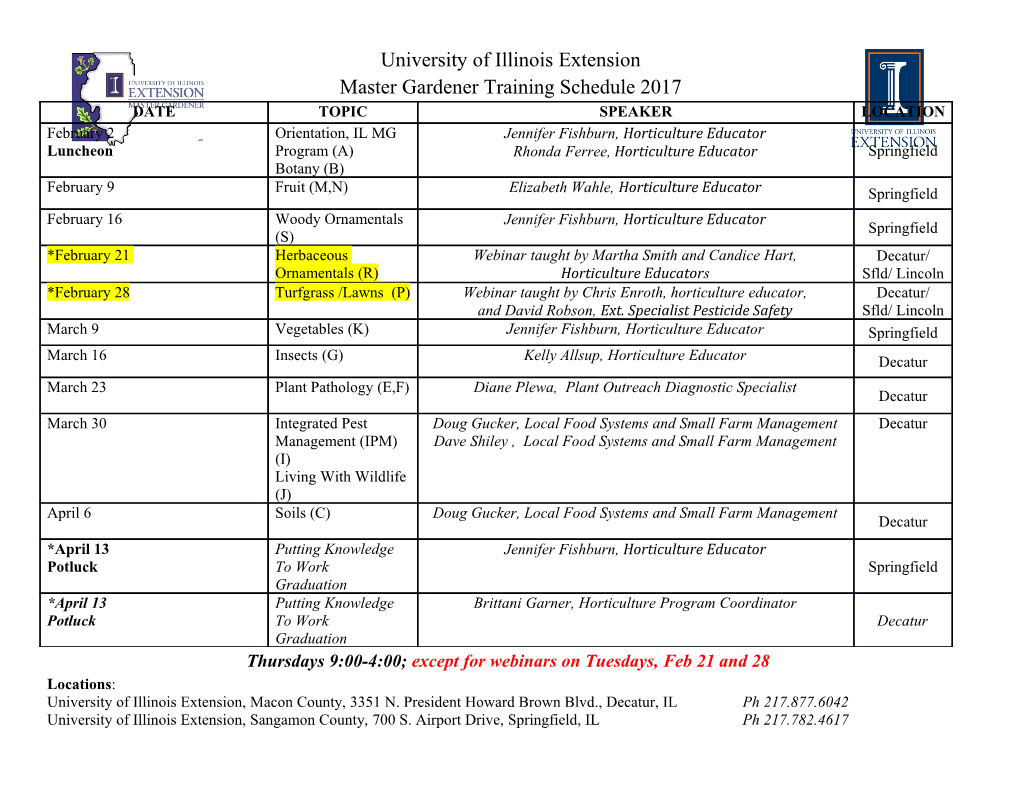
See discussions, stats, and author profiles for this publication at: https://www.researchgate.net/publication/272846799 Engineered bamboo for structural applications Article in Construction and Building Materials · April 2015 DOI: 10.1016/j.conbuildmat.2015.01.077 CITATIONS READS 46 1,904 4 authors: Bhavna Sharma Ana Gatóo University of Bath University of Cambridge 22 PUBLICATIONS 243 CITATIONS 10 PUBLICATIONS 98 CITATIONS SEE PROFILE SEE PROFILE Maximilian Bock Michael Ramage University of Cambridge University of Cambridge 8 PUBLICATIONS 94 CITATIONS 48 PUBLICATIONS 213 CITATIONS SEE PROFILE SEE PROFILE Some of the authors of this publication are also working on these related projects: Engineered Bamboo View project Laser Induced Growth of Carbon Nanotubes View project All content following this page was uploaded by Bhavna Sharma on 07 September 2015. The user has requested enhancement of the downloaded file. Construction and Building Materials 81 (2015) 66–73 Contents lists available at ScienceDirect Construction and Building Materials journal homepage: www.elsevier.com/locate/conbuildmat Engineered bamboo for structural applications ⇑ Bhavna Sharma , Ana Gatóo, Maximilian Bock, Michael Ramage Department of Architecture, University of Cambridge, Cambridge, UK highlights Relevance of engineered bamboo products to construction and industry. Mechanical characterisation of bamboo scrimber and laminated bamboo is presented. Bamboo scrimber is shown to have similar strength to laminated bamboo. Engineered bamboo products have properties that are equal to or surpass that of timber. article info abstract Article history: Bamboo is a rapidly renewable material that has many applications in construction. Engineered bamboo Received 24 September 2014 products result from processing the raw bamboo culm into a laminated composite, similar to glue- Received in revised form 27 January 2015 laminated timber products. These products allow the material to be used in standardised sections and Accepted 29 January 2015 have less inherent variability than the natural material. The present work investigates the mechanical Available online 23 February 2015 properties of two types of commercially available products – bamboo scrimber and laminated bamboo sheets – and compares these to timber and engineered timber products. It is shown that engineered bam- Keywords: boo products have properties that are comparable to or surpass that of timber and timber-based products. Bamboo scrimber Potential limitations to use in structural design are also discussed. The study contributes to a growing Engineered composites Laminated bamboo body of research on engineered bamboo and presents areas in which further investigation is needed. Construction Ó 2015 The Authors. Published by Elsevier Ltd. This is an open access article under the CC BY license (http:// creativecommons.org/licenses/by/4.0/). 1. Introduction by nodes (solid diaphragms) along the culm length (Fig. 1). The thickness of the culm wall tapers from the base of the culm to Bamboo has many advantages as a construction material: it is a the top. As a functionally graded material, the bamboo fibres also rapidly renewable sustainable resource and has mechanical vary within the culm wall decreasing in density from the exterior properties similar to timber. Worldwide, there is a growing inter- to the interior (Fig. 1). est in the development of bamboo products as a sustainable, cost- While