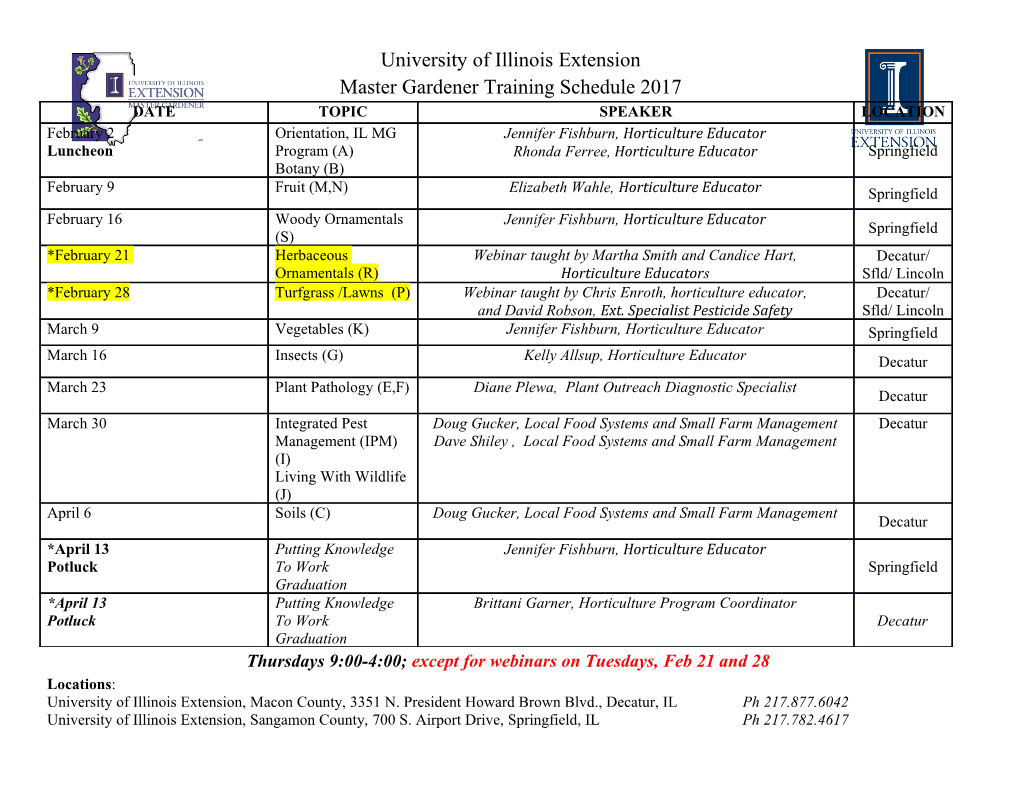
<p>In-depth article </p><p>Reader Contact [email protected]</p><p>Media Contact: Tom Van de Putte, +32 (0) 473 78 49 37 [email protected] </p><p>Traceability: Automatic labelling processes reinforce even smaller Electronics manufacturers</p><p>Tight labelling requirements grow evermore important when the traceability of parts and assemblies through the entire production process is required by the basic conditions of product liability, expanded warranty obligations or established quality standards such as ISO/EN 9001:2000, QS9000, VDA6.2 and TS16949. Brady progressively keeps pace with this development and continues to develop new comprehensive labelling solutions.</p><p>Labelling: The key to traceability Our attention focuses on robust, easy to integrate identification solutions with durable labels, printers and suitable software infrastructures. As a worldwide identification specialist, Brady plays a central role in this growing need around the globe. (Fig. 1).</p><p>“To a large extent, there is real demand for quick, precise and consistent solutions for the identification of components for traceability purposes,” says David Walmsley, Global Market Manager Electronics at Brady (Fig. 2). With over 20 years of experience, Walmsley has a good overview of the requirements of identification solutions for the traceability of assemblies and finished products. </p><p>“Labels are moving towards ever smaller formats. This simultaneously raises placement accuracy requirements. The best results are delivered by the combination of easy-to-use, high-end applicators with label materials specifically developed for automatic processing.” Because of this, Walmsley adds, Brady sees labelling for traceability as a production-related holistic solution. “This applies to the label material as well as to its application system.”</p><p>Increased traceability requirements for the entire supply chain</p><p>“For a long time, traceability was a key concept in large OEMs and their tier 1 suppliers,” says Walmsley. “And now, even smaller subcontractors in the overall supply chain are integrated into this requirement profile. They are increasingly facing demand to offer complete and professionally developed traceability solutions. This applies to the automotive and electronics sectors, the military and aviation businesses and large research institutions.” </p><p>Walmsley considers this development to be absolutely justified. “The costs of product recalls can be drastically minimised if a manufacturer is in a position to identify precisely those parts that need to be returned and replaced.” That is all the more important and vital in the current economic climate, demanding extremely cost-conscious environments. That is why traceability has become a necessary must even for small and medium-sized companies. </p><p>“In recent years, traceability conditions in production and delivery systems all the way to customer and user sites became a production technology driver”, says Walmsley. “This is especially true for the area of production efficiency.” </p><p>The three elements of labelling An efficient component labelling system in mass production consists of three equally important systemic elements:</p><p>• a robust label material with an imprint that allows fault-free identification even after many years of use under extreme conditions,</p><p>• a specific tagging system that allows the automatic labelling of the respective product, and</p><p>• suitable barcode software that can be integrated into the manufacturer’s MRP system and supports the representation of various data on the respective label.</p><p>The label materials and devices used for PC board labelling must ensure the 100% readability of labels in all stages of the production process. Brady offers optimal solutions for this purpose. In their development, special attention was given to great printability and a razor-sharp printed image. Sloppy print edges are a thing of the past. (Fig. 3). </p><p>High temperature resistance</p><p>“The resistance and reliability of labels for traceability depends to a large extent on the material grades. Almost equally important is adapting the label build to its use in automatic tagging systems,” says Tim Van den Eede, Product Marketing Manager at Brady (Fig. 4).