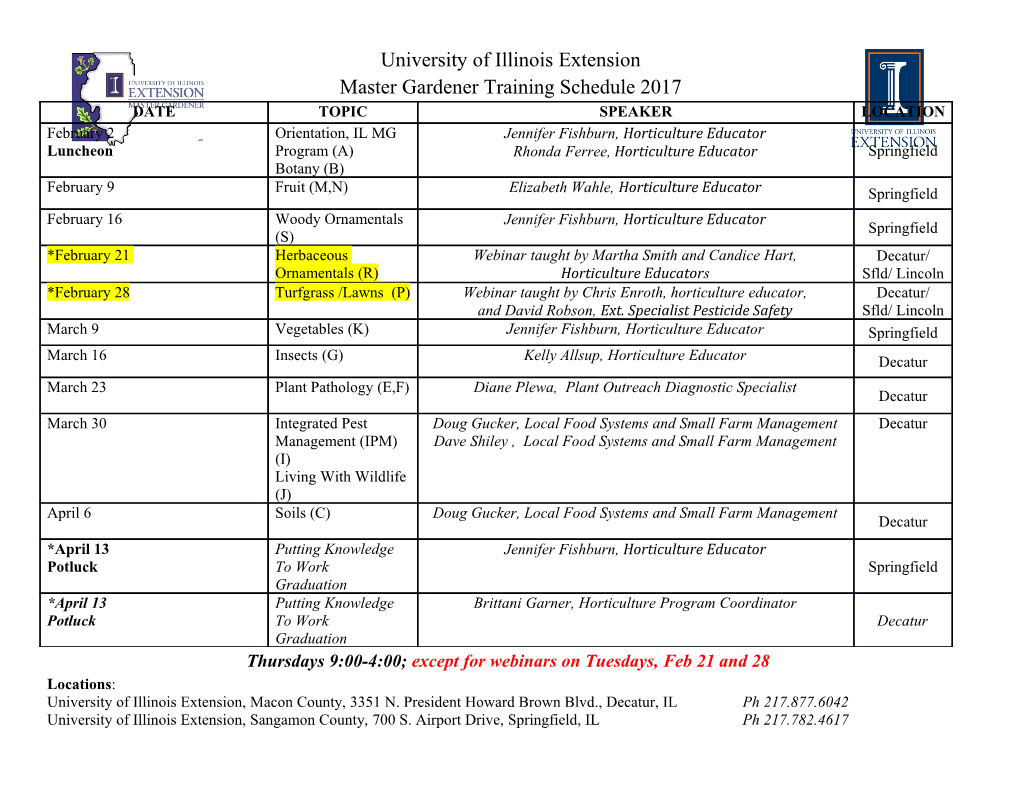
<p>Quality and Statistical Process Control</p><p>The concept of quality has been with us since the beginning of time. As early as the creation of the world described in the Bible in Genesis, God pronounced his creation "good"-- e.g., acceptable quality. Artisans' and craftsmen's skills and the quality of their work are described throughout history. Typically the quality intrinsic to their products was described by some attribute of the products such as strength, beauty or finish. However, it was not until the advent of the mass production of products that the reproducibility of the size or shape of a product became a quality issue. </p><p>Quality, particularly the dimensions of component parts, became a very serious issue because no longer were the parts hand-built and individually fitted until the product worked. Now, the mass-produced part had to function properly in every product built. Quality was obtained by inspecting each part and passing only those that met specifications. This was true until 1931 when Walter Shewhart, a statistician at the Hawthorne plant at Western Electric, published his book Economic Control of Quality of Manufactured Product (Van Nostrand, 1931). This book is the foundation of modern statistical process control (SPC) and provides the basis for the philosophy of total quality management or continuous process improvement for improving processes. With statistical process control, the process is monitored through sampling. Considering the results of the sample, adjustments are made to the process before the process is able to produce defective parts.</p><p>Processes and Process Variability </p><p>The concept of process variability forms the heart of statistical process control. For example, if a basketball player shot free throws in practice, and the player shot 100 free throws every day, the player would not get exactly the same number of baskets each day. Some days the player would get 84 of 100, some days 67 of 100, some days 77 of 100, and so on. All processes have this kind of variation or variability. </p><p>This process variation can be partitioned into two components. Natural process variation, frequently called common cause or system variation, is the naturally occurring fluctuation or variation inherent in all processes. In the case of the basketball player, this variation would fluctuate around the player's long-run percentage of free throws made. Special cause variation is typically caused by some problem or extraordinary occurrence in the system. In the case of the basketball player, a hand injury might cause the player to miss a larger than usual number of free throws on a particular day. </p><p>Statistical Process Control </p><p>Shewhart's discovery statistical process control or SPC is a methodology for charting the process and quickly determining when a process is "out of control" (e.g., a special cause variation is present because something unusual is occurring in the process). The process is then investigated to determine the root cause of the "out of control" condition. When the root cause of the problem is determined, a strategy is identified to correct it. The investigation and subsequent correction strategy is frequently a team process and one or more of the TQM process improvement tools are used to identify the root cause. Hence, the emphasis on teamwork and training in process improvement methodology. </p><p>It is management's responsibility to reduce common cause or system variation as well as special cause variation. This is done through process improvement techniques, investing in new technology, or reengineering the process to have fewer steps and therefore less variation. Management wants as little total variation in a process as possible--both common cause and special cause variation. Reduced variation makes the process more predictable with process output closer to the desired or nominal value. The desire for absolutely minimal variation mandates working toward the goal of reduced process variation. </p><p>The process above is in apparent statistical control. Notice that all points lie within the upper control limits (UCL) and the lower control limits (LCL). This process exhibits only common cause variation.