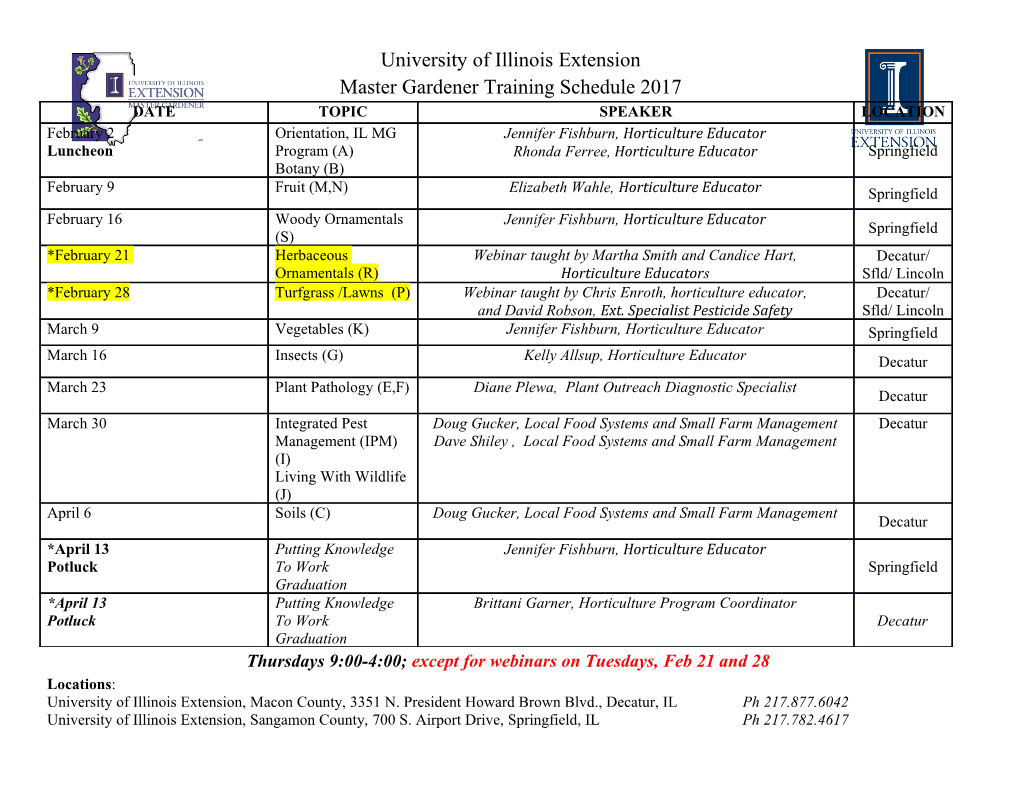
<p> ES4</p><p>Waste Management Project:</p><p>CELLULOSE</p><p>Group members: Joanne Moran Edel Kerins Marc Falconer</p><p>Lecturer: Dr. Michael Broaders</p><p>Date of completion: 6th of December 2005 1- Introduction </p><p>Cellulose is found in plants as micro fibrils. These form the structurally strong framework in the cell walls. Cellulose (E460) is mostly prepared from wood pulp. It was first recognised by Anselm Payen in 1838. </p><p>Structural unit </p><p>4 Cellulose is a linear polymer of b-(1®4)-D-glucopyranose units in C1 conformation. The fully equatorial conformation of b-linked glucopyranose residues stabilizes the chair structure, minimizing its flexibility (e.g. relative to the slightly more flexible a- linked glucopyranose residues in amylose). Cellulose preparations may contain trace amounts (~0.3%) of arabinoxylans. </p><p>Cellulose is an insoluble molecule consisting of between 2000 - 14000 residues with some preparations being somewhat shorter. It forms crystals (cellulose Ia) where intra- molecular (O3-H®O5' and O6®H-O2') and intra-strand (O6-H®O3') hydrogen bonds holds the network flat allowing the more hydrophobic ribbon faces to stack. Each residue is oriented 180° to the next with the chain synthesized two residues at a time. Although individual strand of cellulose are intrinsically no less hydrophilic, or no more hydrophobic, than some other soluble polysaccharides (such as amylose) this tendency to form crystals utilizing extensive intra- and intermolecular hydrogen bonding makes it completely insoluble in normal aqueous solutions (although it is soluble in more exotic solvents such as aqueous N-methylmorpholine-N-oxide </p><p>(NMNO, ), CdO/ethylenediamine (cadoxen), LiCl/N,N'- dimethylacetamide or near supercritical water). It is thought that water molecules </p><p>1 catalyze the formation of the natural cellulose crystals by helping to align the chains </p><p>Cellulose has many uses as an anticake agent, emulsifier, stabilizer, dispersing agent, thickener, and gelling agent but these are generally subsidiary to its most important use of holding on to water. Water cannot penetrate crystalline cellulose but dry amorphous cellulose absorbs water becoming soft and flexible. Some of this water is non-freezing but most is simply trapped. Less water is bound by direct hydrogen bonding if the cellulose has high crystallinity but some fibrous cellulose products can hold on to considerable water in pores and its typically straw-like cavities; water holding ability correlating well with the amorphous (surface area effect) and void fraction (i.e. the porosity). As such water is supercoolable, this effect may protect against ice damage. Cellulose can give improved volume and texture particularly as a fat replacer in sauces and dressings but its insolubility means that all products will be cloudy.</p><p>Swelled bacterial cellulose (ex. Acetobacter xylinum), in its never-dried state with much smaller fibrils (~1%) than from plants, exhibits pseudoplastic viscosity like xanthan gels but this viscosity is not lost at high temperatures and low shear rates as the cellulose can retain its structure. Where individual cellulose strands are surrounded by water they are flexible and do not present contiguous hydrophobic surfaces. Bacterial cells may be removed by hot alkali and the clean wet cellulose used as a substrate for immobilizing biomolecules or for covering wounds. On drying the properties of bacterial cellulose irreversibly lose their hydrated properties and tend About a third of the world's production of purified cellulose is used as the base material for a number of water-soluble derivatives with pre-designed and wide- ranging properties dependent on groups involved and the degree of derivatization (for an extensive review see. Derivatizing cellulose interferes with the orderly crystal- forming hydrogen bonding, described above, so that even hydrophobic derivatives may increase the apparent solubility in water. Methyl cellulose (E461) made by methylating about 30% of the hydroxyl groups) is thermogelling, forming gels above a critical temperature due to hydrophobic interactions between high-substituted regions and consequentially stabilized intermolecular hydrogen bonding. Such gels break down on cooling in a manner similar to that causing the solubility minimum for non-polar gases; hydrophobic saccharides becoming less soluble as the temperature increases. This property is useful in forming films as barriers to water loss and for holding on to small gas bubbles. Hydroxypropylmethylcellulose (HPMC, E464) has similar properties and uses but with added water interaction. Both methylcellulose and HPMC may be used in gluten-free bakery products as gluten substitutes. Hydroxypropyl cellulose (E463) possesses good surface activity but does not gel as it forms open helical coils. It is a water-soluble thickener, emulsifier and film-former often used in tablet coating. Another important derivative of cellulose is carboxymethylcellulose. 2 - Different treatments used in the conversion processes of cellulose</p><p>2.1 -Treatment of Carbon fibres</p><p>In Textile Terms and Definitions, carbon fiber has been described as a fiber containing at least 90% carbon obtained by the controlled pyrolysis of appropriate fibers. The term "graphite fiber" is used to describe fibers that have carbon in excess of 99%. Large varieties of fibers called precursors are used to produce carbon fibers of different morphologies and different specific characteristics. The most prevalent precursors are polyacrylonitrile (PAN), cellulosic fibers (viscose rayon, cotton), petroleum or coal tar pitch and certain phenolic fibers. Carbon fibers are manufactured by the controlled pyrolysis of organic precursors in fibrous form. It is a heat treatment of the precursor that removes the oxygen, nitrogen and hydrogen to form carbon fibers. It is well established in carbon fiber literature