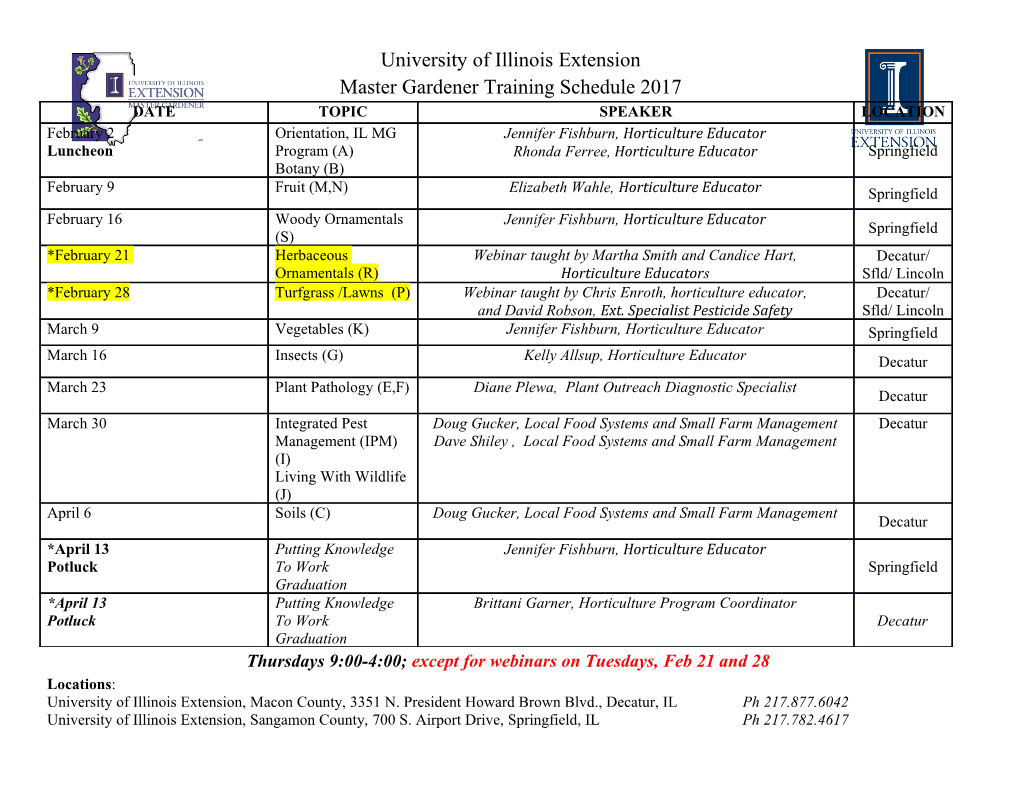
<p>Program Agenda</p><p>Day One:</p><p>Introduction of Lean Product Development: - The origins of Lean Product Development and how it supports Lean Manufacturing - Definition of 12 Wastes found in product development - Toyota benchmarking study overview - Lean Product Development Model: Process, People, Tools & Technology</p><p>Lean Product Development Simulation – Round #1 Traditional Product Development In this simulation round, teams of 6 participants will create drawings; build prototype components and final prototypes using a traditional product development process. This round will illustrate the typical wastes found within product development and metrics will be tracked to quantify these wastes.</p><p>Lean Process Techniques: - Kentou – Overview of the “Study” phase of development at Toyota - Set-Based Concurrent Engineering – definition and examples of a convergent method of development (vs. traditional iterative development approach) - Introduction to Queuing Theory – key principles of queuing related to development are explored including: effects of batching, system-utilization. - Flexible Capacity strategies are shown to reduce effects of system-utilization. - Problem Solving – concept of Genchi Genbutsu (“Go and See”) and effects of early problem solving on development resource loading is discussed.</p><p>People Systems: - Organization structures to balance technical competence with strong system integration are discussed. - Developing Towering Technical Competence – selection process, technical mentoring, evaluation and career paths are presented - Chief Engineer System – role of system integrator, development of integration skills, career path and examples from Toyota are presented.</p><p>Day Two:</p><p>Lean Tools and Technology – Organizational Learning & Continuous Improvement - Supplier Technology demonstrations – How Toyota integrates suppliers’ new technology into their development process - Engineering Checklists – Examples of structuring repositories of knowledge including capture and updating. - Quality Matrix – Unique approach to DFMEA at Toyota to identify, classify and resolve potential product risks throughout a development project - Hansei – Reflection approach at Toyota and other companies are compared and contrasted. - Hansei Exercise: A case study is done by participants to learn the Hansei approach and to “reflect” on class learnings to date.</p><p>Lean Tools and Technology – Tools for Alignment and Communication - Hoshin: A classic method at Toyota for aligning, deploying and reviewing improvement projects. - A3 Reports: A simple 1 page reporting method is presented. Examples of Proposals, Status, Informational and Problem Solving A3’s are presented. - A3 Exercise: Participants will practice using A3 to resolve an engineering problem. - Nemawashi: An informal but important approach to consensus building at Toyota is presented. - Obeya: Visual management techniques for PD are discussed. In particular, program management using the Obeya (Big Room) approach used at Toyota along with examples from other companies.