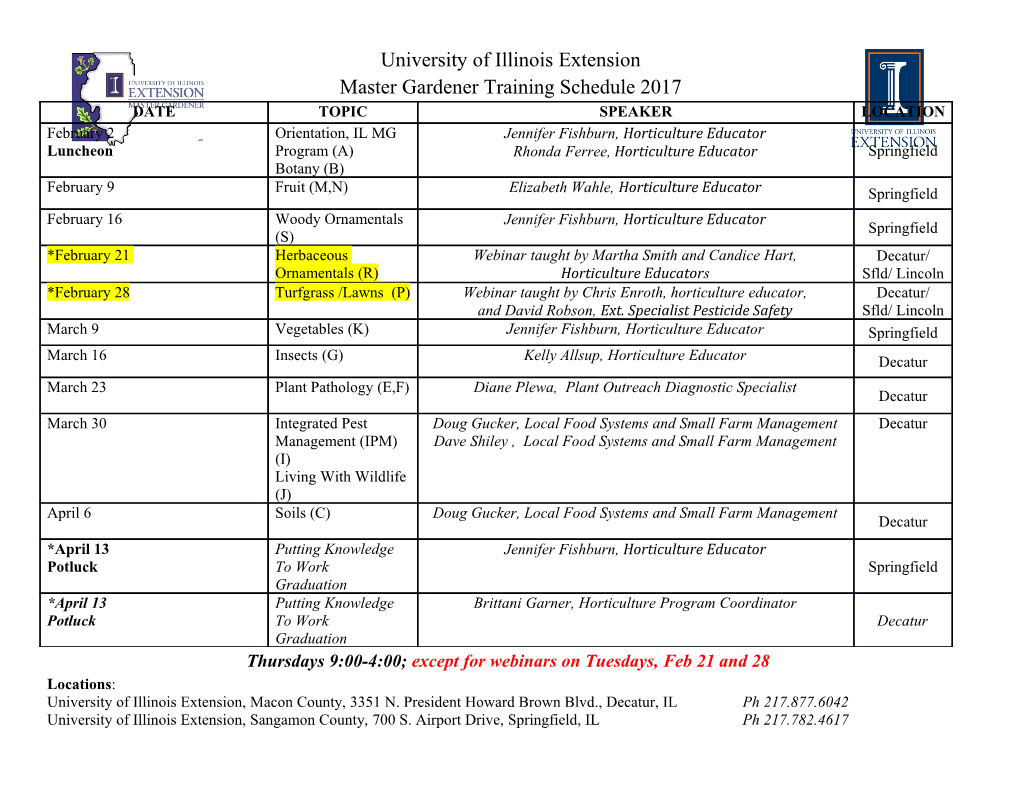
<p>Memorial Hermann Best Practices July, 2013</p><p>SECTION 28 05 00 COMMON WORK RESULTS FOR ELECTRONIC SAFETY AND SECURITY</p><p>PART 1 - GENERAL</p><p>1.01 WORK INCLUDED</p><p>A. Basic materials and methods, along with Division 1, General Provisions, that are applicable to Division 28 sections.</p><p>B. Drawings and general provisions of the contract, including General and Supplementary Conditions and Division 1 specification Sections apply to all Division 28 sections.</p><p>1.02 QUALITY ASSURANCE</p><p>A. Comply with applicable local, state, and federal codes.</p><p>B. Warrant Work against faulty material or Workmanship in accordance with Division 1. If the Project is occupied or the systems placed in operation in several phases at the request of the Owner, then the warranty of each system or piece of equipment used, shall begin on the date each system or piece of equipment was placed in satisfactory operation and accepted as such, in writing, by the Owner. The use of building equipment for temporary service and testing does not constitute the beginning of the warranty.</p><p>C. Equipment and material provided under this Division shall be periodically inspected and serviced by competent technicians. This function becomes the responsibility of the Owner when the system is accepted by the Owner. The one year material and Workmanship warranty is not intended to supplant normal inspection or service and shall not be construed to mean the Contractor shall provide free service for normal maintenance items due to normal use, nor to correct without charge, breakage, maladjustment, and other trouble caused by improper maintenance.</p><p>D. Upon completion of contract and progressively as work proceeds, clean-up and remove dirt, debris and scrap materials. Maintain premises neat and clean. Protect and preserve access to energized equipment at all times. Clean items with factory finishes. Touch-up minor damage to surfaces; refinish entire piece of equipment when sustained major damage. Use only factory supplied paints of matching color and formula. Schedule an off-hour shutdown of all electrical system equipment during the 2-week period preceding substantial completion.</p><p>1.03 REFERENCES</p><p>A. Perform Work specified in Division 28 in accordance with standards listed below of the latest applicable edition adopted by the authority having jurisdiction. Where these Specifications are more stringent, they shall take precedence. In case of conflict, obtain a decision from the Design Professional,. 1. NFPA-20: Standard for Installation of Stationary Pumps for Fire Protection 2. NFPA-72: National Fire Alarm Code 3. NFPA 92A: Standard for Smoke Control Systems Utilizing Barriers and Pressure Differences 4. NFPA 92B: Standard for Smoke Management Systems in Malls, Atria, Large Areas 5. NFPA 96: Standard for the Installation of Equipment for the Removal of Smoke and Grease-Laden Vapors from Commercial Cooking Equipment 6. NFPA-101: Life Safety Code 7. NFPA 110: Standard for Emergency and Standby Power Systems 8. ANSI-A17.1: Elevators, Dumbwaiters, Escalators and Moving Walks 9. ANSI Handicapped Code-A117.1</p><p>COMMON WORK RESULTS FOR ELECTRONIC SAFETY & SECURITY 28 05 00 - Page 1 Memorial Hermann Best Practices July, 2013</p><p>10. IBC: International Building and Fire Codes, 2006 Edition with City of Houston Amendments 11. All applicable Occupational Safety and Health Administration (0SHA) Publications, Rules and Regulations 12. Americans with Disabilities Act (ADA) 13. NFPA 20: Standard for the Installation of Centrifugal Fire Pumps. (1999) a. AIA Gidelines (2006) 14. Texas Department of State Health Services (TDSHS) - Hospital Licensing Standards 15. Special Regulations, supplement and amendments of the State and/or local authorities having jurisdiction</p><p>1.04 RELATED WORK SPECIFIED UNDER OTHER DIVISIONS</p><p>A. Field painting, except such painting as is required to maintain shop coat painting and factory finish painting.</p><p>B. Flashing of conduits into roofing and outside walls.