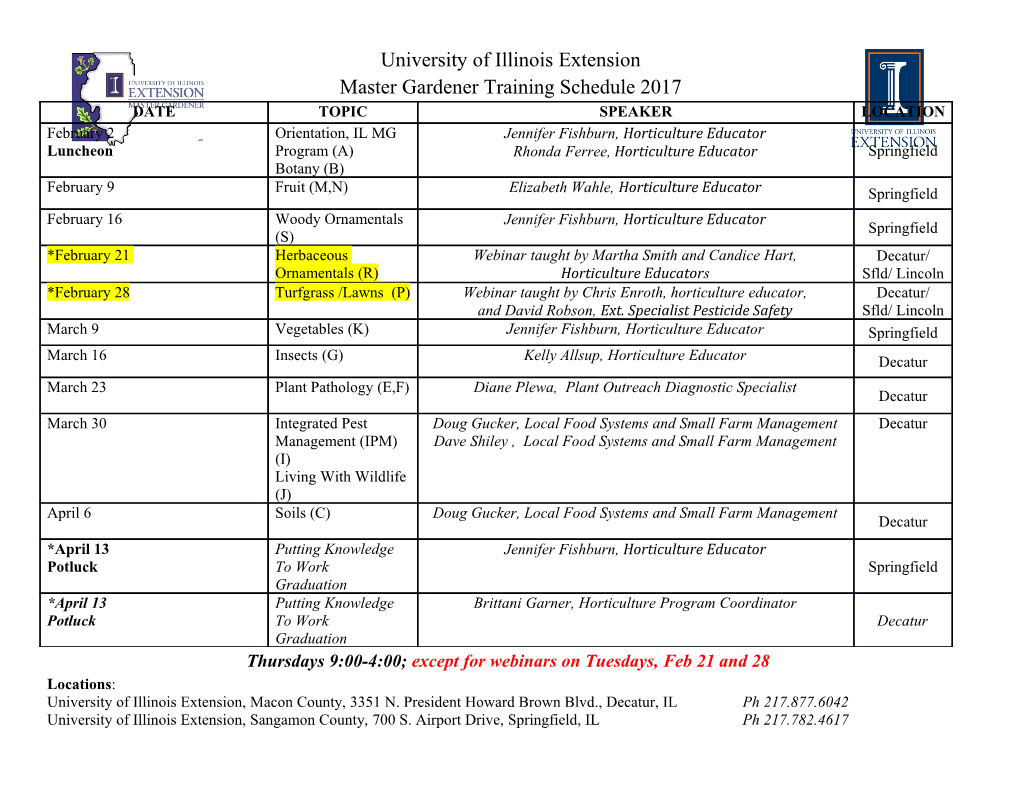
<p> Page 1 of 46 2006 SIDEWALK REPLACEMENT PROGRAM</p><p>FOR</p><p>OAKTON COMMUNITY COLLEGE DES PLAINES, ILLINOIS</p><p>Project Manual May, 2006 Page 2 of 46 PROJECT MANUAL</p><p>CONTRACT DOCUMENTS AND SPECIFICATIONS FOR CONSTRUCTION</p><p>2006 SIDEWALK REPLACEMENT PROGRAM</p><p>OAKTON COMMUNITY COLLEGE DES PLAINES CAMPUS</p><p>PROJECT ENGINEER GEWALT HAMILTON ASSOCIATES, INC. 850 FOREST EDGE DRIVE VERNON HILLS, ILLINOIS 60061 (847) 478-9700</p><p>MAY, 2006</p><p>Address All Communications Regarding This Work To:</p><p>Steven D. Berecz, P.E. Gewalt-Hamilton Associates, Inc.</p><p>Project Manual: </p><p>Copy Number: Page 3 of 46 OAKTON COMMUNITY COLLEGE 2006 SIDEWALK REPLACEMENT PROGRAM</p><p>INVITATION FOR BIDS</p><p>Sealed bids for the 2006 Sidewalk Replacement Program will be received at the Purchasing Office, Room 1540, Oakton Community College, 1600 E. Golf Road, Des Plaines, Illinois until 2:00 P.M. local time, Thursday, June 8, 2006. Bids shall be addressed to Doreen Schwartz, Director of Business Services. All Bids will be publicly opened at that time and read aloud.</p><p>Bid specifications and contract documents will be available after 2:00 PM on Thursday, May 18th. Bidders are encouraged to visit the College’s website at www.oakton.edu for bid specifications. (click on Faculty and Staff, click on Business Services, click on Purchasing, click on Current Bids and Proposals). Specifications may also be picked up at Oakton Community College, Purchasing Office, Room 1540, 1600 East Golf Road, Des Plaines, IL 60016. There is a $10.00 fee for pickup of the contract documents.</p><p>A mandatory pre-bid meeting will be held at 2:00 P.M., Thursday, May 25, 2006 at Oakton Community College, Purchasing Office, Room 1540 at 1600 E. Golf Road, Des Plaines, Illinois 60016. Bidders can also pick up contract documents at this time for a $10.00 fee. </p><p>The project involves the removal and replacement of concrete sidewalk and concrete curb and gutter at various locations around the Des Plaines campus.</p><p>When submitting a bid, all bidders must include a resume of similar projects performed; enumerated as to location, type of work, approximate completion date, and supervising engineering or architectural firm. Additionally, all bidders will submit a list of equipment owned by, or available to them, for the efficient pursuance of the project.</p><p>A Special Provision for time of completion is included with the contract.</p><p>Bid security in the form of either a Bid Bond, Bank Cashier's Check or Certified Check for the amount of 10% of base bid made payable to Oakton Community College shall accompany the bid.</p><p>The College reserves the right to reject any and all bids and bidders and to waive all technicalities. All bids submitted shall be valid for a period of sixty (60) days. </p><p>Dated in Des Plaines, Illinois, May 15, 2006.</p><p>Oakton Community College Director of Business Services 1600 E. Golf Road Des Plaines, IL 60016 Page 4 of 46</p><p>INSTRUCTIONS TO BIDDERS Page 5 of 46 INSTRUCTIONS TO BIDDERS</p><p>1. CONTRACT DOCUMENTS:</p><p>1.1 Before submitting a bid, each bidder shall carefully read and examine all the Contract Documents, consisting of the Following:</p><p>2. BID FORM: 2.1 Only proposals which are made out upon the regular proposal form will be considered. All bids must be signed by the Bidder or his authorized representative, and any corrections to entries made on the bid forms, shall be initialed by the person signing the bid.</p><p>2.2 Bidders must quote on all items appearing on the bid forms. Failure to quote on all items shall disqualify the bid.</p><p>2.3 Modifications to bids already submitted will be accepted if submitted prior to the time fixed in the Invitation for Bids. Modifications shall be submitted as such and shall not reveal the total amount of either the original or revised bid.</p><p>2.4 Bids received after the time indicated shall be returned unopened.</p><p>2.5 Each bid shall be addressed to the Oakton Community College and shall be delivered to the Purchasing Office, Room 1540 of the College on or before the day and hour set for opening the bids in the Invitation to Bidders. The bid shall be enclosed in a sealed nine inch (9") by twelve inch (12") envelope bearing the title of the work, the name of the Bidder, and the date and hour of the opening. It is the sole responsibility of the Bidder to see that his bid is received in proper time.</p><p>2.6 Neither the Oakton Community College nor the Engineer will be responsible for oral instructions.</p><p>2.7 Each Prime Contractor shall furnish with his bid, the following information:</p><p>2.7.1 Name of Bonding Company to be used.</p><p>2.7.2 Letter from bonding company signifying willingness to furnish a performance bond in the amount of the bid submitted. Bonding company must be listed in the current edition of Department Circular #570 of Accounts Surety Bond Branch entitled, "Companies Holding Certificate of Authority as Acceptable Sureties or Federal Bonds and As Acceptable Reinsuring Companies"</p><p>2.7.3 Bid security in the form of either a Bid Bond, Bank Cashier's Check or Certified Check for the amount specified in Article 102.09 of the Standard Specifications (IDOT-SSRBC) made payable to the Oakton Community College. Page 6 of 46 3. BONDS:</p><p>3.1 A Performance Bond and Labor and Materials Payment Bond shall be furnished by the selected Contractor from a bonding company with a Best Rating Service A-/6 or better, in the amount of 100 percent of the contract price at the time of signing the formal Agreement.</p><p>4. EXAMINATION OF DRAWINGS, SPECIFICATIONS AND SITE OF WORK:</p><p>4.1 Bidders are cautioned to be aware of the conditions under which the Work, the structure of the ground, and underground conditions that may be encountered in the progress of the Work and all other relevant matters which may affect the prices submitted for the Work to be performed, so that his bid will cover all expenses in connection therewith. Oakton Community College does not guarantee the existence, non-existence, or location of any subsurface material which may be shown on the plans. The inclusion of such structures or materials is based on the best data available, but should not be regarded as conclusive.</p><p>4.2 If awarded the Contract, the Bidder will not be allowed extra compensation by reason of any matter or thing concerning which such Bidder might have fully informed himself, because of his failure to have done so prior to the bidding.</p><p>4.3 The submission of a bid shall be construed as conclusive evidence that the Bidder has made such examination.</p><p>5. WITHDRAWAL OF BIDS:</p><p>5.1 Bids may be withdrawn at any time prior to opening upon written request of the Bidder. Negligence on the part of the Bidder in preparing his bid shall not constitute a right to withdraw bid subsequent to the Bid Opening.</p><p>5.2 A party who has quoted prices to a Bidder is not hereby disqualified from quoting prices to other Bidders or from submitting a direct bid on his own behalf.</p><p>5.3 No Bidder may withdraw his bid for a period of sixty (60) days after the date set for the opening, and all bids shall be subject to acceptance by the College during this period.