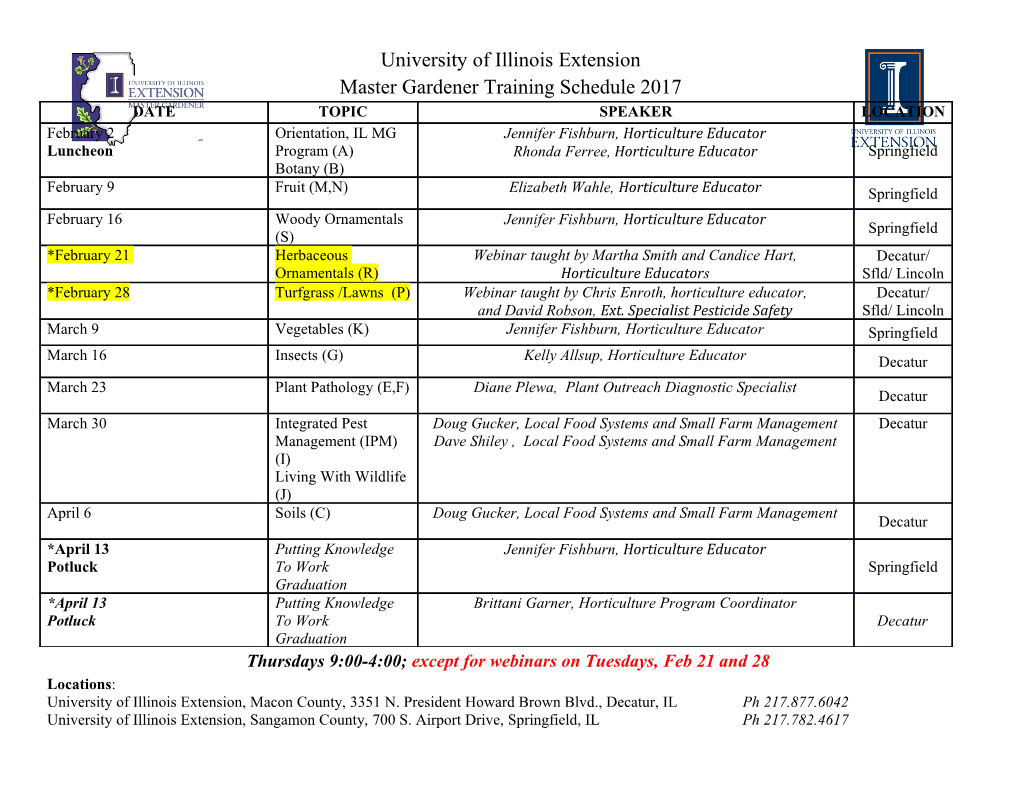
<p> 4.4 Miscellaneous Propulsion Casey Kirchner</p><p>Nomenclature RCS = Reaction Control System; also, provision of maneuvering and control OF = Oxidizer-to-fuel ratio M = Mass, kg or tonnes L = Length, m D = Diameter, m g = Gravitational acceleration, m/s2 F = Thrust, in Newtons</p><p>Isp = Specific impulse, s S = Surface area, m2 tw = Tank wall thickness, m V = Volume, m3 T = Temperature, K p = Pressure, N/m2</p><p>Ru = Universal gas constant tb = Burn time, s CM = Center of Mass ΔV = Delta Velocity, change in velocity required to execute maneuvers, m/s ρ = Density of material, kg/m3</p><p>4.4.1 Introduction In this section we describe the propulsive infrastructure necessary for reaction control and retrograde surface operations on both the Hab and ERA (Earth Return Assembly) vehicles. The propellant budget for these operations applies to the trip from Earth orbit up until landing on the Martian surface. For the ERA vehicle, the budget timeline extends to the trip back to Earth, including propellant to guide the CTV (Crew Transfer Vehicle) through the Earth’s atmosphere. Also included is propellant to spin up the tethered vehicles to provide artificial gravity for the crew. In addition to propellant mass, we size the</p><p>4-4-1 associated hardware, including engines, tanks, plumbing, and support structure for an inert mass estimate. These calculations are made on a staged basis, refiguring with new masses every time the mission moves into a new phase. Historical precedent is used as a basis for much of the sizing, and where not possible, the code is iterated to provide reasonable estimates of the weight cost of the mission.</p><p>4.4.5 Propulsion System Description The propulsion systems discussed in this section fall into two categories which for convenience we’ll call RCS and Retro. All systems use the storable hypergolic propellants MMH (Monomethylhydrazine) and NTO (Nitrogen Tetroxide). These propellants were chosen for their superior storability on long interplanetary missions and vast historical precedent and popularity in a wide variety of RCS applications. Engines on the order of 100 N fall into the “RCS” category and provide propulsion for tasks like docking, tether spin-up, and enroute maneuvering and attitude adjustments. Engines on the order of 100,000 N provide “Retro” propulsion for aeroassist maneuvers, hovering, and landing. The RCS systems are blowdown and the retro systems are fed by a turbopump. Sizing RCS Engines. The basis for the engine sizing was the required level of thrust, derived from the vehicle mass. Galileo’s RCS thrusters provided approximately 0.005 m/s2 of acceleration3, so we size the RCS thrusters for the Hab and ERA systems accordingly, with this acceleration and a simple application of Newton’s Second Law. Mass, length, and diameter estimates for the engines are then easily found with curve fits of historical engine data: F 1 M E,RCS (4.4.1a) g0 (0.006098F 13.44)</p><p>1 LE,RCS 0.0054F 31.92 (4.4.1b)</p><p>1 DE,RCS 0.00357F 14.48 (4.4.1c)</p><p>4-4-2 Again, these numbers are historical predictions and do not represent strict design limitations, which we saw as the best option for integration with the constantly changing structure of the overall vehicle. The dimensions include plumbing up to the prevalve.1 Figure 4.4.1 shows a typical pressure-fed liquid propulsion system, complete with a representative RCS thruster.