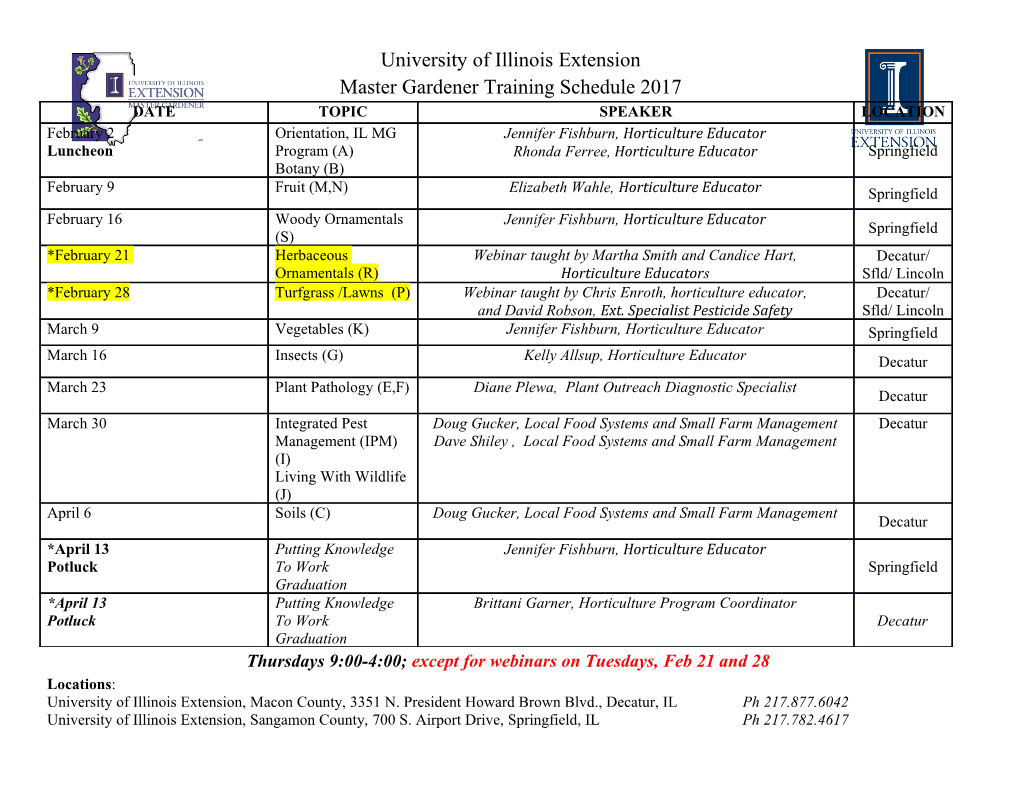
<p>Safe Work Practices Milling Division</p><p>Task: Division: Start up Machine Milling</p><p>Personal Protective Equipment Required: Hard Hats Safety Vest Hearing Protection (Ear Plugs) Steel Toe Footwear</p><p>Task/Activity Potential Hazard Recommended Procedures</p><p>1. Climb ladder to top of Fall off grinder 1. Maintain 3 point machine contact</p><p>2. Unlock and lift hood of Back strain 1. Proper lifting machine procedures</p><p>3. Check fluid levels None</p><p>4. Start machine Possible movement of 1.Warn of machine start machine verbally</p><p>Task: Division: Pre-work Service Milling Ie greasing, warm up of machine</p><p>Task/Activity Potential Hazard Recommended Procedures</p><p>1. Raise machine to clear cutter People in close proximity 1. verbal warning from the ground of machine - crushing 2. install fall supports 2. Engaging cutter People in close proximity – 1.Verbal warning & wait crushing for response</p><p>3. Greasing cutter and drive Person getting caught in 1. Ensure that end gates cutter are full down position</p><p>4. Starting & warming People in line of discharge 1.Lower conveyor to lowest position conveyors People caught up in conveyor 2.Verbally announce start up</p><p>5. Greasing conveyor Person being caught in 1. Run conveyor at conveyor slowest speed Pinch point 2. No loose clothing 3. Have operator within eyesight & position to shut down conveyor if required 4. Greaser to use extreme caution 5. Install anti swing device</p><p>Task: Division: Walking Machine to & from Work Zone Milling</p><p>Task/Activity Potential Hazard Recommended Procedures</p><p>1. Start moving machine Machine coming into 1. Operator does visual contact with objects or inspection from both sides people of operator station. 2. Ground man positions himself with clear view of front & rear of machine 3.Operator makes visual contact with ground man 4.Ground man gives operator OK to move</p><p>2. Walking machine Machine running over 1. Visual inspection of objects or people in blind area spots of operator</p><p> a) forward 1.Ground man position front of machine in eye sight of operator 2.Have TCPs’ where appropriate</p><p> b) backward 1.Ground man position rear of machine in eye sight of operator 2.Have TCPs’ where appropriate</p><p>Task: Division: Putting Machine into Operation Milling</p><p>Task/Activity Potential Hazard Recommended Procedures</p><p>1. Positioning machine for work Possible interference with 1. Operator & ground other personnel and man make visual contact equipment in work zone with all personnel in proximity of machine and physically indicate intention </p><p>2. Lowering machine into cut Possibility of machine 1. Operator to apply lurching backward without brake and have hand control ready on emergency stop shut down switch. 2. Ground man to ensure no one is immediately in the back of machine</p><p>Dust 1.Operator to ensure water system is on 2. Consult the ECP1</p><p>3.Backing in trucks Running over property or 1.Operator and ground personnel man to ensure immediate area behind truck is clear of people & objects 2.Back up alarm must be working</p><p>4.Turning on conveyors Flying debris from 1.Operator to make sure conveyor no one is standing under or close to the conveyor</p><p>1 Added point Task: Division: Working in Traffic Milling</p><p>Task/Activity Potential Hazard Recommended Procedures</p><p>1. Setting up work zone Possible traffic confusion 1. Always have proper signage, delineation & controls</p><p>2.Milling in close proximity of Restricted space for 1.Have TCP monitor traffic ground man setting depth traffic of machine 2.Do adjustments facing traffic</p><p>Contact of cars with 1.Ensure delineators are machine sensors set clear of sensors 2.Position TCP at rear corner of machine</p><p>3.Checking cut Possible contact with 1.Check cut back of traffic machine standing inside cut</p><p>4.Bringing trucks to and from Traffic following trucks into 1.Trucks to have 4 ways machine closure on when entering work zone</p><p>Traffic unaware of truck 1.TCPs’ to accommodate entering travel lane enter & exit of trucks</p><p>Task: Division: Backing up Machine Milling</p><p>Task/Activity Potential Hazard Recommended Procedures</p><p>1. Back up procedure Large blind spot for 1. Ground man to cover operator immediately blind spot for operator behind machine.