</p><p>6. INTERPRETATION OF CONTRACT DOCUMENTS PRIOR TO BIDDING:</p><p>6.1 If any Bidder is in doubt as to the true meaning of any part of the plans, specifications or other Contract Documents, he shall request an interpretation from the Project Engineer prior to bidding. The Project Engineer shall give a written interpretation of the matter in question by issuing an "Addendum" and sending same to each person receiving a set of Contract Documents. Only a written interpretation shall be binding and no Bidder shall rely upon any verbal interpretation or correction given by any other method. Page 7 of 46 6.2 Quantities for materials on the proposal forms and elsewhere in the Plans and Specifications have been computed from plan dimensions and specification requirements, rather than actual field measurements. Each bidder must verify or establish quantities to his own satisfaction and submit a total bid sufficient to cover all of the work outlined in the contract Documents. </p><p>7. AWARD OR REJECTION OF BIDS:</p><p>7.1 Before an award is made of the Contract to a contractor, said Contractor may be required to, upon request of the College or Project Engineer to furnish information concerning his performance record and his capacity to complete the work in an efficient and timely manner.</p><p>8. EXECUTION OF AGREEMENT:</p><p>8.1 The Bidder to whom the Contract is awarded will, within ten (10) days after notice of award and receipt of Agreement forms from the College sign and deliver to the College all required copies of the Agreement.</p><p>8.2 At, or prior to, delivery of the signed Agreement, the Contractor shall deliver to the Project Engineer Policies of Insurance or Insurance Certificates as required by the Contract Documents. All policies or certificates of insurance shall be approved by the College and the Project Engineer before the successful Bidder may proceed with the Work.</p><p>9. EQUAL EMPLOYMENT OPPORTUNITY:</p><p>9.1 In the event of the Contractor's non-compliance with any provision of this Equal Employment Opportunity Clause, the Illinois Fair Employment Practices Act or the Fair Employment Practices Commission's Rules and Regulations for Public Contracts, the Contractor may be declared nonresponsible and therefore ineligible for future Contracts or subcontracts with the State of Illinois or any of its political subdivisions or municipal corporations, and the Contract may be cancelled or voided in whole or in part, and such other sanctions or penalties may be imposed or remedies invoked as provided by statute or regulation. 9.2 During the performance of this Contract, the Contractor agrees as follows: 9.2.1 That, he will not discriminate against any employee or applicant for employment because of race, color, religion, sex, national origin or ancestry; and further that he will examine all job classifications to determine if minority persons or women are underutilized and will take appropriate affirmative action to rectify any such underutilization. Page 8 of 46 9.2.2 That, if he hires additional employees in order to perform this Contract, or any portion hereof, he will determine the availability (in accordance with the Commission's Rules and Regulations for Public Contracts) of minorities and women in the area(s) from which it may reasonably recruit and he will hire for each job classification for which employees are hired in such a way that minorities and women are not underutilized.</p><p>9.2.3 That, in all solicitations or advertisements for employees placed by him or on his behalf, he will state that all applicants will be afforded equal opportunity without discrimination because of race, color, religion, sex, national origin or ancestry.</p><p>9.2.4 That, he will send to each labor organization or representative or workers with which he has or is bound by a collective bargaining or other agreement or understanding, a notice advising such labor organization or representative of the Contractor's obligation under the Illinois Fair Employment Practice Act and the Commission's Rules and Regulations for Public Contracts. If any such labor organization or representative fails or refuses to cooperate with the Contractor in his efforts to comply with such Act and Rules and Regulations, the Contractor will promptly so notify the Illinois Fair Employment Practices Commission and the Contracting agency and will recruit employees from other sources when necessary to fulfill his obligations thereunder.</p><p>9.2.5 That, he will submit reports as required by the Illinois Fair Employment Practices Commission's Rules and Regulations for Public Contracts, furnish all relevant information as may from time to time be requested by the Commission or the contracting agency, and in all respects comply with the Illinois Fair Employment Practice Act and the Commission's Rules and Regulations for Public Contracts.</p><p>9.2.6 That, he will permit access to all relevant books, records, accounts and work sites by personnel of the contracting agency and the Illinois Fair Employment Practices Act and the Commission's Rules and Regulations for Public Contracts.</p><p>9.2.7 That, he will include verbatim or by reference the provisions of paragraphs 1 through 7 of this clause in every performance subcontract as defined in Section 2.10(b) of the Commission's Rules and Regulations for Public Contracts so that such provisions will be binding upon every such subcontractor; and that it will also include the provisions of paragraphs 1,5,6 and 7 in every supply subcontract as defined in Section 2.10(a) of the Commission's Rules and Regulations for Public Contracts so that such provisions will be binding upon every such subcontractor. In the same manner as with other provisions of this Contract, the Contractor will be liable for compliance with applicable further he will promptly notify the contracting agency and the Illinois Fair Employment Practices Commission in the event any subcontractor fails or refuses to comply therewith. In addition, no Contractor will utilize any subcontractor declared by the Commission to be nonresponsible and therefore ineligible for contracts or subcontracts with the State of Illinois or any of its political subdivisions or municipal corporations. Page 9 of 46 9.3 With respect to the two types of subcontracts referred to under paragraph 7 of the Equal Employment Opportunity Clause above, following is an excerpt of Section 2 of the FEPC's Rules and Regulations for Public Contracts: 9.3.1 "Section 2.10". The term "Subcontract" means by agreement, arrangement or understanding, written or otherwise, between a contractor and any person (in which the parties do not stand in the relationship of an employer and an employee): 9.3.1.1 For the furnishing of supplies or services or for the use of real personal property, including lease arrangements, which, in whole or in part, is utilized in the performance of any one or more contracts; or 9.3.1.2 Under which any portion of the Contractor's obligation under any one or more contracts is performed, undertaken or assumed.</p><p>10. PREVAILING WAGES</p><p>10.1 The Bidder will be required to comply with "An Act Regulating wages of laborers, mechanics and other workmen employed in any public works by the State, County, City or any public body or any political subdivision or by any one under contract for public works", approved June 26, 1941, as amended, being Section 39s-1 through 39s-12, Chapter 48, Illinois Revised Statutes, 1973.</p><p>10.2 The Contractor shall not pay less than the prevailing rates of wages as determined by the Department of Labor to all laborers, workmen, and mechanics performing work under this Contract and shall comply with the requirements of the Illinois Wages of Employees on Public Works Act. All contractors are required to follow Public Act 94-0515 regarding certified payroll records.</p><p>11. FEDERAL, STATE AND LOCAL CODES:</p><p>11.1 The Contractor shall be required to comply with all Federal, State and Local codes and laws which apply to the work to be done and Bidders shall ascertain before bidding on the Work as to what codes and laws apply to the Work.