that the mechanical properties of the carbon fibers are improved by increasing the crystallinity and orientation, and by reducing defects in the fiber. The best way to achieve this is to start with a highly oriented precursor and then maintain the initial high orientation during the process of stabilization and carbonization through tension. There are three successive stages in the conversion of PAN precursor into high-performance carbon fibers. Oxidative stabilization: The polyacrylonitrile precursor is first stretched and simultaneously oxidized in a temperature range of 200-300°C. This treatment converts thermoplastic PAN to a non-plastic cyclic or ladder compound. Carbonization: After oxidation, the fibers are carbonized at about 1000°C without tension in an inert atmosphere (normally nitrogen) for a few hours. During this process the non-carbon elements are removed as volatiles to give carbon fibers with a yield of about 50% of the mass of the original PAN. Graphitization: Depending on the type of fiber required, the fibers are treated at temperatures between 1500-3000°C, which improves the ordering, and orientation of the crystallites in the direction of the fiber axis. 2.2 - Optimisation of pre-treatment of fermentable CHO products for Bioethanol production.</p><p>The cellulose cannot be enzymatically hydrolyzed to glucose without a physical and chemical pre-treatment. The physical and chemical protection of cellulose must be removed before subsequent hydrolysis and fermentation steps for bioethanol production. The pre-treatment processes normally applied on the different substrates are acidic hydrolysis, steam explosion and wet oxidation. A problem for most pre-treatment methods is the generation of compounds that are inhibitory towards the fermenting microorganisms, primarily phenols. Degradation products that could have inhibitory action in later fermentation steps are avoided during pre-treatment by wet oxidation. Alkaline wet oxidation (using high temperature, oxygen and carbonate) has been shown to be an efficient pre- treatment method for wheat straw, producing a hydrolysate rich in hemicellulose and highly (67 %) convertible cellulose fibres. The hydrolysate constituted 9 g/L solubilised hemicellulose, 6 g/L carboxylic acids and 0.3 g/L phenolic lignin degradation products. </p><p>A project is under way in cooperation with Elsam, an industrial partner, to develop hydrothermal treatment of wheat straw on a pilot plant scale. The objective of the project is to develop a pilot plant for pre-treatment of plant fibre biomass for bioethanol production and production of solid alkali free biofuel for electricity production. Elsam uses co-combustion of coal and straw (up to 15%) for their electricity production, and more straw is wished to be used to this purpose. The reactor removes the high potassium chloride content from the straw, as these damages the boilers by corrosion. The enzymatic convertibility of cellulose and hemicellulose are also determined in the solid fibres and liquid extracts to assess potential ethanol production following the pre-treatment of biomass. </p><p>The aims of this project are to evaluate the potential of new raw materials and of new microorganisms for bioethanol production. The first aim of the project is to evaluate the suitability of grass-clover leys as feedstock material for fermentation. Clover/grass mixtures present a double advantage, they decrease the reliance on external sources of nitrogen (produced using fossil fuels) both in the field and in the fermentor. The clover plants are fixing nitrogen from the atmosphere and the ley do not need to receive mineral nitrogen fertilizer in the field. N fertilizers represent about one third of the energy budget of plant production in the developed countries. Harvested grass-clover also typically has a high content of nitrogen in the form of proteins. When material low in nitrogen is used as a substrate for the fermentation, it must be supplied in the form of urea, a major energy cost. The use of grass/clover mixture as raw material has the potential to increase the energy efficiency of the ethanol production system, by decreasing the reliance on external sources of nitrogen, in the field and during fermentation. After pre-treatment, a second aim is also to extract and purify hemicelluloses of the substrate to be utilized in the production of biopolymers. A third aim in the project is to study the ability of a new fungus strain to ferment the pentosan fraction of clover into ethanol. The pentosan is a constituent of hemicellulose typically unavailable to the yeasts used during fermentation for the production of ethanol. The utilization of both the cellulose and hemicellulose fraction is required in an economically viable bioethanol production. 3 – Environmental benefits of Cellulose conversions</p><p>3.1 - Biodiesel</p><p>Biodiesel is a clean burning alternative fuel, produced from domestic, renewable resources. It is made by chemically combining any natural oil or fat with an alcohol such as methanol or ethanol. This process, called transesterification, involves mixing methanol with sodium hydroxide, then mixing that with soybean oil, for example, and letting the glycerine settle. The final products are methyl soyate and glycerine. The current key biodiesel markets are mass transit, marine, and other environmentally sensitive areas, such as mines. The potential for biodiesel in these markets is still under investigation. One bushel of soybeans produces about 1.5 gallons of biodiesel. A gallon of soy-based biodiesel contains 132,902 BTUs. Biodiesel improves air quality by sharply reducing the emissions, including particulate matter, that straight petroleum diesel releases when it burns. Biodiesel-powered engines deliver similar torque, horsepower and kilometres per litre as petroleum-powered diesels. Biodiesel does not require new refuelling stations, new parts inventories or expensive engine modifications. France