</p><p>Figure 4.4.1 Pressure-fed Liquid Propulsion System.2</p><p>Retro Engines. The thrust of the retro engines comes from an application of the thrust-to-weight ratio to the landing weight. Given an approximate maximum allowable propellant weight, calculations made in Section 2.3 provide an appropriate thrust-to-weight ratio for the Martian surface landing. Once the retro engine thrust is known, historical estimates for launch engines can then be applied for the estimation of physical parameters:</p><p>4-4-3 F 1 M E,Re tro (4.4.2a) g 0 (25.2log(F) 80.7)</p><p>1 LE,Re tro 0.00003042F 327.7 (4.4.2b)</p><p>1 DE,Re tro 0.00002359F 181.3 (4.4.2c) Using historical estimates as a sizing guide, we investigated current MMH/NTO engines for use in both RCS and retro applications. The Marquardt R-4D RCS engines6 fit the bill for providing RCS to both the Hab and ERV vehicles. The Russian Kosberg RD-0242M engine6, while never mass-produced, provide a good design start point for retro propulsion. Three engines of this size would be used to provide the appropriate thrust. Table 4.4.1 gives the physical parameters for these engines. Table 4.4.1 Engine Physical Parameters RCS Retro Thrust F, N 490 100,000 Mass M, kg 4 185 Length L, m 0.6 1.6 Diameter D, m 0.3 0.8 Placement The retro motor for the Hab is located on the bottom of the Hab module, on the opposite end of the vehicle from where the tether and parachute attach. Its propellant tanks are nearby the retro engines, as are the tanks that feed the RCS engines, which are arranged toward the top of the vehicle. The MLV retro motors are similarly located on its own stage between the garage (which drops off) and the MLV stage. Ten RCS engines are arranged in two groups of three and two groups of two engines around the perimeter of the vehicles requiring RCS, and aligned to provide roll, pitch, and yaw control. Figure 4.4.2 shows the arrangement of engines on a typical landing vehicle. (Non-landing vehicles have RCS engines only.)</p><p>4-4-4 Figure 4.4.2 Typical Engine Configuration, retro engines inside entry heat shield.</p><p>4.4.3 Delta-V Budget Hab System The Hab system (comprised of the Hab vehicle and the spent NTR stage) makes a one-way trip to Mars, where the Hab vehicle lands on the planet and functions as a permanent base. On the way, the system expends propellant at six different budget points. We include propellant for deploying the tether, spinning the tethered system, providing RCS/maneuvering capability, entering orbit around the planet Mars, hovering above the surface, and finally landing on Mars. Table 4.4.2 outlines the propellant budget for the Hab system. The first budget point is the ΔV required to spin the vehicle to deploy the tether safely and efficiently. This maneuver is done in a coupled fashion, where thrust is applied far away from the system CM on both sides to provide maximum moment arms. At this time, the Hab and NTR are still mated with the tether undeployed between them. After the mated system is spun propulsively to an initial angular rate, the Hab and NTR spent stage are demated and allowed to drift away from the CM under centripetal force. At full tether extension, the conservation of angular momentum has slowed the system’s rotation considerably, and we use a second coupled burn to spin the system to 2 rpm. This provides 0.38 g of artificial gravity, which is appropriate to prepare the crew for surface operations on Mars. The next budget point is the baseline RCS propellant. At the request of the customer, we allocate 100 m/s ΔV for enroute maneuvers, course corrections, and attitude adjustments. Upon