</p><p>END Page 10 of 46</p><p>STANDARD SPECIFICATIONS</p><p>All work on this project shall be constructed in accordance with the "Standard Specifications for Road and Bridge Construction", January 1, 2002, adopted by the Department of Transportation (IDOT), State of Illinois, the most recent “Supplemental Specifications and Recurring Special Provisions” from IDOT, and the "Standard Specifications for Water and Sewer Main Construction in Illinois", ISPE, most recent edition. Page 11 of 46</p><p>SUPPLEMENTARY GENERAL CONDITIONS</p><p>The following Supplementary General Conditions Supplement the General Requirements of Section 100 of the Standard Specifications. Page 12 of 46 CONSTRUCTION STAKING</p><p>1.0 GENERAL</p><p>1.1 Line and grade staking: The Contractor shall be responsible for all construction staking. The Contractor shall provide such ordinary labor as may be required by the Engineer to check lines and grades and make other necessary measurements.</p><p>1.2 The location of each structure will be established using plans and invert elevation of that proposed structure. The frame elevations will be set based on actual finished elevation of the surrounding surface or other existing control and are subject to minor adjustment at no additional cost to the College.</p><p>1.3 The work shall be constructed to the lines, grades, and cross sections indicated on the Contract Drawings, unless otherwise directed by the Engineer. The Engineer reserves the right to make changes in the lines, grades and cross sections as may be deemed necessary during the progress of the work. Such minor changes in the line and grade shall not change the payment to the Contractor for such work.</p><p>1.4 All improvements shall be true both horizontally and vertically.</p><p>END</p><p>SUBMITTALS AND SUBSTITUTIONS</p><p>1.0 GENERAL</p><p>1.1 DESCRIPTION:</p><p>1.1.1 Work Included:</p><p>1.1.1.1 Wherever possible throughout the Contract Documents, the minimum acceptable quality of workmanship and materials has been defined by manufacturer's name and catalog number, referenced to recognized industry and government standards, or description of required attributes and performance.</p><p>1.1.1.2 To ensure that the specified products are furnished and installed in accordance with design intent, procedures have been established for advance submittal of design data and for their review by the Engineer.</p><p>1.1.1.3 Make all submittals required by the Contract Documents, and revise and resubmit as necessary to establish compliance with the specified requirements.</p><p>1.2 QUALITY ASSURANCE: Page 13 of 46 1.2.1 Coordination of Submittals: Prior to each submittal, carefully review and coordinate all aspects of each item being submitted and verify that each item and the submittal for it conforms in all respects with the requirements of the Contract Documents. By affixing the Contractor's signature to each submittal, certify that this coordination has been performed.</p><p>1.2.2 Certificates of Compliance:</p><p>1.2.2.1 Certify that all materials used in the work comply with all specified provisions thereof. Certification shall not be construed as relieving the contractor from furnishing satisfactory materials if, after tests are performed on selected samples, the material is found to not meet specified requirements.</p><p>1.2.2.2 Show on each certification the name and location of the work, name and address of Contractor, quantity and date or dates of the shipment or delivery to which the certificate applies, and name of the manufacturing or fabricating company. Certification shall be in the form of letter or company-standard forms containing all required data. Certificates shall be signed by an officer of the manufacturing or fabricating company.</p><p>1.3 REQUIRED SUBMITTALS:</p><p>1.3.1 Submit Shop Drawings and Manufacturer's Literature for each of the following:</p><p>1.3.1.1 P.C.C. Mix Design – Class SI</p><p>END</p><p>TESTING LABORATORY SERVICES 1.0 GENERAL</p><p>1.1 DESCRIPTION: </p><p>1.1.1 Work Included: Throughout the construction the Project Engineer may require the Contractor to perform testing of various materials or installed items. The Contractor shall provide all material and assistance needed to perform inspection and testing required under pertinent other sections of these specifications.</p><p>1.1.2 Work included in this Section: Concrete cylinder testing and breaks will be performed by an outside testing laboratory. This testing will be paid for by the Contractor. The testing company must be approved by the Project Engineer. It is anticipated that about 4 hours of field testing will be required, plus associated lab testing. Work will include pick up and testing of concrete cylinders for each pour of concrete sidewalk. Representatives from Gewalt Hamilton Associates will cast the cylinder, but the contractor’s testing company will be responsible for pick up, testing and reports for all break tests. Page 14 of 46 2.0 PROCEDURES</p><p>2.1 COOPERATION WITH TESTING LABORATORY: Representatives of the testing laboratory shall have access to the work at all times. Provide facilities for such access in order that the laboratory may properly perform its function.</p><p>2.2 CONDUCT OF INSPECTING:</p><p>2.2.1 Notification: To permit the Project Engineer to schedule testing services, notify the Project Engineer not less than 48 hours in advance when testing will be required.</p><p>2.2.2 Reimbursement of Testing Costs: When Project Engineer has dispatched personnel to witness inspection or testing, and the inspecting or testing has been delayed without proper notification to the Project Engineer, the contractor shall reimburse all associated costs arising by virtue of lack of notification.</p><p>2.3 ALTERNATIVE INSPECTION PROCEDURE: The Project Engineer shall have the right to require alternative inspection procedure other than those specified when such is required to demonstrate compliance with Contract requirements. Costs of inspection will be borne by the Contractor in all cases.</p><p>2.3.1 Concrete cylinders casting, transport, breaks and reports for each day of concrete pours.</p><p>END</p><p>SITE PROTECTION AND ACCESS</p><p>1.0 GENERAL</p><p>1.1 The proposed improvements have been located to facilitate access to the work and to prevent damage to planting and other areas outside the limits of work. The Contractor is not permitted to stockpile material or equipment in any area off the project site unless he has received approval to do so from the Project Engineer and property owners in writing.</p><p>1.2 All areas which have been disturbed during the construction, for which a specific bid item has not been established shall be incidental to the contract. All items to be replaced shall be replaced in similar kind to that which was removed. 1.3 All traffic controls, barricades, flagmen, or anything else necessary for construction of the improvements shall be provided by the Contractor and incidental to the contract. The following guidelines shall be adhered to by the Contractor unless written permission to deviate from these guidelines is secured in advance from the Project Engineer.</p><p>1.3.1 Twenty-four hours prior to closing or blocking any roadways, the Contractor shall notify the Des Plaines Police Department and Fire Department as to the schedule, and duration of the restriction or closing. Page 15 of 46 1.3.2 At least one lane sufficient and appropriate for vehicular passage shall be maintained on all streets during working hours. All excavations, stockpiles, spoil piles, and equipment must be adequately protected by moveable barricades with operating flashing lights.