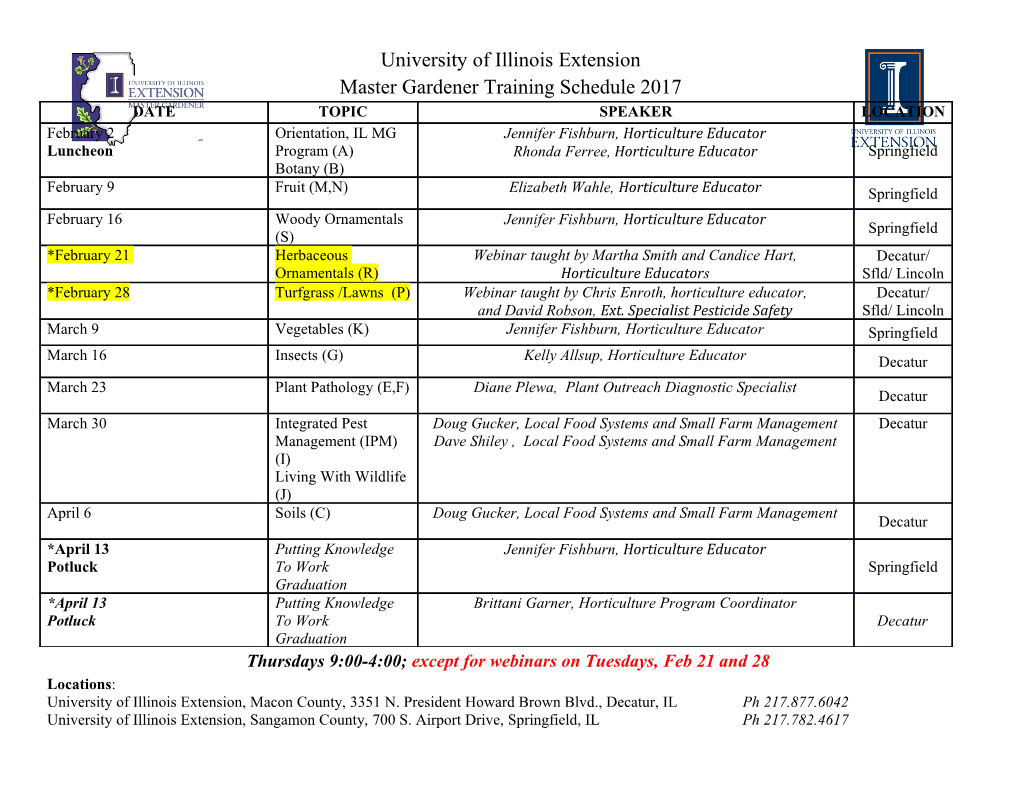
PNNL-19002 Prepared for the U.S. Nuclear Regulatory Commission under an Interagency Agreement with the U.S. Department of Energy Contract DE-AC05-76RL01830 Grain Structure Identification and Casting Parameters of Austenitic Stainless Steel (CASS) Piping CO Ruud AA Diaz MT Anderson November 2009 DI SCLA IM ER This report was prepared as an account of work sponsored by an agency of the United States Government. Neither the United States Government nor any agency thereof, nor Battelle Me morial Institute, nor any of their employees, makes any warranty, express or implied, or assumes any legal liability or responsibility ror t he accuracy, completeness, or useruln ess or any inrormation, apparatus, product, or process disclosed, or represents that its use would not inrringe prh'ately owned rights. Reference herein to any specific commercial product, process, or service by trade name, trademark, manufacturer, or otherwise does not necessarily constitute or imply its endorsement, recommendation, or favoring by the United States Gove rn me nt or any agency thereof, or Battelle Memorial Institute. The views and opinions of authors expressed herein do not necessarily state or reflect those of the Uni ted States Government or any agency thereof PAC IFIC NORTH WEST NATIONAL LABORATORY operated by BATfELLE for the UN ITED STATES DEPARTMENT OF ENERG Y under Contracf DE-ACO>76RLO/830 @T his document was printed on recycled paper. (912003) Grain Structure Identification and Casting Parameters for Austenitic Stainless Steel (CASS) Piping CO Ruud AA Diaz MT Anderson November 2009 Prepared for U.S. Nuclear Regulatory Commission under an Interagency Agreement with the U.S. Department of Energy Contract DE-AC05-76RL01830 Pacific Northwest National Laboratory Richland, Washington 99352 Summary Inservice inspection (ISI) requirements dictate that piping welds in the primary pressure boundary of light-water reactors (LWRs) be subject to a volumetric examination based on the rules contained within the American Society of Mechanical Engineers (ASME) Boiler and Pressure Vessel Code, Section XI. The volumetric examination may be either radiographic (RT) or ultrasonic (UT) but local radiation environments and access limitations may prevent the use of the former. The purpose of the inspection is the reliable detection and accurate sizing of any service-induced degradation and/or material flaws introduced during fabrication. However, the characteristic and varied metallurgical grain structures of cast austenitic stainless steel (CASS) piping, including statically cast stainless steel (SCSS) and centrifugally cast stainless steel (CCSS), introduce significant variations in the propagation and attenuation of ultrasonic sound fields. These variations complicate interpretation of the UT responses and compromise the reliability of UT inspection. The objective for this effort was to initiate development of the theoretical and practical information needed to understand and potentially catalog grain structures of CASS piping based on variables associated with the casting processes. This investigation was concerned with identifying process parameters and their resultant impact on grain structures in LWR CASS piping, including small-diameter piping (i.e., PZR surge line and varied safe ends) and large-diameter primary coolant piping. The investigation began by developing a theoretical understanding of both the centrifugal and static casting processes and the major and minor parameters that affect the grain structure in these castings. Concurrently, industry, government, and academic contacts cognizant of current and past pipe casting processes were developed. These contacts were used to obtain information from LWR fabricators and CASS foundries to determine typical casting practices used and variations in those practices. In this investigation, four foundries were visited and their current and past practices were documented. It was concluded that columnar grains and banding (layers of significantly different grain structures) were common in austenitic steels and that such an array of parameters affected their development that control of these casting variables required extraordinary effort. Further, the grain structure cast by a foundry can vary from heat to heat; and within a heat (pipe or component) from one location to another. The limited amount of information on CASS components relating foundry and heat number to specific grain structures diluted the firmness of the conclusions that could be drawn. The propensity for the development of columnar grains in CASS piping and related components may be enhanced by low ferrite content of the cast alloy. iii iv Acknowledgments Dr. Robert Voigt of the Pennsylvania State University and Mr. Richard D. Rishel of WESDYNE have been of invaluable help in