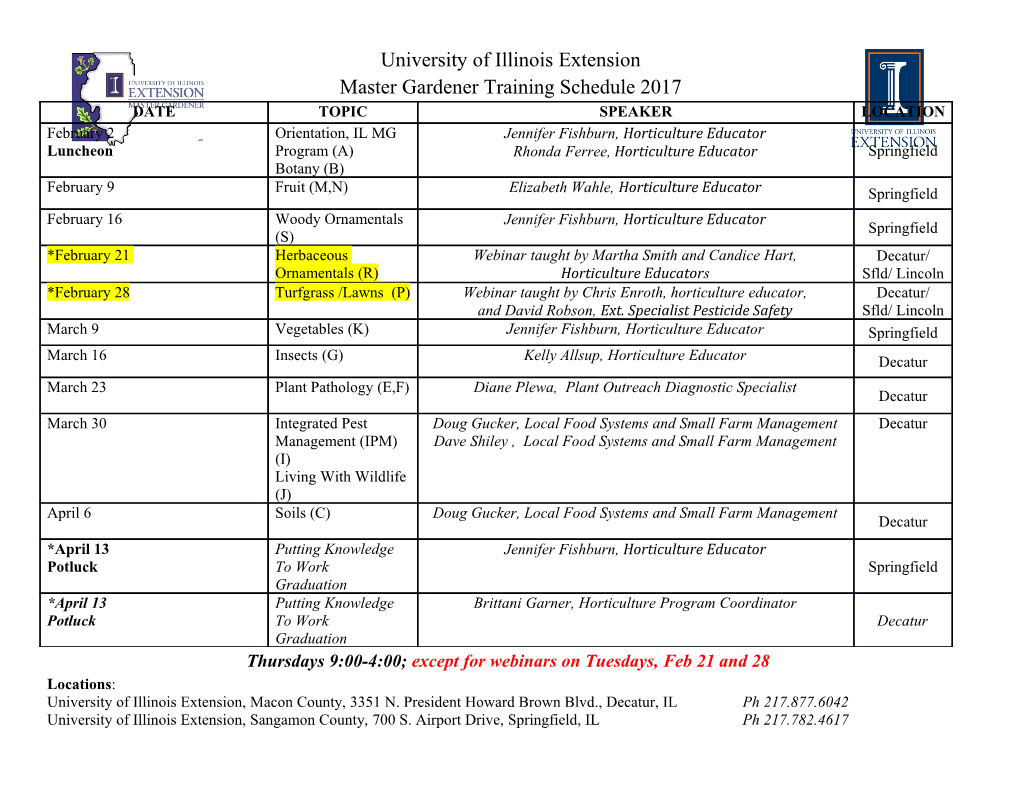
<p> TEMPLATE OPERATING PROCEDURE No 4</p><p>The Procedure for control of materials including non-conforming product</p><p>Authorisation and Amendment Record:</p><p>Issue Date of Reason for re-issue Prepared Authorised No. Issue by: by:</p><p>______Operating Procedure No: …….. Issue: …… Dated: ………… Page 1 of 14 The procedure for control of materials including non-conforming product</p><p>1. Purpose and scope</p><p>The purpose and scope of this procedure is to ensure that:</p><p>(a) Any items, component, subassembly or raw material that is to be incorporated</p><p> into …………. Plc product can be readily identified to type, drawing or part</p><p> number. That items of similar appearance cannot inadvertently get mixed or</p><p> substituted.</p><p>(b) There is no requirement or advantage in providing any form of traceability for</p><p>…….. plc products/services. If there was a particular contract requirement to do</p><p> so, special controls would be introduced.</p><p>(OR where it is a contract or legal requirement, items or material will have</p><p> traceability to the raw material certificate, OR foundry certificate, OR forge</p><p> certificate, OR material analysis, OR test certificate, OR certificate of</p><p> conformity, etc) that was provided by the original supplier, (OR to the</p><p> supplier/date of delivery/order No.) (OR where it is a contract or legal</p><p> requirement, ……………. Plc products [OR the following models ……, ……,</p><p>……,] are manufactured and tested into identifiable lots or batches. These will be</p><p> supplied with appropriate documentation pertaining to the identify and test results</p><p> of the individual lot or batch).</p><p>______Operating Procedure No: …….. Issue: …… Dated: ………… Page 2 of 14 (OR ………plc have identified that the ….., ….., ….., and ……. ranges of</p><p> models [OR food products, OR electric fans, OR ……..] are safety critical [OR</p><p> are susceptible to failure on one component i.e. ……………] and will be</p><p> assembled, [OR processed OR manufactured] and supplied as identifiable</p><p> batches and lots [OR with lot traceability]. This is in order that if a potential</p><p> problem batch is identified by customer complaint or return, ………. plc can</p><p> arrange a withdrawal or replacement and return of the suspect batch).</p><p>(c) ….. plc will ensure an adequate system for inspection status, i.e. can readily</p><p> identify whether materials, items, sub-assemblies or final products are good, bad,</p><p> suspect (OR on hold, OR quarantined) or reject (OR scrap).</p><p>(d) When items identified as suspect (OR placed on hold/quarantine) that there is a</p><p> prescribed and controlled procedure to ensure they are reviewed and controlled</p><p> through rework, repair or disposal. </p><p>(e) Where items (OR materials OR services) are supplied by the customer to assist</p><p>…. plc manufactures the final product (OR supplies the required service) that</p><p> these are positively identified to prevent misuse, substitution, loss or</p><p> deterioration.</p><p>2. Responsibility</p><p>It is the responsibility of the Director and all managers to ensure this procedure is</p><p> implemented fully and effectively. The supply of a defective product from …….. plc can</p><p> have a dramatic effect on customer confidence (OR cause fatal accident, OR ……..), this</p><p>______Operating Procedure No: …….. Issue: …… Dated: ………… Page 3 of 14 procedure must therefore be enforced rigorously. All staff and operatives with ………</p><p> plc must follow this procedure. Any members of ………. plc staff or operatives can and</p><p> must place items under temporary ‘hold’ if they are concerned that they do not conform</p><p> to the required specification.</p><p>Items under temporary ‘hold’ can be released only by the operative who placed them on</p><p> hold, or any manager. Items under formal ‘quarantine’ or ‘rejected’ can only be released</p><p> by the Quality Manager or the Director (OR ……….) and then only by completing the</p><p> prescribed records. No member of the Production Management has authority to release</p><p> items from ‘quarantine’ or ‘reject’. Staff and operatives will ensure there are sufficient</p><p> labels attached to clearly identify the product, or where appropriate, its inspection status.