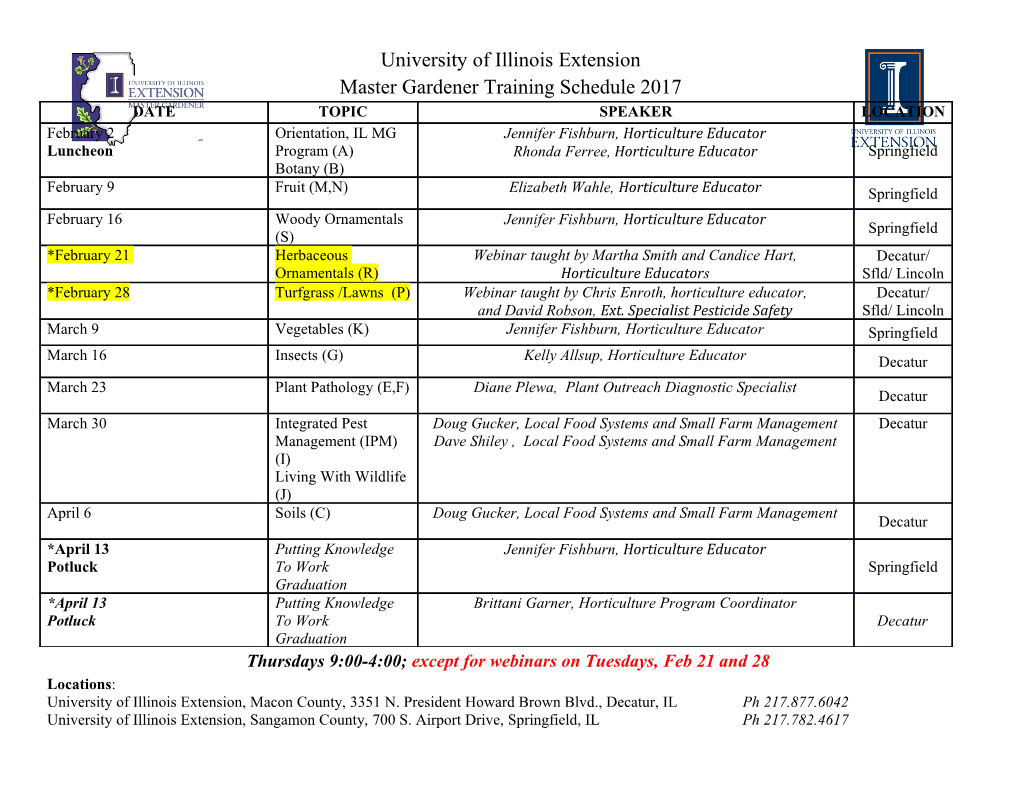
<p>Sheet Metal Forming Basics(Chapter 13)</p><p>A. Basic Characteristics of Sheet Metal Forming 1. Products have a large surface area 2. Products have a low modulus(<1/4 or 5mm) 3. 2D rather than 3D Forming(little thickness change) 4. Also called “press-working”, “stamping”</p><p>B. Major Classes of Sheet Metal Operations 1. Shearing – process of cutting sheet metal into small pieces – some operations are blanking, piercing, slitting 2. Bending Operations – Plastically deform metal into shape – some operations are V-bending, press-brake bending (brackets and angles are often formed by bending) 3. Drawing Operations – process where sheet metal is drawn into die – some operations are stretch drawing, deep drawing, reverse drawing(cartridge shells, pencil/pen shells, etc.)</p><p>1 C. Common Defects in Sheet Metal Operations 1. Orange Peel – outside surface is “grainy” and result of bulging of large grains(reduce grain size). 2. Stretch Marks(Luder Lines) – lines on surface that are harmless with respect to mechanical properties, but are objectionable in appearance. Caused by carbon & nitrogen interstitials in steel. 3. Localized Thinning – where stress exceeds UTS or defect in surface permits concentrated stresses. 4. Earing – results from planar isotropy. Uneven edges from mechanical properties being different in different directions. 5. Fracture – catastrophic defect</p><p>D. Anisotropic Behavior Rm = (R90 + 2R45 + R0 )/4 = mean anisotropic coef. Rp = (R90 - 2R45 + R0 )/2 = planar anisotropic coef. High Rm gives a) High LDR(limiting draw ratio) b) good resistance to thinning Low Rp gives good resistance to earing.(low Rp/Rm) </p><p>2 E. Shearing 1) Shearing Types a) Guillotine (shear area = Lt)</p><p> b) Alligator (shear area = (t/sin) x t)) and assuming sin= tan for small </p><p>2) Shear Forces Ps = shear force = shear area x shear stress Shear area = Length cut(L or t/sin) x Thickness(t) </p><p>3) Coil(strip) Width W = (N-1) x sin(60) x (D + X) + (D + 2Y)</p><p>W = width of coil N = number of disks per press stroke X = minimum distance between 2 disks(skeleton width) Y = minimum edge clearance D = diameter of disk</p><p>Yield = {[N