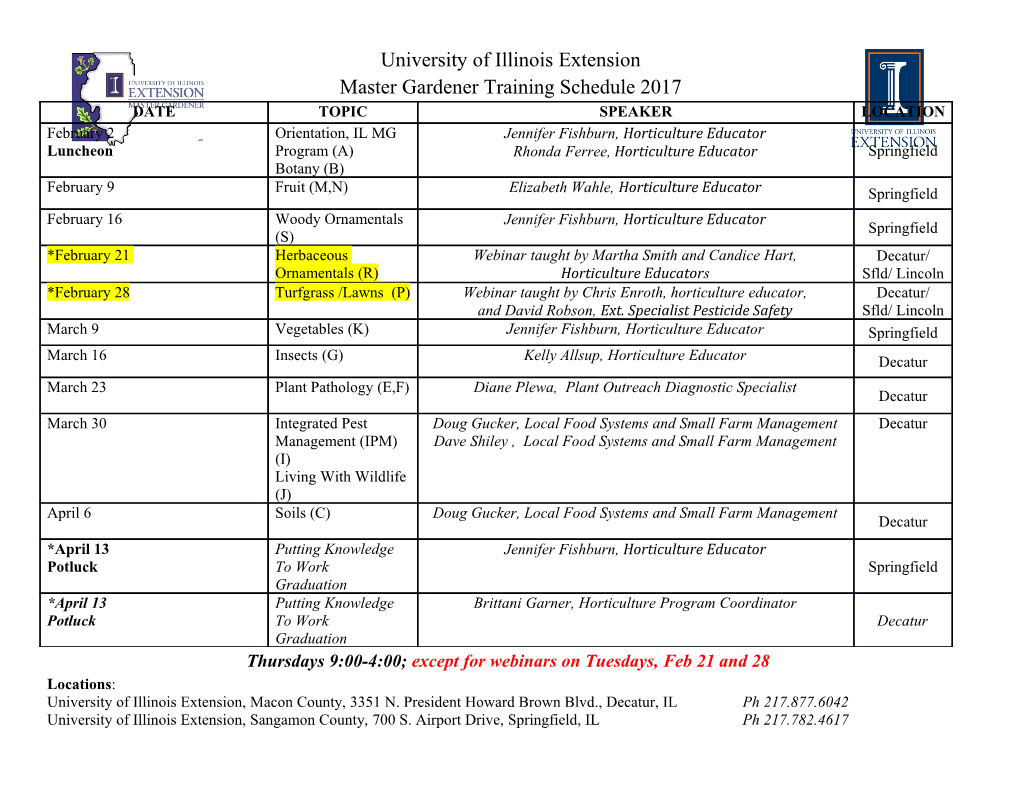
<p> Automated Oiling System P08351 – Concept Design Review (Pre-read)</p><p>Team Member Discipline Role Email address Jim Taylor IE Guide [email protected] John Kaemmerlen IE Consultant [email protected] John Bonzo IE Consultant [email protected] Matt Zapotoski IE Project Lead [email protected] Sharif Hdairis CE CE/EE support [email protected] Joe Jennings ME ME support [email protected] Bob Shackelford ME ME support [email protected] T able Of C ontents 1.0. Introduction ….…..……………………………………………………………. 3 2.0. Customer Needs ….….….………………………………………………………… 4 3.0. Specifications .….……………………………………………………………….. 5 4.0. External Search Results …………………………………………………….6 5.0. Concept Selection …………………………………………………………….7 5.1 Mechanical Engineering 5.1.1 Loading/ Unloading Mechanism …………………………….8 5.1.2 Oil Application …………………………………………………….9 5.1.3 Cleaning process (before application of oil) ……………………10 5.1.4 Removal of excess oil ……………………………………………11 5.2 Electrical Engineering ……………………………………………………13 5.2.1 Signals ……………………………………………………………14 5.2.2 Variable Speed Drive System ……………………………………14 6.0. Proposed Integrated System ……………………………………………………16 7.0. Future agenda ……………………………………………………………………17 1.0 I ntroduction </p><p>The focus of this project will be the automation of the current manual oiling operation of the toolholding assembly process. This purpose of this operation is to fully lubricate the toolholder, hence preventing the oxidation and rusting of the product, while at the same time improving its appeal aesthetically. Parlec currently applies oil to its parts by hand through a rigorous process involving between two and three operators. The inconsistency of this process has resulted in part quality that does not meet customer expectations. In response, Parlec would like a machine to automate the process. The subsystems of this project were identified and listed. The goal of this project is to design and fabricate a machine that will integrate all of the subsystems illustrated below.</p><p>FUNCTIONAL DIAGRAM INPUTS OUTPUT</p><p>COMPRESSED AIR</p><p>REMOVE OILED TOOL LOADING CLEANING APPLY OIL UNLOADING HOLDER EXCESS OIL TOOL HOLDER</p><p>VARIABLE CONTROLS SIGNALS SPEED DRIVE</p><p>ELECTRIC ENERGY</p><p>Figure 1.1 2.0 C ustomer N eeds </p><p>The establishment and clarification of customer needs is a crucial part of the concept development process. A meeting with the customer was required in order to generate a list of needs. The customer needs were then translated from the voice of the customer to an engineering voice stating what the team will attempt to achieve in order to satisfy each of the individual needs.</p><p>N1.0 The product must be safe </p><p>N1.1 The product must meet OSHA standards</p><p>N1.2 The product must be safe for users and bystanders</p><p>N2.0 The product must be durable and robust</p><p>N3.0 The product will improve movement of parts after laser operation</p><p>N3.1 The product will promote continuous flow </p><p>N3.2 The product will help reduce the amount of bottlenecking</p><p>N4.0 Maintain cosmetic standards of foreign markets</p><p>N4.1 The product ensures high quality, fully oiled parts</p><p>N4.2 The product cannot damage tool</p><p>N5.0 Human application of work fully removed</p><p>N5.1 Amount of human error minimized</p><p>N6.0 The end product cannot exceed budget</p><p>N7.0 The end product will be attractive to customer</p><p>N8.0 The product will be easy to operate 3.0 E ngineering S pecifications </p><p>After the customer needs are defined, it is necessary to translate the needs into quantifiable metrics that the design team can use to establish a design that will satisfy all of the needs of the customer. The specifications developed for the automated oiling system are shown in the figure below. The goal of the team is to satisfy the all of these specifications, understanding that some tradeoff might be necessary due to constraints such as money, space, and time.