there are more than 1200 species worldwide, full culm effective and ecologically responsible alternative construction bamboo construction is limited by the variation in geometric and material [1]. Partially due to the faster growth rate, and therefore mechanical properties. The difficulty in making connections and harvest cycle, bamboo forests have up to four times the carbon joints suitable for round (and variable) sections is also prohibitive density per hectare of spruce forests over the long term [2]. Bam- for mainstream construction; however increasing research boo is found in rapidly developing areas of the world where often demonstrates a growing industry and demand for sustainable timber resources are limited [2]. While the potential of bamboo is building products. Studies vary from the use of full culm bamboo promising, more widespread development and use of bamboo is in construction and scaffolding (e.g., [5–10] to engineered hampered by the lack of engineering data for mechanical proper- bamboo composites (e.g., [11–21]. Engineered bamboo compos- ties and appropriate building codes [3,4]. ites are of particular interest due to the standardisation of Bamboo is an anisotropic material, having mechanical proper- shape and the relatively low variability in material properties ties that vary in the longitudinal, radial and transverse directions. [22]. The raw material is a giant grass consisting of a hollow culm Two examples of engineered bamboo are bamboo scrimber and having longitudinal fibres aligned within a lignin matrix, divided laminated bamboo [22]. Bamboo scrimber, also referred to as strand woven or parallel strand bamboo, consists of crushed fibre bundles saturated in resin and compressed into a dense block ⇑ Corresponding author. Tel.: +44 (0)1223 760124. (Fig. 2). The process is materially efficient, utilising approximately E-mail address: [email protected] (B. Sharma). http://dx.doi.org/10.1016/j.conbuildmat.2015.01.077 0950-0618/Ó 2015 The Authors. Published by Elsevier Ltd. This is an open access article under the CC BY license (http://creativecommons.org/licenses/by/4.0/). B. Sharma et al. / Construction and Building Materials 81 (2015) 66–73 67 80% of raw inputs [23], and produces a product with a Janka for structural applications. A comparison with timber and engi- hardness that is acceptable for external applications such as deck neered timber products is also presented. flooring. The process maintains the longitudinal direction of the bamboo fibres and utilises the resin matrix to connect the fibre bundles. In contrast, laminated bamboo maintains both the longitu- 2. Materials and methods dinal fibres as well as a portion of the original culm matrix. The Two commercially produced products from China were used in the study. The bamboo culm is split, planed, processed (bleached or caramelised), bamboo scrimber product is comprised of Phyllostachys pubescens (Moso) with a laminated and pressed to form the board product (Fig. 3). The orien- phenol formaldehyde resin. The final product is a 140 Â 140 mm section available tation of the strip within the board, and therefore the direction of in varying lengths. As shown in Fig. 2 and discussed in the previous section, the pro- cess of manufacturing bamboo scrimber uses the bamboo culm with minimal pro- the radial fibre density, is randomly placed within in the board cessing. The resulting commercial product is tested as a final product with no (Fig. 3). The