</p><p>1.4 Access via local roadways is limited to loads permitted or posted. Use of these roadways shall be at direction of the Engineer and the City of Des Plaines.</p><p>1.5. Barricades, warning signs and flagged-off-areas must be established to warn individuals of the construction modifications. Alternative parking, drive and access must be provided by the Contractor prior to any closure during these site improvements.</p><p>END</p><p>CLEANING</p><p>1.0 GENERAL</p><p>1.1 SAFETY CLEANING:</p><p>1.1.1 Safety Cleaning: The contractor is responsible for safety cleaning, which includes but is not limited to the following:</p><p>1.1.1.1 Keep work areas free of dirt, rubbish, debris and scrap.</p><p>1.1.1.2 Backfill progressively after any underground utility installation.</p><p>1.1.1.3 Remove spills of oil, grease, or other liquids immediately or sprinkle with sand.</p><p>1.2 PROGRESS CLEANING:</p><p>1.2.1 The Contractor shall remove his rubbish and debris from site promptly upon its accumulation, and prior to general cleanup.</p><p>1.2.2 The Contractor shall make daily cleaning of adjacent roadways before leaving the construction site at the end of each work day. Cleaning may be required more frequently if excessive mud build up of over one-half inch (1/2") occurs. The Contractor must completely remove dirt from roadway and shall not simply push it to the shoulder or curb. IDOT Permit requirements and safety concerns may require more frequent cleaning.</p><p>1.3 DUST</p><p>1.3.1 If, during the process of work, the work areas become dusty due to vehicle traffic in these work areas, the Engineer may order the placement of calcium chloride or washing the street, or both. This activity is considered incidental to the contract work and is not an extra pay item. Page 16 of 46 1.4 FINAL CLEANING:</p><p>1.4.1 Immediately prior to substantial completion, the Contractor shall perform thorough cleaning so as to put all such work in a complete and finished condition ready for acceptance and the use intended.</p><p>END</p><p>PROJECT RECORDS</p><p>1.0 GENERAL During progress of the work, the contractor shall maintain on the job site one (l) set of drawings upon which he shall keep an accurate record of final location of each completed part of the work. The Project Engineer will review this record set of drawings each week and will advise the Contractor if final positions are within the tolerance required for proper design.</p><p>1.2 Upon completion of all work called for herein, the Contractor's final marked set of prints shall be turned over to the Project Engineer with other drawings called for in the Contract Documents. Unless otherwise specified, all elevations indicated in the Contract Documents refer to United States Geological Survey (USGS) Datum.</p><p>END</p><p>STORM WATER MANAGEMENT AND EROSION CONTROL PLAN</p><p>1.0 GENERAL</p><p>All areas of the site must drain freely during the project. Blockage of normal or emergency flow will not be permitted, although pumping of normal flow and groundwater is anticipated. The purpose of this provision is to avoid unnecessary property damage.</p><p>END Page 17 of 46</p><p>DIVISION 2 - SITEWORK Section 02520 - Portland Cement Concrete Curbs And Gutters, Sidewalk And Pavements</p><p>PART 1 GENERAL</p><p>1.01 WORK INCLUDED</p><p>A. Provide all cast-in-place concrete, complete, in place, as indicated on the drawings, specified herein, and needed for a complete and proper installation.</p><p>1.02 QUALITY ASSURANCE </p><p>A. Standards:</p><p>1. Comply with standards specified, the latest edition of Illinois Department of Transportation, Standard Specifications for Road and Bridge Construction in Illinois. </p><p>2. American Concrete Institute (ACI) 301, ASpecifications for Structural Concrete for Buildings@.</p><p>3. ACI 318, ABuilding Code Requirements for Reinforced Concrete@.</p><p>4. Concrete Reinforcing Steel Institute (CRSI) AManual of Standard Practice@.</p><p>5. In case of conflict between the referenced standards, the more stringent requirements shall govern.</p><p>6. Concrete Manufacturer Qualifications: Manufacturer of ready-mixed concrete products complying with ASTM C94 requirements for production facilities and equipment.</p><p>7. Concrete Testing Service: The Owner will engage a qualified independent testing agency to perform materials evaluation tests and to design concrete mixes under field quality control. </p><p>B. Submittals</p><p>1. Produce data for proprietary materials and items, including reinforcement and forming accessories, admixtures, joint systems, curing compounds, dry-shrake finish materials and other if required by Architect..</p><p>2. Design mixes for each class of concrete. Include revised mix proportions when characteristics of materials, project conditions, weather, test results, or other circumstances warrant adjustments. Page 18 of 46 1.03 PRODUCT HANDLING </p><p>A. Protection </p><p>1. Use all means necessary to protect the materials of this Section before, during, and after installation and to protect the work and materials of all other trades.</p><p>B. Replacement </p><p>1. In the event of damage, immediately make all repairs and replacements necessary to the approval of the Project Engineer at no additional cost to the Owner.</p><p>1.04 PROJECT CONDITIONS</p><p>A. Traffic Control</p><p>1. Maintain access for vehicular and pedestrian traffic as required for other construction activities.</p><p>PART 2 PRODUCTS </p><p>2.01 CEMENT</p><p>A. General:</p><p>1. All Portland Cement shall conform to the requirements of ASTM C 150, except that 28 day test strength shall be a minimum of 4,000 psi. Minimum percent of entrained air shall be five and maximum percent of entrained air shall be eight. Maximum allowable water cement ratio (gallons per sack of cement) shall be six (6). Maximum design slump or consistency as measured according to ASTM C 143 shall be four inches (4").</p><p>2. Cement to be used in construction at or below grade shall comply with the requirements of Type II or IIA, sulfate resistant. Minimum cement content shall be 564 lbs. per cubic yard (6 bags).</p><p>3. The addition of sodium chloride or calcium chloride is prohibited.</p><p>4. The addition of water to a redi mix load after the truck has left the batch plant is specifically prohibited without the express permission of the Project Engineer.</p><p>5. The Project Engineer reserves the right to reject concrete loads without compensation for excessive slump, excessive waiting time, temperature, water addition, and other causes anticipated to result in poor long term performance.</p><p>2.02 AGGREGATES</p><p>A. General: Page 19 of 46 1. All aggregates shall conform to requirements of ASTM C 33.</p><p>B. Course Aggregates: </p><p>1. Course aggregate shall comply with ASTM C 33, size 57.</p><p>C. Aggregate Sources: </p><p>1. Provide aggregates from one source of supply only.</p><p>D. Aggregate Size:</p><p>1. Maximum aggregate size shall be no larger than one- fifth (1/5) of the narrowest dimension between sides of forms, one-third (1/3) of the depth of slabs, nor three-fourths (3/4) of the minimum clear spacing between individual reinforcing bars or bundles of bars.</p><p>2. Stockpile the aggregates in a manner to protect from contamination.</p><p>2.03 WATER </p><p>A. Water used as an ingredient in concrete shall be clean, potable, and free from injurious amounts of foreign matter.</p><p>2.04 CONCRETE ADMIXTURES</p><p>A. Air Entraining Admixtures:</p><p>1. Conform to ASTM C 260. No other admixture unless required by the Drawings and Specifications shall be used without approval. When used, these admixtures shall conform to ASTM C 494.