</p><p>“Material quality in its entirety accounts for almost 80 per cent of reliability during the automatic application of labels. Brady’s R&D Department has developed purpose-built polyimide materials for auto-apply and materials for automated labelling of PC boards. They are marketed as the UltraTempTM series with a total of nine different label materials.”</p><p>Brady’s UltraTempTM labels survive for five minutes at temperatures of up to 260°C. They resist harsh chemicals and cleaning processes that are common in the production of PC boards, devices and parts. They enable the monitoring of the entire circuit board production cycle and contribute to process optimisation and operating cost reduction.</p><p>UltraTemp label materials are tested under strict conditions to guarantee their resistance to high temperatures, chemicals and mechanical abrasion, and to ensure optimal performance during fusion and wave soldering processes as well as during circuit board cleaning. </p><p>“The new generation of UltraTemp labels can resist the more advanced cleaning processes in the EMS industry. These advanced cleaning processes are more demanding in terms of label materials, because they use more aggressive chemicals and work at higher pressure. Among other things, these fairly new cleaning processes called for more advanced adhesives on the labels”, explains van den Eede.</p><p>Many options in terms of materials With options including static dissipative labels, different substrate thicknesses and manual and automatic attachment, the UltraTemp series is especially suitable for current processes used in PC board labelling. Special backing materials, like anauto-dispense liner, ensure trouble-free use in automatic labelling solutions (Print & Apply). </p><p>The polyimide labels are fabricated in ISO-9001 and ISO/TS-16949-certified processes and they are UL- CSA-approved. Standard sizes and customer-specific special formats are available. The associated printing ribbons are adapted to the label materials, making sure the imprint is resistant to a variety of solvents and washing processes.</p><p>Auto-Apply — Clean Liner against adhesive bleeding The “Thermal Transfer Clean Liner Technology” is an innovative solution in which labels are attached to a liner (backing material) after the punching action. The advantage is that, no adhesive can run into the </p><p> press cut at excess temperatures. This eliminates downtime due to labels not being placed, or due to a fractured liner. Thermal Transfer Clean Liner Technology ensures a smooth production cycle even at high temperatures. </p><p>Label or laser? Two types of traceability solutions, laser identification and traceability labelling, compete with one another in terms of abrasion and solvent resistance as well as optical resolution of available reading technology. </p><p>Enabling traceability with printed labels has the advantage of being able to attach labels to components in small spaces. The technology allows identification of components and PC boards in resolutions between 300 and 600 dpi, even when dealing with a large quantity of data. It also offers more safety, since labelling for traceability does not damage PC board tracks. A fourth advantage of traceability labelling over laser identification is the possibility to rectify any labelling errors, by covering the old label with a new one, or by reprinting the label, at maximum contrast and on surfaces of any shape. </p><p>Print applicators Print applicators offer high-quality thermal transfer printing and accurate label placement, resulting in extreme flexibility, even when changing labelling jobs quickly. Print applicators ensure the highest productivity in challenging automated labelling applications.</p><p>A printer applicator cuts all costs involving manual attachment of labels and ensures reliable positioning, especially when dealing with tiny labels. </p><p>Printing and application time is further reduced with Brady’s special “zero-queue” print and apply principle, processing and tracking labels in real time without queuing. Brady’s zero-queue print and apply principle translates to a substantial shortening of the labelling cycle. Incorrectly printed labels can be reprinted immediately afterwards — up to three times. It also saves time and costs during production.</p><p>Properties of print applicators</p><p>• Application system for reliable and precise labelling on a lot of materials.