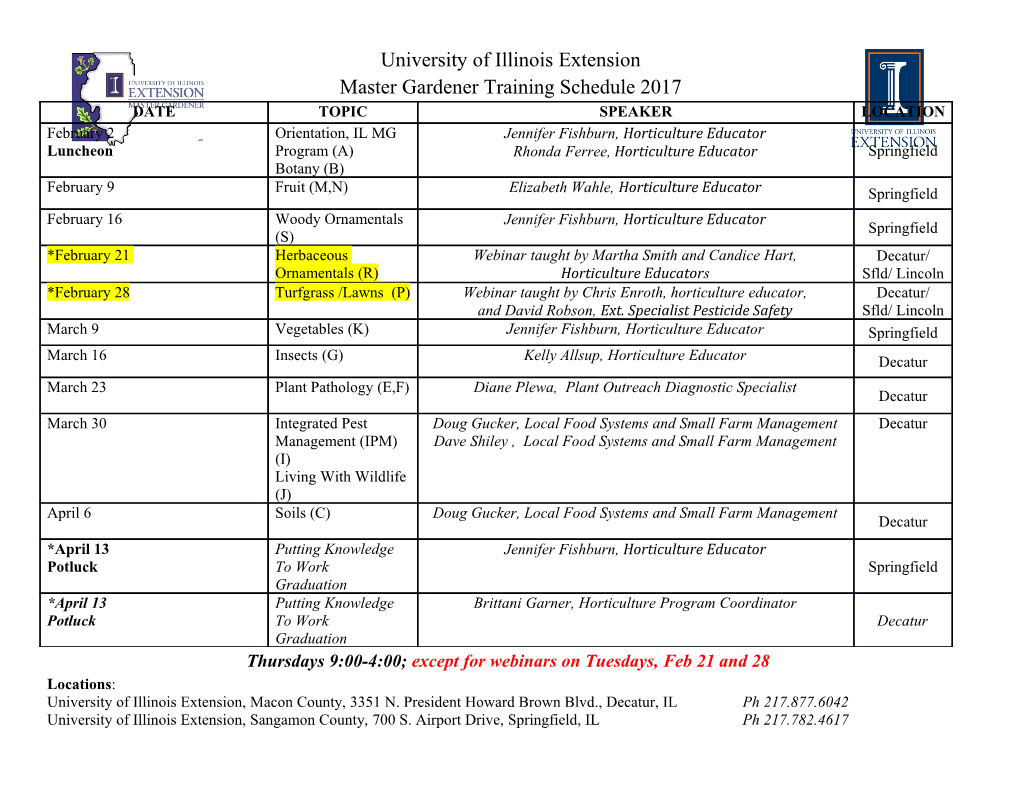
<p>Rochester Institute of Technology Kate Gleason College of Engineering Multidisciplinary Senior Design Project</p><p>Project Number: P13453 Reciprocating Compressor: Wireless Instrumentation for Compression Systems</p><p>Sean Deshaies (Mechanical Engineering)</p><p>Brandon Niescier (Mechanical Engineering)</p><p>Michael Gorevski (Electrical Engineering)</p><p>Erin Sullivan (Electrical Engineering) Table of Contents Abstract……………………………………………….. Erin Project Requirements……………………………….. Mike Project Background and Research………………...</p><p>Accelerometer Research - Sean</p><p>Encoder Research - Brandon</p><p>Wireless Research - Erin Concept Selection…………………………………… Mike Test Fixture…………………………………………… Sean Installation…………………………………………….. Brandon Wireless Transmission………………………………. Mike Summary of Results…………………………………. Brandon Comments and Conclusion…………………………. Sean Works Cited…………………………………………… Erin Appendix………………………………………………. Erin</p><p>Rochester Institute of Technology Multidisciplinary Senior Design Abstract In order to minimize compressor damage and down-time due to bearing failure, there exists a need to be able to monitor the health of the crankshaft bearings. Currently, bearing wear is identified through visual inspection or detected through audible noise. Neither option is ideal: inspection is time consuming, and noise only becomes apparent when the bearing is near failure or has already failed. The purpose of this project is to monitor the health of the main crank bearing on RIT’s Dresser-Rand ESH-1 compressor through vibration measurements via wireless sensor technology to predict bearing failure before it becomes a major problem. Research was completed on accelerometers, encoders and wireless technology to provide a knowledge base and allow the team to choose the best possible solution. The solution was accomplished by selecting 2 PCB accelerometers and installing them in strategic locations on the compressor, selecting TelosB modules to transmit and receive the vibration data wirelessly, and integrating our devices with the existing data acquisition system (DAQ). The resulting system allows an operator to identify wear on the bearing and identify when bearing failure begins to occur. To complete testing for this system, a test fixture was constructed to mimic operating conditions and troubleshoot the solution before installation. Testing successfully verified the functionality and limitations of the accelerometers and wireless components and the system was successfully installed on the compressor. The system interfaces with the preexisting DAQ and vibration data is collected and available for analysis.</p><p>Project Requirements In order to monitor the health of the crankshaft journal bearings, the customer required the use of accelerometers to measure vibrations in the system. To be more specific, the customer required two sensors. One sensor to be stationary and mounted on the bearing housing inside of the compressor, and the other sensor to be rotating and mounted on the flywheel of the system. In order to obtain data from a rotating sensor, a wireless transmission method would be necessary. Measuring vibration would allow us to see if the bearings are going bad. Therefore, the customer required that the sensors are continuously operating, and that the data is accurate and reliable. Due to harsh environments inside of the compressor, the sensors that we chose had to be robust in design. These requirements allowed us to come up with specifications that came into play when choosing the technology. The main specifications are listed below:</p><p>1. Acceleration Range of the Sensor</p><p>2. Acceleration Sensitivity</p><p>3. Range of Wireless Transmission</p><p>4. Maximum Operation Temperature </p><p>5. Size of the Sensor and Wireless Technology</p><p>Rochester Institute of Technology Multidisciplinary Senior Design Project Background and Research The long term goal for this project is to develop a “plug and play” system to monitor the health of the crankshaft journal bearings on RIT’s Dresser-Rand ESH-1 air compressor. Our primary focus will be the implementation and validation of wireless transmission of sensor data. This project will interface with systems installed by previous senior design teams, past senior design projects involving the compressor are listed below</p><p> P12453: Compressor Health Monitoring system</p><p> P11452: Compressor Facility Installation & Validation</p><p> P09452: Compressor Part Fabrication and Compressor Revamp</p><p>To complete the project research was compiled on several different aspects and technologies affecting the project. A summary of major research completed has been included below.