is currently the world's largest producer of biodiesel, using it as heating oil and also in 50 percent blends with petrodiesel. </p><p>3.2 – Ethanol The increased use of renewable fuels will reduce smog and green house gas emissions. Renewable fuels such as ethanol are one of the best tools we have to fight air pollution from vehicles. Ethanol contains 35% oxygen. Adding oxygen to fuel results in more complete fuel combustion, thus reducing harmful tailpipe emissions. Gasoline containing a 10% ethanol blend will reduce smog generating emissions like carbon monoxide (25-30%), particulate matter (50%) and volatile organic compounds (7%).Ethanol can be used in place of harmful aromatics like benzene – the most toxic compound in gasoline. In addition, ethanol does not contain sulphur. The environmental benefits increase as biodiesel and cellulose ethanol grow as a percentage of renewable fuel in Ontario. Some Facts… The Canadian government estimates that, “If 35 percent of gasoline in Canada contained ten percent ethanol, GHG emissions would be reduced by 1.8 mega tonnes per year (1.8 million tonnes), which is the equivalent of removing more than 400,000 vehicles from the road.” The American Lung Association of Metropolitan Chicago credits ethanol-blended reformulated gasoline with reducing smog-forming emissions by 25% since 1990.</p><p>3.3 – Another positive outcome is Cellulose insulation</p><p>Cellulose insulation is made from recycled wood fibre, primarily newspaper. One hundred pounds of cellulose insulation contains 80 to 85 pounds of recycled newsprint. America's cities are struggling with the challenge of solid waste disposal. Waste paper is a major part of the refuse stream. Today more and more communities are addressing this problem through "curbside recycling" and similar conservation programs. These efforts work only if there is demand for recycled products. Paper that is not recycled ends up in landfills, where it may contribute to environmental pollution, or at incinerators where energy is wasted reducing it to ashes, soot, and smoke. When you choose cellulose insulation you are making a positive contribution toward solving the solid waste disposal problem. That may help your community hold down taxes or refuse disposal charges. It certainly contributes to a cleaner environment.</p><p>Advantages of using Cellulose insulation </p><p>Cellulose fills existing walls with fewer voids and stops air infiltration better!</p><p>Demonstrations using transparent plastic "walls" inevitably show the superiority of cellulose in filling existing walls with many fewer gaps and voids than mineral fibre materials. The fibres of cellulose insulation are much finer than mineral fibre blowing wool. When cellulose is run through an appropriate blowing machine it takes on almost liquid-like properties that let it flow into cavities and around obstructions to completely fill walls and seal every crack, seam, and opening. No fibre glass or rock wool material duplicates this action. Liquid-applied foam plastics certainly do, but they cost much more than cellulose. IN new construction cellulose insulation can be installed in walls using wet-spray or several different dense-pack dry techniques that are even more effective at sealing homes against air infiltration.</p><p>Cellulose saves more energy In terms of national policy the energy you save directly at home isn't the only important consideration. Our country has emphasized energy conservation to reduce our dependence on foreign fuel sources and make America less vulnerable to international "energy blackmail." If you are concerned about America's energy independence you need to understand "embodied energy." Embodied energy is the energy consumed in producing products. Mineral insulation comes from giant furnaces that gulp fossil fuel to melt sand, slag, or similar materials. Foam plastics are petrochemicals. They are literally made out of energy! Cellulose insulation is made by processing recycled wood fibres through electrically- driven mills that consume relatively little energy when they are operating, and which can be shut down completely with the flip of a switch at the end of the shift -- or even for lunch and coffee breaks. Fibre glass, rock wool, and plastic insulation have from 50 to over 200 times more embodied energy than cellulose. When you choose these products you will certainly save on the amount of energy you consume at home, but you contribute to increased overall demand for oil and gas. And increased demand drives up prices. n you install cellulose insulation you are not only choosing to save energy in your home; you are choosing to save energy at the factory where the insulation is produced. By helping reduce our nation's overall energy consumption you not only reduce our vulnerability to foreign pressures, you are actually helping hold down utility rates and the price you pay for gasoline, plastic goods, and other products that come from oil and natural gas.</p><p>Cellulose makes homes safer All residential structures contain large amounts of wood. Cellulose insulation is the only wood-based construction material that is normally treated for fire retardancy. This treatment makes cellulose insulation one of the safest materials used in home construction. Cellulose insulation that meets accepted standards is a Class 1 material, just like loose-fill mineral fibre insulation If a fire should occur, the dense structure of cellulose and its fire retardants slow its spread through the building by blocking flames and hot gases restricting the availability of oxygen in insulated assemblies. Fire tends to roar right through fibre glass and the open fibre structure of this material makes oxygen freely available to burning framing lumber. Several fire demonstrations have been conducted in which cellulose-insulated structures have remained virtually intact while uninsulated and mineral-fibre insulated structures were reduced to ashes.