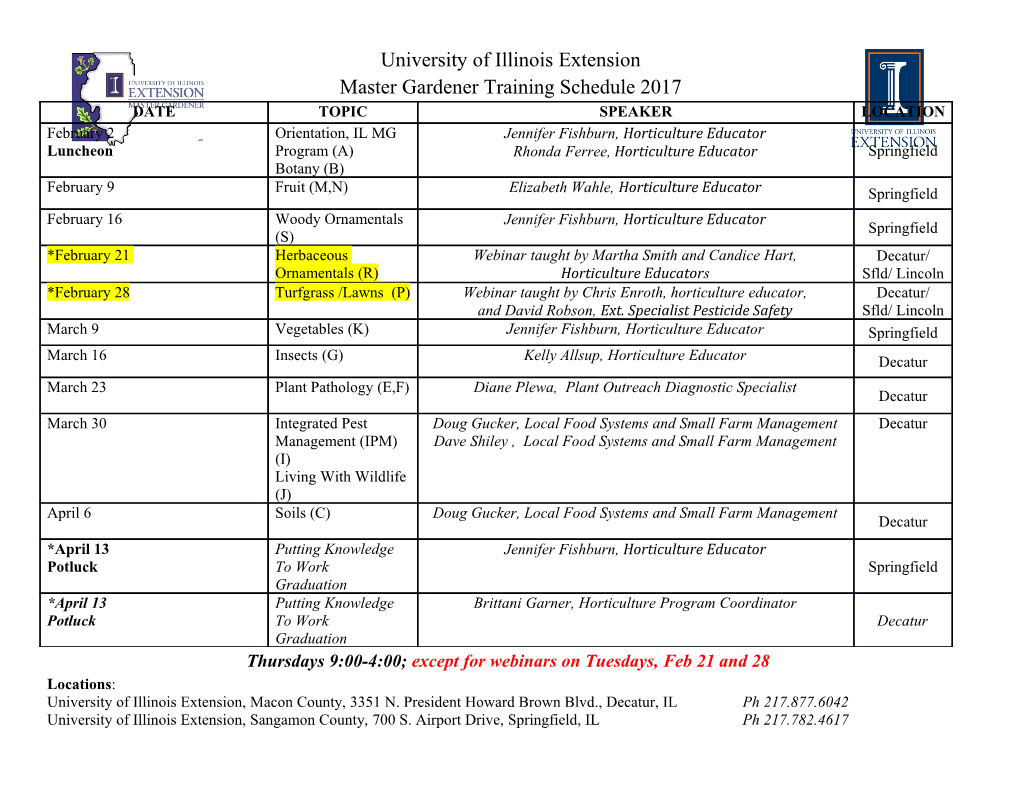
<p> Contents</p><p>1. Examples of risk assessment forms</p><p> a. General Risk assessment form </p><p> b. Risk assessment report form example </p><p> c. Contractors’ risk assessment example for confined spaces NIB</p><p> d. Contractors’ risk assessment example for work on fragile roofs NIB</p><p> e. Machinery risk assessment example NIB</p><p>2. Job safety analysis form</p><p>3. Essential elements of a permit-to-work form</p><p>4. An example of a set of COSHH assessment forms</p><p> a. COSHH 1 - DETAILS OF SUBSTANCES USED OR STORED</p><p> b. COSHH 2 - ASSESSMENT OF A SUBSTANCE </p><p>5. Example of a workstation self-assessment checklist (DSE)</p><p>6. Example of a noise assessment record form</p><p>7. Example of a workplace inspection report form</p><p>8. Workplace inspection checklist</p><p>9. Accident/incident report form</p><p>10. Manual handling of loads assessment checklist</p><p>11. Manual handling risk assessment </p><p>12. Example fire safety maintenance checklist NIB</p><p>13. Example fire risk assessment record of significant findings</p><p>14. Construction inspection report form</p><p>1 1 – (a) General Risk assessment form</p><p>General Health and Safety Risk Assessment No Example 1 Firm/Company Department Contact Name Nature of Business Telephone No</p><p>Principal Hazards 1 2 3 4 5 Persons at Risk</p><p>Main Legal Requirements 1 2 3 4 5 Significant Risks Consequences 1 2 3 4 5 Existing Control Measures 1 2 3 4 5 Residual Risk, i.e. after controls are in place. Severity Likelihood Residual risk</p><p>Information relevant HSE and trade publications</p><p>Comments from Line Manager Comments from Risk Assessor</p><p>Signed Date Signed Date Review Date</p><p>2 (b) Risk Assessment Report Form Name of Company: Date of Assessment: Name of Assessor: Date of Review: Persons Initial Risk Action by Action by Done Hazards Risks Existing Controls Additional Controls affected Level whom? when?</p><p>3 (c) Contractors’ risk assessment example for confined spaces</p><p>INITIAL RISK ASSESSMENT Work in Confined Spaces SIGNIFICANT HAZARDS Low Medium High 1. Poisoning from toxic gases 2. Asphyxiation - lack of oxygen 3. Explosion 4. Fire 5. Excessive heat 6. Drowning 7. 8. ACTION ALREADY TAKEN TO REDUCE THE RISKS:</p><p>Compliance with: H S E Guidance Note - Entry into Confined Spaces Local Authority/client safety standards, e.g. on sewer entry. Entry into Confined Spaces Regulations 1997 The Construction (Design and Management) Regulations 2007 Dangerous Substances and Explosive Atmospheres Regulations. Planning: Eliminate need for entry or use of hazardous materials by selection of alternative methods of work or materials. Assessment of ventilation available and possible local exhaust ventilation requirements, potential presence of hazardous gases/atmosphere, process by-products, need for improved hygiene/welfare facility. Physical: Documented entry system will apply, with a Permit to Work. Adequate ventilation will be present or arranged. Detection equipment will be present before entry to check on levels of oxygen and presence of toxic or explosive substances. The area will be tested before entry and continually during the presence of persons in the confined space. Breathing apparatus or airlines will be provided if local ventilation is not possible. Where no breathing apparatus is assessed as being required, emergency BA and rescue harnesses will be provided. Rescue equipment including lifting equipment, resuscitation facilities safety lines and harnesses will be provided. A communication system with those in confined space will be established. Air will not be sweetened with pure oxygen. Precautions for safe use of any plant or heavier-than-air gases in the confined space must be established before entry. Necessary P PE and hygiene facilities will be provided for those entering sewers. Managerial/Supervisory: The management role is to decide on nature of the confined space and to put a safe system into operation, including checking the above. Flood potential and isolations must be checked. Training: Full training required for all entering and managing confined spaces. Rescue surface party to be trained, including first aid and operation of testing equipment. All operatives must be certified as trained and supervisory staff trained to the same standard. Risk Re-Assessment Date...... Site Manager’s Comments:</p><p>4 (d) Contractors’ risk assessment example for Work on Fragile Roofs – example 4</p><p>INITIAL RISK ASSESSMENT Work on Fragile Roofs SIGNIFICANT HAZARDS Low Medium High 1. Falls of persons through materials 2. Access across fragile material 3. 