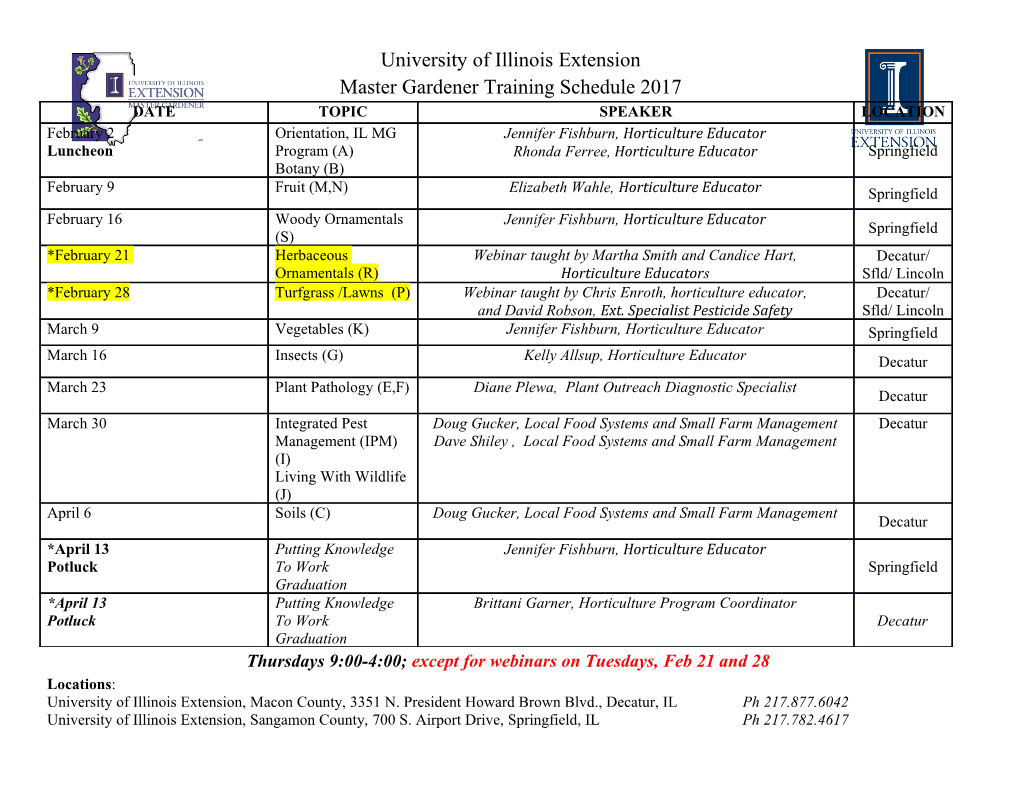
<p> “GH.ASACHI” TECHNICAL UNIVERSITY of IAŞI Approved FACULTY OF MECHANICAL ENGINEERING</p><p>DEAN Machine Design and Mechatronics Department Prof.dr.ing. Spiridon Creţu Academic year 2006-2007</p><p>SYLLABUS for the discipline MECHATRONICAL SYSTEMS DRIVING Specialties: Mechatronics and Robotics, 4th year, semester I Type of matter: Optional matter Courses holder: Assoc. Prof., Ph.D. Eng. Gheorghe PRISACARU Applicative activities holder: Assoc. Prof., Ph.D. Eng. Gheorghe PRISACARU Structure in curriculum: Semester Evaluation Credits Total number of Discipline Number of hours per week form number hours total number K of hours Cours Semina Laboratory Project C S L P e r activities activities 7 3 - 1 1 Exam 7 42 - 14 14 70</p><p>CONTENT</p><p>A. DISCIPLINE OBJECTIVES - Presentation of the place and role of the driving system in the mechatronic system; - Presentation of the general structure of a driving system, particulary of a robot; - Approach of the „conventional” driving types (hydraulic, pneumatic, electric and hybrid) and of the „nonconventional” ones, with the advantages and disadvantages from the constructive and functional point of view; - Knowledge of the present tendencies in the domain of driving systems.</p><p>B. COURSE STRUCTURE 1. General notions regarding the mechatronic systems and mechatronic driving systems…………..……………………………………..……………………… 3 hours Mechatronic systems; Place of the driving system in the frame of the mechatronic system; Principles of choice of the driving system; General presentation of the driving system types; Advantages and disadvantages; Robot driving system (definition; structural scheme of a robot; subsystems that robots consists of) 2. Hidraulic drive…………………………………………………………………..14 hours Organising the hydraulic equipment; Component of the hydraulic driving equipment; Hydraulic driving systems types; Characteristic features of the calculus when driving with a hydraulic motor; Classification of hydraulic motors; Symbols and notations used in practice; Control and auxiliary hydraulic system; Positioning hydraulic systems with sequential command; Electrohydraulic open systems with numeric command; Electrohydraulic pursuance systems. 3. Pneumatic drive………………………………………………………………12 hours Structure of the pneumatic driving systems; Particularities regarding the calculus of the pneumatic driving; Symbols and notations used in pneumatics; Pneumatic equipment: control equipment (distribution, regulation and debit and pressure control equipment); Auxiliary pneumatic equipment; Driving pneumo-hydraulic equipment; Particular pneumatic driving; Special structures of driving pneumatic units; 4. Electric drive……………………………………………………………………..8 hours D.C. electric motor; D.C. servomotor; Step-by-step electric motor; Rotative and liniar step-by-step electric motor; Tri-phased non-synchronic motor; Liniar electric motor; Tendences in the development of the electric motor for the driving of the robots; 5. Special drive……………………………………………………………………….2 hors Chemical actuators ; Actuators based on the shape memory alloy; Piezoelectric actuators; Magnetostictive actuators; electrostatic actuators; Optical actuators etc. 6. Elements of motion transmission …………………………………………… 3 hors Position of the driving motors; Mechanical