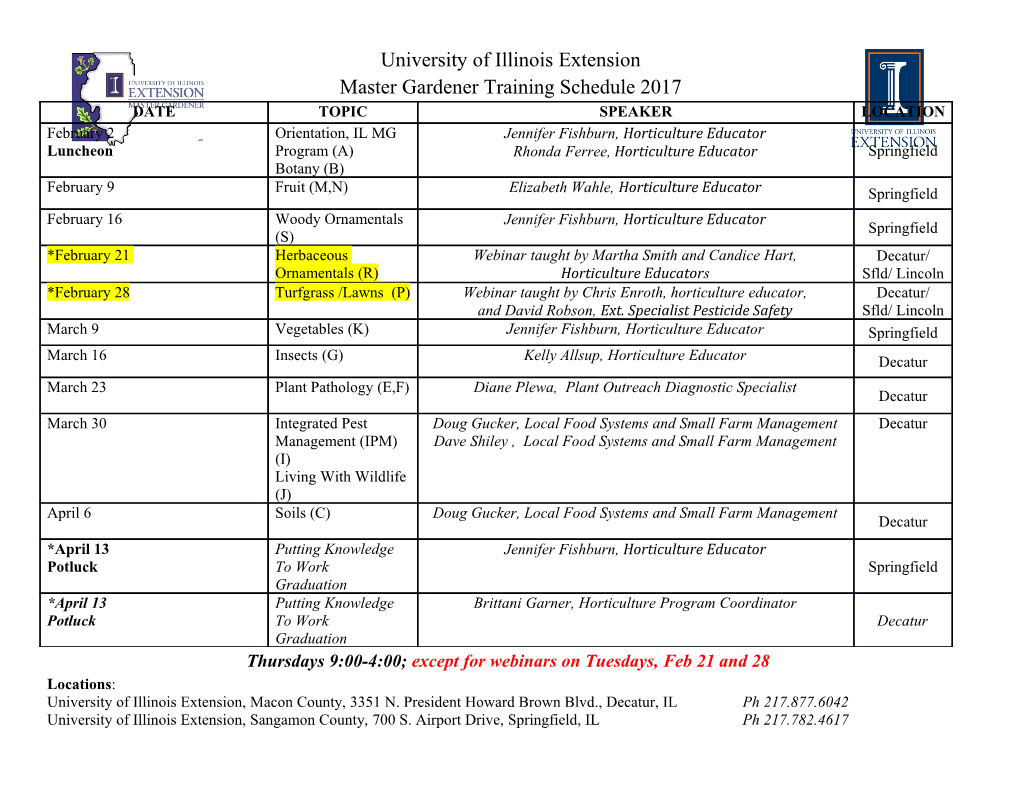
<p> CHAPTER 9 – LECTURE NOTE OUTLINE</p><p>I. Inventory Costing for Manufacturing Companies</p><p>A. Methods of Inventory Costing</p><p>1. Variable Costing</p><p> a. Variable manufacturing costs included as inventoriable costs initially</p><p> b. Fixed manufacturing costs excluded from inventoriable costs; Expensed as incurred</p><p>2. Absorption Costing</p><p> a. Variable and fixed manufacturing costs included as inventoriable costs initially</p><p> b. Required method under GAAP for external and tax reporting</p><p>B. Income Statement Presentation [Exhibit 9-1] </p><p>1. Variable Costing – Contribution Margin Format</p><p> Fixed manufacturing costs expensed in total</p><p>2. Absorption Costing – Gross Margin Format</p><p> Fixed manufacturing costs expensed per unit in cost of goods sold</p><p>3. Direct Costing: Not Variable Costing</p><p> Variable costing does not include all direct costs as inventoriable (direct fixed manufacturing and direct nonmanufacturing excluded)</p><p>C. Operating Income Differences [Exhibit 9-2] </p><p>1. Goods Sold vs. Goods Produced </p><p> a. Variable Costing: Quantity sold drives cost and income because fixed costs are expensed as incurred</p><p> b. Absorption Costing: Quantities sold and produced drives cost and income because all manufacturing costs are computed on a per unit basis</p><p> EI > BI: Less fixed costs expensed; Lower COGS; Higher Operating Income</p><p> EI < BI: More fixed costs expensed; Higher COGS; Lower Operating Income</p><p>1 2. Production-Volume Variance (Fixed Overhead)</p><p> a. Not present under Variable Costing</p><p> b. Exists under Absorption Costing when actual production volume differs from budgeted production volume</p><p> c. Fixed MOH Cost Rate * (Budgeted Production – Actual Production)</p><p>3. Comparative Income Effects – [Exhibit 9-3] </p><p>D. Income Manipulation -- Buildup of Inventories Under Absorption Costing [Exhibit 9-4] </p><p>1. Increase operating income by increasing production (even if no increases in customer demand)</p><p> a. Switch to manufacturing products that absorb the highest amounts of fixed manufacturing costs and delaying those that absorb the lowest</p><p> b. Defer machine maintenance beyond current accounting period</p><p>2. Revise performance evaluations to discourage inventory buildups</p><p> a. Careful budgeting reduces management's freedom to build up excess inventory </p><p> b. Use variable costing accounting system for internal reporting</p><p> c. Incorporate a carrying charge for inventory in the internal system</p><p> d. Change to a longer time period to evaluate performance</p><p>E. Throughput Costing</p><p>1. Only direct materials costs are inventoriable; all other costs expensed as incurred</p><p>2. Reporting includes throughput contribution: Revenues minus direct materials costs of goods sold [Exhibit 9-5] </p><p>3. Provides less incentive to “produce for inventory” than other methods</p><p>II. Fixed Manufacturing Costs – Denominator-Level Capacity</p><p>**Applies only to Absorption Costing**</p><p>A. Denominator-Level Capacity Choices</p><p>1. Theoretical Capacity: Producing at full efficiency all the time</p><p>2. Practical Capacity: Reduces theoretical capacity by unavoidable operating interruptions (i.e. scheduled maintenance; holiday shutdowns)</p><p>2 3. Normal Capacity Utilization: Satisfies average customer demand over several periods (i.e. 2 – 3 yrs)</p><p>4. Master-Budget Capacity Utilization: Expected level of capacity utilization for the next budget period</p><p>**Denominator decreases from Theoretical to Master-Budget Capacity Levels**</p><p>B. Choosing the Capacity Level</p><p>1. Capacity Management</p><p> Use Practical Capacity:</p><p> a. Fixes the cost of capacity as the cost to supply capacity (not demand)</p><p> b. Directs managers’ attention to unused capacity. Manage it by designing new products, leasing unused capacity to others, or eliminating excess capacity</p><p>2. Pricing Decisions</p><p> Use Practical Capacity:</p><p> a. Customers are not willing to bear cost of unused capacity</p><p> b. Downward Demand Spiral: Continuing reduction in demand for products that occurs when competitors’ prices are not met. As demand drops further, higher unit costs result in more reluctance to meet competitors’ prices. </p><p>3. Performance Evaluation</p><p>4. Financial Statements</p><p> a. Magnitude of production-volume variance </p><p> b. Method of disposing of end-of-period variances</p><p>5. Regulatory Requirements: IRS requires use of practical capacity</p><p>6. Difficulties in forecasting chosen denominator-level capacity</p><p>Suggested Problems: 9 – 16; 9 – 17; 9 – 18; 9 – 19; 9 – 20; 9 – 21</p><p>3</p>
Details
-
File Typepdf
-
Upload Time-
-
Content LanguagesEnglish
-
Upload UserAnonymous/Not logged-in
-
File Pages3 Page
-
File Size-