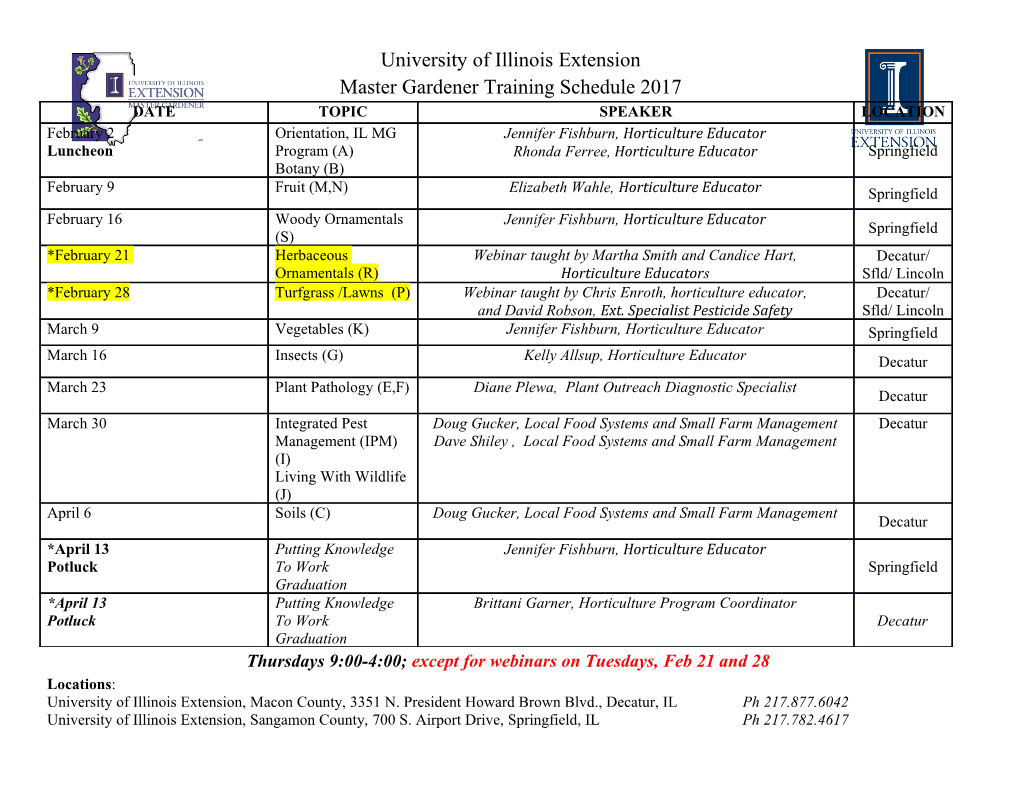
Design Procedure of a Turbopump Test Bench Julian Pauw, Lucrezia Veggi, Bernd Wagner, Joydip Mondal, Maximilian Klotz, Oskar Haidn To cite this version: Julian Pauw, Lucrezia Veggi, Bernd Wagner, Joydip Mondal, Maximilian Klotz, et al.. Design Pro- cedure of a Turbopump Test Bench. 17th International Symposium on Transport Phenomena and Dynamics of Rotating Machinery (ISROMAC2017), Dec 2017, Maui, United States. hal-02419962 HAL Id: hal-02419962 https://hal.archives-ouvertes.fr/hal-02419962 Submitted on 19 Dec 2019 HAL is a multi-disciplinary open access L’archive ouverte pluridisciplinaire HAL, est archive for the deposit and dissemination of sci- destinée au dépôt et à la diffusion de documents entific research documents, whether they are pub- scientifiques de niveau recherche, publiés ou non, lished or not. The documents may come from émanant des établissements d’enseignement et de teaching and research institutions in France or recherche français ou étrangers, des laboratoires abroad, or from public or private research centers. publics ou privés. Distributed under a Creative Commons Attribution| 4.0 International License Design Procedure of a Turbopump Test Bench Julian D. Pauw1*, Lucrezia Veggi1, Bernd Wagner2, Joydip Mondal1,3, Maximilian Klotz1, Oskar J. Haidn1 Abstract TATIN RO G N M e high complexity of turbopumps for liquid rocket engines and their demanding requirements O A A C I H S necessitate that their design process is accompanied by extensive experimental investigations and I O N P E R validation tests. is paper presents the design procedure for a rocket turbopump test bench, where M Y Y S water is used as a surrogate for the cryogenic fluids usually used in rocket engines. Scaling methods, that allow for a comparison of tests under varying conditions, are reviewed from literature and applied to derive the necessary dimensions of the test bench. e resulting test bench design is ISROMAC 2017 shown in detail and its capabilities to support the turbopump design process are assessed. Further, the operational envelope of the derived test bench design is evaluated with respect to later tests of International Symposium on different pumps. Transport Phenomena Keywords and turbopump — liquid oxygen scaling — test bench design Dynamics of Rotating Machinery 1Technical University of Munich, Department of Mechnical Engineering, Chair of Turbomachinery and Flight Propulsion, Divison Space Propulsion, Munich, Germany Maui, Hawaii 2Institute of Space Propulsion Lampoldshausen, German Aerospace Center (DLR), Hardthausen, Germany 3Cryogenic Engineering Centre, Indian Institute of Technology Kharagpur, India December 16-21, 2017 *Corresponding author: [email protected] 1. INTRODUCTION are stored in liquid state under boiling conditions on-board the launcher and thus ground tests with cryogenic fluids are e turbopumps of a liquid rocket engine (LRE) supply the of very complex nature. Besides the difficult generation and combustion devices with fuel and oxidizer at high mass flow storage of the cryogenic fluids, the demands on the turbo- rates and at a high pressure level. Typically, fuel and oxidizer pump under development are very high as the design needs are pumped by separate pumps. e turbopumps increase to withstand high temperature loads and it needs to take the pressure from a low pressure level in the tank to a high into consideration material choices for cryogenic tempera- pressure level needed for the combustion process. Conse- tures for every tests. Consequently, tests with fluids that are quently, the turbopumps are a substantial part of the rocket liquid at ambient temperature are highly desirable. Further, engine. e dimension and the performance of the turbo- it would be beneficial to perform tests at lower rotational pumps depend highly on the desired engine operation point, speeds without loosing information on the flow behaviour in- the engine cycle and the requirements of the combustion side the pump. Test benches operated with water at ambient chamber. temperature have been established as a very good solution e work performed at the Division Space Propulsion of the to this problem. A drawback of tests at ambient temperature Technical University of Munich (TUM) is embedded into the with water is that the cavitational behaviour of turbopumps research project KonRAT, i.e. rocket propulsion engine com- cannot be captured. Especially, the so called thermodynamic ponents for applications in aerospace transportation systems. suppression head (TSH), an effect that can be observed at e project aims at establishing competences in the devel- tests with cryogenic fluids, is not present at ambient temper- opment of turbopumps. [1, 2, 3, 4, 5]. Key objective at the ature tests with water. A solution is provided by the findings Division Space Propulsion, TUM, is the investigation of the of several research groups which show that similarity of the design process of turbopumps and the investigation of fluid cavitational performance can be reached by heating the water phenomena. Both