</p><p>Possible contact with 1. Both operator and objects or personnel ground man to follow during back up strict back up procedure 2. Back up alarms must be functioning</p><p>Task: Division: Backing up Trucks Milling</p><p>Task/Activity Potential Hazard Recommended Procedures</p><p>1. Backing up trucks Running over property or 1. Truck driver to have personnel eye contact with all personnel working around work area 2. Trucks not to move until piles are shovelled and personnel signals trucker to move 3. have conversation with trucker to make sure rules are understood 4. make sure that back up alarms and lights are in working order</p><p>Task: Division: Watering machine – Stationary Milling</p><p>Task/Activity Potential Hazard Recommended Procedures</p><p>1. Truck pulling into closure Traffic following water 1. Water truck stop & beside the stationary machine truck into the closure. sound horn to alert TCP before proceeding into closure. Ensure warning lights are on</p><p>Workers unaware of water 1.Sound horn again once truck in closure to alert crew & equipment </p><p>2. Watering machine Restricted space between 1. Water truck driver to machine & water truck stay back of machine until operator has stopped machine, applied brake and indicates for driver to pull forward 3. Transferring water - Improper connection 1.Both machine & truck in stationary procedure resulting in park position before uncontrolled water spray operation to begin 2.All crew to visually give OK of connections made and valves open before water pump is started 3.Water truck driver monitor water levels</p><p>Task: Division: Watering machine on the Move Milling</p><p>Task/Activity Potential Hazard Recommended Procedures</p><p>1. Stop milling machine None</p><p>2. Pull water truck next to Running over property or 1. Truck driver to have machine personnel eye contact with all personnel working around work area</p><p>3. Attach hose to machine from None truck</p><p>4. Turn pump on None</p><p>5. Truck and machine both Crushing between truck 1. Do not go between move ahead and machine machine and truck while in motion.</p><p>6. Disconnect hose None</p><p>7. Pull truck away from machine Running over property or 1. Truck driver to have personnel eye contact with all personnel working around work area</p><p>Task: Division: Grease Machine Milling Task/Activity Potential Hazard Recommended Procedures</p><p>1. Put in leg stands Crushing due to hydraulic 1. Put in leg stands failure</p><p>2.Turn on conveyors Materials coming out of 1.Visually check below conveyor conveyor 2.Vocally warn of start up</p><p>Person getting caught in 1.Vocally warn of start up conveyor</p><p>Pinch points 1.No one on deck while greasing</p><p>3.Turn on drum Person being caught in 1.Vocally warn of start up drum</p><p>4.Put grease in grease nipples as None directed by greasing schedule</p><p>Task: Division: Changing Teeth Milling</p><p>Task/Activity Potential Hazard Recommended Procedures</p><p>1. Raise machine Crushing due to hydraulic 1. Put in leg stands failure</p><p>2. Raise door to cutter housing Crushing due to Hydraulic 1. Make sure door is Failure proper height and above safety catch</p><p>3. Remove and replace teeth Flying debris 1. Wear safety goggles with air gun or hand tool</p><p>Hitting hand with air tool 1. Wear gloves or hammer.