</p><p>As a pallet or container becomes empty all staff shall ensure that redundant labels are</p><p> removed. The Quality Manager is responsible for re-ordering the Inspection Status</p><p> labels. If they are not available for a short period temporary labels may be used from</p><p> white card.</p><p>3. Implementation (typical Production Manufacturing Shop or Site Installation [OR</p><p>Maintenance])</p><p>3.1 Control or Identity</p><p>The majority of …. Plc products are quite unique in size, shape, etc. and cannot</p><p> be mixed or substituted.</p><p>The only items that can get confused are:</p><p>………. and ……….</p><p>………. and ……….</p><p>______Operating Procedure No: …….. Issue: …… Dated: ………… Page 4 of 14 ………. and ……….</p><p>Only these items will have an identity number stencilled on the part (OR label</p><p> tied, attached or adhered, etc).</p><p>(OR whilst …… plc range of products is different in size and shape it is possible</p><p> for an inexperienced operative to get them mixed. In order to prevent this</p><p> happening and as an aid to training a series of boards are conveniently placed at</p><p> the middle of the production shop with an example of each part affixed to the</p><p> board and identified. By placing an item by the board, the part number of any</p><p> part can be very quickly identified.)</p><p>(OR once ……..plc is placed into sub-assemblies or onto the specified production</p><p> lines and become work within a specific process they cannot be mixed or</p><p> substituted. Hence only the raw materials and components are identified. This</p><p> may be by individual label or part number on the larger products, but the majority</p><p> are identified to type by labels on the tote bins, pallets or bags.)</p><p>(OR the items made by …….. plc are one-offs or small batches. With the job is a</p><p>‘Travelling Job Card’ (OR ‘Planning Sheet, OR ………) detailing the work to be</p><p> carried out. This card also identifies the drawings with the items and appropriate</p><p> material identity. If the identity of any material is not clear it will have a small</p><p> identity card/label attached or marked directly onto the item, with permanent</p><p> ink/paint). (OR some of the products made by …… plc are safety critical.</p><p>Therefore a formal controlled list of safety critical items is maintained. All of</p><p> these items will have the identity number marked onto the item, a batch number</p><p> and also motif to identify the supplier of that component and the year/month of</p><p> manufacture. This is specified as a requirement of our Purchase Order onto our</p><p>______Operating Procedure No: …….. Issue: …… Dated: ………… Page 5 of 14 suppliers. This level of control is essential both to enable product withdrawals</p><p> and also to throw the product liability [consumer protection] back onto the</p><p> original supplier.)</p><p>3.2 Control of material, including non-conforming product</p><p>Within ……. Plc we have introduced a simple coloured card/labelling system to</p><p> identify the inspection status of components.</p><p>(a) A yellow label identified as ‘hold’ see Form ….( OR Annex …..) This is</p><p> a temporary label for use by any member of ……….plc staff, or for an</p><p> operative to be able to use, where items are considered suspect or</p><p> awaiting test or awaiting further components, coat of paint, check by</p><p> customers representative, awaiting goods inward clearance, awaiting</p><p> suppliers certificate of conformity, confirmation of customer’s</p><p> specification, formal order documentation, customer’s returns awaiting</p><p> checking, etc. Items can be placed on ‘hold’ by any member of ..plc</p><p> staff. It can be removed only by the person placing it into ‘hold’, or any</p><p>……..plc Manager or Director.