</p><p>The process above is out of statistical control. Notice that a single point can be found outside the control limits (above them). This means that a source of special cause variation is present. The likelihood of this happening by chance is only about 1 in 1,000. This small probability means that when a point is found outside the control limits that it is very likely that a source of special cause variation is present and should be isolated and dealt with. Having a point outside the control limits is the most easily detectable out-of- control condition. The graphic above illustrates the typical cycle in SPC. First, the process is highly variable and out of statistical control. Second, as special causes of variation are found, the process comes into statistical control. Finally, through process improvement, variation is reduced. This is seen from the narrowing of the control limits. Eliminating special cause variation keeps the process in control; process improvement reduces the process variation and moves the control limits in toward the centerline of the process.</p><p>Types of Out-of-Control Conditions</p><p>Several types of conditions exist that indicate that a process is out of control. The first of these we have seen already—having one or more points outside the 3 limits as shown below:</p><p>Extreme Point Condition </p><p>This process is out of control because a point is either above the UCL or below the UCL.</p><p>This is the most frequent and obvious out of control condition and is true for all control charts. </p><p>Control Chart Zones</p><p>Control charts can be broken into three zones, a, b, and c on each side of the process center line.</p><p>A series of rules exist that are used to detect conditions in which the process is behaving abnormally to the extent that an out of control condition is declared. Two of Three Consecutive Points in Zone A or Outside Zone A</p><p>The probability of having two out of three consecutive points either in or beyond zone A is an extremely unlikely occurrence when the process mean follows the normal distribution. Thus, this criteria applies only to charts for examining the process mean.</p><p>X, Y, and Z are all examples of this phenomena.</p><p>Four of Five Consecutive Points in Zone B or Beyond</p><p>The probability of having four out of five consecutive points either in or beyond zone B is also an extremely unlikely occurrence when the process mean follows the normal distribution. Again this criteria should only be applied to an chart when analyzing a process mean.</p><p>X, Y, and Z are all examples of this phenomena. Runs Above or Below the Centerline</p><p>The probability of having long runs (8 or more consecutive points) either above or below the centerline is also an extremely unlikely occurrence when the process follows the normal distribution. This criteria can be applied to both and r charts. </p><p>Example X above shows a run below the center line. </p><p>Linear Trends</p><p>The probability of 6 or more consecutive points showing a continuous increase or decrease is also an extremely unlikely occurrence when the process follows the normal distribution. This criteria can be applied to both and r charts. </p><p>X and Y are both examples of trends. Note that the zones play no part in the interpretation of this out of control condition.</p><p>Oscillatory Trend</p><p>The probability of having 14 or more consecutive points oscillating back and forth is also an extremely unlikely occurrence when the process follows the normal distribution. It also signals an out of control condition. This criteria can be applied to both and r charts. X is an example of this out of control condition. Note that the zones play no part in the interpretation of this out of control condition.