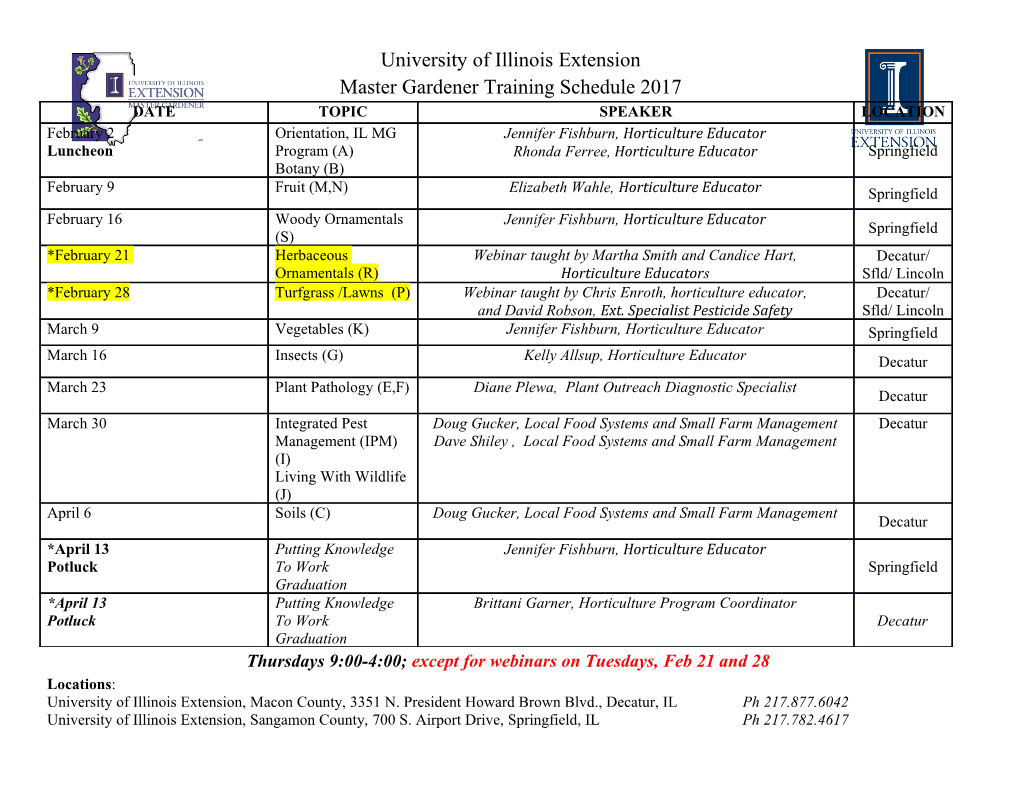
<p>Title: Development of Automated Fixture to Assemble Single Fractured Outer Race Spherical Plain Bearings Sponsor: RBC Bearings Sponsors Advisors: John Albini, John Cowles, [email protected], 203-267-7001 X5544, 203-631-0744 [c], Dave Ineson, [email protected], Brad Smith, [email protected]</p><p>Description: RBC’s West Trenton Division makes several types of metal-on-metal, and self- lubricated spherical plain bearings (SPBs). This project focuses on improvements to the method of assembly of SPBs at RBC that have an outer ring with a single split to allow the inner raceway (ball) to be assembled into the bearing by brute force. The inner ring is pushed into the outer ring causing the outer ring to open and then close over the ball, trapping the ball inside. The brute force method causes a number of these finished outer rings to fracture or chip thus rendering them as scrap. This method can also result in inner ring damage, and liner damage on our maintenance free, self-lubricated product line.</p><p>Project Summary: This is a continuation of a very successful project from last year where the students won second place in the end-of-year design competition. We would like the students to take the fixtures and tooling built last year, make improvements to key components to extend the tooling life, and automate the process of assembling the two bearing components together. The goal would be to create an automated system that can assemble 10 bearings/minute.</p><p>Current Assembly Method: The outer race has a single axial fracture in the outer race The ball is pushed into the outer race with brute force to assemble the bearing together Causes damage to inner and outer race “Snapback” can cause cracks Abrasion to finish of self-lubricating liner</p><p>Last Year’s Task: [1] Reduce stress, [2] Eliminate “snap back” & scratches on inner race, [3] Proof of Concept</p><p>Design Considerations: [1] Cost, [2] Safety, [3] Ease of Use, [4] Adjustability </p><p>Design Parameters: Bearing opening force: ~ 800lbf Coefficient of friction = 0.14 Factor of safety = 2.0 Clamping Force: ~5700lbf Within Budget Able to Fabricate</p><p>2012 – 2013 Goals: 1. Improve last year’s concept bringing it up to a production level piece of equipment 2. Automate the feeding of outer rings and balls such that the automated machine will assemble a minimum of 10 bearings/minute.</p>
Details
-
File Typepdf
-
Upload Time-
-
Content LanguagesEnglish
-
Upload UserAnonymous/Not logged-in
-
File Pages2 Page
-
File Size-