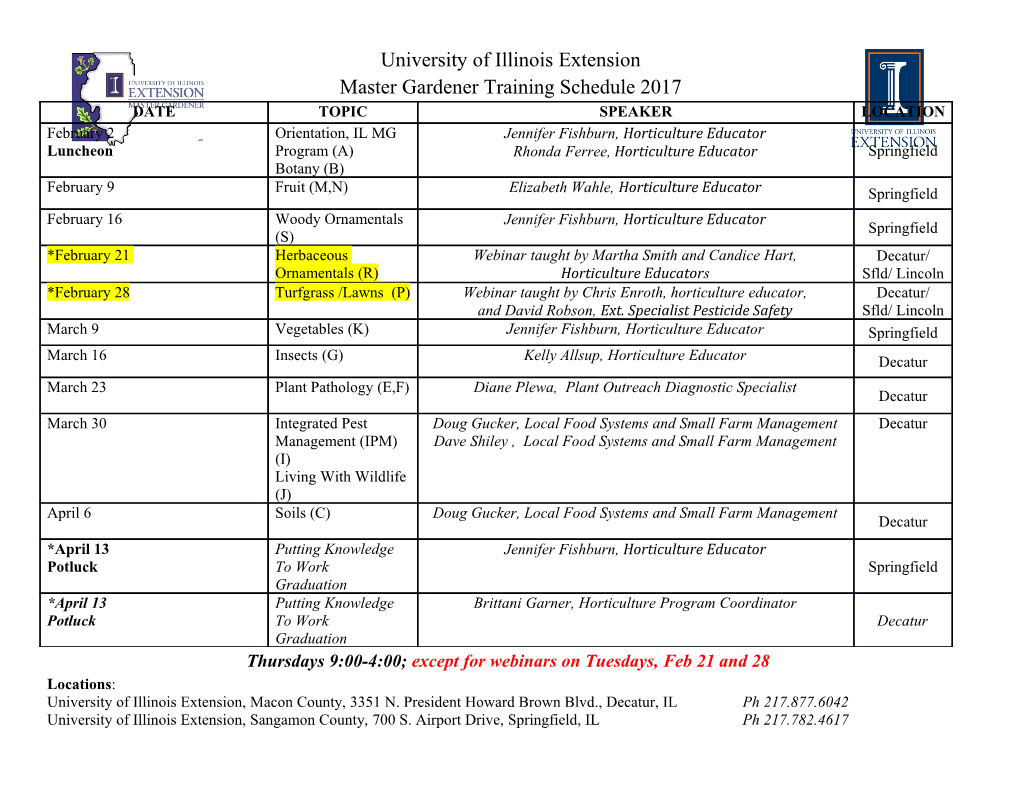
Ultrasonic Sealing in Packaging: Theory & Principles, Equipment & Solutions Presentation Outline • Packaging trends • Ultrasonic Technology Overview • Polymer Welding Characteristics • The Ultrasonic advantage • Package types • Ultrasonic Sealing Processes in Packaging − Continuous processing − Plunge processing − Form, Fill, & Seal − Application solutions Packaging market trends • Sustainability • Recycling/reusing materials • Reduction in Energy used in production (Carbon footprint) • Supply chain transparency • Sourcing • Safety/traceability • End-of life cycle • New Barrier/coating technologies • Paper/board- easily recyclable when combined with new barrier technologies • Lightweight packaging • Reduced costs • Environmental sustainability • “Frustration-free” packaging • Build customer loyalty by offering easy to open packs that can be opened and resealed quickly Ultrasonic Technology Overview Ultrasonic Theory Electrical Energy Mechanical Vibrations 2000 X 20 kHz Power Supply 50/60 Hz Converter Booster Horn Hysteresis Heating Mechanical oscillations about an equilibrium point create molecular stress and heat Ultrasonic System Converter Output Amplitude 30 µm : 15 kHz 20 µm : 20 kHz 15 µm : 30 kHz 8 µm : 40 kHz Horn Amplitude Amplitude: the peak-to-peak displacement of the face of the horn while ultrasonics are applied Amplitude Nodal area Stack Amplitude Converter X Silver Booster X High gain horn = 120 20 microns Gain = 2 Gain = 3 microns Converter X Gold Booster X Unity gain horn = 30 20 microns Gain = 1.5 Gain = 1 microns Amplitude Reference Guide • Most films used in packaging have a semi-crystalline component in the structure. They typically require more amplitude for welding than amorphous materials. 20kHz 30kHz 40kHz Nylon 70 – 120m 56 – 96m 42 - 72m PET 80 – 120m 64 - 96m 48 - 72m PE 90 - 120m 72 - 96m 54 - 72m PP 90 - 120m 72 - 96m 54 - 72m Ultrasonic Theory Energy = Power X Time Force X Velocity Force can be varied Factors of by changing: velocity are: Pressure Downspeed Frequency AmplitudeAmplitude Balun technology • Patented Multi Converter technology • Ultrasonic horn driven by two or more converters • The converters are being driven in parallel and in phase, thereby providing a horn transmitting greater power than the same horn driven by a single converter. • Higher power per linear inch = Faster cycle rates • Available in 20, 30, & 40-kHz • Reduced size and mass • Balanced RF load distribution • Superior amplitude uniformity Balun technology – Ultrasonic Stacks 20kHz – 19” long 30kHz – 9” long 40kHz – 6” long Polymer welding characteristics Polymer Welding Characteristics • Melt Characteristics (Tg, Tm) • Stiffness (high Modulus of Elasticity) • Polymer structure: Amorphous Semi-Crystalline Specific Heat vs. Temperature Amorphous materials: • Gradual softening & melting Semi-crystalline materials: • Narrow melting peak indicates sudden melting and rapid solidification. • Height of peak indicates the amount of energy required to melt. Weldability of Films • Thermoplastics