</p><p>2.05 CURING MATERIALS</p><p>A. Liquid curing and sealing compounds shall conform to ASTM C 309, Type I.</p><p>2.06 OTHER MATERIALS</p><p>A. Performed expansion joint filler material shall be bituminous fiber type conforming to ASTM C 1751.</p><p>B. Waterstops shall be extruded from new stock polyvinyl chloride, ribbed, with expandable center bulb. The minimum width shall be six inches (6") and minimum thickness shall be 0.25 inches. Page 20 of 46</p><p>2.07 BATCHING, MIXING, AND DELIVERY EQUIPMENT: </p><p>Use transit mixed concrete from approved batching and mixing plant. Batch, mix, and transport concrete to site in accordance with provisions of ASTM C 94.</p><p>PART 3 EXECUTION </p><p>3.01 DELIVERY </p><p>A. The concrete shall be discharged into the forms within 1.5 hours after the introduction of water to the cement. When the temperature of the concrete is 85 degrees F. or above the time between the introduction of water to the cement and complete discharge of the concrete into the forms shall not exceed 45 minutes.</p><p>B. Concrete delivered shall have the following maximum and minimum temperatures:</p><p>Minimum Maximum Concrete Concrete Outside Air Temperature Temperature Temperature 45 Degrees F. and above 45 degrees F. 90 Degrees F. 30 to 45 degrees F. 60 degrees F. 90 degrees F. 0 to 30 degrees F. 65 degrees F. 90 degrees F. below 0 degrees F. 70 degrees F. 90 degrees F.</p><p>C. When either water or aggregates are heated above 100 degrees F., they shall be combined first in the mixer before the cement is added to obtain a temperature not to exceed 80 degrees F. for the aggregate and water mixture.</p><p>D. Ice may be used as a part or all of the mixing water on a pound of ice replacing a pound of water basis. However, the ice must be crushed or shaved to assure complete melting of the ice by the time the mixing is completed.</p><p>3.02 CONCRETE PLACEMENT:</p><p>A. General </p><p>1. Place concrete in compliance with practices and recommendations of ACI 304, and as herein specified.</p><p>B. Procedures</p><p>1. Deposit concrete continuously or in layers so such thickness that no concrete will be placed on concrete which has hardened sufficiently to cause the formation of seams or planes of weakness within the section.</p><p>2. If a section cannot be placed continuously, provided construction joints as herein specified. Page 21 of 46 3. Perform concrete placing at such a rate that concrete which is being integrated with fresh concrete is still plastic.</p><p>4. Deposit concrete as nearly as practicable in its final location to avoid segregation due to rehandling and flowing. 5. Do not subject concrete to any procedure which will cause segregation.</p><p>6. Screed concrete which is to receive other construction to the proper level to avoid excessive skimming and grouting.</p><p>7. Do not use concrete which becomes nonplastic and unworkable, or does not meet the required quality control limits, or which has been contaminated by foreign materials.</p><p>8. Remove rejected concrete from the site and dispose of it in a location approved for that purpose.</p><p>C. Concrete Conveying:</p><p>1. Handle concrete from the point of delivery and transfer to the concrete conveying equipment, and to the locations of final deposit, as rapidly as practicable and by methods which will prevent segregation and loss of concrete mix materials.</p><p>2. Provide runways for wheeled concrete conveying equipment from the concrete delivery point to the location of final deposit.</p><p>3. Keep interior surfaces of conveying equipment, including chutes and tremies, free from hardened concrete, debris, water, and other deleterious materials.</p><p>4. Pumps may be used only if they can pump the mix designed. Do not add fine aggregate or water to the mix to satisfy needs of a pumping device.</p><p>5. Use chutes or tremies for placing concrete where a drop of more than 72 inches is required.</p><p>D. Placing Concrete in Forms:</p><p>1. Deposit concrete in forms in horizontal layers not deeper than 24 inches, and to avoid inclined construction joints.</p><p>2. Where placement consists of several layers, place each layer while preceding layer is still plastic and to avoid cold joints.</p><p>3. Remove temporary spreaders in forms when concrete placing has reached the elevation of such spreaders.</p><p>4. Do not place concrete in supporting elements until the concrete previously placed in columns and walls is no longer plastic. Page 22 of 46 E. Placing Concrete Footings:</p><p>1. Deposit and consolidate concrete slabs in a continuous operation, within the limits of construction joints, until the placing of a panel or section is completed.</p><p>2. Consolidate concrete during placement by use of the specified equipment, thoroughly working concrete around the reinforcement and into corners.</p><p>3. Bring slab surfaces to the correct level with a straight edge, and then strike off.</p><p>4. Use bullfloats or darbies to smooth the surface, leaving it free from bumps and hollows.</p><p>5. Cold weather placing: Comply with ACI 306 to protect all concrete work from physical damage and reduced strength which would be caused by frost, freezing actions, or low temperatures.</p><p>F. Hot weather placing:</p><p>1. When hot weather conditions exist which would seriously impair the quality and strength of concrete, place the concrete as follows:</p><p>2. Maintain concrete temperature at time of placement below 90 degrees F. Use chilled mixing water or chopped ice to control concrete temperature, provided the water equivalent of the ice is calculated to the total amount of water.</p><p>3. Cover reinforcing steel with water-soaked burlap if the steel becomes too hot. Steel temperature shall not exceed the ambient air temperature immediately prior to placement of concrete.</p><p>4. Wet forms thoroughly prior to placement of concrete.</p><p>5. Use set-control admixtures in the mix.</p><p>G. General</p><p>1. Consolidate all concrete in accordance with provisions of ACI 309.</p><p>2. Consolidate each layer of concrete immediately after placing, by use of internal concrete vibrators supplemented by hand-spading, rodding, or tamping.</p><p>3. Do not use vibrators to transport concrete inside the forms.</p><p>4. During all phases of operation, maintain a frequency of not less than 10,000 vibrations per minute per internal vibrator.</p><p>5. Do not vibrate forms or reinforcement.</p><p>H. Equipment Page 23 of 46 1. Provide adequate number of units and power source at all times. Maintain spare units on hand to ensure adequacy.</p><p>I. Procedures</p><p>1. Limit duration of vibration to time necessary to produce satisfactory consolidation without causing segregation of aggregates.</p><p>2. Insert the vibrator so as to penetrate the lift immediately below the one being placed, and manipulate to blend the two lifts.</p><p>3. Do not insert the vibrator into lower courses which have begun to set.</p><p>4. Use the vibrator to melt down the concrete as it is being placed, and use the vibrator to consolidate the mass of concrete.</p><p>5. In the case of wall construction, assign at least one vibrator and vibrator-operator to melting down the mix; and assign at least one other vibrator and vibrator-operator to consolidating the mass of concrete.</p><p>6. Under no circumstances shall the points of insertion during the consolidation phase be more than 18 inches apart.</p><p>3.04 JOINTS</p><p>A. Construction Joints:</p><p>1. Horizontal construction joints will not be permitted except as may be shown on the Drawings.</p><p>2. Provide keyways, sized per plans, in all construction joints in wall, slabs, and between footings and walls.