</p><p>Customer Specification Unit of Target Need Design Specification Number measure value affected SAFETY: S1 1.1, 1.2 proper protective guards where necessary subj. yes S2 1.2 closed compartments at beg and end subj. yes S3 1.1,1.2 emergency stop buttons number at least 2 DURABILITY: S4 2.0 The machine will be transportable subj. yes S5 2.0,3.1,3.2 able to support weights of most common toolholders lbs 40 OPERATION: S6 3.1, 3.2 Able to process 1400 parts in an 8 hr shift units / hr 200 S7 3.1,3.2 variable speeds feature subj. yes S8 3.1,3.2 two different load/unload stations subj. yes S9 3.1,3.2 will handle most frequently produced parts Diam (in) Up to 7 QUALITY: S10 4.2 part tolerances will be maintained/unaffected inch 60 millionths S11 4.1 Percentage of part that is oiled % 100 S12 4.1 The product has to consistently lubricate the tools subj. yes S13 5.1 manually loadable/unloadable subj. yes S14 5.1 oiling process is completely automated subj. yes BUDGET: Design and fabrication of the product will be less than S15 6.0 budget $ 20,000 PHYSICAL CHARACTERISTICS: S16 7.0 will have Parlec label on it subj. yes S17 7.0 will fit within floor constraints ft x ft 15 x 8 S18 8.0 intuitive control box (es) subj. yes FIGURE 3.1: QFD Diagram 4.0 I nternal S earch R esults </p><p>Once the metrics were reviewed and finalized, the team began to examine each subsystem individually. The possible alternatives were gathered, and a preliminary breakdown containing the associated positives and negatives of each possible solution were listed.</p><p>SEARCH SUBFUNCTION RESULTS POSITIVES NEGATIVES SIGNALS Digital simple to use more susceptible to noise Analog can filter out noise difficult to design cheaper, more efficient, eases into AC drive+AC motor+µcontroller acceleration shorter engine life, contactors provide full or no power, VSD System DC motor+Contactor+µcontroller expensive</p><p> custom DC drive + DC engine expensive, may be too intricate for the process at hand easy to place part, simple, cheap, most Hooks flexible capacity, prone to damage part, strength? part versatility (size), offers strength and LOADING Racks stability bulky, will require/ take up space</p><p>Fixture flexible in design, holds parts more securely cost, additional labor/ increased setup time</p><p>Air available in facility, low risk of damaging part expensive, will contaminate air, noisy</p><p>Brushes cheap, available, single could fall apart, not thorough coverage, bristles on part? CLEANING Rags cheap, available, single must be maintained, manually operated messy, maintained, lengthen process, may not remove all Solvent/Chemicals will remove all debris debris</p><p>APPLY OIL </p><p>Oil cheap, uniform coating, easily removed messy, requires special packaging, requires time to drain oil coating no shelf life, provides durable, protective material Powder surface on permanently, un-uniform coat NICKEL Coating very expensive, lasts forever </p><p>Submerge simplest uses excess oil, may not coat part completely</p><p>Spray more uniform coat contaminates air, requires energy, may not fully coat part coating process Pour sloppy, difficult to appl full application, slow Tumble more thorough (prevent air pockets) requires additional equipment, potential to damage part</p><p>Brush cheap, versatile bristles wear out, may brush off onto part</p><p>Spin quick, reliability of result, versatile expensive, potentially dangerous, additional equipment req’d</p><p>Hang/Dip simplest, cheapest slowest, requires space REMOVE EXCESS OIL Wipe simplest, cheapest slow, unreliable Air quick, consistent, low maintenance req’d messy, noisy, expensive</p><p>Heat decreases viscosity costs money to produce heat easy to place part, simple, cheap, most Hooks flexible capacity, prone