4. 5. 6. 7. 8. ACTION ALREADY TAKEN TO REDUCE THE RISKS:</p><p>Compliance with: Lifting Operations & Lifting Equipment Regulations. (L O L E R) Provision and Use of Work Equipment Regulations. (P U W E R) Work at Height Regulations 2005 H S E Guidance Booklet HS (G) 33 - Safety in Roof work Construction (Design and Management) Regulations 2007. Planning: Fragile materials will be identified before work begins. In each case, an assessment of risk will be made to provide a safe system of work taking account the work to be done, access/egress requirements and protection of the area beneath the work area. Physical: Suitable means of access will be provided, such as roof ladder, crawling boards, scaffolding, and staging. Where access is possible alongside fragile materials such as roof lights, covers will be provided or the fragile material will be fenced off, catch nets will be provided as appropriate. Barriers and signs will be provided so as to isolate the area below fragile materials while work is in progress. No person is permitted to walk upon suspected fragile materials for any purpose, including access and surveying. Managerial/Supervisory: The role of management is to define a safe work method prior to commencement of work, and to arrange for provision of suitable access equipment and trained personnel as required by the safe system devised. Managers must check risk assessments and method statements supplied by subcontractors and others, including the self- employed, to ensure that the proposed work method is safe. Training: All operatives must be given specific instructions on the system of work to be used in each case. Selection may be required of operatives who have experience of the work and are physically fit. Risk Re-Assessment Date...... Site Manager’s Comments:</p><p>5 (e) Machinery Risk Assessment - example 5 Machine No Model Manufacturer Risk Assessment no</p><p>Model No Other Department ID</p><p>Hazard Yes No Hazard Yes No Hazards Trapping Electrocution Impact Pressure</p><p>Contact Hot/Cold</p><p>Entanglement Fire</p><p>Ejection Other</p><p>Who might be Operatives Cleaners Maintenance Visitors Others harmed? Guarding Fixed Guards Interlocked Adjustable Fixed Distance Movable guards guard Guards Adequate Fitted to machine Fitted to machine Fitted to machine Enclosure of drives and motors Closed to run Readily Securely fixed adjustable Securely fixed in Design OK with Prevent Prevents access to position positive switches Ejection danger zone & robust Tool required to Safe to open Maintained OK Tool to remove remove Maintained OK Maintained OK Controls /Warnings/ Instructions /Training Controls Instruction/ Area Training Clearly Shrouded start Warning signs Lighting OK identified Function clear Warning device Signs clear Stability OK</p><p>Easy to use Isolator nearby Safety sheet OK Ventilation OK</p><p>Emergency stop Isolator SOP available LEV needed lockable Machine stops Permit required Training OK Access operators ok Safe at stop Seating needed Access maintenan ce Action Required</p><p>6 SEVERITY FREQUENCY RISIDUAL RISK (S x F)</p><p>2- Job safety analysis form</p><p>JOB SAFETY ANALYSIS Job Date</p><p>Department Carried out by</p><p>Description of job</p><p>Legal requirements and guidance</p><p>Task steps Hazards Consequence Severity Risk Controls /Likelihood L X S</p><p>Safe system of work</p><p>Job Instruction</p><p>Training requirements</p><p>Review date</p><p>7 3 - Essential elements of a permit-to-work form</p><p>1 Permit Title 2 Permit No 3 Job Title</p><p>4 Plant identification</p><p>5 Description of Work</p><p>6 Hazard Identification</p><p>7 Precautions necessary 7 Signatures</p><p>8 Protective Equipment</p><p>9 Authorization 10 Acceptance 11 Extension/Shift handover 12 Hand back 12 Cancellation</p><p>8 4 - An example of a set of COSHH assessment forms</p><p>COSHH 1 - DETAILS OF SUBSTANCES USED OR STORED</p><p>Name of Manager: ………………………………………………………………………………… Name of Department/Area;………………………………………………………………………..