</p><p>C. Heating, ventilating, and air conditioning equipment.</p><p>D. Fireproofing</p><p>E. Elevators</p><p>F. Automatic Doors</p><p>G. Cutting and patching for Work, except for errors and omissions under this Division.</p><p>1.05 OWNER FURNISHED INFORMATION</p><p>A. To the extent the Owner has performed and made available as Owner Furnished Information an Infection Control Risk Assessment (ICRA), the Contractor shall execute all requirements of the Contract Documents in accordance with the ICRA, and shall perform and provide all labor, materials and supervision to execute the specific infection control measures identified therein.</p><p>B. The Contract Documents do not necessarily depict all the work required by the ICRA, nor are the Contract Documents responsible for the information contained in the ICRA. The Contractor shall request, and obtain if available, the Owner's ICRA documentation, become familiar with its requirements and perform all work accordingly.</p><p>1.06 SUBMITTALS</p><p>A. Comply with provisions of Division 01.</p><p>B. Submit product data, equipment details, capacities, and shop drawings as specified in sections of this Division.</p><p>C. Submit fire alarm point-to-point drawings with product data submission.</p><p>1.07 OPERATING AND MAINTENANCE MANUALS</p><p>A. Provide manuals in accordance with Division 01.</p><p>B. In addition to required submittals, include copies of all test reports required in Part 3, "Execution" of section 26 05 00.</p><p>COMMON WORK RESULTS FOR ELECTRONIC SAFETY & SECURITY 28 05 00 - Page 2 Memorial Hermann Best Practices July, 2013</p><p>C. Provide completed warranty certificates for systems and equipment.</p><p>D. Provide tabulation of overload heaters, including each motor identified, nameplate data and overload heater part number.</p><p>E. Copies of final reviewed submittals indicating all model numbers, serial numbers, cut sheets, and all performance criteria on furnished equipment shall be included. Provide PDF format copy of all final approved submittals. PDF shall be bookmarked per section and per piece of equipment.</p><p>1.08 DELIVERY AND STORAGE</p><p>A. Insofar as possible, deliver items in manufacturer's original unopened packaging. Where this is not practical, cover items with protective materials to keep them from being damaged. Use care in loading, transporting, unloading, and storage to keep items from being damaged.</p><p>B. Store items in a clean dry place and protect from damage. Evidence of damage from water or other contaminants will be cause for rejection.</p><p>1.09 RECORD DRAWINGS</p><p>A. Comply with provisions of Division 01.</p><p>B. Provide record drawings that illustrate the work of Division 28 as finally constructed. Deliver record drawings to the Architect in both reproducible hard copy and Auto CAD format and PDF format on CD Rom or DVD. Also provide PDF format electronic copies of permit set with all revisions and RFI responses noted. Set shall include all architectural, civil, structural, mechanical, electrical, plumbing, low voltage, food service and all other vendors issued with the project. Provide PDF format specification set with all revisions and RFI responses noted. All PDF sets shall be bookmarked per phase, division and per drawing or specification section. A drawing change log shall be provided listing each drawing and all drawing issues including all addendums, clarifications and change orders. Log shall indicate</p><p>C. Record drawings shall reflect all changes made to the Contract Documents, whether generated by addenda, change orders, or field conditions. Maintain a daily record of these changes and keep current set of drawings showing these changes.</p><p>D. Deliver record drawings to Architect within 30 days of Substantial Completion.</p><p>PART 2 - PRODUCTS</p><p>2.01 MATERIALS AND EQUIPMENT</p><p>A. Equipment and materials furnished shall be listed by UL or other nationally accredited testing laboratory where available. When listing is not available for a piece of equipment, it shall be submitted in accordance with Drawings and Specifications and shall be approved by the authorities having jurisdiction.