transmissions (gears, belt-transmission, chains, articulated levers, screw-nut); Brakes;</p><p>C. LABORATORIES Unfolding place: Mechatronic Lab. Application: 1. Constructive knowledge of a mechatronic system (mechanical, pneumatic, electric and electronic components) – 2 hours 2. Regulation and running of the equipment; Prominence of the fast and low speed achievement of the pneumatic motors; vacuum technique; Presentation of the scheduled automat; technical characteristics, hardware construction – 2 hours 3. Presentation of the programming medium FSTFEC: - menu description; creation of a project; configuration etc. - creation of a STL programme (Statement list) – 2 hours 4. STL operands; structure of a STL programme; STL instructions (SET, RESET, LOAD….); Equipment applications – 2 hours 5. Timers; Applications; Counters; Applications; On line connection and On line repairing; On line verification of the programmes. – 2 hours 6. Applications– 2 hours 7. Individual tests. – 2 hours</p><p>D. PROJECT Unfolding place: Mechatronic Lab. Theme: Dimension of the liniar electromagnetic actuator used for a positioning application 1. Enouncement of the theme; Precization of the parameters that characterize the application; Scheme of the imposed constructive variant – 2 hours 2. Determination of the running point of the permanent magnet – 2 hours 3. Establishment of the permanent magnets dimensions and of the iron yoke. – 2 hours 3. Guidance system of the mobile assembly of the actuator; Calculus of the electric and mechanical time constants. – 2 hours 5. Assembly drawing (2D and 3D) – 2 hours 6. Components drawing – 2 hours 7. Project deliver. – 2 hours</p><p>EVALUATION OF STUDENTS. 60% - exam; 40% - the activity at the practical applications;</p><p>E. BIBLIOGRAPHY</p><p> L. Ciobanu - Manipulatoare şi roboţi industriali, Litografia Univ. Tehn. Iasi, 1994. Ph. Coiffet - Robot habilis, robot sapiens, Ed. Hermes, Paris, 1993. Ph. Coiffet, M. Chirouze - Elements de robotique, Ed. Hermes, 1982. G. Cojocaru, F. Kovacs - Roboţii in acţiune, vol I, II, Ed. Facla, Timisoara, 1986 Drimer s.a.-Roboţi industriali şi manipulatoare, Ed. Tehnică, Bucureşti, 1985. R. Ionescu, D. Semenciuc - Roboţi industriali, Editat de O.P.I.C.M., Bucuresti, 1996. G. Ionescu s.a. - Traductoare pentru automatizari industriale, vol.I, Ed. Tehnica, Bucuresti, 1985. N. Ioniţă - Elemente de mecanica automatelor şi dinamica automatizarii proceselor industriale, Ed. Tehnică, Bucuresti, 1985. V. Ispas - Aplicatiile cinematice in constructia manipulatoarelor si a robotilor industriali, Ed. Academiei Romane, Bucuresti, 1990. F. Kovacs, C. Rădulescu - Roboţi industriali,vol.I, II, Litografia Univ.Tehn. Timisoara, 1992. Penes - Roboti industriali, vol. I, OID pentru Ind. constr. de masini, Bucuresti, 1986. V. Maties s.a. – Actuatori in mecatronica, Ed. Mediamira, Cluj-Napoca, 2000. Gh. Prisacaru - Actionarea robotilor industriali, Ed. Vie, Iasi, 2000. Documentatia tehnica a MPS – 1 volum, Festo GmbH. Smart automation training – documentatie SC FESTO SRL Bucuresti</p><p>DISCIPLINE TITULAR, Assoc. Prof. Ph.D. Eng. Gheorghe PRISACARU</p><p>HEAD OF THE DEPARTMENT, Prof. Ph.D. Eng. Barbu DRAGAN</p>
Details
-
File Typepdf
-
Upload Time-
-
Content LanguagesEnglish
-
Upload UserAnonymous/Not logged-in
-
File Pages3 Page
-
File Size-