</p><p>4. Lower cutter housing door Crushing 1. Visual inspection and Verbal warning. Task: Division: Securing Machine after Work Milling</p><p>Task/Activity Potential Hazard Recommended Procedures</p><p>1. Parking machine Property damage sinking 1. Scout suitable parking in soft ground poses area before proceeding to possible risk to public & area traffic 2. Lower machine to lowest possible position and position conveyors appropriately</p><p>2.Securing machine Possible starting and 1. Delineate and lock out operating by unqualified power source. people 2.Lock all control panels</p><p>Possible contamination of 1.Visually inspect area due to oil or fuel machine for leaks & mechanical failures</p><p>Task: Division: Fire Hydrant Use – Opening Milling</p><p>Task/Activity Potential Hazard Recommended Procedures</p><p>1. Pre - opening of a hydrant If you stand in front of 1. Secure proper permits the hydrant and the cap & documentation is not secure, it will Visually & physically come off with significant 2. pressure behind it. This inspect hydrant for could cause serious damage/defects injury/death. 3. If damage is noted, If these procedures are notify your supervisor not done in the proper order, water will be informing him of propelled with such a location & hydrant great force that could I.D.# He will make the violently project items/people. call to the city 4. Stand behind hydrant 5. Ensure that hydrant valve is shut off 6. Ensure all caps are secure 7. Install back flow preventer and hydrant hook up 8. Slightly open back flow valves before opening service valve. This allows the valve to seat properly</p><p>2. Slowly open valve on Prevents water hammer hydrant noting number of & damage to the mains. turns required to fully open The counting is used as a double check system to ensure when closing the hydrant you have made the correct amount of turns.</p><p>3. Purge valve This reduces potential contamination to water tank on machine</p><p>4. Close service valve before Avoids potential connecting to machine trapping water pressure in plastic service hose</p><p>5. Re-open service valve after connection to machine is made</p><p>Task: Division: Fire Hydrant Use – Shut down Milling</p><p>Task/Activity Potential Hazard Recommended Procedures</p><p>1. Close hydrant hook up valves approximately 9/10th</p><p>2. Slowly shut down hydrant Must be done slow to prevent water hammer & damage to the mains 3. Ensure same number of If the numbers don’t 1. Listen for a sucking turns are used to close as match, the hydrant isn’t noise when opening fully closed</p><p>4. Fully open all valves on hydrant hook up</p><p>5. Allow a drain down time of This ensures the stem of 15 minutes the hydrant will be void of water, preventing freeze up and damage to the hydrant</p><p>Task: Division: Milling adjacent to or in close Milling proximity to a drop off or unstable ground</p><p>Task/Activity Potential Hazard Recommended Procedures</p><p>1. Before moving machine 1. If the crew feel that the into area, milling crew do a ground is unstable and walkthrough of area to cannot withstand the evaluate conditions and weight of the machine, it potential hazards. can exercise its right to refuse. 2. Contact their immediate supervisor right away. </p><p>3. Position machine a safe Unstable ground gives 1. Do NOT drive or back distance from potential away; may cause machine into position close hazard, lower legs and set machine to tip or roll to edge of pavement with over depth BEFORE proceeding legs fully extended. forward with the milling 2. Where appropriate, function operator should crab machine to be able to run the front track farther away from edge of pavement</p><p>4. Ground man must monitor 1. Ground man should avoid any changes in ground positioning themselves on conditions so as to be able the side of the potential to warn operator of any hazard within the length of such changes the machine Vehicle Breakdowns and Accidents</p><p>1. If a vehicle breaks down, operators must get the vehicle off and away from the travelled portion of the road if possible (this particularly applies to emergency vehicle routes on the project site). If they can't, then they must: Activate vehicle emergency flashers If visibility is poor because of fog, rain, hill, curve, dusk, etc., set out flares or flashers supplied with the vehicle Set flares or flashers 32 m (100 ft) behind and 32 m (100 ft) in front of the vehicle. (Do not set out flares if you are well off the road.)