</p><p>SUBSTANCE DETAILS 1. Information from the label Trade name:…………………………………………………………………………………… Manufacturer's name:……………………………………………………………………….. Names of any chemical constituents listed:………………………………………………. …………………………………………………………………………………………………. Hazard marking - whether corrosive, irritant, harmful, toxic, very toxic…………………. ………………………………………………………………………………………………….. RISKS Phrases noted on label (e.g. Harmful in contact with skin) …………………………………………...... Safety Phrases noted on labels (e.g. avoid contact with skin) …………………………………………………………………………………………………...... PRECAUTIONS noted on label (e.g. Use in well ventilated area)……………………… ....…………………………………………………………………………………………….... …………………………………………………………………………………………………. ………………………………………………………………………………………………….</p><p>2. Have you got a Health & Safety Data Sheet for this product? YES/NO</p><p>DETAILS OF USE</p><p>3. What it is used for?...... …………………………………………………………………………………………………… 4. By whom?...... 5. How often?...... 6. Where?...... 7. What CONTROL measures (precautions) are used? (E.g. local ventilation, goggles, respirator, protective gloves. etc.)…………………………………………………………….. …………………………………………………………………………………………..... ……………………………………………………………………………………………. …………………………………………………………………………………….……... 8. Is it ABSOLUTELY ESSENTIAL to keep/use this substance? YES/NO</p><p>9. Can it be DISPOSED OF NOW? YES/NO</p><p>9 COSHH 2 - ASSESSMENT OF A SUBSTANCE </p><p>1. Name of substance:…………………………………………………………………………...... 2. The process or description of job where the substance is used…………………………...... ……………………………………………………………………………………………………...... 3. Location of the process where substance is used…………………………………………..... 4. Health & safety information on substance: a) Hazards to health:…………………………………………………………………………...... ……………………………………………………………………………………………………...... ……………….……………………………………………………………………………………. b) Precautions required:………….……………………………………………………………..... …….………….……………………………………………………………………………………...... ………….…………………………………………………………………………………………….... …….………….……………………………………………………………………………………...... …….………….……………………………………………………………………………………...... 5. Number of persons exposed:…………………………………………………………………..... 6. Frequency and duration of exposure:…………………………………………………………... 7. Control measures that are in use:……………………………………………………………..... ……………………………………………………………………………………………………….... ……………………………………………………………………………………………………….... ……………………………………………………………………………………………………….... ……………………………………………………………………………………………………….... 8. The assessment, an evaluation of the risks to health:……………………………………….. ……………………………………………………………………………………………………….... ……………………………………………………………………………………………………….... ……………………………………………………………………………………………………….... ………………………………………………………………………………………………………... 9. Details of steps to be taken to reduce the exposure:………………………………………... ………………………………………………………………………………………………………... ………………………………………………………………………………………………………... ………………………………………………………………………………………………………... ………………………………………………………………………………………………………...</p><p>10. Action to be taken by (name) :…………………………………………(Date):…………….... 11. Date of next assessment/review: ...... 12. Name and position of person making this assessment: ...... 13. Date of assessment: ...... 5 - Example of a Workstation Self Assessment Checklist </p><p>Name Department: Date:</p><p>The completion of this checklist will enable you to carry out a self-assessment of your own workstation. Your views are essential in order to enable us to achieve our objective of ensuring your comfort and safety at work. Please circle the answer that best describes your opinion, for each of the questions listed. The form should be returned to…………………………as soon as it has been completed.