</p><p>B. Specifications and Drawings indicate name, type and/or catalog number of materials and equipment to establish standards of quality. Submittals shall be based on the standards specified. The standards should not be construed as limiting competition.</p><p>C. If materials and equipment other than specified herein are intended to be submitted, a letter providing a list of all the suggested alternates by section number, brand and series or model shall be submitted to the prime Design Professional for review and approval. Submit in accordance with Division 1 or 14 days prior to bids or final pricing are to be submitted.</p><p>COMMON WORK RESULTS FOR ELECTRONIC SAFETY & SECURITY 28 05 00 - Page 3 Memorial Hermann Best Practices July, 2013</p><p>2.02 WALL AND CEILING ACCESS PANELS</p><p>A. Style and type as required for material in which installed. 1. Size: 16" X 16" minimum, as indicated, or as required to allow inspection, service and removal of items served. 2. 14 gauge minimum sheet metal for doors, 16 gauge frames of cadmium-plated or galvanized construction. Doors shall have expanded plaster rings where located in plaster walls or flanged finish where located in drywall or block construction. 3. For all doors installed outside, in ambient conditions, in wet areas, or in areas of high humidity, door shall be aluminum construction. Areas included, but not limited to, are outside air plenums, unconditioned penthouses, bathrooms, kitchens, central sterile areas, and areas adjacent to sterilizers. Door shall be a minimum of 1/8” thick aluminum with ¼” extruded aluminum frane with mitered and welded corners. Hinge shall be continuous stainless steel. 4. Panels shall have spring hinges with screwdriver locks in non-public areas. Key lock, keyed alike, for panels in public areas. 5. Prime painted or rust inhibitive paint finish. 6. UL labeled when in fire-rated construction, 1 1/2 hour rating. 7. Provide in walls, floors, and ceilings to permit access to all equipment and junction boxes. 8. Furnish and locate access panels under this Division. Coordinate with trades who are responsible for building system in which panels are to be installed. 9. Acceptable manufactures: Milcor, Nystrom, Karp, J.L. Industries, or Williams Brothers. Use panels equal to Milcor Style M for masonry and drywall construction; equal to Milcor Style K for plastered masonry walls and ceilings. Stainless steel panels shall be used in ceramic tile or glazed structural tile. For aluminum doors: Micor Style CT, downward swing door.</p><p>PART 3 - EXECUTION</p><p>3.01 COORDINATION</p><p>A. Install equipment in accordance with manufacturer's recommendations. Where conflicts occur between Contract Documents and these recommendations, request a ruling before proceeding with such Work.</p><p>B. Visit site and observe conditions under which work must be performed. No subsequent allowance will be made because of error or failure to obtain necessary information to completely estimate and perform work required by these documents.</p><p>C. Examine Specifications and Drawings to be familiar with items which require system connections and coordination. Electrical Drawings are diagrammatic and shall not be scaled for exact sizes.</p><p>D. Prior to commencement of installation, prepare coordination drawings for work under this division, as specified in Division 1 and as called for herein. Coordinate work in full cooperation with persons performing work under other divisions, including but not limited to mechanical, plumbing, fire protection, telecommunication and miscellaneous steel to develop these coordination drawings that will serve as the agreed upon plan for a coordinated installation of work for all trades. Include system equipment, conduit racks and conduits 2" and larger on drawings confirming coordination with other trades. Incorporate the information onto the coordination drawings required under Division 1, 21, 22, 23, 26, 27 and 28 to develop master coordination drawings. Account for lighting fixture depths in the coordination. Inform Design Professional of conflicts that cannot be resolved.