</p><p>Summary of Lean Product & Process Development System - 13 principles of Lean Product Development are reviewed</p><p>Day Three:</p><p>Value Stream Mapping Overview: - Introduction: Overview and Background of VSM is presented. - Adaptation of VSM to apply to product development process - VSM icons – traditional and product development-specific are shown. Current State Map: - Mapping building blocks are presented - Current State Map Exercise – an engineering example will be worked through in class. The instructor will map one stream with participants and then participants will map a stream. - Current State Analysis – a method to analyze PD maps is presented. Participants will learn by going through the classroom example together. Future State Map: - A method to develop PD maps is presented. - The classroom engineering example will be used to illustrate the approach.</p><p>Implementation: - Implementation strategies for rolling out VSM approach including tips from implementation at companies will be discussed. </p><p>Day Four:</p><p>Design for Error Proofed Lean Manufacturing & Assembly - Different Ways of Thinking . If Manufacturing is becoming Lean; what changes are needed in our products? . Toyota vs. US OEM launch problems . Chief Production Engineer / more on Obeya Error Proofing Your Designs - What is error proofing? - What is systematic error proofing in key design stages? . Conducting Error Proofing mis-builds . Database and Capturing Key Learning’s - (Several) Individual and Team-Based Exercises; Application Design for Lean Manufacturing & Assembly - DFx terms defined - Impact of Design on Total System Costs - Toyota Big Differences: Engineering changes; freeze; cost examples - Four additional launch tips with lean manufacturing - OEM-Supplier Relations - DFA individual and team-based exercises; application Building with Modules Design for Error Proofed Lean Manufacturing & Assembly Checklist and Summary</p><p>Day Five:</p><p>Tools for Lean Launch: - Overview of methods to improve product launch phases - Introduction to 3P (Product & Production Preparation) method with examples. - Preparations for Lean Manufacturing: . Lean Equipment Design: Selection criteria for lean equipment to support lean manufacturing . Staffing and Standard Work: Operator balance and intro to standard work . Plan for Every Part: link from bill of material to part launch in plants . Lean Material Handling: Product/process design considerations to minimize material handling</p><p>Lean Product Development Simulation – Round #2 Lean Product Development In the second round, the same team of 6 participants will apply the tools and techniques learned throughout the week to the simulation product development process. The goal is to demonstrate the effects of applying the tools using a systems approach. Metrics will be collected again to measure the size of the changes relative to the first round.</p><p>Leading Lean Product Development: - Summary of 7 Lean Product Development cultural characteristics are presented - Implementation lessons learned are discussed - Implementation rollout approach is presented - Implementation examples from companies on the Lean Product Development journey - Open discussion</p>
Details
-
File Typepdf
-
Upload Time-
-
Content LanguagesEnglish
-
Upload UserAnonymous/Not logged-in
-
File Pages3 Page
-
File Size-