material can be cast, extruded or blown into a film, generally under 0.010” thick. • Factors Influencing Weldability: − Film thickness − Density − Thermoplastic type Weldability of Laminate / Coated Materials • Coated materials: − Films can covered with a layer of thermoplastic, such as polyethylene, BOPP/EOPP, EVOH, nylon. − Base material need not be thermoplastic, such as coated cardboard or paper. • Factors Influencing Weldability: − Coating material and thickness − Substrate − Sealing layer thickness Joint Design • Rigid Plastics: – Energy director designed into parts themselves • Textiles and Films – Energy directing patterns on the face of the horn, anvil, rotary drum or stitching wheel. The Ultrasonic Advantage The Ultrasonic Advantage Performance: Seals thru contaminants - reduce leakers The Ultrasonic Advantage Energy: Low energy consumption compared to thermal process Energy only applied during process cycle No warm up required Sustainability: Up to 75% reduction in carbon footprint over thermal systems Narrow seal area requires less material Process compatible with PLA and other bio-plastics The Ultrasonic Advantage Performance: No residual heating of package contents Reduced tool clean up = less downtime High cycle rates ( > 110 bags per minute) Increased Process control The Ultrasonic Advantage- Material Savings • Based on film cost of $0.25/ft • Package length of 10” • Cycle time: 100 ft per/ min Sonic seal • Seal area: heat .250” • Seal area: sonic .080“ (2mm) • Utilization:16 hrs/day 250 Heat seal days / yr. • Efficiency: 80% • Savings of 544,000 ft/yr Material savings : $ 136,000 / year The Ultrasonic Advantage- Increased Process Control Parameter Adjustment Increase: • Pressure/Downspeed • Energy • Amplitude Under-welded? Inspect Process Initial Setup Part Validation Over-welded? Decrease: • Pressure • Energy • Amplitude − Amplitude Profile? Additional Control Options Primary Control • Acts as primary control of weld cycle Primary Weld Mode • Can select one Weld Mode Optional Control Capabilities • Terminates ultrasonics once a certain condition is met Secondary Control (e.g. Weld Time Limit is exceeded) Mode −Hold Time is initiated to complete weld cycle • Aborts the weld cycle immediately Cycle Aborts 1. Missing Part: 2. Ground Detect • After weld cycle is complete, triggers alarm indicating parameter is out-of-range Suspect and Reject • Suspect Limit: If weld result may be acceptable, part Limits should be subjected to further evaluation • Reject Limit: Indicates an unacceptable part Types of packages Types of Flexible Packages Flat Bottom / Stand Pillow Bags Stick Packs Up Pouches Types of Rigid Packages Coffee/ Yogurt Cup Tea pods Types of Rigid Packages Gable top coated- Clamshells paperboard cartons Ultrasonic sealing processes Ultrasonic Sealing Processes in Packaging • Continuous mode − Clamshell sealer − Radial actuator • Plunge mode − Standard bench top welder (clamshell, stand up pouches, yogurt cups) − Tube sealer (stand up pouches) − Vertical or horizontal form & seal (various bag types) Continuous