</p><p>Uses of Micro organisms in cellulose based products A biomass fuel is an energy source derived from living organisms. Most commonly it is plant residue, harvested, dried and burned, or further processed into solid, liquid, or gaseous fuels. The most familiar and widely used biomass fuel is wood. Agricultural waste, including materials such as the cereal straw, seed hulls, corn stalks and cobs, is also a significant source. Native shrubs and herbaceous plants are potential sources. Animal waste, although much less abundant overall, is a bountiful source in some areas. Wood accounted for 25 percent of all energy used in the United States at the beginning of this century. With increased use of fossil fuels, its significance rapidly declined. By 1976, only 1 to 2 percent of United States energy was supplied by wood, and burning of tree wastes by the forest products industry accounted for most of it. Although the same trend has been evident in all industrialized countries, the decline has not been as dramatic everywhere. Sweden, for instance, still meets 8 percent of its energy needs with wood, and Finland, 15 percent. Globally, it is estimated that biomass supplies about 6 or 7 percent of total energy, and it continues to be a very important energy source for many developing countries. In the last 15 to 20 years, interest in biomass has greatly increased even in countries where its use has drastically declined. In the United States rising fuel prices led to a large increase in the use of wood-burning stoves and furnaces for space heating. Impending fossil fuel shortages have greatly increased research on its use in the United States and elsewhere. Because biomass is a potentially renewable resource, it is recognized as a possible replacement of petroleum and natural gas. Historically, burning has been the primary mode for using biomass, but because of its large water content it must be dried to burn effectively. In the field, the energy of the sun may be all that is needed to sufficiently lower its water level. When this is not sufficient, another energy source may be needed. Biomass is not as concentrated an energy source as most fossil fuels even when it is thoroughly dry. Its density may be increased by milling and compressing dried residues. The resulting briquettes or pellets are also easier to handle, store, and transport. Compression has been used with a variety of materials including crop residues, herbaceous native plant material, sawdust, and other forest wastes. Solid fuels are not as convenient or versatile as liquids or gases, and this is a drawback to the direct use of biomass. Fortunately, a number of techniques are known for converting it to liquid or gaseous forms. Partial combustion is one method. In this procedure, biomass is burned in an environment with restricted oxygen. Carbon monoxide and hydrogen are formed instead of carbon dioxide and water. This mixture is called synthetic gas or "syngas." It can serve as fuel although its energy content is lower than natural gas (methane). Syngas may also be converted to methanol, a one carbon-alcohol that can be used as a transportation fuel. Because methanol is a liquid, it is easy to store and transport. Cellulose is the single most important component of plant biomass. Like starch, it is made of linked sugar components that may be easily fermented when separated from the cellulose polymer. The complex structure of cellulose makes separation difficult, but enzymatic means are being developed to do so. Perfection of this technology will create a large potential for ethanol production using plant materials that are not human foods. The efficiency with which biomass may be converted to ethanol or other convenient liquid or gaseous fuel is a major concern. Conversion generally requires appreciable energy. If an excessive amount of expensive fuel is used in the process, costs may be prohibitive. Corn (Zea mays) has been a particular focus of efficiency studies. Inputs for the corn system include energy for production and application of fertilizer and pesticide, tractor fuel, on-farm electricity, etc., as well as those more directly related to fermentation. A recent estimate puts the industry average for energy output at 133 percent of that needed for production and processing. This net energy gain of 33 percent includes credit for co-products such as corn oil and protein feed as well as the energy value of ethanol. The most efficient production and conversion systems are estimated to have a net energy gain of 87 percent. Although it is too soon to make an accurate assessment of the net energy gain for cellulose based ethanol production, it has estimated that a net energy gain of 145 percent is possible. Biomass-derived gaseous and liquid fuels share many of the same characteristics as their fossil fuel counterparts. Once formed, they can be substituted in whole or in part for petroleum-derived products. Gasohol, a mixture of 10 percent ethanol in gasoline, is an example. Ethanol contains about 35 percent oxygen, much more than gasoline, and a gallon contains only 68 percent of the energy found in a gallon of gasoline. For this reason, motorists may notice a slight reduction in gas mileage when burning gasohol. However, automobiles burning mixtures of ethanol and gasoline have a lower exhaust temperature. This results in reduced toxic emission s, one reason that clean air advocates often favor gasohol use in urban areas. Biomass is called as a renewable resource since green plants are essentially solar collectors that capture and store sunlight in the form of chemical energy. Its renewability assumes that source plants are grown under conditions where yields are sustainable over long periods of time. Obviously, this is not always the case, and care must be taken to insure that growing conditions are not degraded during biomass production. A number of studies have attempted to estimate the global potential of biomass energy. Although the amount of sunlight