</p><p>Environment 1. Lighting Describe the lighting at your usual workstation. About right Too bright Too dark Do you get distracting reflections on your screen? Never Sometimes Constantly What control do you have over local lighting? Full control Some control No control</p><p>2. Temperature and humidity</p><p>At your workstation, is it usually: Comfortable Too warm Too cold? Is the air around your workstation: Comfortable Too dry?</p><p>3. Noise</p><p>Are you distracted by noise from work equipment? Never Occasionally Constantly 4. Space</p><p>Describe the amount of space around your workstation. Adequate Inadequate</p><p>Furniture</p><p>5. Chair Can you adjust the height of the seat? Yes / No Can you adjust the height and angle of the backrest? Yes / No Is the chair stable? Yes / No Does it allow movement? Yes / No Record (continued)</p><p>Furniture (continued)</p><p>Chair (continued) Is the chair in a good state of repair? Yes / No If your chair has arms, do they get in the way? Yes / No</p><p>6. Desk Is the desk surface large enough to allow you to place all your equipment where you want it? Yes / No Is the height of the desk suitable? Yes / Too high / Too low Does the desk have a matt surface (non-reflectant)? Yes / No</p><p>7. Footrest</p><p>If you cannot place your feet flat on the floor whilst keying, has a footrest been supplied? Yes / No</p><p>8. Document holder If it would be of benefit to use a document holder, has one been supplied? Yes / No</p><p>If you have a document holder, is it adjustable to suit your needs? Yes / No</p><p>Display Screen Equipment</p><p>9. Display screen Can you easily adjust the brightness and the contrast between the characters on screen and the background? Yes / No Does the screen tilt and swivel freely? Yes / No Is the screen image stable and free from flicker? Yes / No Is the screen at a height, which is comfortable for you? Yes / No</p><p>10. Keyboard Is the keyboard separate from the screen? Yes / No Record (continued)</p><p>Display Screen Equipment (continued)</p><p>Keyboard (continued)</p><p>Can you raise and lower the keyboard height? Yes / No Can you easily see the symbols on the keys? Yes / No Is there enough space to rest your hands in front of the keyboard? Yes / No</p><p>11. Software</p><p>Do you understand how to use the software? Yes / No</p><p>12. Training</p><p>Have you been trained in the use of your workstation? Yes / No Have you been trained in the use of software? Yes / No If you were to have a problem relating to display screen work, would you know the correct procedures to follow? Yes / No</p><p>Do you understand the arrangements for eye and eyesight tests? Yes / No</p><p>Any other comments?</p><p>13 6 - Example of a Noise Assessment Record Form</p><p>Name of Department: Date of Survey: Lower Exposure Action Level: Upper Action Level: Peak Pressure: 80 dBA daily or weekly 85 dBA daily or weekly 135 dB(C)/137dB(C) Number of Noise Level Daily LEP'd Peak Pressure Workplace Persons (Leq) Exposure Comments dB(A) dB(C) Exposed dB(A) Period</p><p>General Comments:</p><p>Instrument Used: Date of Last Calibration: </p><p>Signature: Position: Date:</p><p>14 7 - Example of a Workplace Inspection Report Form</p><p>Workplace Inspection Cover Sheet</p><p>Name of Company/Organization Work area covered by this Inspection Activity carried out in work place Person carrying out Date of inspection Inspection (PLEASE PRINT)</p><p>(See Appendix 7.3 Inspection Checklist and Appendix 5.1 for hazard checklist)</p><p>Observations Priority/ Actions to be taken (if Time Scale List hazards, unsafe practices and good risk any) Immediate practices (H,M,L) List all immediate and 1 week etc longer-term actions required</p><p>15 8 - Workplace Inspection Checklist PREMISES 1 Work at Height Ladders/step Right equipment for the job? ladders Level base? Correct angle? Secured at top and bottom? Equipment in good condition? Regularly inspected </p><p>Working Suitable for the task platforms/ Properly erected? Good access? temporary Maintained and inspected scaffolds Use of mobile Suitable for task? elevating work Operators properly trained? platforms Properly maintained </p><p>2 Access Access ways Adequate for people, machinery and work in progress? Unobstructed? Properly marked? Stairs in good condition? Handrails