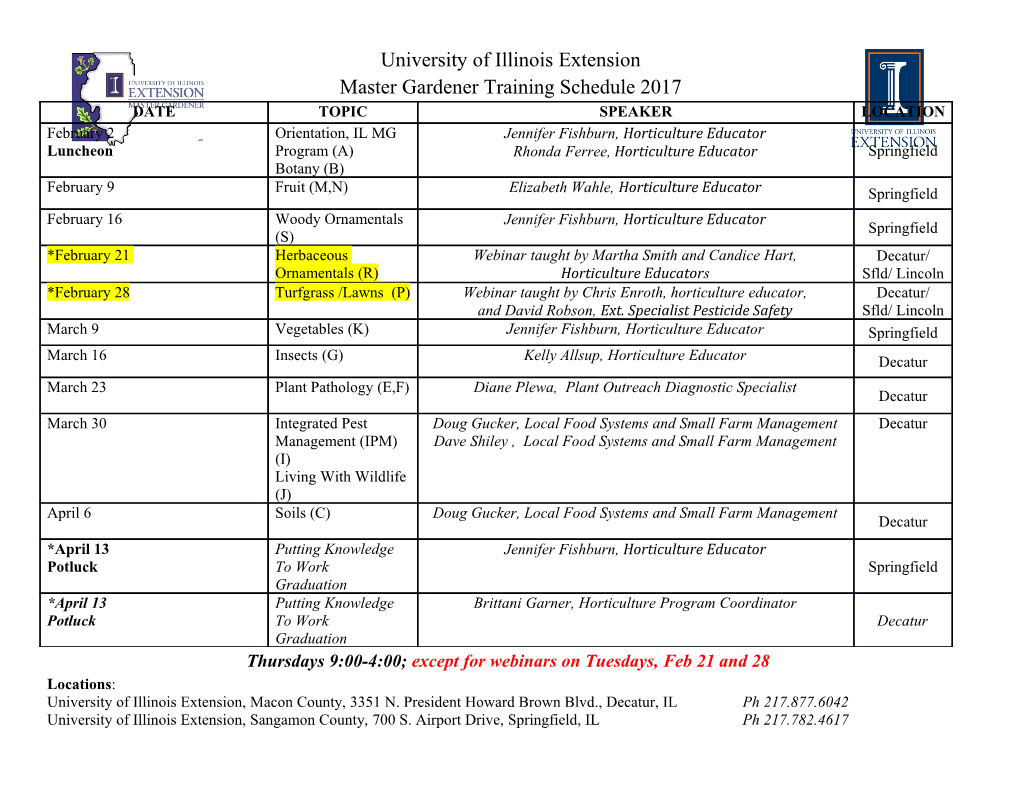
<p> Cost Accumulation System</p><p>The accumulation and classification of routine product cost data are very important and time-consuming tasks. Cost accumulation in general is the organized collection of cost data via a set of procedures or systems. Cost classification is the grouping of all manufacturing costs into various categories in order to meet the needs of management. A figure indicating the total cost of production provides little useful information about a company’s operations, since the volume of production (and therefore cost) varies from period to period. Thus, some common denominator, such as unit costs, must be available in order to compare various volumes and costs. Unit cost figures can be readily computed by dividing the total cost of goods manufactured by the number of units produced. Unit costs are stated in the same terms of measurement used for units of output, such as cost per ton, per gallon, per foot, per assembly, and so on</p><p>COST ACCUMULATION: PERIODIC AND PERPETUAL SYSTEMS</p><p>A periodic cost accumulation system provides only limited product cost information during a period and requires quarterly or year-end adjustments to arrive at the cost of goods manufactured. In most cases, the additional ledger accounts needed are simply added to a financial accounting system. Periodic physical inventories are taken to adjust inventory accounts to arrive at the cost of goods manufactured. A periodic cost accumulation system is not considered a complete cost accumulation system since the costs of raw materials, work-in-progress, and finished goods can only be determined after physical inventories are taken. Because of this limitation, periodic cost accumulation systems are generally used only by small manufacturing companies. A perpetual cost accumulation system is a vehicle for accumulating product cost data, through the three inventory accounts, that provide continuous information about raw materials, work-in-progress, finished goods, cost of goods manufactured, and cost of goods sold. Such cost systems are usually very extensive and are used by most medium and large manufacturing companies. PERIODIC COST ACCUMULATION SYSTEMS</p><p>The first step in comprehending a periodic cost accumulation system is to understand the flow of costs as goods pass through the various stages of production. The flow of costs in a manufacturing company, under a periodic cost accumulation system, is shown in Figure. The cost of goods put into production (direct materials + direct labour + factory overhead) plus the cost of work-in-process inventory is subtracted from the cost of goods in process during the period. The cost of goods manufactured plus beginning finished goods inventory equals the cost of goods available for sale. When the ending finished goods inventory is deducted from this figure, the cost goods sold results. The total operating costs can now be computed by adding selling, general, and administrative expenses to the cost of goods sold. </p>
Details
-
File Typepdf
-
Upload Time-
-
Content LanguagesEnglish
-
Upload UserAnonymous/Not logged-in
-
File Pages2 Page
-
File Size-