</p><p>Accelerometer Research The original plan for this senior design project was to have three accelerometers placed on the compressor. Two of these accelerometers would be placed inside the crankcase on the bearing housing. One would transmit data wirelessly and the other via a wired connection. The third accelerometer was to be placed on the crankshaft in the keyway for the attached flywheel. Due to the rotation of the shaft, this accelerometer would also have to transmit its data wirelessly.</p><p>The placement of these accelerometers added to the design challenge. Originally, the only design requirement necessary for the accelerometers was a measurement range of ± 20 g. Concerns came up when ensuring that the two accelerometers inside the crankcase could withstand both the higher temperature (~200°F) and exposure to oil. Design changes eliminated the need for two accelerometers on the bearing housing. After contacting numerous vendors, PCB’s 607A11 “Swiveler” accelerometer was chosen.</p><p>This accelerometer has a measurement range of± 50 g, well above the requirement of 20 g. In addition to being able to withstand the harsh environment inside the crankcase, this accelerometer is stud mounted, which is preferred over other mounting methods such as epoxy as there is limited distortion of the vibration measurement comparatively.</p><p>The exterior accelerometer mounted on the shaft proved to be a greater problem. Due to it being on a rotating shaft, it would be impossible to power the accelerometer from a traditional power supply without using a slip ring. A slip ring was decided to be too difficult to work with, so the decision was made to power the accelerometer by battery. The challenge then became to find a low powered accelerometer. The vast majority of accelerometers required over 10 VDC, which would have required over six standard 1.5 V batteries. This was problematic as there was limited room for batteries as well as more weight was added to the rotating shaft, the more likely the chance that a vibration would be induced in the system, skewing the data collected. Upon further research, the Series 660 by PCB was come across. It came in various configurations, including a low power version which required only 3 to 5 VDC. As the board being used for wireless transmission was already being powered with 3 VDC from batteries, this</p><p>Rochester Institute of Technology Multidisciplinary Senior Design option proved to be the best fit. A downside to this accelerometer was that it had to be mounted with glue instead of a stud mount, but precautions were made in choosing a glue that would least interfere with vibration transmission.</p><p>How an Accelerometer Works Accelerometers are devices used to measure proper acceleration. This means that they only measure dynamic acceleration relative to a free-fall and does not take into account the earth’s gravitational pull. In our system, piezoelectric accelerometers are used. </p><p>(PCB Piezotronics)</p><p>The above image shows a simplified version of a piezoelectric accelerometer like the ones used in our system. As a force is applied to the mass, the distribution of positive and negative ions in the piezoelectric material attached to it changes. This change induces a charge in the system which is related to the force picked up by the accelerometer. The charge is then either conditioned internally or by a signal conditioner, depending on the type of accelerometer. Once this signal is conditioned, it is ready for viewing, analysis, etc.