</p><p>• No supporting air necessary — that is, no flying label equipment.</p><p>• Suction and compressed-air nozzles for adaptation to differences in material thickness.</p><p>• Zero-queue printing for processing, tracking and troubleshooting in real time.</p><p>• Smallest labels are precisely printed and applied. </p><p>Simple integration into production An improvement in automatic printing and labelling solutions offered by Brady is the BSPTM61, a print applicator with a small footprint that is easy to integrate into production systems (Fig. 5). “Our customers told us that simplicity is of great importance,” says David Walmsley. “The BSP61 offers precisely that: it is easy to integrate and simple to use. In addition, it prints a large quantity of information on a tiny label and places the label very precisely. It cleanly picks up the labels to be placed and is very reliable when working with materials developed for auto-apply.”</p><p>Manual labelling Brady also offers a series of different print systems for manual labelling. These systems offer options to preprint and roll up labels, and facilitate the manual labelling process. Alternatively, labels can be removed manually, simply and quickly from the print system through an optional dispensing plate. Pre- printed labels can also be attached to PC boards by feeders that are compatible with almost all established assembly machines.</p><p>The new BBPTM33 label printer ensures quick and effortless printing, even in cases of frequent changing of materials, because of the printer’s auto-calibrate function. (Fig .6). With its extremely quick, flexible and waste-free changing of material, the BBPTM33 is the perfect solution for production environments with manifold labelling requirements, from PC board labelling to cable identification with heat shrinkable sleeves. The printer can easily be used with various materials resistant to many chemicals and temperatures and available in standard and user-defined sizes.</p><p>Traceability as a system Qualified labels are the central elements of traceability. Labelling solutions that can be integrated seamlessly into the MRP system or other control software of manufacturers ensuring that barcodes, established 2D codes or variable information is printed on and can be read by every individual component or assembly. </p><p>Since this data is transparent through the MRP system for production control purposes, quality testing can be executed more efficiently, resulting in faster fault finding. From a system point of view, the following aspects are important to integrate: </p><p>• high-quality label materials,</p><p>• matching ribbons,</p><p>• suitable, compatible printers, </p><p>• regular printer maintenance,</p><p>• adequate software infrastructure,</p><p>• trained operating personnel.</p><p>Brady can support you in setting up an automated traceability system to answer the growing demand for identification on all fabricated components. We offer traceability solutions that are easy to integrate and simple to use with quality labels that can resist most chemicals, solvents and temperatures.</p><p>Images Fig. 1 Brady Auto-Apply Fig. 2. David Walmsley Fig. 3. Brady labels with clear print image on the finger Fig. 4. Tim van den Eede Fig. 5. BSPTM61 Fig. 6. BBPTM33</p><p>About Brady Corporation:</p><p>Brady Corporation is an international manufacturer and marketer of complete solutions that identify and protect premises, products and people. Brady’s products help customers increase safety, security, productivity and performance and include high-performance labels, signs, safety devices, printing systems and software and precision die-cut materials. Founded in 1914, the company has a diverse customer base in electronics, telecommunications, manufacturing, electrical, construction, education, medical and a variety of other industries. Brady is headquartered in Milwaukee, Wisconsin, and as of July 31, 2013 employed approximately 7400 people in its worldwide businesses. Brady stock trades on</p><p> the New York Stock Exchange under the symbol BRC. More information is available on the internet at www.bradycorp.com. </p><p># # #</p>
Details
-
File Typepdf
-
Upload Time-
-
Content LanguagesEnglish
-
Upload UserAnonymous/Not logged-in
-
File Pages7 Page
-
File Size-