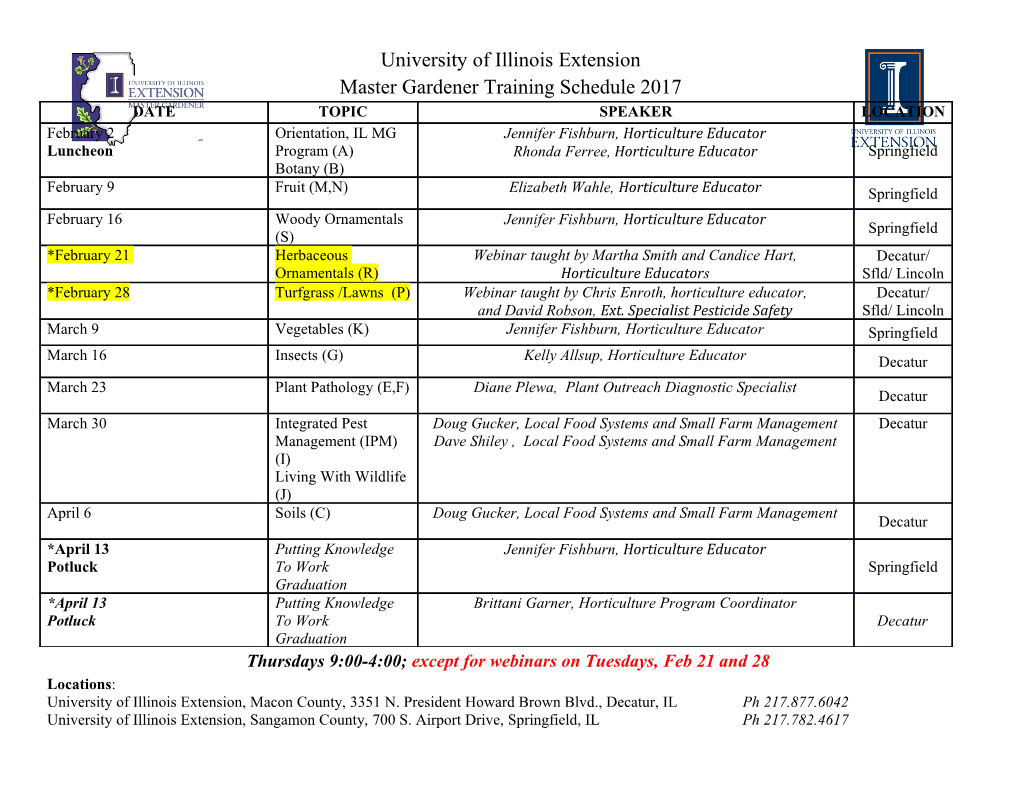
<p>Metric #1 – Power efficiency 1. Prototype power supply as standalone unit. 2. Supply power using EE lab power supplies with current measurement. 3. Connect resistive load equivalent to the expected draw of the system. 4. Measure output power (voltage^2 / load). 5. Output / Input power = efficiency PASS = 80% efficiency FAIL = less than 80% efficiency</p><p>Metric #2 – Input Voltage Range Using EE Lab Adjustable output power supply: 1. Adjust output voltage between 4.6 – 5.8V in 0.2V increments 2. Measure output voltage on all regulators. 3. Connect test load, verify proper output voltage. PASS = All voltage rails maintain voltage within min/max range of IC with most demanding voltage input accuracy. FAIL = One or more voltage rails fail to regulate voltage to within range of most demanding IC spec</p><p>Metric #3 – Operating time 1. Charge power source (Ni-MH battery pack). 2. Run system at full capacity for 30 minutes. 3. Monitor system I/O through PC serial connection to IOC. 4. Shutdown after 30 minutes. 5. Recharge power source with micro-controller charger (Aero Lab) 6. Note the recharge energy in mA-hours. 7. Recharge energy less than full capacity by good margin? PASS = After 30 minutes, no more than 2/3 battery capacity is used FAIL = After 30 minutes, more than 2/3 battery capacity is used</p><p>Metric #4 – Provides hardware / method for connecting to chassis PASS = Product provides mounting holes to accept mounting hardware. Holes are pre-drilled, or a surface is designated for drilling for mounts. Mount is appropriate for attachment to flat surface. FAIL = No mounting points are supplied, and there are no proper places to drill and attach the product to a flat surface.</p><p>Metric #5 – System Weight Weigh final product. PASS = product less than 3 lbs in weight FAIL = product more than 3 lbs in weight</p><p>Metric #6 – Power and Programming ports are externally accessible PASS = System power and programming connectors can be accessed without removing system from MAV aircraft FAIL = System must be removed from MAV aircraft to access power or programming ports</p><p>Metric #7 – Complies with (ESD) HBM MIL-Std 883 Check component ESD ratings PASS = All external connections are ESD protected. FAIL = Any external connection is not ESD protected</p><p>Metric #8 – Has an easily accessible power switch PASS = System can be turned off without removal from MAV aircraft FAIL = System must be removed in order to turn off</p><p>Metric #9 – Compatible Simulink Blocks 1. Create a Simulink model that uses all required Simulink blocks 2. Build model using tool chain PASS = model successfully builds and runs on CCP FAIL = model can not be successfully built, compiled, or executed on CCP</p><p>Metric #10 – I/O Throughput 1. Connect UAV set of peripherals to IOB 2. Configure IOC to communicate with UAV peripherals and to sample at maximum speed PASS = Measured sample rate is greater than 1000 samples per second FAIL = Measured sample rate is less than 1000 samples per second</p><p>Metric #11 – Control Processing Bandwidth 1. Connect IOC to CCP 2. Receive a Simulink control system from Dr. Kolodziej (1000Hz time-step) 3. Run control system on CCP 4. Bandwidth = # of iterations achieved per second PASS = Bandwidth is greater than or equal to 1000 iterations per second FAIL = Bandwidth is less than 1000 iterations per second</p><p>Metric #12 – Non-volatile storage for control code 1. Upload large (larger than 50KB) compiled Simulink control code to NV storage 2. Boot up CCP, load control code PASS = CCP boots and runs control code FAIL = CCP is unable to boot and run control code</p><p>Metric #13 – On board filtering capabilities 1. Enable filtering cores (LP, HP, BP) on IOC 2. Configure programmable filters on IOC 3. Log pre-processed & post-processed data to SD card 4. Process pre-processed data using MATLAB PASS = post-processed data matches results from MATLAB FAIL = post-processed data does not match results from MATLAB Metric #14 – Architecture bit length/accuracy PASS = Sensor data is represented by at least 16 bits FAIL = Sensor data is represented by less than 16 bits</p><p>Metric #15 – Parallel execution of independent subsystems 1. Disconnect IOC from CCP 2. Attempt to log sensor data using the IOC 3. Attempt