</p><p>Encoder Research An encoder was utilized to measure the speed of the rotating shaft within the test fixture. Rotary optical encoders can be broken down into two main types: incremental and absolute. Both function in a similar manner: an LED light is passed through a transparent disk and is then detected by a photodiode. An incremental encoder contains a disk with equally spaced opaque sections, which renders an output of equally spaced pulses measured in pulses per revolution (Encoder Guide). The output signal takes the form of a square wave and can have either one or two channels. Single channel output is useful for systems requiring simple velocity and position information in one direction only, with the encoder functioning as a tachometer. Two channel, or quadrature output consists of two signals phased 90 degrees apart. This phase relationship is used to determine the direction of rotation. In addition, incremental encoders can have an index signal which consists of a single pulse per revolution that corresponds to a fixed mechanical point of shaft rotation. The index signal is separate from the output signal(s) and is utilized for precise positioning in motion control applications (Optical Encoder Guide). An absolute encoder </p><p>Rochester Institute of Technology Multidisciplinary Senior Design contains a disk with concentric opaque sections, generating an output of binary numbers that correspond to each defined shaft position. Since each position has its own unique code, shaft position is always known. For both incremental and absolute encoders, the resolution is described in cycles per revolution. For incremental, it is the number of increments on the disk. For absolute, it is the number of defined positions (Encoder Guide).</p><p>Wireless Research Wireless data transmission was a customer request given for the proposed system. Wireless technology eliminates the need for wires to transfer data. There are several different forms of wireless technology; most common wireless technologies are a form of Radio Frequency (RF) transmissions that communicate data from a source to a destination. For the purposes of this project the following wireless methods were researched- Bluetooth, Wi-Fi, ZigBee and proprietary RF networks. Each option is a form of RF communication that is defined by different protocols defined by the Institute of Electrical and Electronics Engineers (IEEE). 802 protocols include families of various types of wireless networks. There are several different standards under the 802 category, each with separate standards for data transmission methods. Wi-Fi networks uses 802.11 standards and operates in the 2.4 and 5 GHz radio bands. (Discover and Learn) Bluetooth falls under IEEE protocol 802.15.1 and was specifically designed to transmit data over short distances using the 2.4 to 2.485GHz frequencies with a through-rate of 1Mbps. (What is Bluetooth?) ZigBee was built around IEEE protocol 802.15.4 and has a limited through- rate of 250 kbps operating at 2.4 GHz. (What is ZigBee?)</p><p>Each option, Wi-Fi, Bluetooth and ZigBee, has benefits and down falls, but overall each follows a protocol that limits the data transmission and it’s functionality in some way. As each of the wireless methods discussed have the capability of operating on a 2.4 GHz frequency, a proprietary RF network can also exist in the 2.4 GHz range and operate without the restrictions of any IEEE standards. (Comparison of 2.4-GHz proprietary RF and Bluetooth 4.0 for HID applications) The range of transmission, through-rate and power consumption can all be determined by the manufacture. This gives greater flexibility for customization and control to any customer seeking wireless solutions. </p><p>Concept Selection In our pursuit to design and develop wireless instrumentation to monitor the health of the bearings, many different idea organizing tools were utilized. Starting with a function diagram based on customer needs we listed all parameters which needed to be measured on the compressor. Engineering specifications were developed for all of our requirements, and a weighted house of quality was used to rank each engineering specification based on its importance to fulfill customer needs. Concept generation was considered an open team forum. When we had several ideas for each requirement a Pugh concept selection