final products use only approximately 30% of raw mate- additional modifications. The average density of the bamboo scrimber is 1160 kg/ rial input due to large losses of material when the strips are planed m3 with a moisture content of 7%. In comparison, Moso as a raw material has a rela- to form the rectangular section [23]. The sheet product is primarily tive density of approximately 0.5–1.0. used indoors for surface applications or furniture. While both mate- Laminated bamboo sheets are also manufactured from Moso bamboo strips using a soy-based resin as shown in Fig. 3 and discussed in the previous section. rials are currently used for surface applications, both maintain the The structural specimens are built up from a commercial sheet inherent strength of bamboo by maintaining the longitudinal fibre (2440 Â 1220 Â 19 mm). The sheet was cut and the section laminated into the orientation and the engineered product creates a uniform section desired dimensions using polyurethane adhesive (Purbond HB S309). The adhesive 2 for connections and joints in structural applications. was applied manually with a glue proportion of approximately 180 g/m (final pro- duct) and the lamina pressed using manual clamps to apply the required pressure of The present work investigates the mechanical properties of 0.6 MPa for 4 hours (Fig. 4). Two orientations were tested: radial horizontal and bamboo scrimber and laminated bamboo to assess the potential radial vertical, which refer to the orientation of the original strip within the beam, Fig. 1. Details of a bamboo culm. Fig. 2. Bamboo scrimber general manufacturing process in China. Fig. 3. Laminated bamboo general manufacturing process in China. 68 B. Sharma et al. / Construction and Building Materials 81 (2015) 66–73 as shown in Fig. 3. The industry terminologies for the equivalent orientations are sections below. All of the mechanical properties were calculated in edgewise and flatwise respectively, which refer to the orientation of the strips with- the linear elastic region at the limit of proportionality as required in a board, however this terminology is not well-defined for beam sections. There- fore the two orientations are herein described as radial horizontal and radial by the standards. Table 2 lists the average (x) and the coefficient vertical and are shown in Fig. 4. The laminated bamboo has an average density of of variation (COV); ten specimens were tested in every case (i.e., 686 kg/m3 with a moisture content of 6%. All specimens are conditioned in a con- n = 10). stant temperature of 23 °C and a relative humidity of 55% for 2 weeks before testing. 3.1. Tension 2.1. Standard test methods used Fig. 5 shows a comparison of representative failures for both par- To obtain the material and mechanical properties, tension, compression, shear allel to grain and perpendicular to grain tests. In tension parallel to and flexural tests were conducted based on BS 373 Methods of testing small clear spe- grain (f t k), both the bamboo scrimber and the laminated bamboo cimens of timber [24], ASTM D143 Standard Test Methods for Small Clear Specimens of exhibited linear behaviour prior to failure. The tension perpen- Timber [25] and BS EN 408 Timber structures – Structural timber and glue-laminated dicular to grain (f ) results emphasises the low strength of the bam- timber [26].
Details
-
File Typepdf
-
Upload Time-
-
Content LanguagesEnglish
-
Upload UserAnonymous/Not logged-in
-
File Pages9 Page
-
File Size-