Processing – Clamshell Sealing • Easily welds various size packages, including tamper evident • Speeds up to 110 ft/min Continuous Processing- 30-kHz Radial Actuator • RMX-30 Radial Actuator Plunge processing - Clamshell Sealing Plunge processing- Pouch Sealer Plunge processing- Tube / Pouch Sealer Date code in the seal area Vertical Form, Fill and Seal System Vertical Fill Form Sealing Branson USA Lab machine- continuous motion; designed for the snack food market; vertical & horizontal ultrasonic seals VFFS - Ultrasonic End Sealing VFFS – Ultrasonic vertical sealing Machine Formats Single Lane: Has a single lane tube form to shape the pouch at each cycle Suitable for many different sized pouches Most common configuration Multi-Lane: Has multiple lanes of tube to form multiple pouches at each cycle Commonly known as “stick-pack” machines. Used for small packets such as sugar, salt, and condiment packets Application Solution- Rigid container (clamshell) sealing Product/Application Name: Clamshell Market Segment: Packaging Material: PET Requirements: Structural seal Joint Design: None Technology: Ultrasonic Process Parameters: In production Tooling: 30kHz Region: North America Contact: Hans H. Neisser Comments/Advantages: Reliable sealing of one or both edges of a clamshell Application Solution- 4-liter Dairy/Vegetable product Product/Application Name: Restaurant-size pouches Market Segment: Packaging Material: Laminate Poly-films Requirements: Hermetic Seal Joint Design: None Technology: Ultrasonic, plunge, w/20-kHz Balun horn Process Parameters: In production Tooling: 15.5”L Titanium horn w/slot Region: North America Contact: Hans H. Neisser Comments/Advantages: Ability to seal through product contamination in seal area Application Solution- Aroma valves Product/Application Name: Aroma valve- coffee packages Market Segment: Packaging Material: Laminate Poly-films Requirements: Hermetic Seal Joint Design: None Technology: Ultrasonic, plunge Process Parameters: In production Tooling: 20kHz circular high-gain horn Region: North America Contact: Hans H. Neisser Comments/Advantages: Reliable strong seal that does not damage valve function Application Solution- Spout welding Product/Application Name: Spout weld Market Segment: Packaging Material: Coated Paperboard Requirements: Hermetic Seal Joint Design: None Technology: Ultrasonic, plunge Process Parameters: In production Tooling: 20kHz booster horn Region: North America Contact: Hans H. Neisser Comments/Advantages: Reliable, strong seal Application Solution- Cement Bag welding Product/Application Name: Cement “Valve” bags Market Segment: Packaging Material: Poly-coated paper Requirements: Hermetic Seal Joint Design: None Technology: Ultrasonic Process Parameters: In production Tooling: 20kHz rectangular bar horn Region: North America Contact: Hans H. Neisser Comments/Advantages: Reliable strong seal that does not open due to rough handling Questions.
Details
-
File Typepdf
-
Upload Time-
-
Content LanguagesEnglish
-
Upload UserAnonymous/Not logged-in
-
File Pages50 Page
-
File Size-