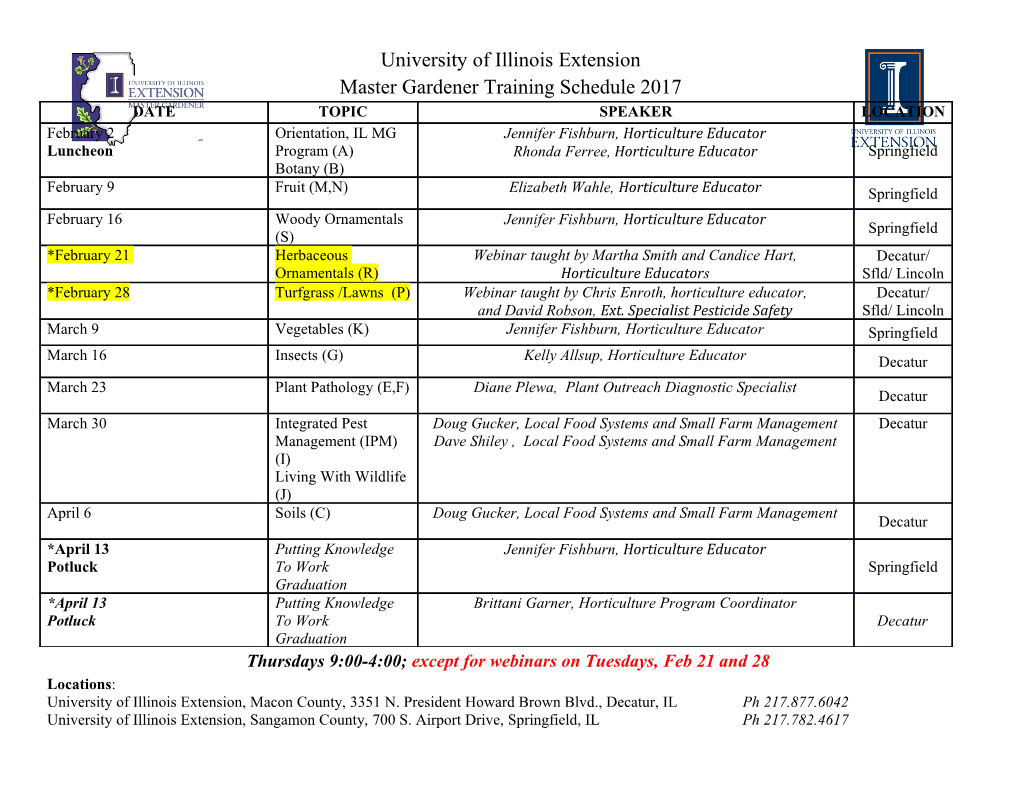
Panel Discussion: Lean Construction: Prefabrication & Modular Construction Wednesday, November 9, 2016 - PANEL DISCUSSION TRANSCRIPT - Douglas Cooper: Pretty impressive stuff. What makes something like that possible? We hear things about efficiency in construction. We hear things about collaboration. We hear about prefabrication. We hear about modular. We hear about all of these things. Modular has been with us a while, but we're beginning to see this resurgence in modular and prefabricated construction, simply because now we have these wonderful tools and these technologies that bring that to fruition for us, like BIM that allows us to collaborate on a completely different dimension, and lean construction practices and that efficiency. We also have, we're driven by these green building things and sustainability and this desire to be more sustainable. My name is Doug Cooper. I'm the regional, lean major for Turner Construction here in the New York business unit. Tonight we're going to delve into this whole concept of prefabrication and a modular construction. We have a panel here that's going to share with us their thoughts. We're not only going to talk about the prefabrication from as a concept and a means and method. We're also going to talk about some of the behaviors that we see as professionals when we get into a prefabrication or a modular construction type scenario so we can try to understand that a little bit. With that I'll allow the panel to introduce themselves. They'll give you about 3 minutes of background and then we'll get started with the questioning. Okay. Bob. Bob Sanna: Thank you, Doug and thank you Charlie for having me here tonight. My name's Bob Sanna. I'm with Forest City Ratner Companies. I'm the Executive Vice President for design development and construction. We've been thinking about efficiencies and innovation in building systems for a while. We've most recently had a full modular building that we've completed with Turner now. We could talk a little bit more about that in a while. It really starts with looking at systems from the beginning. Some of the first things we did was challenge the notion of a brick wall and created brick pre-cast panels, which today are pretty common, same thing with exterior wall systems. Many of us, at least the older ones in the room, have all build stick system aluminum curtain wall and remember the inefficiencies of bolting all that together on site and now we have panel construction. The challenge is how do we ... And we've perfected that prefabrication notion. How do we take that thought pattern, that process and bring it to other building systems beyond structural steel and curtain wall fabrication. That's what I'd like to talk a little bit about tonight. Sylvia Smith: I'm Sylvia Smith, Senior Partner at FXFOWLE. I'm the token architect. To set the scene, FXFOWLE is 140 person global firm. We pride ourselves in design excellence and also implementing environmentally responsible building practices and buildings. We do large scale products around the world. Many of you know us from our large scale commercial buildings in the Times Square area, the recent, residential, beautiful complex at Greenwich Lane, the renovation of Javits, and now the design of Three Hudson Boulevard. We're also developing the framework for Governor's Island and Sunnyside Yards. Those are big, more commercially focused projects. In 1996, I started, I program focused intensive studio in the office and we really focused on cultural and educational work. Within that framework we've done projects from the Center for Global Conservation ... I always get trouble with my lists here. We're doing the Columbia University School of Nursing, the museum for the Statute of Liberty, major renovations now to Pace University and a number of campus projects in sub- Saharan Africa. We've anchored a number of strategic collaborations. The Columbia University School of Business, which is soon going to start construction, and the redevelopment of Lincoln Center, and now we're beginning work on David Geffen Hall at Lincoln Center. We seek to bring the best out of the design and consultant team. We see value in those relationships and I think that's key to the things that we're going to talk about tonight. We also see great value in how our thinking melds with the thinking of the construction team and the subcontractors. This integrated approach is very reliant on belief and collaboration. I think we will talk about that further tonight. I also will say that our firm has been working since 2008 on a modular start-up company called Global Building Modules. We're looking for ways to create component parts