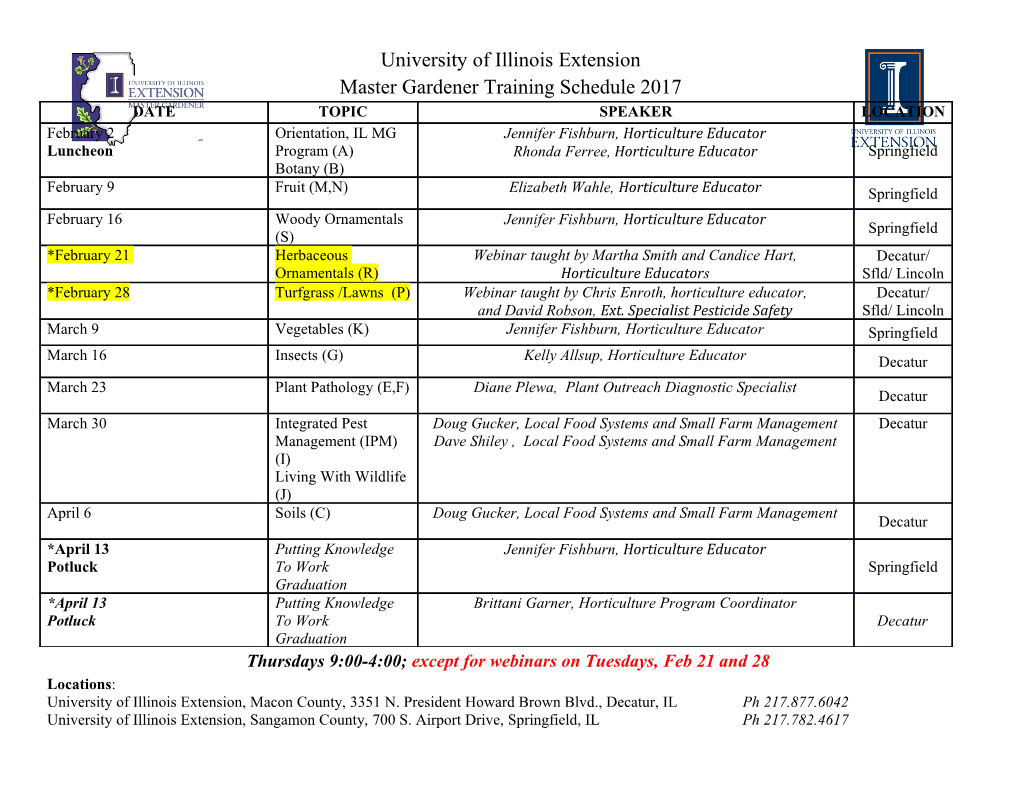
<p> Agenda Item: 650-2032</p><p>Title: Welder ID Marking Date: May 24, 2016</p><p>Handled by Charlie Race Marathon Petroleum Company 17333 Federal Drive Allen Park, MI 45101-3649 Telephone: 313-297-6074 Email: [email protected]</p><p>Purpose: To clarify in the standard which tank welds require welder identification records. Source: Inquiry No. 650-2016-F2 Revision: 3 Impact: The business impact of this item is minor.</p><p>Rationale: Standard clarity</p><p>Discussion: As currently written, section 9.4 of the standard requires all welds with the exception of roof plate welds and flange-to-nozzle-neck welds to either be stamped on the tank or otherwise identified on a weld map. It was suspected that welder identification records were not being kept as an industry practice for several miscellaneous welds such as wind girder to shell welds, rafter clip welds and tank anchor welds. The purpose of the agenda item was to re-write section 9.4 in the standard to better align the document with generally accepted industrial practices and better define which weld joints truly need to be identified in the welding records.</p><p>A survey of seventeen (17) tank manufactures was performed to document which tank welds they currently keep welder or welding operator records on to comply with the requirements of API 650 section 9.4. Below is a summary of the survey.</p><p>Page 1 of 4 Type of Weld Joint Percentage of Fabricators Recording Welder ID</p><p>Shell Welds 100% Corner Weld 100% Shell Openings 94% Shell to Top Angle 71% Permanent Shell Attachments 24% (piping support re-pad, stairs) Wind girder to shell 29% Wind girder to Wind girder welds 12% Rafter Clips 12% Structural Steel Spices 18% Gauge Pole Spices 12% Floor sketch plate 94% Annular plates 100% Floor re-pads 53% Floor sump assemblies 82% Floating Roof Pontoon 59% Floating Roof Leg assemblies 29% Floating deck plates 47% Floating Roof manways 24% Floating Roof nozzles 29% Floating Roof Sumps 29%</p><p>Proposal: </p><p>See changes highlighted in red below </p><p>Current</p><p>9.4 Identification of Welded Joints</p><p>The welder or welding operator’s identification mark shall be hand- or machine-stamped adjacent to and at intervals not exceeding 1 m (3 ft) along the completed welds. In lieu of stamping, a record may be kept that identifies the welder or welding operator employed for each welded joint; these records shall be </p><p>Page 2 of 4 accessible to the inspector. Roof plate welds and flange-to-nozzle-neck welds do not require welder identification.</p><p>Rev 1 (Changes in red)</p><p>9.4 Identification of Welded Joints</p><p>The welder or welding operator’s identification mark shall be hand- or machine-stamped adjacent to and at intervals not exceeding 1 m (3 ft) along the completed welds. In lieu of stamping, a written record may be kept that identifies the welder or welding operator employed for each welded joint; these records shall be accessible to the inspector Records shall be kept for all shell welds, bottom welds and draw off sump welds. Records shall also be kept for shell and bottom opening welds including opening reinforcement welds. Roof plate welds and Flange-to-nozzle-neck welds do not require welder identifications.