reaching the earth's surface is substantial, less than a tenth of a percent of the total is actually captured and stored by plants. About half of it is reflected back to space. The rest serves to maintain global temperatures at life- sustaining levels. Other factors that contribute to the small fraction of the sun's energy that plants store include Antarctic and Arctic zones where little photosynthesis occurs, cold winters in temperate belts when plant growth is impossible, and lack of adequate water in arid regions. The global total net production of biomass energy has been estimated at 100 million megawatts per year per year. Forests and woodlands account for about 40 percent of the total, and oceans about 35 percent. Approximately one percent of all biomass is used as food by humans and other animals. Soil requires some organic content to preserve structure and fertility. The amount required varies widely depending on climate and soil type. In tropical rain forests, for instance, most of the nutrients are found in living and decaying vegetation. In the interests of preserving photosynthetic potential, it is probably inadvisable to remove much if any organic matter from the soil. Likewise, in sandy soils, organic matter is needed to maintain fertility and increase water retention. Considering all the constraints on biomass harvesting, it has been estimated that about 6 million MWyr/yr of biomass are available for energy use. This represents about 60 percent of human society's total energy use and assumes that the planet is converted into a global garden with a carefully managed "photosphere." Although biomass fuel potential is limited, it provides a basis for significantly reducing society's dependence on non-renewable reserves. Its potential is seriously diminished by factors that degrade growing conditions either globally or regionally. Thus, the impact of factors like global warming and acid rain must be taken into account to assess how well that potential might eventually be realized. It is in this context that one of the most important aspects of biomass fuel should be noted. Growing plants remove carbon dioxide from the atmosphere that is released back to the atmosphere when biomass fuels are used. Thus the overall concentration of atmospheric carbon dioxide should not change, and global warming should not result. Another environmental advantage arises from the fact that biomass contains much less sulphur than most fossil fuels. As a consequence, biomass fuels should reduce the impact of acid rain. </p><p>4.0 The Utilization of Cellulose And examples of products derived from cellulose </p><p>Cellulose is a substance which has many valuable attributes which make it an important resource for people all over the world. These attributes have already been discussed in the introduction and will not be dwelt upon in this section; however, the physical and chemical properties of cellulose should be kept in mind as they are the main reason why cellulose can and is utilized by people in so many different ways.</p><p>The first and most important utilization of cellulose is from wood and cotton. Wood and cotton combined are the major cellulose reservoirs for all cellulose products such as paper, textiles, construction materials, cardboard and also derivatives of cellulose which include cellophane, cellulose acetate, rayon, ethyl cellulose, methyl cellulose, microcrystalline cellulose. Of the above list paper is the most important cellulose based product. It is of great economic importance to the human world. The following is a brief summary of how paper is made from higher plants and the reasons why cellulose fibres are so suitable for paper. There are several higher plant sources that can be used to obtain the necessary cellulose fibres for papermaking. These are wood, bamboo, esparto, hemp, jute, wheat sugar cane or rice. Which of the list is used depends on the availability and the quality of the paper required i.e. paper derived from hardwood would be of a superior quality to rice paper. The basic paper production process is as follows (for wood). A mixture which consists of the plant fibres and water (pulp) is filtered through a fine screen to form a sheet of paper. As the wet sheet dries chemical bonds are developed between the molecules in the cellulose fibres, this chemical bonding gives the paper its strength. The reasons why cellulose fibres are so suited for paper making are the following. 1) Hydrophilicity, this permits them to be readily dispersed in water. 2) A fine structure which allows Fibrillation. 3) The fibre length is sufficient to allow the formation of a highly entangled web of considerable strength. 4) The ability for hydrogen bond formation to occur between fibres as the web dries, thus providing additional strength in the sheet of the paper. The Paper production industry is one which has enormous economic value for the world. The forest products industry in the United States is worth $70 billion per year. In the United States alone, more than two million tons of newsprint and writing paper are produced each year. This is an enormous amount of paper and shows the scale of the industry. This demand for paper places a lot of strain on our forests and other reservoirs of cellulose around the world (bamboo, esparto, hemp etc.). The environmental impacts of the paper production industry and other industries which use cellulose will be discussed in the last section of the report. The next area which will be focused on as regards cellulose utilization will be the production of textiles. Textiles derived chiefly from cellulose fibres have been used by people for thousands of years. These are cotton, which is almost one hundred percent cellulose, hemp and linen. Cotton has been found in tombs in India dating back to 3,000 BC. Linen, made from fibres of the flax plant, is one of the world’s oldest fabrics. Lesser known fibres such as ramie, jute, and hemp have many uses, varying from finely