opportunity for improved quality and productivity of the carbonitriding process. 3 3. Achievements in this semester o Performed the microhardness profile measurement of all samples; o Improved CarboNitrideTool©; o Finished the final project report. 3.1 Carbonitriding experiments 3.1.1 Experimental Plans and Procedures The AISI 8620 and AISI 1018 steels were used in the experiments. Both steels are commonly used for carburizing and carbonitriding case-hardened processes. Table 1 shows the chemical compositions of these two steels. Table 1: Compositions of AISI 8620 and AISI 1018 (in wt %) C Mn P S Si Ni Cr Mo 8620 0.18-0.23 0.7-0.9 0.035(max) 0.04(max) 0.15-0.3 0.4-0.7 0.4-0.6 0.15-0.25 1018 0.15-0.20 0.60-0.90 0.04 (max) 0.05(max) ---- ---- ---- ---- The samples were made from cylindrical steel bar by cutting it into disks with a diameter of 1.25 inches and thickness of 0.4 inch. The surface of samples were grinded with sand paper before carbonitriding, to remove rust on the surface, and after grinding the samples were washed by acetone to remove any organic compounds. Both AISI 8620 and AISI 1018 samples were placed in the furnace with an endothermic enriched atmosphere and carbonitriding atmosphere at 850℃ or 800℃ for 2 hours. The carbon potential of endothermic gas was maintained at 0.9% for the entire process. During the last 15 or 45 minutes, ammonia was introduced into the furnace. The processes are shown in Figure 1 According to the experimental plan, 14 groups of samples for each steel, i.e., totally 28 groups of samples have been prepared, and every group has 5 samples (Table 2). 4 Figure 1 Experimental Process Table 2: Experiments design for eaCh steel 3.1.2 Experimental results Carbon concentration and nitrogen concentration were analyzed with SPECTRO MAXX and microhardness was measured with SHIMADZU HMV-2000 and BUEHLER 1600-6300. Surface 5 retained austenite was analyzed with Panalytical PIXcel3D X-ray diffraction instrument. Also, the weight gain during carbonitriding process was measured with the scale, Mettler H54AR, with an accuracy of 0.1mg. Samples were weighed before and after carbonitriding. 3.1.2.1 Optical Emission Spectroscopy (OES) results The OES was used to measure the concentration of carbon and nitrogen. The depth of each OES burn is approximately 40 µm. The depth of carbon diffusion is approximately 500 µm and the depth of nitrogen diffusion depends on the intensity and time of ammonia addition. The measurement results are listed in Appendix A. From the measurement results, it can be concluded that 1) more nitrogen will be introduced into the steel surface with more and longer ammonia addition into the furnace atmosphere; 2) more carbon will be transferred into the steel surface with more nitrogen in the steel surface; 3) higher temperature helps the absorption of carbon and nitrogen into the steel surface. 3.1.2.2 Microhardness measurement results All the measurement results for the microhardness are shown in Appendix B. Figure 2 presents some microhardness measurement results. It can be seen that more and longer ammonia addition increases sample hardness. 1 1000 900 Carbon - 0% NH3 0.8 800 Nitrogen - 0% NH3 700 carbon - 5% NH3 15min 0.6 600 Nitrogen - 5% NH3 15min 500 Carbon - 15% NH3 45min 0.4 400 Nitrogen - 15% NH3 45min ViCkers hardness 300 Hardness - 0% NH3 0.2 200 Hardness - 5% NH3 15min Weight percent of carbon or nitrogen 100 Hardness - 15% NH3 45min 0 0 0 100 200 300 400 500 600 Figure 2 MiCrohardness (HV) and C&N ConCentrations (wt%) vs depth from sample surfaCe (µm) (Material: AISI 1018 Temperature: 850°C) 6 From Figure 2, the microhardness of first test point is always smaller than the measurement result of the second test point. The possible reasons are: 1) during the microstructure hardness test, the edge part always takes larger deformation with the load pressure because of edge effect; and 2) in steel, nitrogen and carbon are always considered as the austenite stabilizers, and there are more carbon and nitrogen at the sample surface, which help to produce more retained austenite and decrease the surface microhardness. 3.1.2.3 Discussion on retained austenite at the sample surface The heat treatment of steels by quenching and tempering to produce a martensitic structure involves three basic steps which include: 1) Austenitizing – The process in which the steel is heated into the red-heat temperature range where it will become a single-phase mixture of face- centered cubic iron with the carbon dissolved into solution. This phase of steel is known as austenite and important parameters during this stage include heating rate, final holding temperature and time at temperature. 2) Quenching – The stage in which the austenite is quickly cooled to room temperature or below. This stage is designed to convert the austenite to a new single-phase of carbon in iron known as martensite. The crystal structure of martensite is body centered tetragonal and its formation is diffusion controlled phases such as bainite, and important parameters include cooling rate and final quench temperature. 3) Tempering – The process of heating the martensitic steel to temperatures below its critical temperature for the purposes of decomposing the martensitic structure. Changes that take place during this step include stress relief of the microstructure, decomposition of the martensite to tempered martensite and transformation of retained austenite to other products. While austenite is the stable phase of steel at high temperature, it is an unstable phase at room temperature where it is termed to as retained austenite. Retained austenite is most often produced during the heat treatment of plain carbon steels with carbon contents greater than 0.4% or in alloy steels with significant alloy contents. Typically most of the austenite transforms to martensite upon quenching. In practice, however, this does not always happen with some steels, as the steel must be quenched to below a certain characteristic temperature known as the martensite finish temperature, Mf, in order to complete the austenite to martensite transformation. The martensite finish temperatures in many steels such as high carbon and/or alloy steels is often low enough to retain some of this austenite at room temperature.
Details
-
File Typepdf
-
Upload Time-
-
Content LanguagesEnglish
-
Upload UserAnonymous/Not logged-in
-
File Pages47 Page
-
File Size-