</p><p>3.05 CONCRETE FINISHING</p><p>A. Finish of formed surfaces:</p><p>1. Rough form finish: a. Provide as-cast rough form finish to formed concrete surfaces that are to be concealed in the finish work, by any other construction, or under earth fills. b. Standard rough form finish shall be the concrete surface having the texture imparted by the form facing material used, with tie holes and defective areas repaired and patched, and all fins and other projects exceeding one-quarter inch in height rubbed down or chipped off.</p><p>2. Smooth form finish: Page 24 of 46 a. Provide as-cast smooth form finish for formed concrete surfaces that are to be exposed to view. Grind and patch all surfaces so that no hole or fin is greater than 1/8 inch. Rub smooth with cement mortar mix and leave surface void of sand particles. Do not brush on mortar mix; use burlap for final cleaning. All grinding and finishing shall be carried twelve inches (12") below the ground surface. b. Produce smooth form finish by selecting form material to impart a smooth, hard, uniform texture and arranging them orderly and symmetrically with a minimum of seams. c. Repair and patch defective areas with all fins and other projections completely removed and smoothed. d. Related Unformed Surfaces: At tops of walls, horizontal offsets, and similar unformed surfaces occurring adjacent to formed surfaces, strike off smooth and finish with a smooth troweled finish.</p><p>4. Trowel Finish: a. Apply trowel finish to top surfaces of curbs that are to be exposed to view, unless otherwise shown. b. Grind smooth those surface defects which have been damaged during removal of forms.</p><p>5. Broom Finish: a. Apply light broom finish to all curbs and gutters, sidewalks and driveway aprons. b. Curing compound shall be used on all exposed surfaces and shall be applied immediately after broom finish has been applied. Apply in accordance with the IDOT SSRBC, including weather and calendar limitations. c. If concrete is poured outside the period permitted for curing compound, use wet curing methods (burlap and visqueen) and prevent from freezing, during curing period.</p><p>3.06 DAMAGED OR DEFECTIVE CONCRETE </p><p>A. Damaged or defective concrete resulting from the Contractor's operation at any time before completion and acceptance of the work shall be removed and replaced by the Contractor with acceptable concrete at no cost to the Owner. Page 25 of 46 3.07 CONCRETE CURB AND GUTTER</p><p>A. Curb and gutter shall be barrier curb, vertical curb, or match existing for short sections as shown on the plans. The curb shall consist of Portland Cement Concrete, 4" slump, 6.1 bag mix, and air entrainment of not less than five (5%) or more than eight (8%). Concrete shall be a minimum compressive strength (4000 PSI) at fourteen (14) days. All curb and gutter shall be broom finished. Saw joints at 15' O.C. within 24 hours. </p><p>B. Expansion joints in the curb and gutter shall be placed in all PC's and PT's and at 60 foot on-center maximum. Sawcut contraction joints at least 2 inches in depth 15 feet on-centers within 24 hours of pouring. Curing compound shall be applied when finished. Premolded joint filler shall be used in all expansion and contraction joints in the curb and gutter. Curb and gutter shall be backfilled prior to pavement installation. It shall be backfilled and compacted for a distance of about 5 feet behind the curb. </p><p>C. 3/4" thick pre-molded fiber expansion joints with 3/4" X 18" PLAIN round, steel dowel bars shall be installed in all curbs, 1/2" X 12" PLAIN round steel dowel bars in sidewalk at sixty foot (60') intervals and at all P.C.'s, P.T's, and curb returns. Alternate ends of the dowel bars shall be greased and fitted with metal expansion tubes.</p><p>D. Two (2) coats of white curing compound shall be applied to all concrete work as soon as the finish is complete, within one (1) hour of final striking, subject to IDOT seasonal limitations. During the colder portion of the year, use wet curing methods as per IDOT specifications.</p><p>E. In situations where curb is to be added adjacent to an existing asphalt surface, sawcut the existing asphalt surface at least 2 feet from the proposed edge of concrete, and remove the asphalt and stone base sufficiently to provide adequate working room to form the curb or curb and gutter. Protect the sawcut edge. If damaged, or if material below the surface is undermined, recut in a long straight line further back. After a minimum 7 day cure, if test cylinders indicate at least 3500 psi strength, backfill behind curb and then place and compact a stone (CA6) base followed by the asphalt surface mix to a depth of 4 inches to refill the space between the curb and the sawcut edge. Compact to 93% density forming a smooth surface flush with the existing surface. If not overlaid, the complete parking lot surface shall be seal coated and restriped.</p><p>In situations where a new curbline is construed along an existing road, replace the road pavement in kind, but with a minimum of 4 inches of CA6, 6 inches of BAM and 4 inches of Class I Surface Mix.</p><p>F. All curb on-site shall be constructed with 2 continuous #4 rebar. Rebar shall not span the expansion joints, but smooth dowels shall.</p><p>3.08 ABUTTING CONCRETE</p><p>A. Whenever new concrete abuts existing concrete set a 3/4" thick pre-molded fiber expansion joint and dowel with SMOOTH 12" #4 bars at 24" O.C. except at building entrances where they shall be at 12" O.C. This includes concrete poured adjacent to existing sidewalks, curbs and building. The dowel bars should be 4" into existing concrete with 8" extending into new concrete. Page 26 of 46 3.09 CONCRETE SIDEWALKS</p><p>A. Concrete sidewalks and aprons shall be 5" thick, set on a CA-6 base 4" thick, set on a compacted subbase and shall be 1/4" per foot above the adjacent curb. Specifications for concrete and curb and gutter shall have a 14 day compressive strength of 3500 psi with a 5%-8% entrained air, with 6.1 bag mix and 2-4 inches of slump. Finish with a light broom surface. Meet pavement grade with a depressed curb. Curing in accordance with Section 3.05. Minimum cross slope shall be 1/4" per foot toward street. Handicapped ramps shall be provided and shall be installed for IDOT standards. </p><p>B. Contraction joints shall be tooled at 5' intervals in the sidewalk. The cost of these joints shall be considered as incidental to the cost of the contract. Contraction joints shall also be tooled down the center of all sidewalks greater than 6' wide or as shown on the plans. (Five foot spacing maximum)</p><p>C. When a sidewalk crosses a disturbed area or a trench line, place 3 - #4 bars, at least 10 feet long each, or 10 feet wider than the trench or disturbed area, in the concrete, approximately 2 inch above the stone base. </p><p>D. Prior to ordering, all material such as pipe, valves, fittings, hydrants, and structures shall be submitted to the Project Engineer in Shop Drawing format. Approval of specific materials by the City Engineer is also required. </p><p>3.10 FIELD QUALITY CONTROL TESTING </p><p>A. The Owner will employ a qualified testing and inspection agency to sample materials, perform tests, and submit test reports during concrete placement. Sampling and testing for quality control may include the following:</p><p>1. Sampling Fresh Concrete: ASTM C172, except modified for slump to comply with ASTM C94.</p><p>2. Slump: ASTM C143; one test at point of placement for each compressive-strength test but no less than one test for each day's pour of each type of concrete. Additional tests will be required when concrete consistency changes.