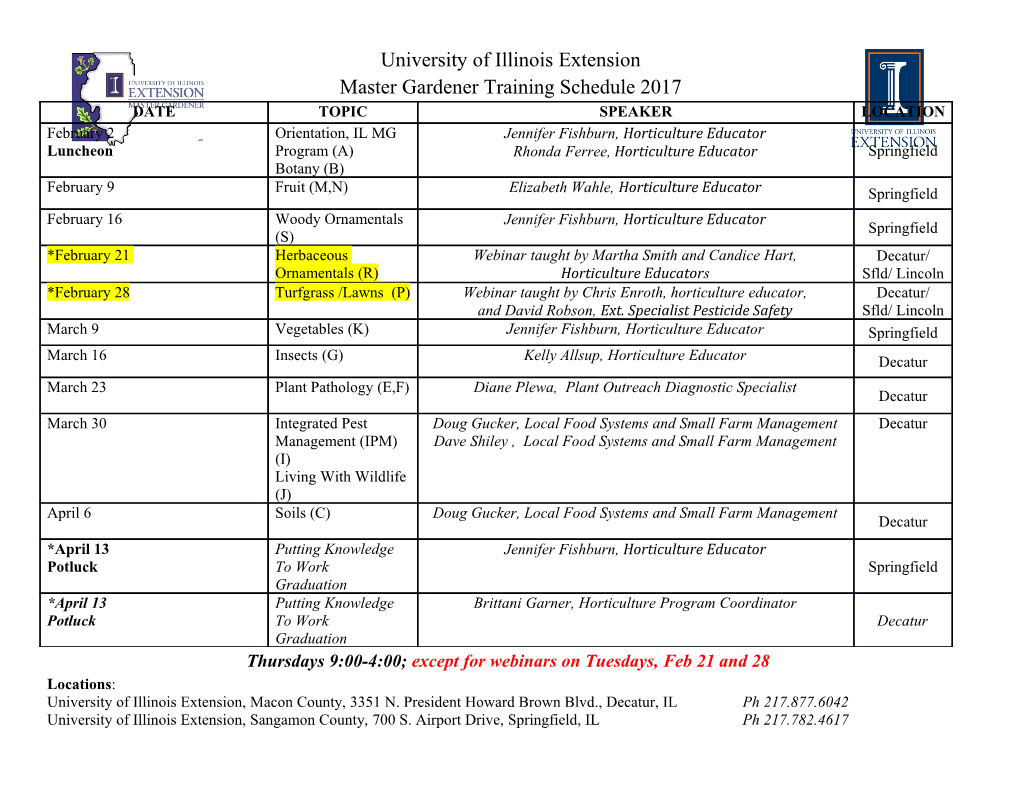
Benign Processing of High Performance Polymeric Foams of Poly(arylene ether sulfone) Desmond J. VanHouten Dissertation submitted to the faculty of the Virginia Polytechnic Institute and State University in partial fulfillment of the requirements for the degree of DOCTOR OF PHILOSOPHY In Macromolecular Science and Engineering Donald G. Baird, Chair James E. McGrath Scott W. Case Richey M. Davis December 2, 2008 Blacksburg, Virginia Keywords: supercritical carbon dioxide, foaming, plasticizer, high performance polymer, poly(arylene ether sulfone) Benign Processing of High Performance Polymeric Foams of Poly(arylene ether sulfone) Desmond J. VanHouten ABSTRACT This work is concerned with the production of high performance polymer foams via a benign foaming process. The first goal of this project was to develop a process and the conditions necessary to produce a low density (>80% density reduction) foam from poly(arylene ether sulfone) (PAES). Water and supercritical carbon dioxide (scCO2) were used as the blowing agents in a one-step batch foaming process. Both water and scCO2 plasticize the PAES, allowing for precise control on both the foam morphology and the foam density. To optimize the foaming conditions, both thermogravimetric analysis and differential scanning calorimetery (DSC) were used to determine the solubility and the reduced glass transition temperature (Tg) due to plasticization of the polymer. It was determined that 2 hours was sufficient time to saturate the PAES with o water and scCO2 when subjected to a temperature of 220 C and 10.3 MPa of pressure. Under these conditions, a combination of 7.5% of water and scCO2 were able to diffuse o into the PAES specimen, correlating to ~60 C reduction in the Tg of the PAES. The combination of water and scCO2 produced foam with up to an 80% reduction in density. The compressive properties, tensile modulus, and impact strength of the foam were measured. The relative compressive properties were slightly lower than the commercially available structural foam made of poly(methacrylimide). The second objective of the dissertation was to enhance the compressive properties of the PAES foam, without concern for the foam density. Foam was produced over a range of density, by controlling the cell size, in order to optimize the compressive properties. Carbon nanofibers (CNFs) were also added to the PAES matrix prior to foaming to both induce heterogeneous nucleation, which leads to smaller cell size, and to reinforce the cell walls. Dynamic mechanical thermal analysis (DMTA), on saturated CNF-PAES, was used to determine the reduced Tg due to plasticization and establish the temperature for pressure release during foaming. DMTA proved to be more effective than DSC in establishing quantitative results on the reduction in the Tg. The CNF-PAES foam produced had compressive properties up to 1.5 times the compressive properties of the PAES foam. iii Acknowledgements I would like to thank my advisor, Dr. Donald G. Baird, for his thoughts and guidance on my project. The insightful conversations helped to spark new ideas and directions on my research. In addition I would like to thank my committee members, present and past, for their time and suggestions: Dr. Davis, Dr. Case, Dr. McGrath, and Dr. Riffle. In addition my committee, I would like to thank the following people: ¾ The staff in both Chemical Engineering and the Macromolecular Science and Engineering program: Diane, Laurie, Millie, Angie, Mike, and Riley. ¾ Steve McCartney and Rick Caudill for time from their schedule to help me test my material. ¾ My best friend, my loving and caring wife, and my editor, Rachael. Throughout the process she has shown me tremendous support and encouragement. She was always there to keep my spirits high during the stressful times of graduate school, which helped me to persevere. I enjoyed being able to spend every lunch time with her over the past 4 ½ years and I look forward to the future that this opportunity will provide for us. ¾ My family: A special thank you goes to my grandparents, James and Theresa VanHouten, for raising me and always pushing me to work hard. Thank you also goes to Destiny and Joel Narloch, Dawn VanHouten, Doug Schrupp, Betty Zellner, Alex Zellner, Katie and Michael Abramczyk, and Kent and Stacy VanEgtern for their support. iv ¾ The men and woman of the Polymer Processing Lab whom I have had the pleasure of working with: Aaron, Chris S., David, Gregorio, Myoungbae, Chris M., Kevin, Chen, Mike, and Neeraj. ¾ My church family at Main Street Baptist Church for their support. ¾ Ultimately, I would like to thank God. Without His love and guidance in my life, nothing would be possible. My personal relationship with Him has gotten me through stress and dead-ends of my research. v Original Contributions The following are considered to be original contributions of this research: 1. Development of a benign process, which utilized a dual plasticizer blowing agent system, to produce low density (>80% density reduction) foams from poly(arylene ether sulfone). A combination of water and supercritical carbon dioxide were used as the blowing agents. 