that can fit together and create great flexibility in creating buildings in a modular, excuse me, an expedited fashion. On the cultural side, perhaps the key driver on a current project is time. Our philosophy is: How can we look at a building as not separate elements, but as systems? How many of those systems can we fabricate off-site and bring onto the site and put together very quickly? As I was sitting here looking at the film, I'm hoping in a few years we'll be showing the film of that project showing the implementation of equally creative strategies. Thank you. Mitchel Simpler: Good evening. I'm Mitch Simpler, managing partner at Jaros, Baum and Bolles Consulting Engineers. For the 2 of you out here who don't know who we are, we are 101 year old consulting engineering firm specializing in mechanical, electrical, plumbing, and fire protection. Some of our legacy projects include the original World Trade Center, the Sears Tower, the Mesaterm in Germany, Sony Center in Berlin, Bank of China in Hong Kong, which turns out to be the Branch Bank, and we did the headquarters in Beijing. We also have a large practice in institutional healthcare and health sciences, and have been privileged to work with virtually all the people in this room and on this stage. One of the unique things I think that we're going to talk about tonight, in terms of the concept of modular and offsite fabrication, this technology is not new. It's new to New York. Most of us have been employing that technology overseas for 30 to 40 years. I have privileged to work with JBB now for, I'm in my 40th year. It's a real privilege to have been able to see this industry go through the changes that Charlie outlined earlier. I think this is truly going to be a break-through technology, not only form a construction standpoint, but also in the way we as designers formulate the design concepts and working with the construction team and designing a heads-up concept that plays into the modular and offsite prefabrication concepts. I think we'll dive into it pretty deep in the next hour and a half. Robert Barbera: Thank you. Good afternoon. My name is Rob Barbara. I'm responsible for the operation of the Turner Engineering Group. This division within Turner is a technical services group that provides design guidance and design knowledge for our design-build projects across the country. Our mission and focus is 3-fold. First and very simply is to manage and mitigate risk, design risk. Secondly we try and get a real jump on coordination, design coordination and related challenges. Thirdly, our focus is to try and optimize design to the best extent we can. We do so by collaborating with our design partners, like JB&B. We are not designers of record. Instead we inject ourselves into the process early on and really take the construction approach with design expertise and combine that with really obtaining the best engineered solutions for an efficient project. We have people from coast to coast within our group. We have geo-technical engineers, structural engineers, we have building envelope specialists as well. We will provide analysis and technical review of our own Turner projects, again in an effort to obtain an efficient design. The concept of prefabrication really feeds very well into all of the things we do in design, build. It's all about, a lot to do with schedule, it's a lot to do with fast-track, and how can we be as efficient and collaborative as early on as possible? That, I think, we're going to hear a lot about today. Thank you. Doug. Douglas Cooper: Great. We'll jump right into it. The first question is ... Forum panels, and I think I'll start with you, Bob. What do you see as some of the tangible benefits of prefabrication and modular? Bob Sanna: Well, I think the obvious one that comes to mind first is the quality control. Again, with BIM technology we're building to a higher degree of tolerances. We're building inside. In most cases, most of this fabrication is happening either low to the ground or inside a building or inside a tent. I think that gives a more ergonomic way for workers to approach their work, and I think it's safe. I think there's an element of you can see it with the work that was stacked up in the video. There was complicated structural connections that were all made off-site, that making them above the river, you have to do some naturally, but a multitude of connections and work that was happening over the side and over the highway, albeit shut down, but pretty high in the air, could happen at an off- site location in a safer manner.
Details
-
File Typepdf
-
Upload Time-
-
Content LanguagesEnglish
-
Upload UserAnonymous/Not logged-in
-
File Pages25 Page
-
File Size-