identifying foundries and cast pipe specimen sources. Also, Dr. Steve Doctor’s knowledge of the history of many of the specimens identified in this report was vital. The author’s are grateful to Chris Oldfather, Senior Metallurgist at ESCO’s Portland, Oregon, facility and Sr. Sales Engineer Gerry Craft at US Pipe and Foundry’s Union City, California, facility, who were excellent hosts and spent a great deal of time providing historical information and technical details associated with our mission. Finally, the authors wish to thank Kay Hass at PNNL for her significant efforts in compiling, editing, and formatting this document through its evolution. v vi Acronyms and Abbreviations ACE Alloy Casting Institute AISI American Iron and Steel Institute ANL Argonne National Laboratory AOD argon-oxygen decarburization APE pipe-to-elbow (auto weld) ASME American Society of Mechanical Engineers ASTM American Society for Testing and Materials BCC body centered cubic CARRE Cast Austenitic Round Robin Exercise CASS cast austenitic stainless steel CCSS centrifugally cast stainless steel CEGB Central Electricity Generating Board EPRI Electric Power Research Institute FAM French Foundry FCC face centered cubic GFN grain fineness number ID inner diameter INE inlet nozzle-to-elbow IPD Industrial Products Division ISI inservice inspection LD large diameter LWR light-water reactor MD moderately defined MG mixed grains MPE pipe-to-elbow (manual weld) Mwe megawatts electric NRC U.S. Nuclear Regulatory Commission OD outer diameter ONP outlet nozzle-to-pipe OPE outlet pipe-to-elbow PD poorly defined PIRR Piping Inspection Round Robin PISC Programme for Inspection of Steel Components PNNL Pacific Northwest National Laboratory POP pump outlet-to-pipe PZR pressurizer vii RCL reactor coolant loop RRT round robin test RT radiographic testing SCC stress corrosion cracking SCSS statically cast stainless steel SFM Sandusky Foundry and Machine SwRI Southwest Research Institute UNK unknown UNS Universal Numbering System USP U. S. Pipe UT ultrasonic testing WO well organized WOG Westinghouse Owners Group WSS wrought stainless steel viii Contents Summary ...................................................................................................................................................... iii Acknowledgments ......................................................................................................................................... v Acronyms and Abbreviations ..................................................................................................................... vii 1.0 Introduction ....................................................................................................................................... 1.1 2.0 Objective ............................................................................................................................................ 2.1 3.0 Procedure ........................................................................................................................................... 3.1 3.1 Literature Review ...................................................................................................................... 3.1 3.2 Networking ................................................................................................................................ 3.1 3.3 Internet ...................................................................................................................................... 3.1 4.0 Results ............................................................................................................................................... 4.1 4.1 Process Description and Parameters ......................................................................................... 4.2 4.1.1 Introduction .................................................................................................................... 4.2 4.1.2 Centrifugal Cast Stainless Steel ..................................................................................... 4.2 4.1.3 Statically Cast Stainless Steel....................................................................................... 4.10 4.1.4 Summary of Process Parameters to Document for CASS Pipe .................................... 4.12 4.2 Grain Structure Development .................................................................................................. 4.14 4.2.1 Introduction .................................................................................................................. 4.14 4.2.2 Centrifugal Cast Stainless Steel ................................................................................... 4.16 4.2.3 Statically Cast
Details
-
File Typepdf
-
Upload Time-
-
Content LanguagesEnglish
-
Upload UserAnonymous/Not logged-in
-
File Pages160 Page
-
File Size-