</p><p>(b) An orange label identified as ‘quarantine’ see Form ……(OR Annex</p><p>………) This is where items are confirmed as not to the required</p><p> specification. They must then go through a simple but formal review</p><p> procedure before they can be reworked, repaired, scrapped, etc. (see</p><p>Operating Procedure ….). Any member of …..plc staff can quarantine</p><p> items. It can only be lifted by the QA Manager or the Director (OR</p><p>……….) with the appropriate completed authority and record forms.</p><p>______Operating Procedure No: …….. Issue: …… Dated: ………… Page 6 of 14 (c) A red label identified as ‘reject’ see Form …… (OR Annex ….) These</p><p> items are not suitable for ….plc products; the label will not be removed</p><p> whilst the items are within …..plc. They will be sent for disposal, or</p><p> returned to the supplier with the red ‘reject’ label securely fixed. If</p><p> appropriate instructions may be given to ‘ruin’ or ‘slight’ the product by</p><p> painting or spraying red (Or chiselling across the working face or</p><p> stamping ‘R’ onto working face OR chopping off the connecting wires,</p><p>OR ……..) to positively prevent their re-introduction into the</p><p> manufacturing process. A ‘Reject’ label can only be fixed by an</p><p> approved Inspector, a Manager or a Director.</p><p>(d) A blue label identified as ‘special’ see Form……(OR Annex …..) It will</p><p> generally only be authorised by the Goods Inward Inspector, the Quality</p><p>Manager or the Director. This label will be used for the following:</p><p>* to positively identify ‘free issue’ or customer supplied products to</p><p> prevent its misuse, substitution or loss. At the completion of the</p><p> order/contract all excess ‘free issue’ material must be returned to the</p><p> customer. It will only be disposed of following written instructions or</p><p> permission from the customer;</p><p>* to identify all special batches where lot traceability has been requested;</p><p>* to identify items or batches that are special, have unique properties and</p><p> must not be mixed with normal production;</p><p>* special marking or assembly trials or items under development; also can</p><p> be used to identify ‘first offs’ for critical examination or machining trials;</p><p>* for use to identify test supplies taken by laboratory staff;</p><p>______Operating Procedure No: …….. Issue: …… Dated: ………… Page 7 of 14 * for use to identify ‘Approved Visual Standards’. The inspection of item</p><p>…… is a subjective visual inspection. To provide guidance to acceptable</p><p> standards on the features, acceptable surface defects, cosmetic</p><p> appearance, etc. acceptable examples of product are provided. These are</p><p> clearly identified and authorised using the label above, (OR there are</p><p> three examples of this approved visual standard. All three have been</p><p> approved, signed and dated by a representative of the customer and the</p><p>Quality Manager [OR ……..] of ……. Plc. The customer has selected</p><p> and holds one, the Quality Manager holds another and there is one</p><p> available at the place of work). Care should be taken not to damage the</p><p> visual standard. If it deteriorates it should be replaced. The blue label</p><p> will stay on the item whilst it is within …………..plc.</p><p>(e) (OR ………plc machines from various diameters of metal and</p><p>[OR plastic] bar stock that are held in racks in the bar stores. It is</p><p> vital that these are readily identifiable to type and specification of</p><p> material. Hence wherever practical the ends of the bar will have a</p><p> colour code painted onto the end. Care must be taken when doing</p><p> this as some stockists have their own colour codes. The colour</p><p> codes are shown at Form …..