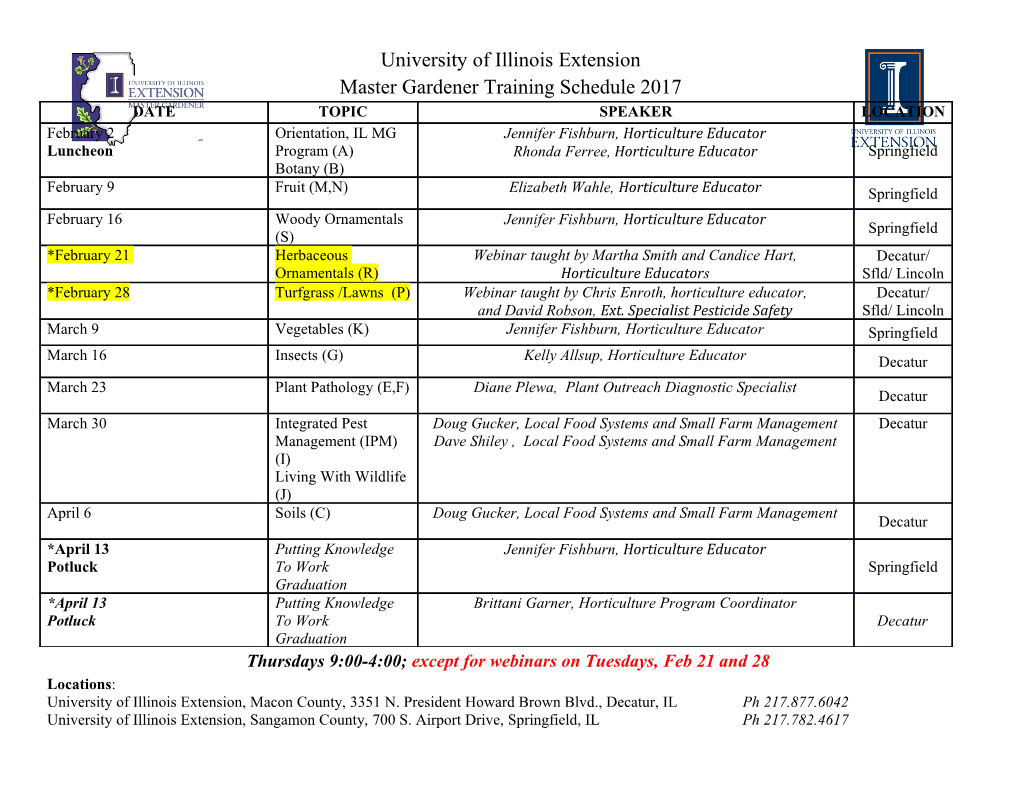
<p>KALART (KALART/VICTOR) PROJECTORS</p><p>The information contained in this appendix relates mainly to the 70 series, but it applies generally to the Kalart/Victor range, including older Victor models. We are indebted to the Film Collectors reference Centre of Illinois, a division of Harris Co, and to Bob Connelly for original material. Much of the following is extracted from original American literature. Some terminology has been modified to suit Australian conditions and for consistency with the content of this manual.</p><p>(Illustration: The Kalart Victor. No illustration good enough for the purpose could be found at time of writing.)</p><p>To anyone used to working with conventional projectors, the Kalart/Victor (known often as Kalart and less often as Victor) is an extraordinary, even exotic machine. Everything about it is different. The feed reel is on the left, the take up reel on the right. You start threading from the sound drum (which is static) to the take up sprocket and reel, then go back to the sound drum and thread through the gate and feed sprocket (which is actually the other side of the take up sprocket) to the feed reel. But that’s just the beginning. Its film path is offset first in one direction and then the other to accommodate the unique film transport system. And to make it even more interesting, the amplifier is valve (or tube) powered in many models. But don’t be misled into thinking the Kalart is inferior in any way to better known brands. Its film transport system is arguably as good as anything in the business, despite its apparent strangeness. It will succeed in screening films other projectors stumble over. The valve amplifier delivers a soft, easy-to-listen-to sound, and although the lamp is only 200 watts the picture is crisp and steady. When it is operating, the Kalart is very quiet. The greatest shortcoming of the Kalart is its complexity, especially if you want to maintain it in good condition. It is belt driven, but the belts are difficult to get at when they have to be replaced. Parts, including valves, are becoming harder to find. Its electrics are an unending source of fascination, as many machines were imported from the USA. Some were converted from 110 to 240 AC before they arrived, others after they landed. Some were never converted and still rely on an external transformer, without which they cannot run. For a while Kalart projectors were manufactured under licence in Australia, and these did not need to be converted. They had a transformer fitted inside them. Some Kalarts still use tungsten lamps, with large lamp houses and reflectors, while others are fitted with QI one piece units. It just goes on and on. If you need to move your projector often, a Kalart is probably not the best choice. At around 24 kg, it is a real lump to carry even short distances.</p><p>Setting up Install the reel arms so that the reel shafts point towards the operator’s side of the projector. Place the rewind belt on the large pulley of the rear reel arm. Twist the reverse take up belt (nearest or inside belt) through half a turn and place it on the small pulley of the rear reel arm. Twist the front belt (or outside belt) through half a turn and place it on the small pulley of front reel arm for films of 400’ or less and on large pulley for films of greater length. Place the supply reel on the rear reel arm so that the film comes off the top clockwise. Place the take up reel on the front reel arm.</p><p>Speaker set up Remove the speaker cord from the rack in the speaker case. Plug the cord into the projector speaker socket. If you are using two or more 12 inch speakers, plug the main speaker into the projector socket marker ‘dual’. Then plug the second speaker into the first.</p><p>Sound controls Turn on the exciter lamp. Turn on the amplifier. Raise volume by turning the volume control clockwise. Increase bass by turning the tone control clockwise. Threading Before threading, open the sound tension rollers, open the swing out lens at the catch marked ‘pull’ and open film shoes. Thread film from the supply reel to the top of the take up reel so that it takes up the film clockwise. Pull enough film from the supply reel to cover the name plate below the projector motor. Slide the film over the sound drum. Engage perforations on the teeth of the sound sprocket to the right of the sound drum. Close front and rear pinch rollers to the left and right of the sound drum. Thread film loosely around and to the left of the middle safety trip (red) and under the take up sprocket. This is the lower half of the main drive sprocket located above the sound drum. Engage sprocket teeth and close the bottom sprocket shoe. Position film to the right of the tension roller and to the left of the final roller before the take up reel. Place the film in the gate channel, allowing a bottom loop the size of an index finger to the left of and below the lower safety trip (red). (Bottom loop determines the accuracy of film synchronization.) Close the swing out lens. Allowing for the top loop, thread film over the feed sprocket (the top half of the main drive sprocket) engaging perforations with teeth and close the sprocket shoe.