to communicate with CCP and determine if it is in a ‘ready’ state PASS = Steps 2 & 3 are accomplished FAIL = Either steps 2 or 3 cannot be accomplished</p><p>Metric #16 – I/O interface types, numbers, and pin-outs are configurable 1. Connect MAV peripheral set to IOC and attempt to acquire data 2. Connect a different peripheral set to IOC and attempt to acquire data PASS = All of the above steps are successful FAIL = Any of the above steps fail</p><p>Metric #17 – All source data is freely available and documented 1. Download a snapshot of the repository 2. Check that every codebase is compliable 3. Check that code meets documentation standard 4. Check for schematics and layouts of every board 5. Record a 3rd party's ability to recreate project solely from the snapshot PASS = All of the above steps are successful FAIL = Any of the above steps fail</p><p>Metric #18 – I/O peripherals connect externally PASS = Control Platform can be removed from vehicle without removing connected peripherals FAIL = Removal of the Control Platform requires the removal of one or more vehicle peripherals</p><p>Metric #19 – Physical Size 1. Assemble and package system 2. Attach battery 3. Measure total volume. PASS = Volume is less than or equal to the specification FAIL = Volume is greater than the specification</p><p>Metric #20 – Provide interface to telemetry 1. Connect IOC to CCP 2. Create dummy telemetry device 3. Read sensor values through telemetry interface with dummy device 4. Send test commands to IOC and CCP, record whether they respond correctly 5. Determine if there is enough bandwidth to record every sensor and control system value PASS = All of the above steps are successful FAIL = Any of the above steps fail Metric #21 – Non-volatile removable storage for logged data 1. Configure IOC to log data to removable SD card 2. Remove SD card and insert into a standard card reader for a PC PASS = Logged data is readable directly from PC FAIL = Logged data is not able to be read</p><p>Metric #22 – Voltage ranges of analog sensor inputs Check ADC spec sheet for maximum ratings for analog inputs PASS = Supports 1.8 to 4.5 volt inputs FAIL = Requirements exceed maximum ratings</p><p>Metric #23 – Number of analog channels PASS = Design supports the ability to connect and read at least 3 analog inputs FAIL = Less than 3 analog inputs can be used at a time</p><p>Metric #24 – Protocols Supported Connect MAV digital peripherals to IOC PASS = Communication to peripherals is possible FAIL = Communication to peripherals is not possible</p><p>Metric #25 – Number of Concurrent Digital Peripherals 1. Connect IOB to CCP 2. Connect IMU and GPS to IOB 3. Log data to SD card 4. Log data on CCP side PASS = CCP and IOC log the same data FAIL = Either CCP or IOC fail to receive data</p><p>Metric #26 – External Payload interface specification and interface exists PASS = Electronic payload may connect using one or more of the following: SPI, I2C, UART, PARALLEL I/O, PWM FAIL = There is no possibility of communicating with an external electronic system in payload</p><p>Metric #27 – Peripherals are easily detached or disconnected 1. Assemble and package system. 2. Measure with a stop watch: i. Time taken to attach peripherals. ii. Time taken to detach peripherals. PASS = Measured time taken is less than 30 seconds per peripheral FAIL = Measured time taken is greater than 30 seconds per peripheral</p><p>Metric #28 – Debug information is accessible 1. Configure program to output additional debug values 2. Connect system to USB interface 3. Attempt to read debug values PASS = Debug values are available using USB interface FAIL = Debug values are inaccessible</p><p>Metric #29 – Manual Override 1. Connect control platform to UAV IOB 2. Connect R/C Receiver to UAV IOB 3. Load CCP with test control code to fluctuate servo outputs 4. Flip override switch on R/C transmitter. 5. Move R/C transmitter controls. PASS = Upon override switch, control servos stop responding to control code. R/C transmitter has complete control over servo motion. FAIL = Upon override switch, control servos fail to follow R/C transmitter inputs without interference or sporadic behavior. </p>
Details
-
File Typepdf
-
Upload Time-
-
Content LanguagesEnglish
-
Upload UserAnonymous/Not logged-in
-
File Pages5 Page
-
File Size-