to damage part, strength? UNLOADING Racks part versatility (size), offers strength/stability bulky, will require/ take up space Fixture flexible in design, holds parts more securely cost, additional labor/ increased setup time</p><p>Storage provides extra time(manage/maintain flow) additional floor space required ENERGY Electric convenient, clean, requires no modifications High powered air expensive FIGURE 4.1: Preliminary solution analysis separated by subsystem</p><p>5.0 C oncept S election Concept Generation: With the customer needs defined and quantified, the subsystems contributing to the entire system were broken down and brainstorming exercises were conducted to generate possible solutions. In addition, internal searches were conducted, resulting in more results, as well as a more detailed analysis of each possible alternative. Pros and cons associated with each were developed, resulting in the unfeasible alternatives being removed as possible resolutions to the challenge at hand.</p><p> Concept Screening: With the remaining results, each was compared to one another through a screening process known as Pugh’s Method in which a list of selection criteria relevant to the success of the specific subsystem was developed. The different alternatives were scaled against a reference concept (any of the choices in which zeroes were input in each column) the other choices would then be compared to the reference concept and if better in regards to the selection criteria, a plus was input (and a minus for worst qualities).</p><p> Concept Scoring Each of the different criteria was then given weights (a total of 100%) based on their overall significance to successfully attain the needs associated with each individual subsystem. The objective of this method (expansion of Pugh’s method) is to narrow down the possible solutions to one or two concepts for each subsystem. This will then enable us to combine each of the possible solutions with one another to form different combinations for an integrated system. </p><p>Note: One downfall of this process is the uncertainties associated with choosing a non- representative set of criteria or incorrectly weighing individual criteria. In the unlikely event that this occurs, the result could be a compromise in the best possible solution for that particular subsystem.</p><p>5.1 M echanical E ngineering The mechanical concept development was divided into four main categories; loading/unloading the tool holders into the system, the application of oil, and the two cleaning processes before and after the oil application. Below are the separate categories pertaining to mechanical engineering have been broken down and expanded upon in separate sections. There are several challenges that will factor into the concept developed. The tool holders have various geometries, sizes, and mass that will bring forth difficulties in loading, cleaning, oiling, and transporting them throughout the system. The oil has a high viscosity will make it difficult to flow for application and the removal and excess. </p><p>5.1.1 L oading/ U nloading </p><p>Hooks, racks, form fitting fixtures, and magnets were all considered due to their associated qualities involving: ease of manufacture, availability, and cost effectiveness.</p><p>SUBFUNCTION SEARCH RESULTS POSITIVES NEGATIVES easy to place part, simple, linear, cheap, capacity, prone to damage Hooks most flexible part, strength</p><p> part versatility (size), bulky, will require/ take up Racks offers strength and space LOADING / stability UNLOADING flexible in design Fixture (custom), holds parts cost, additional labor/ more securely increased setup time</p><p>Magnets durable, part security part versatility? , cost</p><p>FIGURE 5.1.1: Preliminary analysis for loading/unloading mechanisms</p><p>Since the customer opted that the machine is loaded and unloaded