</p><p>Avoidance of Zone C</p><p>The probability of having 8 or more consecutive points occurring on either side of the center line and do not enter Zone C is also an extremely unlikely occurrence when the process follows the normal distribution and signals an out of control condition. This criteria can be applied to charts only. This phenomena occurs when more than one process is being charted on the same chart (probably by accident—e.g., samples from two machines mixed and put on a single chart), the use of improper sampling techniques, or perhaps the process is over controlled or the data is being falsified by someone in the system. </p><p>X is an example of this out of control condition. </p><p>Run in Zone C </p><p>The probability of having 15 or more consecutive points occurring the Zone C is also an extremely unlikely occurrence when the process follows the normal distribution and signals an out of control condition. This criteria can be applied to charts only. This condition can arise from improper sampling, falsification of data, or a decrease in process variability that has not been accounted for when calculating control chart limits, UCL and LCL. X is an example of this out of control condition. </p><p>Quality Control Tools</p><p>Production environments that utilize modern quality control methods are dependant upon statistical literacy. The tools used therein are called the seven quality control tools. These include:</p><p>. Check Sheet . Pareto Chart . Flow Chart . Cause and Effect Diagram . Histogram . Scatter Diagram . Control Chart</p><p>Checksheet</p><p>The function of a checksheet is to present information in an efficient, graphical format. This may be accomplished with a simple listing of items. However, the utility of the checksheet may be significantly enhanced, in some instances, by incorporating a depiction of the system under analysis into the form.</p><p>A defect location checksheet is a very simple example of how to incorporate graphical information into data collection. Additional data collection checksheet examples demonstrate the utility of this tool. The data collected will be used in subsequent examples to demonstrate how the individual tools are often interconnected.</p><p>Pareto Chart Pareto charts are extremely useful because they can be used to identify those factors that have the greatest cumulative effect on the system, and thus screen out the less significant factors in an analysis. Ideally, this allows the user to focus attention on a few important factors in a process.</p><p>They are created by plotting the cumulative frequencies of the relative frequency data (event count data), in decending order. When this is done, the most essential factors for the analysis are graphically apparent, and in an orderly format.</p><p>From the Pareto Chart it is possible to see that the initial focus in quality improvement should be on reducing edge flaws. Although the print quality is also of some concern, such defects are substantially less numerous than the edge flaws. Flowchart</p><p>Flowcharts are pictorial representations of a process. By breaking the process down into its constituent steps, flowcharts can be useful in identifying where errors are likely to be found in the system.</p><p>By breaking down the process into a series of steps, the flowchart simplifies the analysis and gives some indication as to what event may be adversely impacting the process. </p><p>Cause and Effect Diagram</p><p>This diagram, also called an Ishikawa diagram (or fish bone diagram), is used to associate multiple possible causes with a single effect. Thus, given a particular effect, the diagram is constructed to identify and organize possible causes for it.</p><p>The primary branch represents the effect (the quality characteristic that is intended to be improved and controlled) and is typically labelled on the right side of the diagram. Each major branch of the diagram corresponds to a major cause (or class of causes) that directly relates to the effect. Minor branches correspond to more detailed causal factors. This type of diagram is useful in any analysis, as it illustrates the relationship between cause and effect in a rational manner. Having decided on which problem to focus on, a Cause and Effect diagram of the related process is created to help the user see the entire process and all of its components.</p><p>In many instances, attempts to find key problem areas in a process can be a hit or miss proposition. In this instance, it was decided to collect data on the curetimes of the material.