</p><p>Threading the Kalart/Victor</p><p>Check the threading by rotating the inching wheel downwards (forwards).</p><p>Screening 1. Select sound or silent 2. Raise clutch lever 3. Press motor switch down to start motor 4. Press lamp switch down to light lamp 5. Raise and lower the screen image by releasing the spring loaded tilt wheel at the front. 6. Focus by turning the lens barrel until the screen image is sharp. 7. Frame the screen image by turning the knurled framing knob on the side of the gate. 8. Adjust sound tone and volume 9. To stop film movement, press the top safety trip (red). Cleaning The optical system Every ten hours of use, polish the projector lens. At all times avoid finger marking the lens surface.</p><p>The sound system Every five hours. Clean the rear pinch roller and the front sound sprocket, also the front and rear tension rollers, using soft cloth. Oil or hardened film emulsion gum can be removed using carbon tetrachloride. (Editor’s note: (!) Isopropyl alcohol, a plastic scraper and a cotton bud will do the job.) Be sure the pinch roller and tension rollers revolve freely. Loosen the sound drum set screw and remove the sound drum by pulling directly outwards. Refer to the diagram below.</p><p>The sound drum removed</p><p>After wiping the sound film channel, clean the film channel slot by inserting the doubled end of a pipe cleaner in the opening. Also clean the lower side of the sound lens inside the sound drum. Be sure no lint remains on the lens or in the slot. Blow out if necessary. When you return the sound drum be sure it is fully seated, all the way in and with the slot at the top.</p><p>Every 50 hours Remove the sound drum as described above. Remove screws ‘A’ and ‘B’. Lift off the sound film channel and sound lens assembly and place in inverted position. Refer to the diagrams below.</p><p>The sound film channel and sound lens assembly inverted</p><p>Remove screws ‘C’ and ‘D’ and lift out the sound lens unit. Warning: Don’t go near screw ‘E’. The sound lens unit</p><p>WARNING #2: Do not tamper with or loosen screw ‘E’. If you do, the entire assembly will have to be referred to an expert who is able to reset the lens unit. At last count there was one in Australia.</p><p>With a clean lintless cloth, polish sound slit ‘F’ by placing the cloth over a thumbnail. Also polish the condensor lens ‘G’.</p><p>Reassemble the sound unit and sound drum, taking care to have the slot in the sound channel nearest screw ‘B’ as shown.</p><p>Cleaning the film channel and rollers The film channel and rollers should be cleaned before each screening. Caution: Do not use a metal instrument to clean these or any part of the film path. Keep film trip rollers and upper and lower sprocket shoes clean. Check that the sprocket shoe rollers and the film trip rollers operate freely.</p><p>Lubrication More service problems result from over oiling than under oiling. Excess oil clogs the light slit in the sound lens, gums the brushes in the motor and governor commutators and destroys wire insulation. The result is loss of sound quality, irregular speed and short circuiting of electrical components. The following oiling schedule is recommended. Refer to the diagram below.</p><p>Oiling points</p><p>Oiling points 1, 2 and 3: four drops every three hours of running 4 and 5: one drop every ten hours of running 6 and 7: two drops every four hours of running All oiling points should be oiled if the projector has been idle for a long period of time.</p><p>Trouble shooting The Troubleshooting chapter covers most of the problems you are likely to encounter with the Kalart. But there are a couple of features that are unique to this machine. </p><p>1. Safety trips If threading is incorrect or film is defective, the safety trips will operate and automatically stop the projector. Reset the loops and start again. Remember to engage the clutch before starting the motor.</p><p>2. Loss of bottom loop The Kalart does not have an automatic loop restorer, but the bottom loop can be restored by flipping it down with the tip of a pencil.</p>
Details
-
File Typepdf
-
Upload Time-
-
Content LanguagesEnglish
-
Upload UserAnonymous/Not logged-in
-
File Pages5 Page
-
File Size-