x D2/4] / [ W x (D + X)]} x 100 (assuming close packed spacing of disks)</p><p>3 F. Bending 1.Bend Radius:Thickness Ratio(Rb/t) a. Engineering Ultimate Tensile Strain eu >= (L – Lo) / Lo</p><p>Lo = before bending & at neutral axis = x (Rb + t/2)</p><p>L = outside surface length after bending = x (Rb + t)</p><p> eu >= {[ x (Rb + t) - x (Rb + t/2)] / [( x (Rb + t/2)] eu >= 1/[2Rb /t + 1] or Rb/t >=(1/2) x [(1/eu ) – 1] b. True Strain & Reduction of Area a) = ln(L/Lo) = ln[(Rb + t) / (Rb + t/2) ] <= ln A0/A</p><p>Ra = reduction of area = [(A0 - A)/Ao] x 100 =[ 1 – A/Ao] x 100 b) (1 - Ra/100) = A/Ao or Ao/A = 100/( 100 – Ra)</p><p>Inserting b) in a) and solving Rb / t >= [50/Ra – 1] (experimental data gives value of 60 instead of 50, general range of Ra is between 20 and 70)</p><p>4 2. Bend Length</p><p>L = (/360) x 2(Rb + kt) Where k = neutral axis location fraction = 0.50(normal) = 0.33 for tight bends(Rb < 2t)</p><p>5 F. Deep Drawing (see figure with punch, die, blank holder) 1.Blank Diameter Calculations Assumptions a) Constant Volume b) Constant Thickness Therefore have constant surface area</p><p>Surface Area of Blank = Surface Area of Part For cup ______2 Dblank = d + 4dh where d = punch diameter and h = cup height</p><p>If the thickness of the bottom remains constant and the thickness of the walls thin to the clearance ([die diameter - punch diameter] / 2), then the expression becomes ______2 Dblank = d + 4hd x (twall/tbase)</p><p>6 2. Limiting Draw Ratio(LDR) Limit</p><p>Dblank(max) = LDR x Dpunch = maximum blank size for a punch (if blank is larger, a larger punch will be required for the first draw and more than 1 draw will be required)</p><p>3.Maximum Force for Deep Drawing</p><p>Fmax = x Dpunch x t x UTS x[Dblank/Dpunch – 0.7]</p><p>Dblank/Dpunch = Draw Ratio</p><p>4.Percent Reductions in Drawing - R(%) a) Diameter Based Reduction(circular parts only) R(%) = {[Dblank – Dpunch] /Dblank} x 100</p><p> b) Area Based Reduction R(%) = {[Ablank – Apart base] / Ablank}| x 100 Ablank = area of blank, Abase = area of base of part </p><p>7</p>
Details
-
File Typepdf
-
Upload Time-
-
Content LanguagesEnglish
-
Upload UserAnonymous/Not logged-in
-
File Pages7 Page
-
File Size-