</p><p>Histogram</p><p>Histograms provide a simple, graphical view of accumulated data, including its dispersion and central tendancy. In addition to the ease with which they can be constructed, histograms provide the easiest way to evaluate the distribution of data.</p><p>Data for a test of curetimes was collected and analyzed using a histogram.</p><p>From this chart, the curetime distribution does not appear to be a normal distribution as might be expected, but is bimodal instead. Deviations from a normal distribution in a histogram suggest the involvement of additional influences in the process. </p><p>Curing Time Test Results order curetime defects order curetime defects 1 31.6583 0 51 40.53732 3 2 29.7833 0 52 41.69992 3 3 31.8791 0 53 38.01712 2 4 33.9125 0 54 42.23068 4 5 34.4643 0 55 40.16485 2 6 25.1848 0 56 38.35171 2 7 37.76689 1 57 44.17493 4 8 39.21143 2 58 37.32931 1 9 41.34268 3 59 41.04428 3 10 39.54590 2 60 38.63444 2 11 29.5571 0 61 34.5628 0 12 32.5735 0 62 28.2506 1 13 29.4731 0 63 32.5956 0 14 25.3784 1 64 25.3439 2 15 25.0438 1 65 29.2058 0 16 24.0035 2 66 32.0702 0 17 25.4671 1 67 30.6983 0 18 34.8516 0 68 40.30540 3 19 30.1915 0 69 35.55970 0 20 31.6222 0 70 39.98265 2 21 46.25184 5 71 39.70007 2 22 34.71356 0 72 33.95910 0 23 41.41277 3 73 38.77365 1 24 44.63319 4 74 35.69885 0 25 35.44750 0 75 38.43070 2 26 38.83289 2 76 40.05451 3 27 33.0886 0 77 43.13634 4 28 31.6349 0 78 44.31927 5 29 34.55143 0 79 39.84285 2 30 33.8633 0 80 39.12542 2 31 35.18869 0 81 39.00292 2 32 42.31515 3 82 34.9124 0 33 43.43549 4 83 33.9059 0 34 37.36371 1 84 28.2279 0 35 38.85718 2 85 32.4671 0 36 39.25132 2 86 28.8737 1 37 37.05298 1 87 34.3862 0 38 42.47056 4 88 33.9296 0 39 35.90282 0 89 33.0424 0 40 38.21905 2 90 28.4006 1 41 38.57292 2 91 32.5994 0 42 39.06772 2 92 30.7381 0 43 32.2209 0 93 31.7863 0 44 33.202 0 94 34.0398 0 45 27.0305 1 95 35.7598 0 46 33.6397 0 96 42.37100 3 47 26.6306 2 97 30.206 0 48 42.79176 4 98 34.5604 0 49 38.38454 2 99 27.93 1 50 37.89885 1 100 30.8174 0 Scatter Diagram</p><p>Scatter diagrams are graphical tools that attempt to depict the influence that one variable has on another. A common diagram of this type usually displays points representing the observed value of one variable corresponding to the value of another variable.</p><p>Applying curing time test data to create a scatterplot, it is possible to see that there are very few defects in the range of approximately 29.5 to 37.0 minutes. Thus, it is possible to conclude that by establishing a standard cure time within this range, some degree of quality improvement is likely. Control Chart</p><p>The control chart is the fundamental tool of statistical process control, as it indicates the range of variability that is built into a system (known as common cause variation). Thus, it helps determine whether or not a process is operating consistently or if a special cause has occurred to change the process mean or variance.</p><p>The bounds of the control chart are marked by upper and lower control limits that are calculated by applying statistical formulas to data from the process. Data points that fall outside these bounds represent variations due to special causes, which can typically be found and eliminated. On the other hand, improvements in common cause variation require fundamental changes in the process.</p><p>Applying statistical formulas to the data from the curetime tests of base material, it was possible to construct X-bar and R charts to assess its consistency. As a result, we can see that the process is in a state of statistical control.</p><p> order ct1 ct2 ct3 ct4 1 27.34667 27.50085 29.94412 28.21249 2 27.79695 26.15006 31.21295 31.33272 3 33.53255 29.32971 29.70460 31.05300 4 37.98409 32.26942 31.91741 29.44279 5 33.82722 30.32543 28.38117 33.70124 6 29.68356 29.56677 27.23077 34.00417 7 32.62640 26.32030 32.07892 36.17198 8 30.29575 30.52868 24.43315 26.85241 9 28.43856 30.48251 32.43083 30.76162 10 28.27790 33.94916 30.47406 28.87447 11 26.91885 27.66133 31.46936 29.66928 12 28.46547 28.29937 28.99441 31.14511 13 32.42677 26.10410 29.47718 37.20079 14 28.84273 30.51801 32.23614 30.47104 15 30.75136 32.99922 28.08452 26.19981 16 31.25754 24.29473 35.46477 28.41126 17 31.24921 28.57954 35.00865 31.23591 18 31.41554 35.80049 33.60909 27.82131 19 32.20230 32.02005 32.71018 29.37620 