(OR Annex ….) at the end of this</p><p> procedure. A copy of the latest issue of this …………. will be</p><p> displayed in a plastic cover on the wall in the bar stores and in the</p><p> machine shop. This will be personally controlled and updated by</p><p> the Quality Manager to ensure it is the latest issue. Care must be</p><p> taken by machinists when sawing bars that the material identifying</p><p> codes stays with and on the bar left in stock. If there is a usable</p><p>______Operating Procedure No: …….. Issue: …… Dated: ………… Page 8 of 14 ‘cut-off’ that can be returned to store the code should be repainted</p><p> onto the end. All material without the paint code, such as angles,</p><p> plate must have the material identified on the item by permanent</p><p> labels or by ‘paint stick’. Material ordered or set aside for specific</p><p> jobs will have the job number affixed or painted onto it.) [ OR</p><p> the majority of bar or plate used by …………. plc is mild steel (</p><p>OR plastic, OR concrete OR ……….. ) to general spec ……….. ,</p><p>. This will not be colour coded, however all other material will be</p><p> carefully identified and coded ] </p><p>(OR useable bar stock off-cuts are put in the bin [OR shelves, etc.]</p><p> marked ‘Unidentified and uncontrolled material’. This material is</p><p> to be used for machine setting up or development trials. It may be</p><p> used on low cost, low duty jobs [where the customer has not</p><p> specified specific grade or material] on the instruction of the</p><p>Director or Quality Manager [OR Project Engineer, OR ……] this</p><p> will be detailed on the Job Card records and initialled and dated by</p><p> the Director [OR ……….., OR ……………])</p><p>(f) A green label identified as ‘Accepted/Passed Test’ see Form …. (</p><p>OR Annex ….) This is an OPTIONAL label. Due to effective</p><p> controls introduced within ….plc, it can generally be assumed that</p><p> any items without a hold, quarantine or other specified label is in</p><p> fact either acceptable material or work in progress. It may be used</p><p> to very clearly identify batches or items that have been subject to</p><p>______Operating Procedure No: …….. Issue: …… Dated: ………… Page 9 of 14 critical examination or test and have passed. It may also be</p><p> specified on individual Job Cards to be attached to each item or</p><p> batch for certain Quality Critical products (OR batches to be</p><p> supplied to Sony, Hitachi and Aiwa will always be subject to a</p><p> formal verification inspection and a ……plc green label neatly</p><p> completed and fixed to each item or packing box).</p><p>(OR ………plc products are supplied as home aids to the</p><p> handicapped. The customer particularly needs assurance that the</p><p> product has been carefully tested hence every product will have a</p><p>…plc green label attached. The label will be NEATLY completed</p><p> and signed off with an identifiable signature.) The green label will</p><p> only be affixed and signed by the operative or member of staff</p><p> either inspecting or testing the product.</p><p>(g) (OR …….plc wishes to positively identify items that have been the</p><p> subject of a concession/waiver or have been sold as sub-</p><p> standard/seconds. Such items will be marked (OR stamped) with a</p><p>‘C’ or ‘S’ as appropriate.)</p><p>(h) A white label identified as ‘Uncontrolled’. This is an optional</p><p> general-purpose label that may be attached if appropriate to items</p><p> that are outside the QA control system. Can be attached by any</p><p> member of ……. Plc staff. Typical examples are competitors’</p><p>______Operating Procedure No: …….. Issue: …… Dated: ………… Page 10 of 14 products, drawing office samples or exhibition pieces. This label</p><p> will generally stay on the item whilst it stays within </p><p>……………plc.</p><p>3.3 Where possible or practical items that are under ‘quarantine’ or ‘rejected’</p><p> will be segregated to a designated area. In some cases due to size of</p><p> product (OR explosive building limits OR chemical hazards, OR ……….)</p><p> it is not possible to physically segregate. In these cases special care should</p><p> be taken to ensure each item or container is clearly identified as</p><p>‘quarantine’ or ‘reject’.</p><p>3.4 In some cases it is essential (either to meet client’s critical delivery date, or</p><p> to keep operatives productively employed) to work on material under</p><p>‘hold’ or ‘quarantine’. If the Works Manager or Director wishes to take</p><p> this risk of subsequent rejection, they must authorise its use by a signed</p><p> and dated memo. The items must retain their identity and inspection status</p><p> as ‘hold’ or ‘quarantine’ until the items are subsequently accepted or</p><p> rejected.