</p><p>3. Air Content: ASTM C231, pressure method; one test for each compressive-strength test but no less than one test for each day's pour of each type of air-entrained concrete.</p><p>4. Concrete Temperature: ASTM C1064; one test hourly when air temperature is 40 degrees F (4 deg. C) and below and when 80 degrees F (27 deg C) and above, and one test for each set of compressive-strength specimens.</p><p>5. Compression Test specimens: ASTM C31; one set of four standard cylinders for each compressive-strength test, unless directed otherwise. Mold and store cylinders for laboratory-cured test specimens except when field-cured test specimens are required. Page 27 of 46 6. Compressive Strength Tests: ASTM C39; one set for each day's pour of each concrete class exceeding 5 cu. yd. but less than 25 cu. yd., plus one set for each additional 50 cu. yd. Test one specimen at 7 days, test two specimens at 28 days, and retain one specimen in reserve for later testing if required. </p><p>7. When frequency of testing will provide fewer than five strength tests for a given class of concrete, conduct testing from at least five randomly selected batches or from each batch if fewer than five are used. </p><p>8. When total quantity of a given class of concrete is less than 50 cu. yd., Engineer may waive strength testing if adequate evidence of satisfactory strength is provided. </p><p>9. When strength of field-cured cylinders is less than 85% of companion laboratory-cured cylinders, evaluate current operations and provide corrective procedures for protecting and curing the in-place concrete.</p><p>10. Strength of level of concrete will be considered satisfactory if averages of sets of three consecutive strength test results equal or exceed specified compressive strength and no individual strength test result falls below specified compressive strength by more than 500 psi.</p><p>11. Test results will be reported in writing to Engineer, concrete manufacturer, and contractor within 24 hours of testing. Reports of compressive strength tests shall contain the project identification name and number, date of concrete placement, name of concrete testing agency, concrete type and class, location of concrete batch in paving, design compressive strength at 28 days, concrete mix proportions and materials, compressive breaking strength, and type of break for both 7-day and 28-day tests.</p><p>12. Non-destructive testing: Impact hammer, sonoscope, or other non-destructive device may be permitted but shall not be used as the sole basis for acceptance or rejection.</p><p>13. Additional Tests: The testing agency will make additional tests of the concrete when test results indicate slump, air entrainment, concrete strengths, or other requirements have not been met, as directed by the Engineer. Testing agency may conduct tests to determine adequacy of concrete by cored cylinders complying with ASTM C42, or by other methods as directed. </p><p>END OF SECTION Page 28 of 46</p><p>SPECIAL PROVISIONS</p><p>The following Special Provisions supplement the "Standard Specifications for Road and Bridge Construction", adopted January 1, 2002, the "Supplemental Specifications and Recurring Special Provisions", adopted January 1, 2006 (as indicated on the check sheet included herein) and the latest edition of the Illinois Manual on Uniform Control Devices for Streets and Highways", in effect on the date of invitation for bids, and the current edition of the "Standard Specifications for Watermain and Sewer Construction in Illinois". These Special Provisions included herein apply to and govern the proposed improvement and, in case of conflict with any part or parts of said specifications, said special provisions shall take precedent and shall govern. Page 29 of 46 SPECIAL PROVISION SOIL AND EROSION CONTROL 1.0 GENERAL</p><p>1.1 Description: The following are standards for soil and erosion control to be observed during the course of the work:</p><p>1.2 All bypass channels, devices, and coffer dams must be constructed so that channel flows will not cause erosion of excavated material. In each case a sedimentation basin must be constructed so as to allow some of the sediment to settle prior to the downstream outlet of the project area.</p><p>1.3 Pumps may be used as bypass devices but in no case will the water be diverted outside the project limit.</p><p>1.4 Work included under this section shall be incidental to the base contract.</p><p>END</p><p>SPECIAL PROVISIONS </p><p>A. START OF CONSTRUCTION / CONSTRUCTION SCHEDULE The contractor shall commence construction on July 31, 2006. All work must be completed by August 11, 2006. Weather permitting work should be continuous and every effort must be made to impact normal College business as little as possible. It is the College’s desire that work be completed as soon as possible so that the sod can be placed.</p><p>B. TIME OF COMPLETION A final completion date for all work on this project has been specified as August 11, 2006.</p><p>C. NOTIFICATION The College requires 48 hours notice in advance of any roadway or parking lot closures.</p><p>D. P.C.C. CURB AND GUTTER REMOVAL AND REPLACEMENT (SPECIAL)</p><p>This work consists of replacing approximately 78 lineal feet of curb and gutter noted in “Section A” on the attached work zone location map.</p><p>Patching replacement work will include saw cutting, removal and disposal, backfilling and restoration of the bituminous parking (1’ overdig, removed pavement shall be replaced with P.C.C base course and 2” bituminous surface). Page 30 of 46 Replacement curb and gutter type will be a fully depressed section. Stone base and continuous rebar will be required and are incidental to the cost. Curb shall be tied into existing curb using rebar at both ends.</p><p>Payment for all Combination P.C.C. Curb and Gutter Removal and Replacement (Special) shall be per lineal foot and is to include all items of work as specified. </p><p>E. P.C.C. SIDEWALK REMOVAL & REPLACEMENT, 5” (SPECIAL)</p><p>This item consists of removal and replacement of all P.C.C. Sidewalk as indicated in the bid proposal and as indicated in the work zone map. Replacement material shall include compacted CA-6 crushed stone as necessary to meet required subbase grade and 5” of P.C.C. Class SI. All sidewalk shall be tied into existing sidewalk, building slabs, curb, etc. using #4 rebars at 24” on center. Work shall also include curing and a concrete protective coat. All this work is incidental to the pay item.</p><p>Payment for P.C.C. Sidewalk Removal & Replacement, 5” (Special) will be per square foot and is to include all items of work as specified.</p><p>F. ADA ACCESSIBLE P.C.C. SIDEWALK REMOVAL & REPLACEMENT, 5” (SPECIAL)</p><p>This item consists of removal and replacement of all P.C.C. Sidewalk as indicated in the bid proposal and as indicated in the work zone map. Replacement material shall include compacted CA-6 crushed stone as necessary to meet required subbase grade and 5” of P.C.C. Class SI. All sidewalk shall be tied into existing sidewalk, building slabs, curb, etc. using #4 rebars at 24” on center. This work is incidental to the pay item.</p><p>Work shall also include constructing an ADA Accessible Sidewalk in accordance with IDOT Standard 424001-04. The ramp texturing shall be done with an expanded metal grate placed and removed from wet concrete to leave a truncated dome pattern as shown. The tactile surface shall be tinted red with pigment integrally incorporated into the concrete mix. Work shall also include curing and a concrete protective coat.