20 26.91603 29.77775 33.92696 33.78366 21 35.05322 32.93284 31.51641 27.73615 22 32.12483 29.32853 30.99709 31.39641 23 30.09172 32.43938 27.84725 30.70726 24 30.04835 27.23709 22.01801 28.69624 25 29.30273 30.83735 30.82735 31.90733 Summary</p><p>The tools listed above are ideally utilized in a particular methodology, which typically involves either reducing the process variability or identifying specific problems in the process. However, other methodologies may need to be developed to allow for sufficient customization to a certain specific process. In any case, the tools should be utilized to ensure that all attempts at process improvement include:</p><p> Discovery Analysis Improvement Monitoring Implementation Verification </p><p>Furthermore, it is important to note that the mere use of the quality control tools does not necessarily constitute a quality program. Thus, to achieve lasting improvements in quality, it is essential to establish a system that will continuously promote quality in all aspects of its operation. Control Charts as a tool in SQC (Statistical Quality Control)</p><p>Overview</p><p>This page has been designed to help in understanding and learning the use, design and analysis of Control Charts, which is the most important tool of Statistical Quality Control.</p><p>The information has been formatted in the form of a tutorial, which will guide you through the process. It includes the history, background information, the uses, the types with examples, analysis of patterns, related software and additional sources of information about control charts. </p><p>History</p><p>Control charting is one of the tools of Statistical Quality Control(SQC) It is the most technically sophisticated tool of SQC. It was developed in the 1920s by Dr. Walter A. Shewhart of the Bell Telephone Labs.</p><p>Dr. Shewhart developed the control charts as an statistical approach to the study of manufacturing process variation for the purpose of improving the economic effectiveness of the process. These methods are based on continuous monitoring of process variation. </p><p>Background Information</p><p>A typical control chart is a graphical display of a quality characteristic that has been measured or computed from a sample versus the sample number or time. The chart contains a center line that represents the average value of the quality characteristic corresponding to the in-control state. Two other horizontal lines, called the upper control limit(UCL) and and the lower control limit(LCL) are also drawn. These control limits are chosen so that if the process is in control, nearly all of the sample points will fall between them. As long as the points plot within the control limits, the process is assumed to be in control, and no action is necessary. </p><p>However, a point that plots outside of the control limits is interpreted as evidence that the process is out of control, and investigation and corrective action is required to find and eliminate the assignable causes responsible for this behavior. The control points are connected with straight line segments for easy visualization.</p><p>Even if all the points plot inside the control limits, if they behave in a systematic or nonrandom manner, then this is an indication that the process is out of control. </p><p>Uses of Control charts Control chart is a device for describing in a precise manner what is meant by statistical control. Its uses are </p><p>1. It is a proven technique for improving productivity. 2. It is effective in defect prevention. 3. It prevents unnecessary process adjustments. 4. It provides diagnostic information. 5. It provides information about process capability. </p><p>Types of control charts</p><p>1. Control Charts for Attributes</p><p>Introduction</p><p>Many quality characteristics cannot be conveniently represented numerically. In such cases, each item inspected is classified as either conforming or nonconforming to the specifications on that quality characteristic. Quality characteristics of this type are called attributes. Examples are nonfunctional semiconductorchips, warped connecting rods, etc,.