provided? Housekeeping Tidy, clean, well organized? Flooring Even and in good condition? Working Non-slippery? Environment Comfort /health Crowded? Too hot/cold? Ventilation? Humidity? Dusty? Lighting? </p><p>Cleaning Slip risk controlled? Hygienic conditions Noise Normal conversation possible? Noise assessment needed/not needed? Noise areas designated? Ergonomics Tasks require uncomfortable postures or actions? Frequent repetitive actions accompanying muscular strain? Visual display Workstation assessments needed/not needed units Chairs adjustable/comfortable/maintained properly? Cables properly controlled? Lighting OK? No glare?</p><p>16 4 Welfare Toilets /Washing Washing and toilet facilities satisfactory? Kept clean, with soap and towels/ Adequate changing facilities </p><p>Eating facilities Clean and adequate/Means of heating food? </p><p>For pregnant or nursing mothers Rest room Kept clean? </p><p>Suitably placed and provisioned? Appointed person? First aid Trained first aider? Correct signs and notices? Eye wash bottles as necessary? </p><p>5 Services Electrical Portable equipment tested? equipment Leads tidy not damaged? Fixed installation inspected Gas Equipment serviced annually? </p><p>Water Hot and cold water provided? Drinking water provided? </p><p>6 Fire precautions Fire In place? Full? Correct type? extinguishers Maintenance contract? </p><p>Fire instructions Posted up? Not defaced or damaged? </p><p>Fire alarms Fitted and tested regularly? </p><p>Means of Adequate for the numbers involved? escape/ Fire Unobstructed? exits Easily opened? </p><p>Properly signed? </p><p>Means of Adequate for the numbers involved? escape/ Fire Unobstructed? exits Easily opened? </p><p>Properly signed? </p><p>17 PLANT AND SUBSTANCES 7 Work Lifting Thoroughly examined? Equipment equipment Properly maintained? Slings etc properly maintained? Operators properly trained? Pressure Written schemes for inspection? systems Safe working pressure marked? Properly maintained? Sharps Safety knives used? Knives/needles/glass properly used/disposed of? Vibration Any vibration problems with hand held machinery or with whole body from vehicle seats etc? Tools and Right tool for the job? equipment In good condition? Manual Moving excessive weight? handling Assessments carried out? Using correct technique? Could it be eliminated or reduced? 8 Manual & Mechanical Forklifts and other trucks properly Mechanical handling maintained? Handling Drivers authorized and properly trained? Passengers only where specifically intended with suitable seat? 9 Vehicles On site Speeding limits? Following correct route? Properly serviced? Drivers authorized </p><p>Road risks Suitable vehicles used? No use of mobile phones when driving? Properly serviced? Schedules managed properly?</p><p>18 10 Dangerous Flammable Stored properly? substances liquids and Used properly/minimum quantities in gases workplace? Sources of ignition? Correct signs used? </p><p>11 Hazardous Chemicals COSHH assessments OK? substances Exposures adequately controlled? Data sheet information available? Spillage procedure available? Properly stored and separated as necessary? Properly disposed of? </p><p>Exhaust Suitable and sufficient? ventilation Properly maintained? Inspected regularly? </p><p>PROCEDURES Risk Carried out? General and fire? 12 assessments Suitable and sufficient? </p><p>13 Safe systems Provided as necessary? of Kept up to date/ Work Followed </p><p>14 Used for high risk maintenance? Procedure OK? Permits to work Properly followed? </p><p>15 Personal Correct type? Protective Worn correctly? Good condition? Equipment 16 Contractors Is their competence checked thoroughly? Are there control rules and procedures? Are they followed? </p><p>17 Notices, Signs Employers' Notice displayed? In date? and Posters liability insurance Displayed? Health and Safety law poster Safety Signs Correct type of sign used/ Signs in place and maintained?</p><p>19 PEOPLE 18 Health Specific surveillance required by law? surveillance Stress or fatigue? </p><p>19 People's Are behaviour audits carried out? behaviour Is behaviour considered in the safety programme? </p><p>20 Training and Suitable and sufficient? supervision Induction training? Refresher training? 