woven fabrics to rope. These textiles utilized the inherent natural qualities of cellulose and were generally comfortable and absorbent. Synthetic fibres are created through a process that results in the usable fibre. Rayon consists of regenerated cellulose materials (like cotton waste and wood pulp). Even though the cellulose material is of natural origins, it has to be processed with chemicals in order that a thick liquid can be created which can then be spun into fibre. Cellulose based fibres, including acetate and rayon usually require dry-cleaning. </p><p>Example of natural cellulose based textile Fig 1.0 Cellulose based products can also be found in use in the Construction Industry. Examples of products used which are cellulose based are A) Carbon Fibre Reinforced Polymers (CFRP’s). These are used for the post- strengthening of existing structures. They are made from the extraction of cellulose fibrils out of wood with a diameter of just a few nm and a length of several µm. These fibrils can be used as polymer reinforcement preferably in combination with biodegradable polymers. CFRP’s are used to correct design defects, correct workmanship defects, support additional load requirements and provide resistance to the effects of seismic activity. Fig 1.1</p><p>Carbon reinforced concrete beam. Another important cellulose based product which is used in the construction industry would be cellulose insulation products. Cellulose insulation is formed by adding a carefully formulated mixture of mineral salts to recycled newsprint which has already been ground down to the requisite level. Cellulose insulation can be used as a Spay applied blanket (SAB), Spray cavity system (SCS) or Acoustic thermal coat (ATC). Cellulose insulation is very efficient, easily applied and cost effective. Cellulose based insulation was first patented in 1893 in England. Worldwide use began to expand in the early 20th century. Cardboard is a cellulose based product which is very widely used around the world, mainly for packaging purposes. It was first invented in China sometime in the 15th century. The type of wood pulp used to make the cardboard will have a bearing on its strengths and weaknesses. Cardboard made from Hardwood pulp (which has shorter fibres) has good compression strength and is easily mouldable with heat and moisture, but is weak in tension and tears easily. On the other hand cardboard boxes made from softwood pulp (which have longer fibre length) will be more resistant to puncturing and tearing, less plastic and have more tensile strength. The corrugated cardboard box was invented in 1890. By the beginning of the 20th century the wooden crates and boxes used in trade started to be superseded by the introduction of corrugated cardboard boxes. The following is a list of products which are derived from cellulosic material. i) Cellulose acetate. This material was first prepared in 1865 by Paul Schutzenberger. It required another 29 years of research and development before it was able to be manufactured commercially. Cellulose acetate is made from processed wood pulp. The pulp is processed using acetic anhydride to create acetate flake from which products are made. The typical properties of cellulose acetate include among others; deep gloss, good toughness, high transparency and a natural feel. Cellulose acetate has many uses. Cellulose acetate fibres can be used for textiles and clothing and can be combined with many other fibres such as rayon, cotton, wool, silk etc. It can also be used for spectacle frames, tool handles etc. It was also used as a waterproofing and strengthening agent for the fabrics used to cover the wings of aeroplanes. ii) Cellulose nitrate. This was the first successful plastic. It was developed in 1869 by converting alcoholic cellulose into nitrate esters. Cellulose nitrate was also of benefit to the automobile industry with the development of lacquers in the 1920s. It is used now for making toilet pieces and other industrial items. iii) Ethyl cellulose. This material is formed when alkali cellulose is treated with ethyl chloride or ethyl sulphate. This material is used in making flashlight cases, fire extinguishers and parts for electrical appliances. Ethyl cellulose is also used in both the granular and tape form as an inhibitor of rocket propellant grains. Ethyl cellulose is the lightest and most expensive of the cellulosic products.</p><p> iv) Methyl Cellulose. This substance is a weak adhesive which is non toxic and has a plasma like consistency. The main use for Methyl cellulose, in its pure state, is as a cleaning agent for the spines of books which are being re-cased or put into new cases. It is a very good solvent of hide glue, some modern adhesives and will soften PVA (polyvinyl acetate) up to a point. Methyl cellulose is also used as a bulk forming fibre laxative. Bulk laxatives absorb liquid in the intestines and swell to form a soft bulky stool. The bulky mass stimulates the intestinal muscles which hastens the progress of the stools passage through the intestine. v) Rayon. This is a transparent fibre made of processed cellulose. The cellulose fibres which are derived from wood or cotton are dissolved in alkali to create a solution called viscose. The viscose is then pulled through a nozzle into an acid bath in which the viscose is reconverted into cellulose. Rayon was fist produced commercially in 1884 for use in the Textile industry but was rapidly recalled from the market due to its extreme flammability, there were too many Victorian gentlemen going up in flames after reaching over a candle. Rayon is now a much safer material and is used widely in many articles of clothing. It is the most useful fibre to people. vi) Microcrystalline cellulose. (MCC) This is basically cellulose which is derived from high quality wood pulp. Microcrystalline cellulose can only be derived from a special grade of alpha cellulose. The amorphous region and any impurities are removed through a process which involves passing the wood pulp through a mineral acid bath, the slurry is then spray dried, this is spraying the slurry through hot jets to evaporate the moisture. Microcrystalline cellulose has many uses which include; binder, carrier, drying agent and tableting aid. vii) Hydroxylpropyl Methylcellulose (HPMC) HPMC is a cellulose ether. It is derived from alkali treated cellulose that has been reacted with methyl chloride and propylene oxide. It can be used as an ingredient in hard capsules which are used for encapsulating powdered herbs. It also has many other uses which include; emulsifier, thickening agent, stabilizer, gellant and suspending agent. HPMC and MCC are both used extensively in the food production industry. </p><p>4.1 Microbial Cellulose A new resource for Wood, Paper, Textiles, Food and Specialty products.