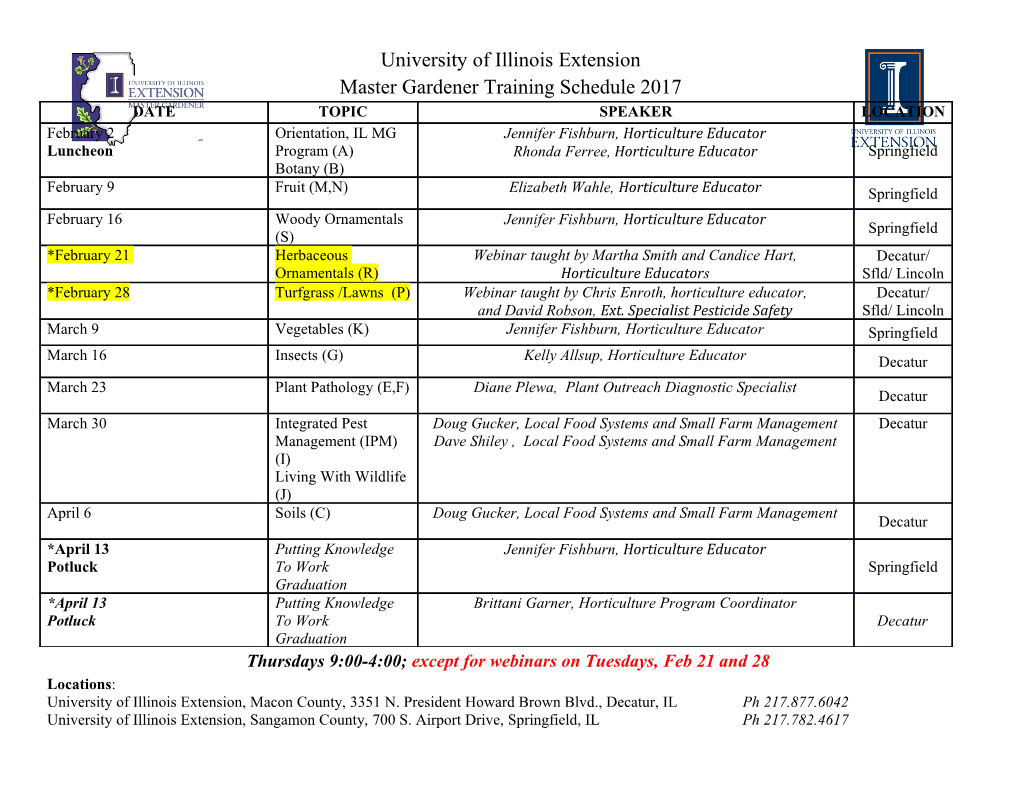
<p> RESEARCH ON VIBRATION CHARACTERISTICS OF CIRCULATION PUMP</p><p>Zhong Li, School of energy and power engineering, Jiangsu University Zhenjiang, China Dawei Zhen, School of energy and power engineering, Jiangsu University Zhenjiang, China Long Abstract Fuli Zhi, School of energy and power engineering, Jiangsu University Zhenjiang, China Dan Ni, School of energy and power engineering, Jiangsu University Zhenjiang, China Minguan Yang, School of energy and power engineering, Jiangsu University Zhenjiang, China</p><p>Introduction The circulation pump is one of rotary hydraulic machinery applied widely in some liquid cycle process of many fields. The operation stability is one of concerned characteristics for modern circulation pump, and with the development of increasing rotate speed to decrease overall dimension, more attention should be paid to it. The vibration is the main reason to damage pump’s operation stability, so we need to analysis its inducement and then reduce its negative influence. In some special application situation, the damage caused by vibration is breaking the system effectiveness and the vibration performance is the most important properties for pump. The mechanical factor, electrical factor and hydraulic factor are three mainly inducing factor of vibration for pump, the third is the most complicated. The unsteady flow phenomenon exist in pump such as cavitation, recirculation and stall are the main exciting source of pump vibration. In order to solve the vibration problem, we must master the relationship between flow structure and induced vibration characteristics firstly, and then optimize internal flow to realize active vibration control. From the recent research status, it is not difficult to find that researchers have done many works in unsteady flow characteristics. JENS, et al[1], investigated two similar centrifugal pump impellers of low specific speed and found the cavity volume in relation to the incidence angel and the characteristic propagation frequencies of rotating cavitation. CERYONE, et al[2], built a high-speed optical system and obtained the characterization of flow instabilities generated by cavitation. PHILIPPE, et al[3], combined a high frequency accelerometer and revealed the fluid-structure interaction caused by Karman vortices in the wake of a truncated 2D hydrofoil. LI, et al[4] and ZHANG, et al[5] visualized the supercavitation flow structures around a hydrofoil and employed the DPIV to survey the velocity distribution inside the cavity. Although the experimental research on flow structure and the interaction between flow structure and energy performance has been done, there are less study of relationship between flow and vibration performance for axial-flow pump has been published to date. This paper carried out the experimental monitoring on vibration acceleration at main points of circulation pump under different operating conditions by using LMS sound and vibration measurement. The relationship between root mean square value of vibration acceleration within specific frequency domain and variable operating conditions of pump were revealed preliminarily. The research achievements are helpful to promote the understanding of mechanisms of unsteady flow and induced vibration and provide the theoretical basis for circulation pump’s optimal design for low vibration and stable operation.