21 Appropriate Is there a system for authorizing people for authorized certain special tasks like permits to work, dangerous machinery, entry into confined person spaces? </p><p>22 Violence Any violence likely in workplace? Is it controlled? Are there policies in place 23 Especially at Young persons Employed? risk Special risk assessments? categories New or Employed? expectant Special risk assessments? mothers </p><p>20 9 - ACCIDENT/INCIDENT REPORT</p><p>INJURED PERSON: ……………………………….Date of Accident: ...../.... /20 Time……….am/pm</p><p>POSITION: …………………………………………Place of Accident: …………………………………….</p><p>DEPARTMENT: …………………………………… Details of Injury: ……………………………………....</p><p>Investigation carried out by: ………………………..……………………………………...... </p><p>Position: ……………………….. Estimated Absence: …………………………………...... </p><p>Brief details of Accident (A detailed report together with diagrams, photographs and any witness statements should be attached where necessary. Please complete all details requested overleaf.)</p><p>Immediate Causes Underlying or Root Causes</p><p>Conclusions (How can we prevent this kind of incident/accident occurring again?)</p><p>Action to be taken: …………………………………Completion Date:.... /...... /20</p><p>Please ensure that an accident investigation and report is completed and forwarded to Personnel within 48 hours of the accident occurring.</p><p>Remember that accidents involving major injuries or dangerous occurrences have to be notified immediately by telephone to the local authority.</p><p>Signature of Manager making Report: ……………………………Copies: Personnel Manager Health & Safety Manager Date:...../...... /20 Payroll Controller</p><p>INJURED PERSON: Surname …………………...... Forenames ………………..…………...... Male/Female Home address ………………………………………………………...... Age…………</p><p>Consent to share this information with Safety Representatives</p><p>Signature of Injured Person...... Date...... /...... /.....20... Employee Agency Temp Contractor Visitor Youth Trainee (Tick one box)</p><p>21 Kind of Accident Indicate what kind of accident led to the injury or condition (tick one box)</p><p>Contact with moving Injured whilst handling Drowning or Contact with electricity or machinery or material lifting or asphyxiation an electrical discharge being machined 1 5 9 13</p><p>Struck by moving Slip, trip or fall on Exposure to or Injured by an animal including flying, or same level contact with harmful falling object 2 6 10 14</p><p>Struck by moving Fall from height Exposure to fire Violence vehicle 3 indicate approx. 7 11 15 Distance of fall………mtrs Struck against something fixed Trapped by something Exposure to an Other kind of or stationary 4 collapsing or overturning 8 explosion 12 accident 16</p><p>Detail any machinery, chemicals, tools etc. involved</p><p>Accident first reported to : Name …………………………………….. Position & Dept……………………………………………………………………………………………..</p><p>First Aid/medical attention by: First Aider Name ……………………Dept …………………………. Doctor Name …………………...... Medical centre ……………………Hospital……………………….</p><p>WITNESSES Name Position & Dept Statement obtained (yes/no) Attach all statements taken …………………………… .………………………………………… …………………… yes/no …………………………… .………………………………………… …………………… yes/no …………………………… .………………………………………… …………………… yes/no …………………………… .………………………………………… …………………… yes/no</p><p>For Office use only</p><p>If relevant: Date reported to Enforcing Authority a) by telephone ..../….../20 b) by internet ..../...... /20 c) on form F2508 …./…../20</p><p>Date reported to Company Insurers …../…../20</p><p>22 Were the Recommendations Effective? Yes/No If No say what further action should be taken.</p><p>23 10 - Manual Handling of Loads: Assessment Manual Handling of Loads: Assessment Checklist</p><p>Section A - Preliminary Task description: Is an Assessment needed? Factors beyond the limits of the guidelines? (i.e. is there a potential risk of injury, and are the factors beyond the limits of the guidelines?)