</p><p>What is Microbial cellulose?</p><p>Microbial cellulose is cellulose which is produced by Acetobacter xylinum which is one of the most advanced types of purple bacteria. This is a non-photosynthetic organism which can procure glucose, sugar, glycerol, or other organic substrates and convert them into pure cellulose</p><p>How is it formed? </p><p>Microbial cellulose is formed by the natural cellulose making process inherent to Acetobacter xylinum. Acetobacter xylinum is nature’s most prolific cellulose producing vinegar bacterium. One typical cell is capable of converting up to 108 glucose molecules per hour into cellulose. If for example a million cells could be packed into one big liquid droplet and if each of those single cell factories produced 108 glucose molecules per hour, then the product would appear to be made before your eyes. A single Acetobacter cell has a linear row of pores from which glucan chain polymer aggregates are spun. Up to one hundred of these pores would be capable of producing a composite cable of glucan polymers resulting in a ribbon. The carrying out of time-lapse analysis has shown that individual Acetobacter cells carry out a wide variety of activities. Each cell acts as a nano-spinneret which produces a bundle of sub-microscopic fibrils. The entangled mesh of these fibrils produces a gelatinous membrane known as a pellicle. The end product is a membrane of pure cellulose.</p><p>What could it be used for? Microbial cellulose has two great properties. It has great strength in the never dried state and is capable of holding hundreds of times its own weight in water. It has great absorptivity and strength. At the moment relatively few industries using microbial cellulose are organized. The following is a list of representative product areas and products which could potentially be developed. Healthfood Industries. Microbial cellulose is very suitable for use in healthfood products due to its gel- like properties and its complete indigestibility in the human intestinal tract. Examples of products it is used in are Nata, the Philippine dessert and Kombucha, the fermented health drink. Audio components. The first audio speaker diaphragms using microbial cellulose were developed by the Sony Corporation. The excellent dimensional stability of microbial cellulose gives rise to a sound transducing membrane which maintains high sonic velocity over a wide frequency range. This makes it the best material to meet the high standards for optimum sound transduction. The costs at the moment are quite high but as the production techniques become more advanced these should start to come down and the products become more affordable. Wound care products. Microbial cellulose was first tested as a wound care products in the early 1980’s by Johnson & Johnson. Since then a company called Biolfill Industias have continued research into the properties of microbial cellulose and have a limited range of woundcare products out on the market which are based on microbial cellulose. There has also been research into developing moulded objects of microbial cellulose directly during the fermentation process. These moulded objects could include non-woven, shaped objects, suitable for use in medicine such as artificial arteries, skin, vessels etc. Paper and Paper Products. Microbial cellulose has been investigated for use as a binder in papers. This is because of its consisting of very small clusters of cellulose microfibrils. This property greatly adds to the strength and durability of the pulp when it is integrated into paper. Companies such as Mitsubishi Paper Mills in Japan are investing a lot of resources in developing microbial cellulose for paper products. Future prospects for Microbial cellulose. The future development of Microbial cellulose will require fermentation scale up so that the conversion to a large scale fermentation technology will deliver microbial cellulose onto the market at a competitive rate. There is a requirement for more money to be invested in research and development so that fermentation techniques can be honed and refined. In a world where deforestation, global industrialization and climate change are major issues it is time to look to the future and start investing more resources in developing an alternative source for the world’s most abundant and heavily used biopolymer. </p><p>5.0 Cellulose and the Environment</p><p>There are many different ways that cellulose interacts with the environment. As cellulose is the most abundant naturally occurring biopolymer on the planet it is only natural that it will play a major role in the earth’s environment. Since the issue of converting cellulosic biomass into biofuel has already been dealt with previously in this report it will not be focused on in this section. It just remains to be said that the development of technology and treatment processes to develop biomass into alternate energy sources is something which is of great importance to the world, especially with the impending crisis in fossil fuel supplies and the deterioration in our environment caused by the burning of fossil fuels. The following