manually, the choices analyzed for loading and unloading were inherently narrowed as choices such as robotic arms and a few others would have been otherwise considered. Fixture Loose fitting Tight fitting Selection Criteria Weight Hooks Magnets fixture fixture Pegs None durability 0.15 0 + 0 0 0 + part versatility 0.25 0 0 + - 0 + tolerance protection 0.5 0 0 0 + 0 - Fabrication cost 0.1 0 - - - - + Total 0 0.05 0.15 0.15 -0.1 0 FIGURE 5.1.2: Pugh’s matrix for different L/UL concepts</p><p>From the matrix, the results suggest that a tight or loose fitting fixture will be the better options. Magnets could be considered as an add-on feature, but are inadequate by themselves.</p><p>5.1.2 O il A pplication </p><p>The first and foremost objective of this sub function is to consistently oil the whole part. </p><p>SUBFUNCTION SEARCH RESULTS POSITIVES NEGATIVES uses excess oil, may not coat Dip simplest part completely</p><p> contaminates air, requires Spray more uniform coat energy to apply, may not coat part completely (air pockets) Apply sloppy, difficult to apply full Pour Oil application, slow more thorough requires additional equipment, Tumble (prevent air pockets) potential to damage part bristles wear out, may brush off Brush cheap, versatile onto part FIGURE 5.1.3: Preliminary analysis for oil application</p><p>Dipping the part in oil, spraying oil on the part, pouring oil over the part, tumbling or rotating the part about one axis while simultaneously submerging the part in the oil, and brushing oil on the part were initially all relevant choices.</p><p>Apply Oil Selection Criteria Weight Dip Pour Tumble Brush Spray Part versatility 0.15 0 - - - - speed 0.1 0 0 0 0 0 part coverage 0.4 0 - - - 0 running cost 0.05 0 - 0 - - maintenance 0.05 0 0 0 - - tolerance protection 0.25 0 0 - 0 0 Total 0 -0.6 -0.8 -0.65 -0.2 FIGURE 5.1.4: Pugh’s matrix for different oiling techniques</p><p>From the matrix, the results suggest that dipping (submerging) the part in oil would be the best option, followed by spraying. The other options bare a risk of poor part coverage and were inevitably rejected. </p><p>5.1.3 C leaning The goal of the cleaning process is to consistently remove any excess debris that may have not been removed from entire part. The next goal at hand is how accommodating the process is to a variety of different sized parts. Minimal changeovers are a preferred feature. </p><p>SUBFUNCTION SEARCH RESULTS POSITIVES NEGATIVES available in facility, low risk expensive, will contaminate air, Air of damaging part noisy could fall apart, not thorough Brushes cheap, available, single coverage, bristles on part? CLEANING must be maintained, manually Rags cheap, available, single operated messy, lengthen process Solvent/Chemicals will remove all debris (drying time req'd), may not remove all debris FIGURE 5.2.1: Preliminary analysis for cleaning strategies</p><p>Using compressed air to blow the excess oil off the part, a spongy type brush or rag to eradicate excess debris from the part, as well as the use of chemicals are all initial possibilities for cleaning the part before the oiling process. Cleaning Selection Criteria Weight Air Brushes Rags chemicals Part versatility 0.2 0 - 0 0 speed 0.2 0 0 0 - part coverage 0.4 0 - - 0 running cost 0.1 0 - 0 - - maintenance 0.1 0 - - - Total 0 -0.80 -0.5 -0.5 FIGURE 5.2.2: Pugh’s matrix for the different cleaning techniques</p><p>From the matrix, the results suggest that using compressed air to free the part of any remaining debris would be the best option, followed by rags. The other options bare a risk of inefficient part coverage and lack of part versatility</p><p>5.1.4 R emove E xcess O il </p><p>The purpose of the removing the excess oil process is to consistently remove any excess oil that may be remaining on the part. The secondary goals of this subsystem are to handle the most