</p><p>1. Methods In order to carry out the performance tests and capture the vibration performance of circulation pump, the experimental system is setup as shown in Fig.1 which comprises the closed pump system and the vibration monitoring system. 1.vacuum pump 2.tank 3.valve 4.computer 5. LMS Test Lab 6.acceleratin sensor 7.model pump 8.torque and rev measurement instrument 9.auxiliary pump 10.turbin flow meter 11.exlecronic valve 12.temperature sensor Fig. 1 Experimental setup LMS multi-channel noise and vibration testing and dynamic analysis system (LMS SCADAS III) adopted by the LMS SCADA mobile number front-end, ICP acceleration sensor, acceleration sensor calibrator, photoelectric speed sensor, data acquisition and analysis software and high-performance computers composition. This instrument is one of the most advanced vibration test and analysis equipment. In order to survey the vibration characteristics fully, seven acceleration sensors are installed respectively in main position of circulation pump. The mounting position of each sensor is shown in Fig.2.</p><p>Fig. 2 Acceleration sensor installing position</p><p>Conclusions 1) The shaft frequency, blade frequency and their higher harmonic are main exciting frequency of pump. 2) The trends of root mean square value of vibration acceleration within 10~8000 Hz frequency domain with flow rate is the same as trend of head of pump with flow rate. With the decrease of flow rate, the changing process of vibration level can be divided into three stages: low-level stage, rapid increase stage and high-level stage. Within 10~350 Hz frequency domain, the flow rate according to lowest vibration level point in low-level stages is the same as flow rate of best efficiency point. 3) The vibration induced by cavitation is mainly high frequency vibration, and bubble collapse in very short period of time, generally in milliseconds or less. 4) With the decrease of NPSH value, the level of high and low frequency vibration all increased first and then decreased. The high frequency vibration is easy weakened than low frequency vibration by damping. The inflection point of high frequency vibration rising curve is the same as the energy decreased critical point induced by cavitation. </p><p>References [1]JENS F, Gunter K , 2002, “Rotating Cavitation in a Centrifugal Pump Impeller of Low Specific Speed”, Journal of Fluid Engineering,Vol. 124, No. 2, pp. 356-362. [2] CERYON A, BRAMANTI C, TORRE L, et al, 2007,“Setup of a High-speed Optical System for the Characterization for Flow Instabilities Generated by Cavitation”, Journal of Fluids Engineering, Vol. 129, No. 7, pp. 877-885. [3] PHILIPPE A, MOHAMED F, FRANCOIS A, et al, 2005,“Cavitaion Effects on Fluid Structure Interaction in the Case of a 2D Hydrofoil”, 2005 ASME Fluids Engineering Division Summer Meeting, V2005, pp. 2461-2466. [4] LI Xiang-bin, WANG Guo-yu, ZHANG Min-di, et al,2008,“Characteristics of Supercavitating Flows around a Hydrofoil”, Chinese Journal of Theoretical and Applied Mechanics, Vol. 40, No. 3, pp. 316- 322. [5] ZHANG Bo, WANG Guo-yu, HUANG Biao, et al,2009,“Unsteady Dynamics of Cavitating Flows around a Hydrofoil”, Journal of Experiments in Fluid Mechanics, Vol. 23, No. 3, pp. 44-49.</p>
Details
-
File Typepdf
-
Upload Time-
-
Content LanguagesEnglish
-
Upload UserAnonymous/Not logged-in
-
File Pages3 Page
-
File Size-