parts are carried out numerically as well up [6, 7, 8, 9, 10, 11]. as experimentally. e Division Space Propulsion, TUM, has established a design In literature, many different scaling and similarity methods process for rocket engine turbo pumps based on well-known are present. is paper will present a set of those methods literature and commercially available soware tools [1]. In based on a literature survey and makes use of the methods order to fully understand all design parameters and to ensure in order to define the operating conditions of a test bench for that those parameters desired can be reached, experimental a liquid oxygen turbo pump developed at TUM. e derived validation of those design parameters is an indispensable test bench will be shown in detail and its properties will be step in the design loop of every rocket engine turbopump. evaluated for later usage. is is mostly done by making use e fuel and the oxidizer of cryogenic liquid rocket engines of a numerical test bench representation in the commercially Design Procedure of a Turbopump Test Bench — 2/11 available soware tool EcosimPro®. In order to be able to use to model flows with free surfaces where gravitational forces the test bench for other configurations as well, an outlook on have a large impact. the generalized operational envelope of the test bench will complete this paper, so that the possible use for future test inertia force v2 campaigns with different configurations can be estimated. Fr = = (4) gravitational force gLc 2. SCALING METHODS e Reynolds number relates between the acting inertia In order to test a pump in a test facility at conditions that forces and the viscous forces. Equivalent Reynolds num- differ from the normal operating conditions, the similarity of bers predict a similar development of boundary layers inside the flow passing through the pumps needs to be established two compared pumps. e generation of boundary layers both at the test bench and at the operational conditions. Ac- is closely linked to the surface roughness of the parts that cording to [12, 13, 14], this similarity can be reached if four conduct the flow. Especially for geometrically scaled models different parameters are comparable: (1) the geometry un- it is difficult to generate a comparable surface roughness of der investigation, (2) a comparable establishment of velocity all pump components. For the purpose of comparing differ- triangles at pump inlet and outlet, (3) a similar dynamic be- ent radial machines, the Reynolds number is oen defined as haviour of the pump and (4) comparable thermodynamic the product of peripheral velocity U3 at the impeller outlet properties of the fluids. and the corresponding tip radius R3 divided by the kinematic viscosity υ. When comparing the scaled measurements in Following Sigloch [13, 14], geometric comparability of two detail, it is strongly recommended to calculate the Reynolds turbo machines is fulfilled if the dimensions of the parts number locally to guarantee comparable boundary layers all conducting the flow follow a certain ratio in all spatial di- over the pump [14, 13, 15, 16]. mensions. is offers not only comparable interaction of the fluid with the static and dynamic parts of the machine, 2 inertia force U R , ωR , but also yields similar velocity triangles at every correspond- Re = = 3 t 3 = t 3 (5) viscous force υ υ ing point for friction-free conditions because the velocity vectors are then governed by passage dimensions and the e Euler number describes the ratio between pressure forces rotational speed only. It is important to make sure that not and inertia forces. For the scaling of pumps, it is inevitable only the rotor and blade geometries are comparable, but also to keep the Euler number the same for model and prototype. the gap geometries and clearance distances between rotor and housing. pressure force ∆p Eu = = (6) inertia force ρv2 = dimension of prototype = Xm λgeometry (1) Further, the thermal properties of the fluids, i.e. the spe- dimension of model Xa cific heat, the enthalpy and the thermal diffusivity, largely influence the flow characteristics. is is especially true for velocities of prototype vm machines that exhibit a large pressure difference. It is advis- λvelocity = = (2) velocities of model va able to make use of fluids with comparable properties and to closely track property changes. In the case of single-phase flows, i.e. in the case of non- cavitating flows, the forces acting on the pump are the fol- e above scaling methods need to be incorporated in order lowing: inertia forces, pressure forces, viscous forces and the to design a test bench that can be used to test a LOX turbop- gravitational force. Additionally, forces resulting from the ump with water. For ground tests of liquid rocket engine elasticity of the mechanical system, especially the sha, can turbopumps, the gravitational effects are negligible. e dif- act on the pump components.
Details
-
File Typepdf
-
Upload Time-
-
Content LanguagesEnglish
-
Upload UserAnonymous/Not logged-in
-
File Pages12 Page
-
File Size-