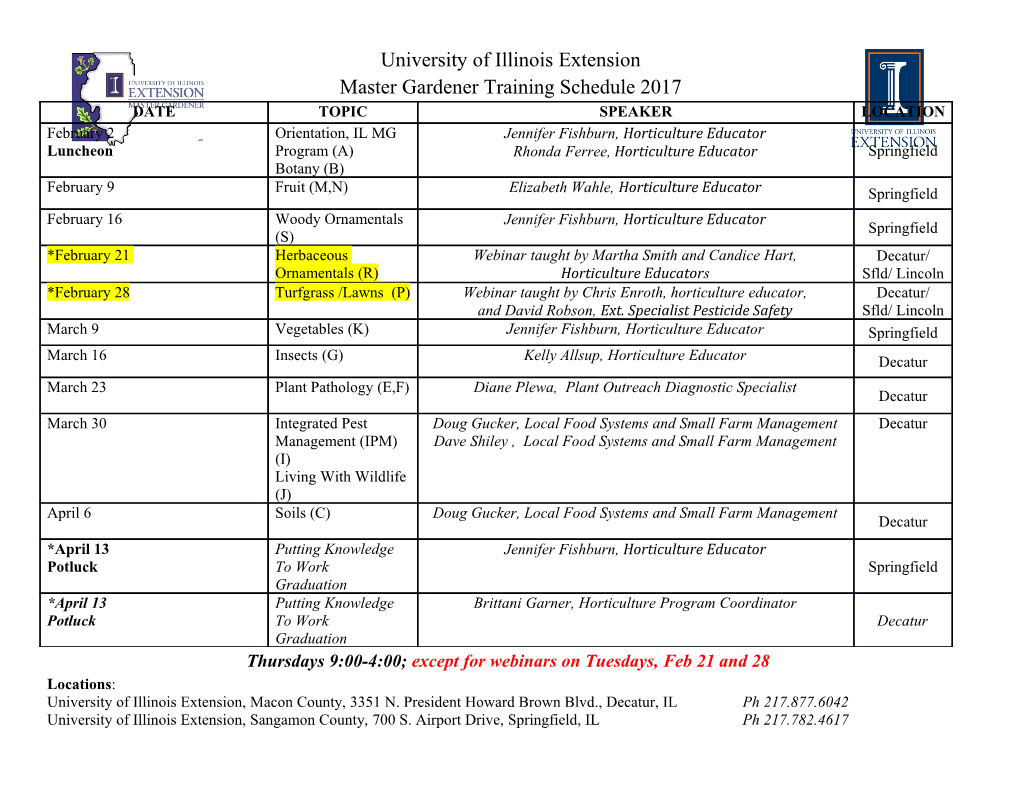
DECORATIVE CHROMIUM PLATING I=o44-5 by Donald L. Snyder 2$& f Engelhard Corp., Beachwood, OH 13lcctrotlcposition of chromium is thc principii1 tncitns of iiiip:trting thc physicill itntl clicniical propcrtics ol’chromium 10 thc surface of lcss cxpcnsive antl casier to lbrm matcriiils such as steel and plastics. The most desirable properties of chromium as a metal coating are its inherent protective and decorative characteristics. The deposit’s high reflectively is retained in service because of chromium’s excellent tarnish, corrosion, wear and scratch resistance. Chromium is almost exclusively plated over a nickel electrodeposit which can easily be plated over substrates such as plastics, steel, aluminum, copper alloys, and zinc die castings. Nickel is preferred because it protects the substrate from corrosion, helps give chromium a white color, and is protected from surface oxidation by the chromium. Stainless steel is the only substrate that is frequently plated directly with chromium, but a nickel preplate before chromium is also used. Multiple or single layers of nickel and copper can precede the nickel/chromium deposits depending upon the intended use of the part. Decorative chromium deposits typically are plated in the 2 to 20 millionths of an inch range. Thicker deposits tend to be duller and contain visible cracks. The traditional chromium deposit is produced from an electroplating electrolyte contain- ing hexavalent chromium ions and has a pleasing bluish-white decorative appearance. About 1975, a chromium electrolyte containing the less toxic and less hazardous trivalent chromium ion began replacing many decorative hexavalent chromium electroplating installations. De- pending upon the process, trivalent chromium electrolytes can either produce a metallic white deposit almost identical in appearance to the bluish-white hexavalent chromium deposits or a deep looking pewter or stainless steel appearing deposit. In almost all chromium plating applications, both hexavalent and trivalent chromium processes are interchangeable with each other; however, one or the other process might offer unique advantages. CHEMISTRY FOR HEXAVALENT CHROMIUM Hexavalent chromium clcctrolytcs rcquirc a source of chromium and one or more catalysts in order to plate. The formulation of the traditional process, called the conventional bath, contains hexavalent chromium and sulfate as the only catalyst. Proprietary additives can be added to thc convcntional hcxavalent chromium plating bath formulation to enhance particular plating operations or the deposit’s properties. In most cases, these proprietary processes are called mixed-catalyst baths since the additives contain at least one additional catalyst in addition to sulfate. Mixed-catalyst baths are used when their special properties are required but they are more expensive to operate than convcntional processcs. They typically plate at faster spceds, have better coverage, have wider bright ranges, and are more tolerant to impurities. They also are less sensitive to current interruptions and can be plated over more passive surfaces. The basic formulation of both types of hexavalent chromium processes are very similar. They consist of chromic trioxide (CQ) which when combined with water forms chromic acid (H,CIO,), and the sulfate ion (SO,) added in the form of sulfuric acid or a sulfate salt. Even though chemically incorrect, in most literature solid