are a number of ways cellulose effects the environment. i) Cellulose and the carbon cycle. Fig 2.0</p><p>One can imagine all the cellulose on the earth as a giant carbon “sink”. Carbon incorporation into cellulose remains there for quite a substantial period of time, can be up to thousands of years. The increase in carbon dioxide levels in the atmosphere is one of the main reasons for the gradual heating up of the earth’s surface. Carbon dioxide is a “greenhouse gas” i.e. it traps heat from the suns radiation as it tries to escape into space. One long term alternative to this problem is to try and reverse this problem by increasing photosynthesis, which will result in higher quantities of CO2 being trapped. The harvesting of massive acreages of trees is neither helping the management of the photosynthetic potential nor maintaining a global “sink” for CO2. The continued deforestation of very substantial areas combined with the loss of land with the potential for growth to processes such as desertification, industrialisation, and urbanisation. The scales are becoming increasingly unbalanced. Cellulose in the oceans. This is an area which is often overlooked. The majority of cellulose found in the oceans is produced by either unicellular plankton or algae.</p><p>They use the same photosynthetic fixation method for obtaining CO2 as do land plants. It is believed that these organisms are Natures biggest resource for cellulose production. Life in the oceans is dependent on photosynthetic microbes; they are the foundation stone for all life that exists there. How we can improve the environment by improving our utilisation of waste cellulose and developing more products based on waste cellulose as alternatives to wood and plastic products. The environment could be improved by constantly trying to increase the percentage of waste cellulose which is recycled and reused instead of it being sent to landfills. People around the world should be encouraged to be economical in their use of paper and to try and use recycled paper. With the increased use of computers and the internet around the world there could in the future be a viable alternative to using paper for newspapers, books etc. This would not happen for many years but already small steps are being taken with the amount of people with access to the internet increasing every year. In 2002 544million people had access to the internet globally; in 2004 729 million people had access. Although the majority of these people are located in the more developed parts of the world there will hopefully be an upsurge in internet access in the less developed regions in the future. There could also be more use made of recovered waste paper for alternative products such as pulp mouldings and building boards. Currently only 1-3 % of recovered waste paper is used for such alternative products. There is a lot of scope for developing products such as furniture, panels, moulded ceilings etc. In fact during the Industrial revolution there was a lot more use made of waste cellulose in the form of “Papier Mache”. As well as it being utilised for the products already mentioned there were also more unconventional uses such as a church built in Norway in 1793 which consisted entirely of Papier Mache blocks ,it lasted for 37 years. There was also the manufacture of an entire village by George Bielefeld in the mid nineteenth century which managed to survive two feet of flooding. Papier Mache was widely used until near the end of the nineteenth century when it started to go out of fashion. Its decline was more related to its design rather than any structural limitations. The discovery of electro-plating was also another nail in Papier Mache’s coffin as it provided a cheap alternative for household articles with electro-plated nickel silver. Although there were some developments in the twentieth century such as pulpware (used for domestic items and safety hats), there was a general decline in use as plastics superceded other products. With the major technological advances in the 20th century and the recent emergence of innovative techniques like the production of microbial cellulose there is now an opportunity to utilise an alternative material which is more environmentally friendly than modern plastic and wood products. The use of toxic chemicals is less necessary in processes used to develop products from waste cellulose than those used to develop plastics and products from freshly cut down trees i.e. paper, furniture, cardboard etc. Cellulose as well as being very important to the natural world is also very important to humans. It benefits us in the most basic ways like clothing and writing, and many other ways like food additives, adhesives, explosive inhibitors. The emphasis should now be on increasing efforts to reduce, reuse and recycle cellulose based products (as well as others). It is also up to governments and private industries to invest more heavily in microcellulose and cellulose based structural products. Another alternative would be to utilise the millions of acres of forest which are currently under water behind dams all over the world. These trees were never cleared before flooding took place and are very well preserved in the fresh water. The trees can be safely harvested using remote control robotic technology as developed by companies such as Aquatic cellulose International Corporation. This development would only be a part of the solution. We cannot go on exploiting our resources of cellulose at the current rate, with the expansion of the world’s population and the increasing industrialisation taking place in many regions of the world the situation is now becoming critical. There must be more emphasis placed on alternatives to our current uses of cellulose and the development of more environmentally friendly production methods. </p>
Details
-
File Typepdf
-
Upload Time-
-
Content LanguagesEnglish
-
Upload UserAnonymous/Not logged-in
-
File Pages26 Page
-
File Size-