</p><p>Payment for P.C.C. Sidewalk Removal & Replacement, 5” (Special) will be per square foot and is to include all items of work as specified. Page 31 of 46 Page 32 of 46 Page 33 of 46 SECTION 00480</p><p>NONCOLLUSION CERTIFICATION PART 1</p><p>______as part of its Bid on a contract for: (Name of Contractor)</p><p>Golf Road Baseball Field Rehabilitation Oakton Community College Des Plaines, Illinois</p><p>To:</p><p>Oakton Community College 1600 East Golf Road Des Plaines, Illinois and pursuant to Illinois Revised Statues, Chapter 38, Article 33E, Public Contracts, hereby certifies that said Contractor is not barred from bidding or contracting with any unit of State or local government as a result of a violation of either Section 33E-3 or 33E-4 of said statue.</p><p>By: ______(Authorized Agent of the Contractor)</p><p>______Title</p><p>Subscribed and sworn to before me this ______day of ______, 200___</p><p>______Notary Public</p><p>Seal: Page 34 of 46 SECTION 00510 NONCOLLUSION PART 2</p><p>CONTRACTOR’S CERTIFICATION (Upon Contract Execution)</p><p>______, Having executed a contract for the:</p><p>2006 Sidewalk Replacement Program Oakton Community College Des Plaines, Illinois</p><p>To:</p><p>Oakton Community College 1600 East Golf Road Des Plaines, Illinois hereby certifies that said Contractor is not barred from executing said Contract as a result of a violation of either Section 33E-3 or 33E-4, Article of Chapter 720 of the Illinois Compiled Statutes.</p><p>By: ______(Authorized Agent of the Contractor)</p><p>______Title</p><p>Subscribed and sworn to before me this ______day of ______, 200___</p><p>______Notary Public</p><p>Seal: Page 35 of 46 SECTION 00570 HOLD HARMLESS AGREEMENT</p><p>OWNER: Oakton Community College 1660 East Golf Road Des Plaines, Illinois</p><p>STATE OF ILLINOIS</p><p>COUNTY OF COOK</p><p>______(company name) agrees to indemnify, hold harmless and defend Owner, its consultants for this project, agents, servants and employees, Gewalt Hamilton Associates, Inc. (Engineers), and its subconsultants, and each of them against and hold them harmless from any liability, loss, cost, damages and claims, cause of action, demands, rights, costs loss of service expenses, compensation, and expenses (including reasonable attorney’s fees and court costs) which the undersigned or which may hereafter accrue, directly or indirectly, for or on account of any and all known and unknown, foreseen and unforeseen, resulting from, arising out of, or incurred by reason of claims, actions, or suits based upon or alleging bodily injury, including death, or property damages arising out of, or resulting from the Contractors operations under this Contract, whether such operations be by himself or by any subcontractor or by anyone directly or indirectly employed by either of them</p><p>Signed this _____ day of ______, 200__</p><p>By: ______</p><p>Title: ______</p><p>Address: ______STATE OF ILLINOIS</p><p>COUNTY OF ______</p><p>I, the undersigned, a notary public in and for the State and County aforesaid, hereby certify that ______appeared (Name of Signatory) before me this day in person and, being first duly sworn on oath, acknowledged that he/she executed the foregoing certification as his/her free act and deed.</p><p>DATED: ______</p><p>(NOTARY SEAL) </p><p>Notary Public Page 36 of 46</p><p>BID PROPOSAL</p><p>BP-36 Page 37 of 46</p><p>2006 SIDEWALK REPLACEMENT PROGRAM FOR OAKTON COMMUNITY COLLEGE DES PLAINES CAMPUS</p><p>BID PROPOSAL</p><p>To: Board of Trustees</p><p>Oakton Community College</p><p>The undersigned hereby certifies that he is familiar with all the local conditions affecting the cost of the work, and hereby proposes to furnish all labor, materials, tools, and equipment necessary to perform and complete in a thorough workmanlike manner, the construction of specified improvements to Oakton Community College, Des Plaines Campus, all in accordance with the Plans and Specifications attached hereto, as prepared by Gewalt Hamilton Associates, Inc. </p><p>The undersigned further agrees to furnish the required performance and payment bond of 100 percent of the contract and to enter into a contract no earlier than July 15, 2006. The undersigned further agrees to start construction on or after July 31, 2006 and to complete all work covered by this Proposal in accordance with the stipulated conditions and requirements as specified.</p><p>Accompanying this proposal is a ______(Bid Bond, Bank Cashiers Check or Certified Check) in the amount of dollars ( ), being ten percent (10%) of the Contract Bid.</p><p>I hereby certify that all statements herein are made of ______(name and address of corporation, partnership or person submitting bid) in the City of , State of ______; and that I have examined and carefully prepared this Proposal from the plans and specifications and have checked the same in detail before submitting this Proposal; that I have full authority to make such statements, and submit this Proposal on its/their behalf; and that the said statements are true and correct.</p><p>This Proposal has incorporated addenda numbers: ______</p><p>BP-37 Page 38 of 46 PROPOSAL ITEMS DESCRIPTION BASE BID: SITE IMPROVEMENTS The work includes providing all necessary labor, material and equipment to complete all the site improvements as detailed in the contract documents for the Des Plaines Campus of Oakton Community College, 2006 Sidewalk Replacement Program, including, but not limited to, Portland cement concrete sidewalk, concrete curb and gutter, general site cleanup, etc. </p><p>PROPOSAL </p><p>SCHEDULE OF PRICES</p><p>ITEM UNIT TOTAL NO. DESCRIPTION UNIT PRICE AMOUNT QUANTITY 1. P.C.C. CURB & GUTTER REMOVAL & REPLACEMENT (Special) LF 78 $ $ 2. P.C.C. SIDEWALK REMOVAL & REPLACEMENT, 5” (Special) SF 7,000 $ $ 3. ADA ACCESSIBLE P.C.C. SIDEWALK REMOVAL & REPLACEMENT, 5” (Sp) SF 100 $ $ 4. PRICE OF PERFORMANCE/PAYMENT EA 1 $ $ BOND</p><p>TOTAL BID $</p><p>BP-38 Page 39 of 46 The Contract Documents which will comprise the Contract between the College and the Contractor will be attached hereto and made a part hereof and will consist of the following:</p><p>1. Notice to Bidders; 2. Instructions to Bidders; 3. Supplementary General Conditions; 4. Bid Proposal; 5. Form of Contract & Contract Bond; 6. Standard Specifications for Road and Bridge Construction; 7. Standard Specifications for Water & Sewer Main Construction in Illinois; 8. Supplementary Specifications; 9. Special Provisions; 10. Drawings & Plan Notes; 11. Addenda.</p><p>If a conflict between any of the above documents or sections of documents occurs, generally the more stringent requirement, as determined by the owner, shall govern.</p><p>I will be using the only following Subcontractors or Suppliers on this project:</p><p>SUBCONTRACTORS OR SUPPLIERS PORTION OF WORK</p><p>______</p><p>BP-39 Page 40 of 46</p><p>A. CORPORATION</p><p>The bidder is a corporation organized under the laws of the State of ______</p><p>______Duly authorized officer's signature</p><p>______Title</p><p>CORPORATE SEAL</p><p>B. PARTNERSHIP</p><p>The bidder is a co-partnership consisting of individual partners whose full names are listed below:</p><p>______(Print) (Partner's Title) ______</p><p>C. INDIVIDUAL</p><p>The bidder is an individual. ______(Individual's Signature) (A, B, or C Notarize) Sworn and subscribed to me on this _____ day of ______, 20___.</p><p>______(Notary Public or other officer authorized to administer oaths)</p><p>My commission expires </p><p>BP-40 Page 41 of 46</p><p>SAMPLE FORM OF CONTRACT</p><p>AND</p><p>SAMPLE CONTRACT BOND Page 42 of 46 Page 43 of 46 Page 44 of 46 Page 45 of 46 Page 46 of 46</p>
Details
-
File Typepdf
-
Upload Time-
-
Content LanguagesEnglish
-
Upload UserAnonymous/Not logged-in
-
File Pages46 Page
-
File Size-