</p><p>2. Immediately report all Company vehicles breakdowns to head office.</p><p>3. Report accidents involving Company vehicles as described in Section 8 - Incidents. Give all the details possible, such as width of roads, length of skids, presence of traffic signs, vision obstructions, names and addresses of persons involved and witnesses. In case of an accident the operator must: Pull off the road, if possible, to avoid obstructing traffic Place warning reflectors on the road as necessary Render first aid to any person who may be injured Report the accident to his supervisor as soon as possible Refrain from entering into any argument or dispute with the driver of the other vehicle, pedestrians or bystanders Make no admission of liability or offer any settlement of claim Record license plate numbers and driver's license numbers of any other involved persons (including witnesses) Make arrangements with your supervisor to report the accident to the necessary authorities</p><p>Boosting a Battery</p><p>Always wear safety goggles to protect yourself from acid and fragments in case of an explosion. It’s a good idea to store safety goggles with your jumper cables. Check to see if the battery is really dead, or if the terminals and clamps might just be corroded. Restore correct fluid levels to the battery. If you are dealing with the more recent sealed type batteries, it is not always possible to restore these fluid levels. If this is the case, the battery should be replaced. Make sure the battery is not frozen. Trying to jump a frozen battery could result in an explosion. The electrical systems of both vehicles must be the same voltage and both must have a negative ground. Mismatched batteries are less likely than they were 20 years ago but six-volt batteries are still in use today. Using a 12 volt battery to boost a six volt battery could cause the six volt battery to explode. Part the vehicles close together, but not touching. Put both vehicles in “park” or in “neutral”, with parking brakes set. Turn off the engine, and any electrical accessories including interior lights on both vehicles. Remove the battery vent caps to allow any previously built up gas to escape. Then cover the holes with a damp rag or replace the caps. Do not lean over the battery at any time. Connect the red clamps to the positive “+” posts of each battery. Reverse connection causes a battery explosion hazard. Connect one black clamp to the negative “-“ terminal of the good battery. Connect the other black clamp to a good ground; a clean, unpainted spot on the engine, frame or body of the disabled vehicle, placing it as far away as possible from the battery. This will prevent sparks from occurring in the vicinity of any explosive gases. When connecting the clamps, do not allow them to touch any other metal. This would not only cause a spark which could trigger an explosion, but it could destroy parts of the vehicle’s electrical and computer system. Start the vehicle with the good battery. Start the disabled vehicle. Remove the cables in reverse order. Detach the “-“cable first from the disabled car’s frame. Then take the “-“of the good car’s negative terminal. Remove the disabled cars “+” cable. Then remove the live car’s “-“connection.</p><p>Other Tips Avoid any sparks or flames. NO SMOKING.</p>
Details
-
File Typepdf
-
Upload Time-
-
Content LanguagesEnglish
-
Upload UserAnonymous/Not logged-in
-
File Pages12 Page
-
File Size-