chromatic trioxide is commonly referred to as its hydrated form, chromic acid. A number of theories have been proposed to explain the mechanism of hexavalent chromium electroplating. Basically, they all resemble the following multiple reactions. Cr03 + H20 -+ H2Cr0, + Cr0,-2 + 2H+ (1) ZH2Crij, -+ H2Cr20, + H20 -+ Cr207-’ + ZH’ + H20 (ij 183 -- P Deposition Iicilction: CAT Cr20,-2 + 14H” + 12(e) -2cr0+ 7H20 (3) This reaction has an efficiency of about 20% or less. CAT is a required catalyst, e.g. sulfate, while (e) refers to an electron. Side Reactions: 2H+ -1- 2(e) + H, + mist (4) This reaction consumes 80% or more of the available power. Cr20,-’ + 14H+ + 6(e) + 2w3+ 7H20 (5) PbOz SOLUTIONS TO YOUR 2Cr+3. + 302 - 6(e) -2Cr0, (6) METAL FINISHING PROBLEMS ( --I This reaction takes place at ’the lead anode, Pb02. ’s 1200 :hemicals comes with Dilute conventional formulations consist of about 250 g/L (33 odgal) chromic trioxide, takes to solve your most critical “chromic acid”, with about 2.5 glL (0.33 odgal) sulfate. Concentrated conventional baths :My and economically. contain about 400 g/L (53 odgal) chromic trioxide and 4.0 g/L (0.53 odgal) sulfate. In POST practice, however, concentrations in between these are used. FINISHING The dilute formulation is extensively used to give good coverage, moderate nickel Metal strippers I substrate activation, and consistent current efficiency. It also has a lower cost to originally Paint strippers m make up, plates faster, and produces less waste to treat. The conccntratcd formulation gives Protective treatments m better coverage and greater resistance to impurities and requires lower operating voltages; however, it is more expensive to operate because of its higher chromium concentration and the resulting additional chromium to be waste treated. MASS FINISHING A critical point in all bath formulations is the requirement for close control of the Chemically dccelerared CrO3/S0, weight ratio in order to produce consistent plating results. Ratios of between 80:l fmishmg systems and 130: 1 are typical with a ratio around 100: 1 being most common for conventional processes. Abrasive compounds H Non-abrasive H A low ratio results in relatively poor throwing and covering power and an increased limiting debumng compounds current density. Higher ratios result in slow deposition rates, produce dull deposits, have Burrushing compounds B increased covering power, and decrea.sed limiting current density. Descaling compounds m The addition of a fluoride catalyst necessitates an adjustment in the Cr03/S0, weight ratio. Ratios of 170:l to 210:l are required with 190:l being most typical. The chromium concentration, for both the dilute and concentrated mixed-catalyst formulations are the same ALUMINUM EQUIPMENT as for conventional baths, however, the sulfate concentration is lowered. FINISHING Unlike most plating baths in which the metal, M, is present in solution as a cation, RectifiersTanks mW BasketsBarrels H M” ,the chromium metal is present as an anion complex, Cr207=,which very likely undergoes H Non-etch cleaners m Etchanrs Tank liners H Dryers H further complexing with ions such as the sulfate catalyst to permit chromium deposition. H Desmutteddeoxiduers Heating coils I Filters a Fluoride or silicofluoride ions are extensively used today in mixed-catalyst formulations, H Bondal modified Electric heaters Pumps m especially in proprietary self-regulati,ng baths. The solubility constants of