</p><p>Yes / No If ‘YES ‘continue. If ‘NO’ the assessment need go no further. Tasks covered by this assessment Diagrams and other information: (detailed description):</p><p>Locations:</p><p>People involved:</p><p>Date of assessment:</p><p>Section B – See separate sheet for detailed analysis Section C – Overall assessment of the risk of injury? Low / Medium / High Section D – Remedial action needed: Remedial steps that should be taken, in priority order: a b c d e f g h Date by which action should be taken: Date for reassessment: Assessor’s name: Signature: 11 - Manual Handling Risk Assessment Manual Handling Risk Assessment Employee checklist</p><p>Task Description Employees ID No</p><p>Risk Factors A. Task Characteristics Yes/No Risk Level Current Controls H M L 1. Loads held away from trunk? 2. Twisting? 3. Stooping? 4. Reaching upwards? 5. Extensive vertical movements? 6. Long carrying distances?</p><p>24 7. Strenuous pushing or pulling? 8. Unpredictable movements of loads? 9. Repetitive handling operations? 10. Insufficient periods of rest/recovery? 11. High work rate imposed? B. load characteristics 1. Heavy? 2. Bulky? 3. Difficult to grasp? 4. Unstable/unpredictable? 5. Harmful (sharp/hot)? C. Work environment characteristics 1. Postural constraints? 2. Floor suitability? 3. Even surface? 4. Thermal/humidity suitability? 5. Lighting suitability? D. Individual characteristics 1. Unusual capability required? 2. Hazard to those with health problems? 3. Hazard to pregnant workers? 4. Special information/training required?</p><p>Any further action needed? Yes/No Details:</p><p>25 12- Example fire safety maintenance checklist</p><p>A fire safety maintenance checklist can be used as a means of supporting your fire safety policy. This example list is not intended to be comprehensive and should not be used as a substitute for carrying out a fire risk assessment. You can modify the example where necessary, to fit your premises and may need to incorporate the recommendations of manufacturers and installers of the fire safety equipment/systems that you may have installed in your premises. Any ticks in the grey boxes should result in further investigation and appropriate action as necessary. In larger and more complex premises you may need to seek the assistance of a competent person to carry out some of the checks.</p><p>Source: Department for Communities and Local Government Fire Safety Guides</p><p>Yes No N/A Comments Daily Checks (not normally recorded) Escape Routes Can all fire exits be opened immediately and easily? Are fire doors clear of obstructions? Are escape routes clear? Fire warning systems Is the indicator panel showing ‘normal’? Are whistles, gongs or air horns in place? Escape lighting Are luminaries and exit signs in good condition and undamaged? Is emergency lighting and sign lighting working correctly? Firefighting equipment Are all fire extinguishers in place? Are fire extinguishers clearly visible? Are vehicles blocking fire hydrants or access to them? Weekly checks Escape routes Do all emergency fastening devices to fire exits (push bars and pads, etc.) work correctly?</p><p>26 Yes No N/A Comments Are external routes clear and safe? </p><p>Weekly checks continued Fire warning systems Does testing a manual call point send a signal to the indicator panel? (Disconnect the link to the receiving centre or tell them you are doing a test.) Did the alarm system work correctly when tested? Did staff and other people hear the fire alarm? Did any linked fire protection systems operate correctly? (e.g. magnetic door holder released, smoke curtains drop) Do all visual alarms and/or vibrating alarms and pagers (as applicable) work? Do voice alarm systems work correctly? Was the message understood? Escape lighting Are charging indicators (if fitted) visible? Firefighting equipment Is all equipment in good condition? Additional items from manufacturer’s recommendations. Monthly checks Escape routes Do all electronic release mechanisms on escape doors work correctly? Do they ‘fail safe’ in the open position? Do all automatic opening doors on escape routes ‘fail safe’ in the open position? Are fire door seals and self-closing devices in good condition? Do all roller shutters provided for fire compartmentation work correctly? Are external escape stairs safe? Do all internal self-closing fire doors work correctly? Escape lighting Do all luminaries and exit signs function correctly when tested? Have all emergency generators been tested? (Normally run for one hour.) Fire fighting equipment Is the pressure in ‘stored pressure’ fire extinguishers correct? Additional items from manufacturer’s recommendations.