</p><p> p charts</p><p>This chart shows the fraction of nonconforming or defective product produced by a manufacturing process. It is also called the control chart for fraction nonconforming. </p><p> c charts</p><p>This shows the number of defects or nonconformities produced by a manufacturing process.</p><p> u charts</p><p>This chart shows the nonconformities per unit produced by a manufacturing process.</p><p>2. Control Charts for Variables</p><p>Introduction</p><p>Many quality characteristics can be expressed in terms of a numerical measurement. A single measurable quality characteristic, such as a dimension, weight, or volume, is called a Variable. Control charts for variables are used extensively. They usually lead to more efficient control procedures and provide more information about process performance than attributes control charts. When dealing with a quality characteristic that is a variable, it is a standard practice to control both the mean value of the quality characteristic and its variability. Control of the process average or mean quality level is usually with the control chart for means, or the x bar chart. The control of the process range is done by using the control chart for range, or the R chart. </p><p>X bar and R charts</p><p>The X bar chart is developed from the average of each subgroup data. The R chart is developed from the ranges of each subgroup data, which is calculated by subtracting the maximum and the minimum value in each subgroup. An example showing the development of the charts is provided.</p><p>Example showing procedure for making X bar and R Control Charts</p><p>Construction of Control charts</p><p>Plastic Keychains are being produced in a company named Etcetra. The plastic material is first molded and then trimmed to the required shape. The curetimes during the molding process affect the edge quality of the keychains produced. The aim is to achieve statistical control of the curetimes using X bar and R charts.</p><p>Curetime data of twenty-five samples, each of size four, have been taken when the process is assumed to be in control. These are shown in table 1. Save the raw data for this table and try to draw the control charts. Compare the results with those given here. </p><p>Table 1 ------Sample No. Observations means range ------1 27.34667 27.50085 29.94412 28.21249 28.25103 2.59745 2 27.79695 26.15006 31.21295 31.33272 29.12317 5.18266 3 33.53255 29.32971 29.70460 31.05300 30.90497 4.20284 4 37.98409 32.26942 31.91741 29.44279 32.90343 8.54130 5 33.82722 30.32543 28.38117 33.70124 31.55877 5.44605 6 29.68356 29.56677 27.23077 34.00417 30.12132 6.77340 7 32.62640 26.32030 32.07892 36.17198 31.79940 9.85168 8 30.29575 30.52868 24.43315 26.85241 28.02750 6.09553 9 28.43856 30.48251 32.43083 30.76162 30.52838 3.99227 10 28.27790 33.94916 30.47406 28.87447 30.39390 5.67126 11 26.91885 27.66133 31.46936 29.66928 28.92971 4.55051 12 28.46547 28.29937 28.99441 31.14511 29.22609 2.84574 13 32.42677 26.10410 29.47718 37.20079 31.30221 11.09669 14 28.84273 30.51801 32.23614 30.47104 30.51698 3.39341 15 30.75136 32.99922 28.08452 26.19981 29.50873 6.79941 16 31.25754 24.29473 35.46477 28.41126 29.85708 11.17004 17 31.24921 28.57954 35.00865 31.23591 31.51833 6.42911 18 31.41554 35.80049 33.60909 27.82131 32.16161 7.97918 19 32.20230 32.02005 32.71018 29.37620 31.57718 3.33398 20 26.91603 29.77775 33.92696 33.78366 31.10110 7.01093 21 35.05322 32.93284 31.51641 27.73615 31.80966 7.31707 22 32.12483 29.32853 30.99709 31.39641 30.96172 2.79630 23 30.09172 32.43938 27.84725 30.70726 30.27140 4.59213 24 30.04835 27.23709 22.01801 28.69624 26.99992 8.03034 25 29.30273 30.83735 30.82735 31.90733 30.71869 2.60460 ------Means 30.40289 5.932155 ------The means and the ranges in each sample are calculated. The mean of the sample means and the sample ranges are also calculated. The mean for the ranges gives the center line for the R chart. Using n=4 from the table for calculating the control limits, we get that D3 = 0 and D4=2.282. Therefore the control limits for the R chart are LCL = Rmean x D3 = 0</p><p>UCL = Rmean x D4 = 13.525</p><p>The R chart is drawn with the 25 sample ranges plotted on the chart. The Control limits and the center line are also drawn. This is shown in the figure below. All the points are within the control limits and no particular pattern can be