sparingly soluble alloy zincate Mass finishing media H Racks m salts of the catalysts are utilized to control the catalysts’ ratio in self-regulating baths because Ventilation systems m only enough catalyst will dissolve. For this reason, less frequent catalyst analysis is required. Vibratory equipment Much more routine analyses and chemical control of the catalysts are needed in nonself-reg- .dated formulations since they must be added to the bath as they are depleted. Chromic acid concentrations may be maintained by making frequent specific gravity A comprehensive line of chemicals determinations using a hydrometer. Occasionally, more accurate chromium analyses should and equipment, md the expertise to keep it all running sinoorhly that’? Gumm be conducted by an analytical method specific for chromium. Chromium is consumcd and ‘2711 toddy hrIltLnwrc .ind ilic ii.im of your nearby rcprescnidtive dragged out of the bath. It is replenished by additions of chromic acid. 1-800-223-GUMM IN NJ 1-201-991-4171 Sulfate concentrations should be: determined frequently by measuring the volume of the sulfate precipitated with barium. Occasionally, gravimetric analyses should be conducted to confirm the quick, less accurate, centrifuge method. Sulfate concentrations may be raised 184 I by adding sulfuric acid. To add 0.05 g/L H2S04, add 0.0272 ml/L concenvated H2S04. Sulfate is both dragged into and out of the tank. To lower the concentration of sulfate by Table I. Chromium Plating Typical Operating Conditions 0.05 g/L of H,SO,, add 0.01 g/L barium carbonate. Sulfate is an impurity in other chemicals such as chromic acid. For this reason, sulfate should be controlled carefully and any sulfate Trivalent Hexavalent present as impurities should be accounted for. Chromium Chromium 4 CHEMISTRY-TRIVALENT CHROMIUM Chromium, g/L 5 to 25 100 to 200 PH 2.3-4.0 The literature contains far less information on the chemistry of trivalent chromium Less than I Tcmpcra1ure, “F 70- I20 90- 120 processes than for hexavalent. This is the result of the relative newness of the commercially Cathode current density, successful processes, the proprietorships of the processes, and the wider differences in the Alft2 40- 1 50 175-300 chemistries used. Basically, the significant reactions in the trivalent chromium processes are Agitation Mild air very simple. Optional Rectifier voltage 4-15 4-12 Anode-cathode ratio 2: 1 1:l-3: 1 Deposition Reaction: Anode material Single-cell Carbon Cr+’ + 3(c) -f CP (7) Lead-7% tin Doublc-ccll Lcad-7% tin Chromium concentration, g/L Side Reaction: Single-cell 4-20 150-300 Double-cell ~r+~-+ Cr+6 3(e) (8) 5-10 + Maximum thickness, mil This takes place at the anode under some conditions. Single-cell The electrolytes for trivalent chromium plating solutions differ in chemistry, but they Room temperature about 0.05 5 or more all contain a source of trivalent chromium which is typically added as the sulfate or chloride High temperature 1 or more salt. They also contain a stabilizing material that combines with the chromium to permit it Double-cell about 0.01 to plate in the desired form. Salts are also added to increase conductivity in the solution. Plating rate, mil per min Wetting agents are used to help in the deposition reaction and to reduce the surface tension Single-cell (constant) of the solution.
Details
-
File Typepdf
-
Upload Time-
-
Content LanguagesEnglish
-
Upload UserAnonymous/Not logged-in
-
File Pages5 Page
-
File Size-