2. The incorporation of carbon nanofibers into the poly(arylene ether sulfone) foam to greatly enhance the compressive properties of the foam via heterogeneous nucleation and reinforcement of the cell walls. 3. The use of dynamic mechanical thermal analysis on plasticized poly(arylene ether sulfone) to quantitatively determine the reduced Tg and to use the data to control the cell size by decreasing the temperature at which the foam is produced. 4. Incorporating the Williams-Landel- Ferry based equation into cell growth modeling to account for the increase of viscosity during the foaming of a polymer with blowing agents that plasticize the polymer. vi Format of Dissertation This dissertation is written in manuscript format. Chapters 3.0 through 5.0 are manuscripts which stand alone and describe the experiments, results, and conclusions for the work. With the exception of the literature review, chapter 2.0, the tables and figures are located after the references of each manuscript. vii Table of Contents Table of Tables ................................................................................................................xiii Table of Figures ...............................................................................................................xiii 1 Introduction................................................................................................................. 1 1.1 References........................................................................................................... 4 2 Literature Review........................................................................................................ 6 2.1 Role of Carbon Dioxide in Polymer Processing................................................. 6 2.1.1 Supercritical Carbon Dioxide Properties .................................................... 6 2.1.2 Solubility in Polymers ................................................................................ 7 2.1.3 Diffusivity in Polymers............................................................................. 10 2.1.4 Plasticization of Polymers......................................................................... 11 2.2 Structural Polymers and Composites................................................................ 12 2.2.1 Structural Sandwich.................................................................................. 13 2.2.1.1 Polymer Core Materials ........................................................................ 13 2.2.1.1.1 Polyetherimide foam....................................................................... 14 2.2.1.1.2 Poly(methacrylimide) Rigid Foam ................................................. 16 2.2.1.1.3 Polyimide foam............................................................................... 17 2.2.1.2 Honeycomb Core .................................................................................. 18 2.2.1.3 Syntactic Foam Core............................................................................. 20 2.3 Benefits of Microcellular Foams ...................................................................... 22 2.4 Processing of Microcellular Foams .................................................................. 24 2.4.1 Batch Processing....................................................................................... 25 2.4.1.1 Two-Step Batch Processing .................................................................. 25 viii 2.4.1.2 One-step Batch Process......................................................................... 27 2.4.2 Continuous and Semi-Continuous Processes............................................ 28 2.4.2.1 Continuous Extrusion Process .............................................................. 28 2.4.2.2 Continuous Injection Molding Process................................................. 31 2.4.2.3 Semi-continuous Extrusion Process...................................................... 34 2.5 Parameters Affecting Microcellular Foaming .................................................. 35 2.5.1 Control of Processing Parameters for Desired Foam Properties .............. 36 2.5.1.1 Batch Processing................................................................................... 36 2.5.1.1.1 Cell Density .................................................................................... 36 2.5.1.1.2 Cell Size.........................................................................................
Details
-
File Typepdf
-
Upload Time-
-
Content LanguagesEnglish
-
Upload UserAnonymous/Not logged-in
-
File Pages188 Page
-
File Size-