arrival at Mars, a 10 m/s burn is employed following aerocapture to raise the periapsis above the sensible atmosphere, placing the vehicle in a parking orbit. Another 10 m/s burn lowers</p><p>4-4-5 the perigee of that orbit to induce aeroentry. Aerodynamic forces (by way of aeroentry and parachute deployment) are used to accomplish most of the deceleration, but some propulsion must be employed very close to the surface to ensure a safe and accurate landing. First of all, there is enough propellant available to allow for 20 s of hover time, if necessary for a safe landing. This is in addition to the propellant required for landing. From analysis of the parachute/propulsive landing operations, Section 2.3 provides a landing ΔV and burn time which minimizes the weight of the combined parachute/retro propulsion system and gives a surface impact velocity of 0.5 m/s. ERA Vehicle The ERA system requires more ΔV than the Hab, since there is both a trip out to and a trip back from Mars that must be considered. More complex operations like docking in Martian drive up the ΔV budget as well. Still in place is the 100 m/s customer requirement for enroute RCS and maneuvering. This time, aerobraking into the Martian atmosphere uses a small amount of propellant. A landing ΔV is again found in Section 2.3, and extra propellant is reserved for 10 s of hovering. The return trip begins with docking operations on-orbit between the MLV/CTV and the ERV. After departing Mars, the vehicles require an artificial gravity spin-up like the Hab system. After the initial spin-up, the g level is increased from 0.38 g to 1.0 g over 31 days to re-acclimate the crew to Earth- level gravity. A third ΔV associated with spin-up is therefore given for the ERA system, which is the sum of the angular acceleration burns between Martian and Earth gravity levels. We add another 100 m/s for attitude control and maneuvering on the way back. Finally, ΔV is allocated to the CTV for adjustments necessary upon reentering the Earth’s atmosphere. Table 4.4.2 outlines the propellant budget for the ERA vehicle in terms of ΔV and propellant mass.</p><p>Table 4.4.2 Propulsive ΔV and Mass Budget. Propellant Application Hab ΔV, Hab prop, ERA ΔV, ERA prop,</p><p>4-4-6 m/s kg m/s kg Landing 75.22 3413 70.67 2964 Hovering 0.00 642 0.00 662 Mars Orbit Entry/Adjustment 20.40 460 4.08 91 Tether deployment 27.27 706 24.30 387 Spin-up, 0.38g 72.24 1840 146.12 2265 Spin-up, 1.0g N/A N/A 56.04 841 Spin-up, total 99.51 2546 226.46 3493 Enroute RCS/Maneuvering 102.00 2525 204.00 3990 CTV Earth entry N/A N/A 20.40 27 ERV orbit maintenance N/A N/A 1.02 10 Orbital docking ops N/A N/A 10.20 164 Total 297 9650 537 11,400</p><p>4.4.4 Propellant and Pressurant Masses The mass of propellant included on each vehicle system is found by calculating the mass fraction for each ΔV in the rocket equation: M final 1 V g 0 I sp ln glocal tb (4.4.3) M initial The mass fraction is applied to a known final weight for each budget point to give the total propellant weight related to that ΔV. At this point, the mixture ratio can be employed to separate the contributions to that total mass from the oxidizer and the fuel, per eqs. 4.4.2:</p><p> OF 1 M ox M prop (4.4.4a) OF 1</p><p> 1 1 M fu M prop (4.4.4b) OF 1 The pressurant (Helium was chosen for its low molecular weight) is assumed to be a separate mass, but is small when compared to the masses of the propellants. After the propellant volume is found, we calculate propellant tank pressures based on three pressure drops