</p><p>E. Drawings are not to be submitted to Engineer. Submit a copy to the General Contractor and keep a copy on site for references. Notify design professional of conflicts that cannot be resolved. COMMON WORK RESULTS FOR ELECTRONIC SAFETY & SECURITY 28 05 00 - Page 4 Memorial Hermann Best Practices July, 2013</p><p>F. Coordination Drawings shall be prepared to include the following: 1. Drawn to a scale of ¼” = 1’-0”. 2. Room dimensions 3. Sheet size matching contract documents. 4. Show equipment, columns, and beams. 5. Junction and pull boxes. 6. Concrete pad and foundation layouts including anchor bolt and sleeve locations. 7. Wall mounted equipment. 8. Conduit 2” and larger, with elevations from finished floor to bottom of conduit. 9. Space allocation for conduits and cable trays. 10. Ceiling height.</p><p>3.02 FEES AND PERMITS</p><p>A. Obtain and pay for all necessary permits and inspection fees required for electrical installation.</p><p>3.03 DEMOLITION</p><p>A. Visit the site before submitting a bid to observe existing conditions.</p><p>B. Work in existing buildings shall be scheduled well in advance with the Owner. Work shall be performed at such times and under such conditions as suit the convenience of the Owner. Plan the Work to minimize disruption of normal operations. Notify Owner before any circuit is de- energized in occupied areas.</p><p>3.04 CUTTING AND PATCHING</p><p>A. Comply with provisions of Division 01.</p><p>B. Repair or replace routine damage caused by cutting in performance of Work under this Division.</p><p>C. Correct damage caused due to installation of electrical Work.</p><p>D. Holes cut through floor slabs shall be core drilled with drill designed for this purpose. All openings, sleeves, and holes in slabs between floors shall be properly sealed, fire proofed and water proofed.</p><p>E. Holes cut through walls shall be drilled or cut with tools designed for the purpose. All openings, sleeves and holes in walls that extend to underside of floor above shall be properly sealed and fire proofed.</p><p>F. Repairs shall be performed with materials which match existing materials and be installed in accordance with appropriate sections of these Specifications.</p><p>G. Contractor shall not be permitted to cut or modify any structural members without the written permission of the Design Professional.</p><p>3.05 TRENCHING, EXCAVATION, BACKFILLING, AND REPAIRS</p><p>A. Comply with provisions of Division 31.</p><p>B. Provide trenching, excavation, and backfilling necessary for performance of Work under this Division.</p><p>COMMON WORK RESULTS FOR ELECTRONIC SAFETY & SECURITY 28 05 00 - Page 5 Memorial Hermann Best Practices July, 2013</p><p>C. Provide sheathing, shoring, dewatering, and cleaning necessary to keep trenches and their grades in proper condition for Work to be carried on.</p><p>D. Trenching and excavation shall be unclassified. No extra will be paid in event that rock is encountered.</p><p>3.06 FOUNDATIONS AND PADS</p><p>A. Provide concrete foundations and pads for equipment per the requirements Division 03. Locate and size foundations, pads, and anchor bolts as required for equipment in this Division.</p><p>3.07 INFECTION CONTROL REQUIREMENTS</p><p>A. Coordinate with the Owner the exact requirements for the infection control measures to be executed and performed during the course of this Project.</p><p>B. Prior to execution, present to the Owner for approval a written execution plan for each infection control measure.</p><p>C. Coordinate infection control measures as needed with all other trades and disciplines.</p><p>D. Provide documentation of infection control measures to the Owner, as required and specified in the ICRA.</p><p>END OF SECTION</p><p>COMMON WORK RESULTS FOR ELECTRONIC SAFETY & SECURITY 28 05 00 - Page 6</p>
Details
-
File Typepdf
-
Upload Time-
-
Content LanguagesEnglish
-
Upload UserAnonymous/Not logged-in
-
File Pages6 Page
-
File Size-