frequent parts that are manufactured within plant, as well ability to meet desired throughput. How effectively each alternative can reacquire the excess oil removed so that it may be recycled and reused is taken into consideration. </p><p>SUBFUNCTION SEARCH RESULTS POSITIVES NEGATIVES quick, reliability of expensive, potentially dangerous, Spin result, versatile additional equipment required</p><p>Hang/Dip simplest, cheapest slowest, requires space REMOVE Wipe simplest, cheapest slow, unreliable EXCESS OIL quick, consistent, low Air messy, noisy, expensive maintenance req'd</p><p>Heat decreases viscosity costs money to produce heat</p><p>FIGURE 5.2.3: Preliminary analysis for removal of excess oil</p><p>Using compressed air to blow the excess oil off the part, a spongy type brush or rag to eliminate the excess oil off the part, hanging the part and allowing the excess oil to simply drip, or using heat to attempt to dry or thicken some of the oil were all researched and considered. Heat was ruled out as an alternative in the first stage.</p><p>Remove excess oil Selection Criteria Weight Air Spin Wiping Drip Part versatility 0.2 0 0 0 0 speed 0.2 0 - 0 - part coverage 0.4 0 0 - 0 running cost 0.1 0 - 0 + maintenance 0.1 0 - - + Total 0 -0.4 -0.5 0 FIGURE 5.2.4: Pugh’s matrix for different removal techniques</p><p>Based on the results, the primary solutions appear to be the methods of compressed air and hand/drip to remove excess oil. </p><p>5.2 E lectrical E ngineering </p><p>The electrical components’ function is to ensure proper operation of the machine while providing an easy to use interface for the operator. The electrical system will be responsible for taking input from both the operator and the internals of the machine and determine what the machine will do by providing feedback to the user and sending control signals to the machine’s main drive and other internal components. The control system can be broken down into smaller subsystems: user input and feedback panel, internal sensor input and feedback, the processing unit, and an electric drive and matching motor. Of these components, it was necessary to pick out a couple of important design concerns to perform concept development on. The selected concerns were types of signals used for input/feedback, and the drive/electric motor combination.</p><p>Figure 5.2: Control System</p><p>5.2.1 S ignals </p><p>When considering the signals the processing unit will handle, it was necessary to weigh the pros and cons of the available two solutions, analog and digital. Due to the nature of the values transmitted, it was decided that a mix of analog and digital signals will be used.</p><p>SUBFUNCTION SEARCH RESULTS POSITIVES NEGATIVES SIGNALS Digital simple to use, Components are more no conversion required complex to process Must filter out noise. Fewer components, Must be converted Analog simpler elements into digital domain to process. FIGURE 5.3.1: Preliminary analysis for signal possibilities</p><p>5.2.2 V ariable S peed D rive S ystem </p><p>This component was selected because it is central to the machine’s smooth operation, and because it represents the area in which the designer has the least experience. After performing independent research, and consulting with academic faculty, the following drive/motor combinations cover all the concepts encountered.