back-calculated from the desired chamber pressure. These drops are line losses through the feedsystem, an injector loss, and dynamic pressure loss (based on a representative flow velocity of 10 m/s).1 With the requisite propellant replacement volume and propellant tank pressures, the mass of the pressurant is then found according to: </p><p>4-4-7 p p ox fu 1 M press V press M He RuT f (4.4.5) 2 HAB Vehicle Because this particular vehicle makes but one trip out to Mars, the mass fractions are calculated chronologically backwards for the entire vehicle assembly, starting with the landing on the surface of Mars. The first mass fraction found is the landing mass fraction, which is applied to the final landing weight to find the vehicle weight including all propellant necessary for the landing event. Preceding the landing is the hover mass fraction sufficient for 10 s of hover time. Continuing backward, mass fractions are found for parking orbit entry and circularization, enroute maneuvers and attitude adjustments, and tether spin-up and deployment. Propellant masses are split between the Hab module and NTR spent stage for the spin-up and RCS phases of the mission, according to the masses of the two vehicles. Approximate propellant and pressurant masses for the Hab system appear in Table 4.4.4. Table 4.4.4 Propellant Masses for Hab. Hab NTR Total Oxidizer masses (kg) 3800 2100 5900 Fuel masses (kg) 2400 1300 3700 Pressurant masses (kg) 5 7 12 Total prop masses (kg) 6205 3407 9612</p><p>Figure 4.4.3 shows the drop in system mass corresponding to each of these mission events. Between events 5 and 6 (Mars Orbit and Hover), the system weight drops nearly 20 tonnes. This is because approximately 17.5 tonnes of heat shield are jettisoned after transit through the atmosphere.</p><p>4-4-8 Figure 4.4.3 Mass Schedule of Hab Vehicle after Earth Departure ERA Vehicle This vehicle is made up of many smaller parts which require their own RCS systems and have different functions chronologically throughout the two- part mission (trip to and from Mars). The entire ERA must have RCS propellant available on the trip to Mars. The MLV must have RCS and retro landing propellant (on a separate retro stage that gets left on Mars). In addition, it must have propellant aboard to dock with the ERV in orbit and to spin as a counterweight for tether-induced gravity on the trip back to Earth. Finally, the CTV needs propellant for Earth re-entry. The gravity spin here begins the same way as the Hab vehicle, with the spin for tether deployment and the second spin to induce gravity. However, the ERV trip back calls for an addition of a 0.2g per day over a 31-day progression back to Earth’s 1.0g. As the vehicle accelerates, the burn times to accomplish the gravitational increments get smaller, requiring less propellant.</p><p>4-4-9 Because of the more sophisticated mission architecture for this vehicle system, a graph of the chronological mass schedule has not been included. Propellant and pressurant masses for the ERA system appear in Table 4.4.5. Table 4.4.5 Propellant Masses for ERA. ERV CTV MLV Descent Total Oxidizer masses (kg) 3700 16 1060 2200 6976 Fuel masses (kg) 2300 10 660 1400 4370 Pressurant masses (kg) 10 0.2 5 10 25.2 Total prop masses (kg) 6010 26 1725 3610 11371</p><p>4.4.5 Infrastructure Masses Tankage mass is calculated based on propellant volume, tank pressure, and tankage material densities. The tanks are made from graphite for weight and strength considerations. To counteract the corrosive effects of the hypergolic fuels, the fuel tanks are fitted with liners of aluminum. 