</p><p>27 Yes No N/A Comments</p><p>Three-monthly checks</p><p>General Are any emergency water tanks/ponds at their normal capacity? Are vehicles blocking fire hydrants or access to them? Additional items from manufacturer’s recommendations. Six-monthly checks General Has any fire fighting or emergency evacuation lift been tested by a competent person? Has any sprinkler system been tested by a competent person? Have the release and closing mechanisms of any fire-resisting compartment doors and shutters been tested by a competent person? Fire warning system Has the system been checked by a competent person? Escape lighting Do all luminaries operate on test for one third of their rated value? </p><p>Additional items from manufacturer’s recommendations. Annual checks Escape routes Do all self-closing fire doors fit correctly? Is escape route compartmentation in good repair? Escape lighting Do all luminaries operate on test for their full rated duration? Has the system been checked by a competent person? Fire fighting equipment Has all fire fighting equipment been checked by a competent person? Miscellaneous Has any dry/wet rising fire main been tested by a competent person? </p><p>Has the smoke and heat ventilation system been tested by a competent person?</p><p>28 Yes No N/A Comments</p><p>Miscellaneous continued Has external access for the fire service been checked for ongoing availability? Have any fire-fighters’ switches been tested? Has the fire hydrant bypass flow valve control been tested by a competent person? Are any necessary fire engine direction signs in place? </p><p>29 13- Example Fire risk assessment record of significant findings Risk Assessment – Record of significant findings Fire Risk Assessment – Record of significant findings Risk assessment for Assessment undertaken by Company Date</p><p>Address Completed by </p><p>Signature</p><p>Sheet number Floor/area Use</p><p>Step 1 - Identify fire hazards Sources of ignition Sources of fuel Sources of oxygen</p><p>Step 2 – People at risk</p><p>Step 3 – Evaluate, remove, reduce and protect from risk (3.1) Evaluate the risk of the fire occurring</p><p>(3.2) Evaluate the risk to people from a fire starting in the premises</p><p>(3.3) Remove and reduce the hazards that may cause a fire</p><p>(3.4) Remove and reduce the risks to people from a fire</p><p>Assessment review Assessment review date Completed by Signature</p><p>Review outcome (where substantial changes have occurred a new record sheet should be used)</p><p>(1) The risk assessment record of significant findings should refer to other plans, records or other documents as necessary. (2) The information in this record should assist you to develop an emergency plan; coordinate measures with other ‘responsible persons’ in the building; and to inform and train staff and inform other relevant persons.</p><p>30 14 - Construction Inspection Report Form</p><p>Construction Inspection Report 1. Name and address of person for whom inspection was carried out.</p><p>2. Site address. 3. Date and time of inspection.</p><p>4. Location and description of place of work or work equipment inspected.</p><p>5. Matters which give rise to any health and safety risks.</p><p>6. Can work be carried out safely? Yes / No 7. If not, name of person informed. 8. Details of any other action taken as a result of matters identified in 5 above.</p><p>9. Details of any further action considered necessary.</p><p>10. Name and position of person making the report. 11. Date and time report handed over. 12. Name and position of person receiving report. 94 I</p><p>Safety at work</p><p>31</p>
Details
-
File Typepdf
-
Upload Time-
-
Content LanguagesEnglish
-
Upload UserAnonymous/Not logged-in
-
File Pages31 Page
-
File Size-