</p><p>Rev 2 (Changes in Blue)–</p><p>9.4 Identification of Welded Joints</p><p>The Manufacturer shall assign each welder or welding operator’s an identifying number, letter, or symbol. This identifying identification mark shall be hand- or machine-stamped, either by hand or machine, on all tanks adjacent to and at intervals of not more than exceeding 1 m (3 ft) along the completed welds made by a welder or welding operator; alternatively, the Manufacturer may keep a written record of welders employed on each joint and shell-opening joint and omit the stamping. In lieu of stamping, a Written and stamped welder ID records shall be maintained until tests are completed may be kept that identifies the welder or welding operator employed for each welded joint; these records and shall be available accessible to the inspector for all pressure boundary containing welds and for all opening welds including all opening reinforcements. Records shall be kept for all shell welds, bottom welds and draw off sump welds. Records shall also be kept for shell and bottom opening welds including opening reinforcement welds. Roof plate welds Lap welded roof seams and flange-to-nozzle-neck welds do not require welder identifications.</p><p>Rev 3 (Changes in green) –</p><p>9.4 Identification of Welded Joints</p><p>The Manufacturer shall assign each welder or welding operator’s an identifying number, letter, or symbol. This identifying identification mark shall be hand- or machine-stamped, either by hand or machine, on all tanks adjacent to and at intervals of not more than exceeding 1 m (3 ft) along the completed welds made by a welder or welding operator; alternatively, the Manufacturer may keep a written record of welders employed on each joint and shell-opening joint and omit the stamping. In lieu of stamping, a Written and stamped welder ID records shall be maintained until tests are completed may be kept that identifies the welder or welding operator employed for each welded joint; these records and shall be available accessible to the inspector for all pressure boundary containing welds including and for all opening welds including and all opening reinforcements Records shall be kept for all shell welds, bottom welds and draw off sump welds. Records shall also be kept for shell and bottom opening welds including opening reinforcement welds. Roof plate welds except for the following: lap welded roof seams and flange-to- nozzle-neck welds. do not require welder identifications.</p><p>Clean Copy</p><p>The Manufacturer shall assign each welder or welding operator an identifying number, letter, or symbol. This identifying mark shall be stamped, either by hand or machine, on all tanks adjacent to and at </p><p>Page 3 of 4 intervals of not more than 1 m (3 ft) along the welds made by a welder or welding operator; alternatively, the Manufacturer may keep a written record of welders employed on each joint and shell-opening joint and omit the stamping. Written and stamped welder ID records shall be maintained until tests are completed and shall be available to the inspector for all pressure boundary containing welds including all opening welds and all opening reinforcements except for the following: lap welded roof seams and flange- to-nozzle-neck welds.</p><p>Page 4 of 4</p>
Details
-
File Typepdf
-
Upload Time-
-
Content LanguagesEnglish
-
Upload UserAnonymous/Not logged-in
-
File Pages4 Page
-
File Size-