method was used. Similar to a house of quality with engineering specifications, concepts were evaluated against criteria, but all concepts are given a “plus” or “minus” compared to a datum concept. We moved forward with the concept that had the best score. Testing potential concepts for robust design by modeling, holding design reviews with peers and specialists, and interviews with knowledgeable people in the field also helped generate new concepts and rule original concepts out. </p><p>Rochester Institute of Technology Multidisciplinary Senior Design Implementing all of these results easily narrows down options and hardware capable of the particular application.</p><p>Test Fixture The test fixture designed for this project was created for many reasons. Most importantly, it was designed for risk mitigation. With at least three different groups working on the compressor at once, the chance that there would not be an opportunity to install the bearing monitoring system was high enough that a test rig would be designed to validate the system. Early design decisions included what needed to be replicated as close as possible on the test rig. The result was that the diameter of the rotating shaft and the speed at which the shaft rotated. The common shaft diameter is 2.75” while the rotational speed is 6 revolutions per second. Major differences between the test rig and the compressor include the use of different types of bearings and a different mounting strategy for the wireless transmitter. These differences were in large part to keep the cost of the test fixture down and these features were deemed non- critical to the proper functioning of the bearing health system.</p><p>CAD Assembly of Test Fixture</p><p>The CAD model shown above is the design of our test fixture. Aside from the aforementioned shaft (orange), components include the power supply (red box) which powers both the motor controller (black box) and the encoder (green cylinder at end of shaft). The motor controller allows control over the speed of the motor while the encoder records the speed at which the shaft rotates. At the end of the shaft opposite the encoder is the motor (black cylinder) which drives the shaft. It is connected to the shaft with a flexible coupling (green cylinder) and a stub shaft mounted to the shaft (not visible). The flexible coupling takes up any misalignment in the system between the shaft and the motor, allowing for looser tolerances. Holding the shaft up on either of its ends are bearing housings (blue) with bearings held in place with an interference fit </p><p>Rochester Institute of Technology Multidisciplinary Senior Design inside them (red). The seals on the bearings were removed to decrease the rolling resistance. The last significant part of the fixture is the gray box on top of the shaft. It contains the wireless transmitter. The translucent fixture around the shaft is the safety shield in case anything mounted to the shaft should come loose while it is rotating.</p><p>The tests this fixture will/can be/was used for include validation of the wireless system, comparing the outputs of both the wired and wireless accelerometer and comparing the differences in vibration measurements from accelerometers placed on the shaft and on the bearing housing Installation.</p><p>Installation </p><p>Wireless System The wireless system consists of an accelerometer and an enclosure containing the wireless module. The flywheel hub was selected as the mounting location for the accelerometer for both ease of installation and ease of maintenance. To provide a suitable mounting surface, a flat was milled onto the hub roughly 0.01in deep (Figure x). The mounting surface was cleaned with methyl ethyl ketone and the accelerometer was attached with an adhesive compound (Figure x).</p><p>For ease of installation, the battery pack was detached from the circuit board. Header pins were soldered onto both the board and the battery pack (Figure x). The board was attached to the lid of the enclosure via standoffs while the battery pack was glued to the enclosure body. A switch was installed on the side of the enclosure to easily turn the wireless circuitry on or off. The full assembly can be seen in figure x. The enclosure was mounted in the center of one of the spokes on the flywheel (Figure x). Two 1/4in-20 holes were drilled and tapped in the spoke for enclosure mounting. </p><p>The receiver module is attached to the data acquisition computer via a USB cable (Figure x).