</p><p>3.5 All entries onto labels, both identity and inspection status, must be clearly</p><p> legible and in permanent ink, paint, engraving, moulded in, stamped, etc.</p><p>(OR as an additional improvement to labelling items, where specified it is</p><p> permitted to use a ….plc approved work mark to confirm items have been</p><p> personally inspected and are accepted. This is a rubber stamp [Or a metal</p><p> punch]. These are shown on Form…. (OR Annex …..). The Quality</p><p>______Operating Procedure No: …….. Issue: …… Dated: ………… Page 11 of 14 Manager has a record book identifying the unique work mark number to</p><p> the member of staff, date of issue and signature and date of withdrawal.</p><p>To prevent any conflict any work mark withdrawn, is scrapped and not re-</p><p> issued, also the identity number or initials will never be re-introduced).</p><p>3.6 It has been found that certain members of ………..plc staff have unusual</p><p> or illegible signatures. The QA Manager retains a control book of</p><p> inspectors, operatives and staff who can complete Quality Records. This</p><p> is known as the “Squiggle list”. It identifies the name of the authorised</p><p> signatory, with an example of signature and an example of initials.</p><p>3.7 Certain items received (OR used or made) at …..plc has a limited shelf</p><p> life. As these are received (OR made) they will be identified on their</p><p>……. with indelible ink or paint with their withdrawal date (or have a label</p><p> attached with date of retest, withdrawal, etc.</p><p>3.8 When items are identified as ‘Quarantined’ or ‘Reject’ they will then</p><p> become subject to the review and control of Operating Procedure 7.</p><p>3A Implementation (Typical Service Business)</p><p>3A.1 ….plc does not manufacture products but provide a service. The identity</p><p> of the specific service being provided is very clear from the documentation</p><p>(OR work order OR job requirement OR job file, OR …..) held by the</p><p> provider.</p><p>______Operating Procedure No: …….. Issue: …… Dated: ………… Page 12 of 14 3A.2 The inspection status of work (OR each document) is clear from the</p><p> progress of signatures on the control documents. From simple</p><p> examination of the documents it can clearly be identified which</p><p> item/service has been issued, which is in progress, which has been</p><p> completed and signed off and what has been verified. Not must also be</p><p> taken of Operating Procedure 8, reference ‘Control of Contract</p><p>Information, Drawings and Specifications’, with regard to control of mail</p><p> and other documents. (OR to have full control of incoming documents,</p><p> and also documents between departments or individuals, each document</p><p> will have small transmittal slip stapled or securely attached [OR be</p><p> stamped with rubber stamp]. This will show Project/Job number, who to</p><p> see it for information, who to action it, who to file it, with space available</p><p> for initials and date to confirm it has been seen or actioned.)</p><p>3A.3 As an additional Inspection Status control we have a ‘Quarantine’ label.</p><p>These can be applied to doubtful or non-conforming files or envelopes,</p><p> etc. to prevent despatch.</p><p>3A.4 Occasionally the customer provides ………...plc with copies of their</p><p> specifications (OR examples of products, OR confidential</p><p> documents/records). To prevent loss, misuse (OR unauthorised copying),</p><p> these will be identified by a ‘Blue’ Special Control label see Form……(</p><p>OR Annex ……)</p><p>______Operating Procedure No: …….. Issue: …… Dated: ………… Page 13 of 14 3A.5 Within the documents held are old or obsolete documents, brochures,</p><p> standards, wall charts, etc. These are held for general and background</p><p> information only. These are identified with a stamp stating ‘uncontrolled</p><p> copy for info only’.</p><p>______Operating Procedure No: …….. Issue: …… Dated: ………… Page 14 of 14</p>
Details
-
File Typepdf
-
Upload Time-
-
Content LanguagesEnglish
-
Upload UserAnonymous/Not logged-in
-
File Pages14 Page
-
File Size-