</p><p>SEARCH SUBFUNCTION POSITIVES NEGATIVES RESULTS Cheaper, better power AC Motor w/ prebuilt efficiency, easy to More expensive than custom drive drive replace parts and solution. maintain. Wiring and quality of drive AC Motor w/ custom Cheapest, better power components is lower. Harder to drive efficiency. interface with processing unit. VSD System Replacing drive is harder. Better acceleration, DC Motor w/ prebuilt comparable High power DC drives are very drive maintenance to expensive. AC/prebuilt expensive, harder to maintain and DC Motor w/ custom Better acceleration. replace parts, design time of drive custom drive. FIGURE 5.3.3: Preliminary analysis for VSD systems</p><p>It is expected that the solution combination will lean towards an AC/prebuilt drive, because the AC motors are cheaper, and using drives simplifies the design, increases reliability, and eases maintenance by utilizing off-the-shelf products. The criteria selected should reflect the main objective of the subsystem, which is to provide a reliable, durable, flexible driving power for the machine that is cost effective and has minimal maintenance efforts.</p><p>Drive System Selection Criteria Weight AC/Custom AC/prebuilt DC/prebuilt DC/custom fabrication cost 0.25 0 - - - maintenance cost 0.25 0 + 0 - reliability 0.2 0 + + 0 ease of implementation 0.2 0 + + 0 start/stop performance 0.1 0 0 + + Total 0 0.4 0.25 -0.4 FIGURE 5.3.4: Pugh’s matrix for the different systems</p><p>As anticipated, the systems with prebuilt drives are best suitable because they meet the desired specs more than combinations with custom controller circuitry; AC was preferred to DC due to the cost advantage, although its torque/acceleration is not as good as what DC can offer.</p><p>While the AC/Custom solution is not really a contender based on its raw score, it was included in the Integrated system, in order to examine it combined with different concepts of other subsystems, and perhaps realize unforeseen benefits not demonstrated by Pugh’s matrix.</p><p>6.0 I ntegrated S ystem </p><p>From the Pugh’s matrices of the individual subsystems, the top two choices selected were combined with the other top rated concepts to develop different integrated systems. Seven total possible arrangements were developed. Each was analyzed on a level of criteria drawn around the customer needs, thus focusing more on the specifications associated with the end product. </p><p> removing excess System loading/unloading cleaning apply oil oil VSD 1 hooks air dip air ac/prebuilt</p><p>2 tight fitting air dip air ac/custom</p><p>3 loose fitting rags spray air ac/prebuilt</p><p>4 hooks rags spray drip dc/prebuilt</p><p>5 tight fitting air spray drip ac/custom</p><p>6 loose fitting air dip drip dc/prebuilt</p><p>7 tight fitting air dip air ac/prebuilt FIGURE 6.1: Possible combinations for the final solution</p><p>Pugh's chart for possible systems</p><p>Criteria/ Machine # 1 2 3 4 5 6 7</p><p> ease of manufacture 0 - - - - 0 0</p><p> fabrication cost 0 - - - - - +</p><p> ease of use for user 0 + + 0 + + +</p><p> durability 0 + - - 0 + +</p><p> consistency 0 0 - - - 0 0</p><p> safe 0 + + 0 + + +</p><p> maintenance 0 - - - - + 0 TOTAL 0 0 -3 -5 -2 3 4 FIGURE 6.2: Pugh’s matrix for different system proposals</p><p>The results from the Pugh’s chart for the whole integrated system suggest that systems 6 and 7 are the legitimate possibilities. System 7 is the teams’ choice for the initial concept design. The only possibility that exists is using the unloading/loading mechanism from system 6 (loose fitting fixture vs. tight fitting fixture) A preliminary sketch of the system in mind is illustrated below. 7.0 Future Agenda </p><p>The basic concept was constructed using several concept development methods. To finalize this concept and to bring it into more detail, each component will undergo theoretical analysis and be tested ensuring that it will function as desired. This will consist of hand calculations, modeling, and prototyping. This is done to prevent risk of not having a fully functioning oiling system on time. These risks consist of the system operating too slowly, tool holders not being cleaned or oiled properly, components not sized properly, and the system not being safe.</p>
Details
-
File Typepdf
-
Upload Time-
-
Content LanguagesEnglish
-
Upload UserAnonymous/Not logged-in
-
File Pages17 Page
-
File Size-