</p><p>Wired System The wired accelerometer was installed in the housing of the flywheel-side journal bearing (Figure x). This bearing was selected over the other as the desired the mounting location by the customer, who wished to have the wired accelerometer as close to the wireless accelerometer as possible for the purpose of data comparison. The bearing housing is part of the compressor frame, consisting of a cylinder of approximately 0.75in of cast iron supported by interior gussets. The mounting surface was prepared by stripping the paint off using a dremel (Figure x). Using a right angle drill, a 0.213in hole was drilled approximately 0.5in deep and then tapped with a 1/4in-28 thread roughly 0.375in deep (Figure x). To pass the wire through the crankcase wall, a 9/16in hole was drilled and tapped with a 3/8in NPT thread at the location shown in Figure x. The accelerometer mounting stud was screwed into the bearing housing and the accelerometer was fastened onto the stud. The cable was fed through the hole in the crankcase and then passed through a cable gland. Lastly, the cable gland was installed in the tapped hole, forming an oil-tight seal around the cable (Figure x). </p><p>Rochester Institute of Technology Multidisciplinary Senior Design Since the accelerometer cable lacked the necessary termination, a male BNC connector with two wire leads was soldered to the ends of the cable (Figure x). This connector was then plugged into the National Instruments data acquisition system (Figure x).</p><p>Wireless Transmission Wireless communication is defined as the transfer of information between two or more points that are not connected by an electrical conductor. For our application, the TelosB wireless module was selected for its low power sensor network capabilities. This module combines a low power microprocessor along with a radio and an integrated on board antenna. The wireless transmission of the signal occurs between two of these wireless modules. One of the modules is responsible for taking in the data from the sensor into an analog to digital converter, sampling that data, and transmitting it over the air. The other module is responsible for receiving the data and decoding it so it can be analyzed. These modules are configured through code written in the TinyOS environment. The transmission occurs at 2.4 GHz. This band is the same band used by wireless local area networks (Wi-Fi). In order to avoid interference with Wi-Fi networks, the modules are programmed to operate on a different channel than that of a Wi-Fi network. </p><p>Summary of Results</p><p>Conclusion</p><p>Works Cited Encoder Products Company. (2006, Fall). Retrieved December 27, 2012, from Optical Encoders Guide.</p><p>Anaheim Automation. (n.d.). Retrieved December 27, 2012, from Encoder Guide: http://www.anaheimautomation.com/manuals/forms/encoder-guide.php</p><p>Comparison of 2.4-GHz proprietary RF and Bluetooth 4.0 for HID applications. (n.d.). Retrieved January 3, 2013, from Cypress: http://www.cypress.com/?docID=26882</p><p>Discover and Learn. (n.d.). Retrieved January 3, 2013, from Wi-Fi Alliance: http://www.wi- fi.org/discover-and-learn</p><p>PCB Piezotronics. (n.d.). Technical Support Home. Retrieved January 11, 2013, from Introduction to Piezoelectric Accelerometers: http://www.pcb.com/techsupport/tech_accel.php</p><p>What is Bluetooth? (n.d.). Retrieved January 3, 2013, from Tech Radar: http://www.techradar.com/us/news/phone-and-communications/mobile-phones/what-is- bluetooth-1063913</p><p>Rochester Institute of Technology Multidisciplinary Senior Design What is ZigBee? (n.d.). Retrieved January 3, 2013, from Wise Geek: http://www.wisegeek.com/what-is-zigbee.htm</p><p>Drawings</p><p>Rochester Institute of Technology Multidisciplinary Senior Design</p>
Details
-
File Typepdf
-
Upload Time-
-
Content LanguagesEnglish
-
Upload UserAnonymous/Not logged-in
-
File Pages10 Page
-
File Size-