4 The tank mass is found with this simple equation (the aluminum portion is omitted if sizing the pressurant tanks):</p><p>1 M tan k S tan k t w graphite (S tan k tw ) alu min um (4.4.6) We size the support structure for the engine by assuming 10% of the overall system mass is necessary for the structure.1 Combining the engines, support structure, and tank weights, we arrive at inert mass figures for each of the vehicles. These inert masses are generally very small compared to the mass of the corresponding propellant. Tables 4.4.6 and 4.4.7 summarize the inert mass budget for the Hab and ERA vehicles.</p><p>Table 4.4.6 Inert Mass on Hab Hab NTR Total Descent Engine mass (kg) 555 0 555</p><p>4-4-10 RCS Engine mass (x10) (kg) 40 40 80 Oxidizer tank masses (kg) 24 13 37 Fuel tank masses (kg) 24 13 37 Pressurant tank masses (kg) 4 5 9 Struct. support mass (kg) 65 7 72 Stage inert mass (kg) 712 78 790</p><p>Table 4.4.7 Inert Mass on ERA ERV CTV MLV Descent Total Descent Engine mass (kg) 0 0 0 555 555 RCS Engine mass (x10) (kg) 40 40 40 40 160 Oxidizer tank masses (kg) 20 0.5 7.5 55 83 Fuel tank masses (kg) 20 0.5 7.5 55 83 Pressurant tank masses (kg) 8 0.2 3.5 .1 11.8 Struct. support mass (kg) 9 4 6 71 90 Stage inert mass (kg) 97 45.2 64.5 776 983</p><p>4.4.6 Conclusions We use primarily pressure-fed, hypergolic liquid propulsion systems to provide the propulsion necessary for tether operations, enroute maneuvers and attitude adjustment, and planetary landings. We use a total of 297 and 537 m/s of ΔV on the Hab and ERA, respectively. These requirements result in total system masses of 10.4 tonnes on the Hab and 12.4 tonnes on the ERA. This translates to a $2000 million development and launch cost for the miscellaneous propulsion components.</p><p>Sources 1. Henry, Gary N., Humble, Ronald W., and Larson, Wiley J., “Space Propulsion Analysis and Design,” McGraw-Hill, Inc., 1995, pp.1-30, 179- 294. 2. Sutton, George P., “Rocket Propulsion Elements,” John Wiley & Sons, Inc., New York, NY, 1949, pp.22-36, 188. 3. Personal communication with Prof. Longuski 4. Personal communication with Shannon Fitzpatrick</p><p>4-4-11 5. Kowalsky, C., and Powell, J.D., “Tethered Artificial Gravity Spacecraft design,” Astrodynamics 1993; Proceedings of the AAS/AIAA Astrodynamics Conference, Victoria, Canada, Aug. 16-19, 1993. San Diego, CA, Univelt, Inc., 1994, p. 645-664 6. Wade, Mark, “Encyclopedia Astronautica,” http://www.friends- partners.org/mwade/, last updated March 26, 2001.</p><p>4-4-12 Abstract A manned mission to Mars places propulsion demands on the spacecraft beyond launch and parking orbit departure. Propellant budget is also allocated for enroute maneuvering and attitude adjustment, tether rotation for artificial gravity, parking orbit entry, orbit operations and docking, and surface landing. The propulsion systems required for these tasks are smaller, but must be located on nearly all vehicles that make up the larger Hab and ERA systems. We use primarily pressure-fed, hypergolic liquid propulsion systems to provide the propulsion necessary for these miscellaneous operations. We require a total of 298 and 535 m/s of ΔV on the Hab and ERA, respectively. These requirements result in total miscellaneous propulsion system masses of 10.0 tonnes on the Hab and 11.7 tonnes on the ERA.</p><p>4-4-13</p>
Details
-
File Typepdf
-
Upload Time-
-
Content LanguagesEnglish
-
Upload UserAnonymous/Not logged-in
-
File Pages13 Page
-
File Size-