observed. Therefore the process variability is in control. </p><p>Since the R chart indicates the process variablity is in control, the X bar chart is now constructed. The center line is the mean of the sample means. Using the same table, and taking n=4 the control limits calculated are </p><p>UCL = xmean_of_means + A2 x Rmean = 34.733</p><p>LCL = xmean_of_means - A2 x Rmean = 26.072 The X bar chart is drawn with the 25 sample means plotted on the chart. The Control limits and the centre line are drawn too. This is shown in the figure below. No indication of out of control condition is observed from this figure. </p><p>Since both the X bar and the R chart exhibit control, the process can be taken to be in control at the stated levels and the control limits can be adopted for use in on-line statistical process control. </p><p>Continuation of the X bar and R charts</p><p>Twelve additional samples of curetime data from the molding process were collected from an actual production run. The data from these new samples are shown in table 2. Save the raw data for this table and try to draw the control charts. Compare the results with those given here </p><p>Table 2 ------Sample No. Observations means range ------</p><p>1 31.65830 29.78330 31.87910 33.91250 31.80830 4.12920 2 34.46430 25.18480 37.76689 39.21143 34.15686 14.02663 3 41.34268 39.54590 29.55710 32.57350 35.75480 11.78558 4 29.47310 25.37840 25.04380 24.00350 25.97470 5.46960 5 25.46710 34.85160 30.19150 31.62220 30.53310 9.38450 6 46.25184 34.71356 41.41277 44.63319 41.75284 11.53828 7 35.44750 38.83289 33.08860 31.63490 34.75097 7.19799 8 34.55143 33.86330 35.18869 42.31515 36.47964 8.45185 9 43.43549 37.36371 38.85718 39.25132 39.72693 6.07178 10 37.05298 42.47056 35.90282 38.21905 38.41135 6.56774 11 38.57292 39.06772 32.22090 33.20200 35.76589 6.84682 12 27.03050 33.63970 26.63060 42.79176 32.52314 16.16116 ------The X bar and the R charts are drawn with the new data with the same control limits established before. They are shown below </p><p>The observations from the control charts :</p><p>X bar chart </p><p> Six points fall above UCL. One point falls below LCL. One point falls on UCL. </p><p>R chart </p><p> Two points fall above UCL. Eight consecutive points are above the center line. Both the charts show that the process is out of control. The possible reasons for it can be understood by looking at the Analysis of Patterns on Control charts</p><p>Analysis of Patterns on Control Charts</p><p>A control chart may indicate an out-of-control condition either when one or more points fall beyond the control limits, or when the plotted points exhibit some nonrandom pattern of behavior. </p><p>The process is out of control if any one or more of the criteria is met. </p><p>1. One or more points outside of the control limits. This pattern may indicate: o A special cause of variance from a material, equipment, method, or measurement system change. o Mis-measurement of a part or parts. o Miscalculated or mis-plotted data points. o Miscalculated or mis-plotted control limits. 2. A run of eight points on one side of the center line. This pattern indicates a shift in the process output from changes in the equipment, methods, or materials or a shift in the measurement system. 3. Two of three consecutive points outside the 2-sigma warning limits but still inside the control limits. This may be the result of a large shift in the process in the equipment, methods, materials, or operator or a shift in the measurement system. 4. Four of five consecutive points beyond the 1-sigma limits. 5. An unusual or non-random pattern in the data. </p><p> a. A trend of seven points in a row upward or downward. This may show . Gradual deterioration or wear in equipment. . Improvement or deterioration in technique. b. Cycling of data can indicate . Temperature or other recurring changes in the environment. . Differences between operators or operator techniques. . Regular rotation of machines. . Differences in measuring or testing devices that are being used in order. 2. Several points near a warning or control limit. </p>
Details
-
File Typepdf
-
Upload Time-
-
Content LanguagesEnglish
-
Upload UserAnonymous/Not logged-in
-
File Pages22 Page
-
File Size-