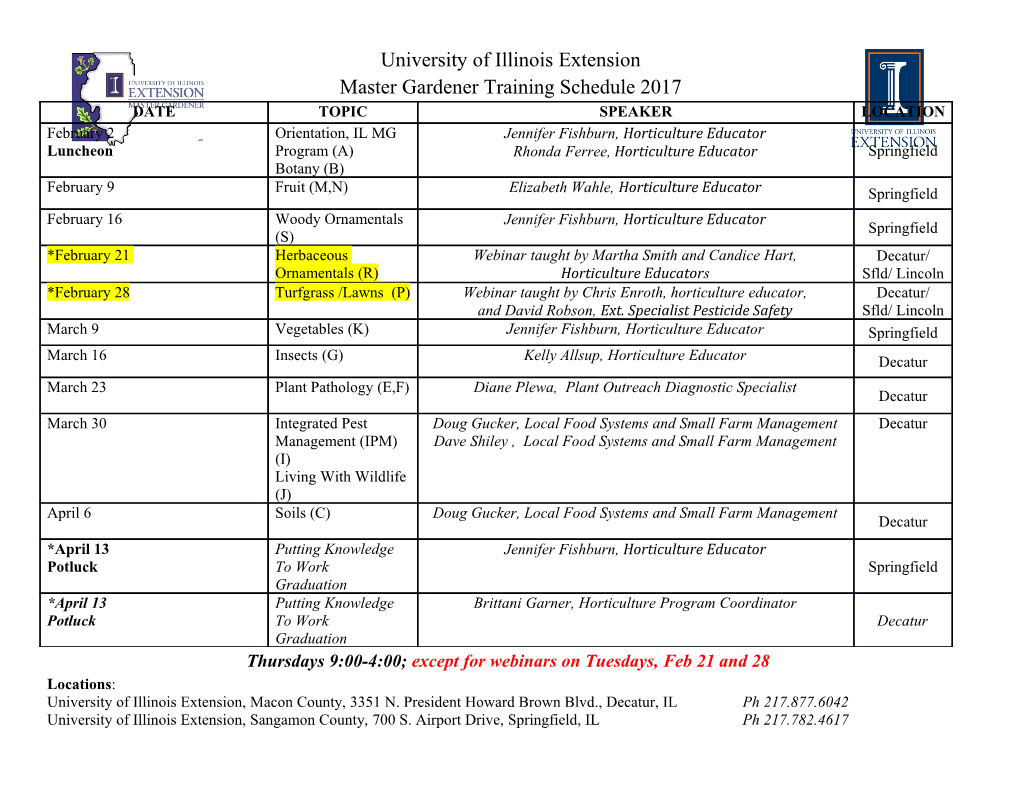
<p> Operational Procedure QP-05</p><p>CORRECTIVE ACTION</p><p>Issued by: General Manager</p><p>QP-05</p><p>Rev.: 1/7/24</p><p>Pg. 1 of 2</p><p>I PURPOSE The purpose of this procedure is to provide for a system to assign responsibilities for initiating, implementing, and verifying the effectiveness of corrective actions so as to not recur. This tool is used to get to the root cause of a problem so the root cause can be corrected. II APPLICATION This procedure applies to: correcting major system nonconformities; internal audit nonconformities; repeating product non-conformances and; customer complaints. III PROCEDURE 1 Corrective actions Corrective actions are implemented to address actual nonconformities. A corrective action request (CAR) may be initiated by anyone in the organization. Corrective actions may be requested in the following cases: * A significant problem with a process or work operation; * A nonconformity identified during an audit; * Repeat identification of a nonconforming product; * Significant and legitimate customer complaint.</p><p>Approved by: </p><p>John Graham CORRECTIVE ACTION</p><p>Operational Procedure</p><p>QP-05</p><p>Rev.: 1/7/24</p><p>Pg. 2 of 2</p><p>2 Requesting and processing CARs Any employee may issue a CAR according to the above criteria. When a problem or situation requiring a corrective action is identified, 1. the first section of the CAR form is to be used to record the situation and the person initiating the corrective action. 2. The CAR is then to be sent to the ISO 9000 Management Representative (General Manager). 3. Upon receiving a request for corrective action, the ISO9000 Management Representative will assign the CAR to the appropriate person to investigate the nonconformance (this may include the General Manager self-assigning the CAR). 4. Using the CAR form, the assignee will record the ‘Root Cause’ and then the ‘Action Necessary’ to correct the nonconformity. 5. Once the action is implemented, the date is recorded on the CAR form. 6. Return the form to the ISO 9000 Management Representative (General Manager). 7. Once the ISO Management Representative (General Manager) has objective evidence that the corrective action is ‘effective,’ the CAR will be closed out and signed by the ISO Management Representative. The CAR is to be submitted in the next Management Review. IV REFERENCED DOCUMENTS * Blank Corrective Action Request (CAR) form V ASSOCIATED RECORDS * Completed Corrective Action Request form</p>
Details
-
File Typepdf
-
Upload Time-
-
Content LanguagesEnglish
-
Upload UserAnonymous/Not logged-in
-
File Pages2 Page
-
File Size-